Ограничения по массе
|
Бетонная ВПП
|
Грунтовая ВПП
|
максимальная рулежнаямасса,
кг
|
17100
|
153000
|
максимальнаявзлетнаямасса,
кг
|
170000
|
152000
|
максимальная посадочная
масса, кг
|
151500
|
135500
|
максимальная масса пустого
самолета без тплива, кг
|
128000
|
118000
|
максимальная масса топлива
на исполнительном старте, кг
|
4600
|
66600
|
максимальная масса топлива
при посадке, кг
|
3000
|
24000
|
максимальная масса
нагрузки, кг
|
40000
|
30000
|
масса служебной нагрузки,
кг
|
3400
|
3400
|
В исключительных случаях разрешается посадка с любой массой до
максимальной взлетной включительно, а так же с запасом топлива, превышающим
максимально допустимый, при повышенном внимании экипажа. Емкость топливной
системы составляет около 112000 л.
Взлет и посадка разрешается на аэродромах, расположенных на
барометрической высоте от минус 300 м (давление 787 мм рт.ст) до плюс 1000 м
(давление 674 мм рт.ст). Температура воздуха на аэродромах взлета и посадки от
минус 50ºС до минус 45ºС. Эксплуатация самолета допустима до
Н=12000 м в диапазоне температур от “Минимальной для арктических условий” до
“Максимальной межконтинентальной”. Самолет при рулении устойчив.
Удовлетворительные маневренные характеристики при этом обеспечиваются
управлением колесами передней опоры и, в случае необходимости, односторонним
подтормаживанием колес основных опор шасси. При рулении с запасом топлива более
55000 кг не допускается одностороннее торможение колес основных опор и резкий
односторонний перевод РУД двигателей. Колеса передней опоры управляются
штурвальчиком или педалями управления. В первом случае реализуется разворот на
угол ±50º,
а во втором - ±7º.
Для разворота самолета
на 180º
требуется полоса шириной
около 40 м при минимальном радиусе разворота около 13..15 м.
В процессе выполнения взлета и посадки необходимо помнить, что величина
предельно передней и предельно задней центровок зависит от остатка топлива. В
том случае, если центровка самолета без топлива находится в пределах 20..40%
САХ, то допустимый диапазон полетных центровок следующий [8]:
Таблица 4
Допустимый диапазон полетных центровок
mT,
т
|
84,6
|
80
|
70
|
60
|
50
|
40
|
30
|
10
|
20
|
XT ПП,
%САХ
|
22.9
|
22.9
|
22.9
|
9
|
2.9
|
29
|
22.6
|
22.3
|
22
|
XT ПЗ,
%САХ
|
33.0
|
33.7
|
35.2
|
36.4
|
38.0
|
38.5
|
39.0
|
39.5
|
40
|
Рис. 5 График изменения центровки самолета в зависимости от выработки
топлива [8]
Рис. 6 Графики для определения угла установки стабилизатора при взлете с
различной центровкой [8]
2. Особенности конструкции и эксплуатации топливной
системы Ил-76
2.1 Характеристика и схема топливной системы самолета Ил-76
Топливная система предназначена для подачи топлива к двигателям самолета,
к двигателю вспомогательной силовой установки и к генератору нейтрального газа.
Топливо размещается в двенадцати кессонных баках, расположенных по всему
размаху крыла между передним и задним лонжеронами. Все баки образуют четыре
изолированные группы (по числу двигателей), по три бака в группе. В каждую
группу входят главный бак, дополнительный и резервный. Каждый двигатель
питается от своей группы баков. Топливо подается к двигателю насосами подкачки
по отдельным трубопроводам, которые соединены между собой электрокранами
кольцевания. Электрокраны кольцевания дают возможность при необходимости
осуществить питание двигателей топливом из любого сочетания групп баков.
Топливо из баков каждой группы перекачивается в герметичный расходный отсек
главного бака в первую очередь из резервного бака, во вторую очередь - из
дополнительного бака, в третью очередь - из главного. Топливные баки
оборудованы системой дренажа, выполненной раздельно для баков левого и правого
полукрыла. В каждом полукрыле имеется два дренажа: основной, связывающий бак с
атмосферой в горизонтальном полете, в наборе высоты и на земле, и
дополнительный, обеспечивающий сообщение топливных баков с атмосферой при
планировании (аварийном снижении), когда основной дренаж заполнен топливом. В
концевой части каждого полукрыла расположен дренажный бак для сбора топлива,
попадающего в дренажный трубопровод. Накопившееся в дренажных баках топливо
автоматически при помощи центробежных насосов перекачивается в резервные баки
двигателей 1 и 4.
Заправка топливных баков осуществляется снизу под давлением через два стандартных
заправочных штуцера в обтекателе правых главных ног шасси. Управление заправкой
производится со щитка, расположенного рядом с заправочными штуцерами. Для
заправки сверху на всех баках установлены заливные горловины. Для слива топлива
в каждом баке имеется отдельный сливной кран.
Кроме того, возможен слив топлива из отдельной группы баков через сливные
краны, установленные на двигателях. В этом случае топливо сливается самотеком
или с помощью насосов подкачки. При работающих двигателях расход топлива
контролируется по указателям расходомеров и топливомеров, расположенных на
приборной доске летчиков. Кроме того, на приборной доске летчиков установлены
табло (по два на каждый двигатель), сигнализирующие о минимальном давлении
топлива и об отказе топливного фильтра. Кроме этого имеется табло
сигнализирующее об остатке 2000 кг топлива. Управление работой топливной
системы осуществляется с панели 15А центрального пульта летчиков, где
расположены выключатели и сигнальные лампы пожарных кранов, кранов кольцевания
и насосов подкачки и перекачки топлива.
Рис. 7 Панель управления топливной системой [8]
Рис. 8
Монтажная схема топливной системы [8]
Топливная система (ТС) состоит из:
системы дренажа;
системы слива конденсата и топлива;
топливных баков, размещённых по всему крылу и представляющие собой
кессон-баки, входящие в силовую схему крыла;
системы перекачки топлива и подачи его к основным двигателям;
системы заправки топливных баков;
системы подачи топлива к вспомогательной силовой установке (ВСУ).
2.1.1 Система
дренажа
Дренажная система выполнена раздельно для баков левого и правого
полукрыла. В каждом полукрыле предусмотрено два дренажа: основной,
обеспечивающий дренажирование баков в горизонтальном полете, в наборе высоты,
на земле, и дополнительный, обеспечивающий дренажирование баков при
планировании (аварийном снижении), когда основной дренаж будет залит топливом.
В каждом полукрыле имеется дренажный бак для сбора топлива, попадающего в
дренажный трубопровод. Накопившееся в дренажных баках топливо автоматически
перекачивается в резервные топливные баки двигателя 1 (из левого дренажного
бака) и двигателя 4 (из правого дренажного бака). Перекачка может быть включена
вручную с центрального пульта летчиков. Каждый дренажный бак сообщается с
атмосферой посредством воздухозаборника, выведенного под нижнюю поверхность
концевой части крыла.
Рис. 9 Схема дренажа топливных баков [8]
.1.2 Система слива конденсата
Для слива конденсата из топливных баков на самолете установлена система
централизованного слива, позволяющая произвести откачку конденсата ручным насосом
поочередно из каждого бака топливной системы. Кроме того, во всех топливных
баках установлены нажимные сливные краны 5120-150(с 0043453552-5120-825),
которые открываются с помощью специального приспособления с земли.
Основной системой слива конденсата топлива является система
централизованного слива. Слив конденсата через нажимные краны производится
только в сроки, определенные регламентом технического обслуживания самолета, а
также в тех случаях, когда при централизованном сливе в конденсате топлива будут
обнаружены механические примеси [5].
Рис. 10 Схема системы слива конденсата [8]
.1.3 Система перекачки топлива
Для обеспечения бесперебойной подачи топлива к двигателям расходные
отсеки главных баков непрерывно пополняются топливом, перекачиваемым из всех
баков с помощью насосов ЭЦНГ-10с76. Для обеспечения более полной выработки
топлива из баков ГГ, 4Г, 2Р и ЗР в них установлены струйные топливные насосы,
перекачивающие топливо в предрасходные отсеки этих баков.
Очередность выработки топлива из баков внутри каждой группы
обеспечивается автоматически.
В первую очередь топливо вырабатывается из резервного бака, во вторую
очередь из дополнительного и в третью - из главного. Насосы резервных баков
включаются вручную выключателями, расположенными на панели управления топливной
системой, а выключаются автоматически. Насосы перекачки из дополнительных и
главных баков включаются и выключаются автоматически, причем выключатели
насосов на панели управления находятся в положении «Выключено». Кроме того, все
насосы перекачки могут быть включены и выключены вручную соответствующими
выключателями.
При полной заправке баков топливом перекачку начинают включением вручную
насосов перекачки из резервных баков. Если резервные баки не заправлены,
перекачку топлива начинают включением вручную насосов перекачки из
дополнительных баков; если были заправлены только главные баки, перекачку
начинают включением вручную насосов перекачки из главных баков. Если до взлета
самолета не будут включены насосы перекачки хотя бы из одного резервного
заправленного топливом бака, то после отрыва самолета от ВПП на панели
управления топливной системой загорится желтая сигнальная лампа "Включи
перекачку резервных баков". Если резервные баки не заправлялись и до
взлета самолета не были включены вручную насосы перекачки из дополнительных
баков, то их включение после отрыва самолета произойдет автоматически. Если
заправлялись только главные баки, а их насосы перекачки не были включены
вручную до взлета самолета, включение произойдет также автоматически после
отрыва самолета от ВПП. При ручном включении насосов перекачки система
управления перекачкой обеспечивает их автоматическое отключение по окончании
перекачки топлива; выключение насосов до окончания перекачки может быть
произведено вручную теми же выключателями, с помощью которых производилось их
ручное включение [5].
Рис. 11 Схема системы перекачки топлива [8]
При автоматической включении насосов перекачки из дополнительных или
главных баков, насосы могут быть выключены вручную соответствующими автоматами
защиты сети (АЗС) системы автоматического управления перекачкой.
.1.4 Система заправки топливных баков
Заправка самолета топливом производится через систему заправки баков
снизу под давлением. Предусмотрены также заливные горловины, установленные на
верхних поверхностях баков, для заправки сверху. Система заправки снизу под
давлением выполнена одинаково в левой и правой половинах крыла; от заправочных
штуцеров до разветвления в левую и правую половины крыла магистраль заправки
является общей. Система обеспечивает заправку с максимальной
производительностью до 3000 л/мин при давлении топлива перед заправочными
штуцерами до 4 кГ/см2. Заправка баков под давлением производится
через два стандартных заправочных штуцера. Топливо в баки подается через
электрогидравлические клапаны заправки. Клапаны закрываются автоматически, если
баки заправляются полностью, и вручную, если баки заправляются частично.
Предусмотрено также автоматическое закрытие клапанов, если давление в баках
повысится до 0,2 кГ/см2.
С целью сокращения времени заправки предусмотрена возможность
одновременного подключения к системе четырех заправочных шлангов от двух
топливозаправщиков с помощью специального переходника 9108.500.
Управление заправкой и контроль осуществляется со щитка, расположенного в
правом обтекателе шасси.
Полная заправочная ёмкость баков составляет:
бак ТГ (4Г) - 4140 л;
бак ТД 4Д) - 5890 л;
бак ТР (4Р) - 16760 л;
бак 2Г (ЗГ) - 7490 л;
бак 2Д (ЗД) - 7180 л;
бак 2Р (ЗР) - 13280 л;
Полная ёмкость системы составляет 109480 л [5].
Рис. 12 Схема системы заправки самолета топливом [8]
Рис. 13 Щиток управления заправкой топливом [8]
.2 Агрегаты
топливной системы
.2.1 Топливные баки
Топливные баки самолета образованы внутренними объемами кессонов крыла,
герметизированных с помощью герметика УЗО-ЫЭС. Всего в крыле имеется двенадцать
топливных и два дренажных бака. Топливные баки разбиты на четыре изолированные
группы, по три бака в группе. Каждый двигатель питается от своей группы баков,
нумерация групп соответствует принятой нумерации двигателей (первая группа
баков - группа, питающая двигатель 1, вторая груша баков - группа, питающая
двигатель 2,и т.д.). В каждую группу входят главный бак (бак 1Г - в первой
группе, 2Г - во второй группе, ЗГ - в третьей группе, 4Г - в четвертой группе),
дополнительный бак (баки 1Д, 2Д, ЗД, 4Д) и резервный (1Р, 2Р, ЗР, 4Р). Баки
отделены один от другого герметичными перегородками. Главные баки всех групп
имеют расходные и предрасходные отсеки; дополнительные и резервные баки -
только предрасходные отсеки. В расходных отсеках главных баков установлено по
два насоса подкачки топлива к двигателю, в предрасходных отсеках баков - насосы
перекачки топлива в расходные отсеки главных баков (по два насоса перекачки в
предрасходных отсеках дополнительных и резервных баков и по одному насосу в
предрасходных отсеках главных баков).
Топливные баки первой ГРУППЫ (баки двигателя 1) размещены в левой ОЧК
(баки 1Г и 1Д) и левой СЧК (бак 1Р). Главный бак первой группы занимает
герметизированный отсек ОЧК, заключенный между нервюрами № 28 и 38 (с боков),
передним и задним лонжеронами крыла (спереди и сзади). Нервюра № 28 отделяет
бак 1Г от дополнительного бака первой группы, нервюра № 38 отделяет его от
левого дренажного бака. Внутри бака между нервюрами № 36 и 38 выделен расходный
отсек, в котором установлены два подкачивающих насоса ЭЦНГ-10с76 датчик
топливомера из комплекта СПУТ4-1. Подкачивающий насос между нервюрами № 36 и 37
заключен в противоотливной стакан, служащий для обеспечения подачи топлива
насосом при отрицательных перегрузках; подкачивающий насос, установленный между
нервюрами № 7 и 38, заключен в экран, который препятствует отливу топлива от
насоса при резком торможении самолета. Нервюрой № 36 расходный отсек отделен от
предрасходного, в котором размещены перекачивающий насос (с противоотливным
экраном) и датчик топливомера (с компенсатором и нижним сигналом выключения
насоса перекачки). Для сообщения предраходного отсека с расходным в нижней
части стенки нервюры № 36 установлен обратный клапан, который обеспечивает
перетекание топлива в сторону расходного отсека. В верхней части нервюры № 16 и
36 установлены поплавковый клапан и два предохранительных клапана,
отрегулированные на перепад давления 0,45 кГ/с. Поплавковый клапан предназначен
для того, чтобы перекрывать отверстие, сообщающее расходный отсек с
предрасходным, и тем самым исключать возможность перелива в главный бак
топлива, которое поступает в расходный отсек из магистралей перекачки.
Устройство поплавкового и предохранительного клапанов показано на рис.
15. Предрасходный отсек отделен от остальной части главного бака нервюрой № 34.
В стенке этой нервюры установлены струйный насос СН-7, два больших и четыре
малых обратных клапана. На верхней панели кессона, образующей верхнюю стенку
главного бака, установлена заливная горловина для заправки бака топливом
сверху, имеются чаши для установки поплавкового клапана системы заправки снизу
под давлением и четырех датчиков топливомера. На нижней панели кессона между
каждой парой нервюр выполнены 10 люков для подхода во внутренние объемы
главного бака. На крышке люка между нервюрами № 35-36 имеется кран слива топлива
из главного бака. Кроме того, на нижней панели кессона, в расходном и
предрасходном отсеках, установлены два крана для слива конденсата топлива. Во
внутренней полости главного бака смонтированы трубопроводы следующих
магистралей топливной системы: откачки топлива из дренажного бака, основного
дренажа баков 1Д, ГР, 2Г, 2Д, 2Р, дренажа бака ГГ, подачи топлива к двигателю
I, перекачки топлива из бака ГГ, перекачки топлива из баков 1Д и ГР,
дополнительного дренажа. На задней стенке бака (на заднем лонжероне крыла)
установлены четыре сигнализатора давления: между нервюрами № 28 и 29 -
сигнализатор СДУ2А-0.3 закрытия крана заправки, между нервюрами № 35 и 36 -
сигнализатор СДУ2А-0.3 работы кессона перекачки топлива, между нервюрами № 36 и
37, № 37 и 38 - два сигнализатора СДУЗА-0,6 работы насосов подкачки топлива.
Дополнительный бак первой группы расположен между нервюрами № 20 и 28 левой
ОЧК.
Нервюра № 28 отделяет дополнительный бак от главного бака группы, по
нервюрам № 20 и 19 производится стык ОЧК с СЧК. Предрасходный отсек бака 1Д
образован объемом крыла, заключенным между нервюрами № 27 и 28 и
соответствующими частями переднего и заднего лонжеронов, нижней и верхней
панелей кессона. Внутри предрасходного отсека установлены два топливных насоса
ЭЦНГ-10с76, перекачивающих топливо в расходный отсек главного бака. Нервюрой №
27 предрасходный отсек отделен от остального объема бака 1Д.
В нижней части стенки этой нервюры установлены шесть обратных клапанов,
обеспечивающих пополнение предрасходного отсека топливом по мере его
расходования. Внутренний объем бака, ограниченный с боков нервюрами № 20 и 27,
с помощью герметизированной нервюры № 24 разделен на две части. Одностороннее
перетекание топлива (в сторону предрасходного отсека) обеспечивается через семь
обратных клапанов в нижней части стенки нервюры
№ 24.На части нижней панели кессона крыла, составляющей нижнюю стенку
бака 1Д, выполнены восемь закрываемых крышками люков для подходов во внутренние
объемы бака. На крышке люка между нервюрами № 27 и 28 размещен кран слива
топлива из бака. На верхней панели бака установлена заливная горловина для
заправка топливом (между нервюрами № 20 и 21), а также установочные чаши под
поплавковый клапан системы заправки под давлением (нервюры № 20-21) и под пять
датчиков топливомера (нервюры № 21-22, 22-23, 25-26. 27-28). На задней стенке
бака (на заднем лонжероне крыла) размещены три фланца для крепления
сигнализаторов давления СДУ2А-0.3: один фланец (между нервюрами № 20 и 21) для
крепления сигнализатора закрытия кранов заправки и два фланца (между нервюрами
№ 27 и 28) для крепления сигнализаторов работы перекачивающих насосов
ЭЦНГ-10с76.
Рис. 14 Схема расположения топливных баков (отсеков) в кессонах крыла [8
Рис. 15 Внутрибаковые агрегаты
Резервный бак первой группы занимает объем кессона левой средней части
крыла (СЧК), ограниченный с боков нервюрами № 9 и 19. Нервюра № 9 отделяет бак
1Р от баков второй группы, по нервюре № 19 производится стык СЧК с отъемной
частью крыла (ОЧК). На верхней панели бака выполнены 14 люков для подхода
внутрь бака: 8 люков между передним и средним лонжеронами и 6 люков между
средними и задним лонжеронами крыла. Здесь же размещены заливная горловина
(между нервюрами № 9 и 10) и чаши под поплавковый клапан заправки (между
нервюрами № 9 и 10) и под четыре датчика топливомера (по одному между нервюрами
№ 12-13, 14-15 и два между нервюрами № 17-18). На нижней панели бака между
нервюрами № 18 и 19 установлены кран для слива топлива из бака и два крана для
слива конденсата. Между нервюрами № 10 и 11, № 17 и 18 на нижней панели
размещены фланцы, с помощью которых внутрибаковые магистрали подачи топлива
соединяются с магистралями, расположенными в пилонах двигателей 2 и 1. На
передней стенке бака установлены три перекрывшие топливных крана с
электромеханизмами МШ-13А-5: один кран кольцевания (между нервюрами № 11 и 12),
соединяющий магистрали подачи топлива к двигателям 1 и 2, и два пожарных крана
(между нервюрами № 9 и 10 двигателя 2, между нервюрами № 16 и 17 - двигателя
I). На задней стенке бака находятся три сигнализатора давления СД72А-0.3; между
нервюрами № 9 и 10 - сигнализатор закрытия кранов заправки, между нервюрами №
16-17 и № 18-19 - сигнализаторы работы перекачивающих насосов. Предрасходный
отсек бака ограничен частью нервюр № 16 и 19 и частью стенок среднего и заднего
лонжеронов. В предрасходном отсеке установлены два насоса перекачки топлива в
расходный отсек бака 1Г. Для сообщения предрасходного отсека с остальной частью
бака на участке стенки нервюры № 16, ограничивающей предрасходный отсек,
имеются четыре обратных клапана; на участке стенки среднего лонжерона,
ограничивающей предрасходный отсек спереди, - два малых и один большой обратные
клапаны [5].
Весь объем бака разделен на две части герметизированной нервюрой № 14.
Для сообщения этих частей в нижней части стенки нервюры установлены четыре
больших обратных клапана.
Топливные баки второй группы (баки двигателя 2) размещены в левой СЧК (баки
2Г и 2Д) и в центроплане крыла (бак 2Р). Главный бак второй группы занимает
герметизированный отсек СЧК, заключенный между нервюрами №4 и 9 (с боков)
передним и средним лонжеронами крыла. Часть бака, ограниченная с боков
нервюрами № 8 и 9, образует расходный отсек; часть, ограниченная с боков
нервюрами № 7 и 8, образует предрасходный отсек. Расходный отсек сообщается с
предрасходным с помощью одного большого и четырех малых обратных клапанов в
нижней части стенки нервюры № 8, двух предохранительных клапанов ( Р=О,45 кГ/см2)
и поплавкового клапана дренажа в верхней части нервюры № 8. С остальной частью
бака предрасходный отсек сообщается с помощью одного большого и трех малых
обратных клапанов, установленных в стенке нервюры № 7. В расходном отсеке бака
размещены два насоса ЭЦНГ-10с76 подкачки к двигателю 2, в предрасходном отсеке
- один насос ЭЦНГ-10с76, перекачивающий топливо в расходный отсек. Один из
насосов подкачки (установленный ближе к оси самолета) заключен в
противоотливной стакан, препятствующий отливу топлива от насоса при
отрицательных перегрузках. Второй насос подкачки и насос перекачки
предрасходного отсека заключены в экраны, препятствующие отливу топлива от
насосов при резком торможении самолета. Вне предрасходного отсека, между
нервюрами № 6 и 7, установлен топливный насос постоянного тока ЭЦН-14Б. На
верхней панели бака выполнены четыре люка для подхода в его внутренний объем, а
также установлены чаши, в которых размещены: заливная горловина и датчик
топливомера (между нервюрами № 4 и 5); поплавковый клапан и датчик-сигнализатор
уровня ДСМК-3 (между нервюрами № 4 и 5); по одному датчику топливомера (между
нервюрами № 6 и 7, № 7 и 8); два датчика топливомера (между нервюрами № 8 и 9).
На нижней панели бака установлены кран слива топлива (между нервюрами № 7 и 8)
и два крана слива конденсата (между нервюрами № 7 - 8 и № 8 - 9). На передней
стенке бака размещены пять сигнализаторов давления: между нервюрами № 4 и 5 -
СДУ2А-0.3 закрытия кранов заправки; между нервюрами № 7 я 8 - два СД72А-0.3 сигнализации
работы насоса перекачки топлива и насоса постоянного тока ЭЦН-14Б; между
нервюрами № 8 и 9 - два СДУЗА-0,6 сигнализации работы насосов подкачки топлива
к двигателям. Между нервюрами № 7 и 8 установлен перекрывной топливный кран
подачи топлива от насоса постоянного тока ЭЦН-14Б.
Дополнительный бак второй группы расположен сзади главного бака и
ограничен нервюрами № 4 и 9, стенкой среднего и стенкой заднего лонжеронов
крыла. Предрасходный отсек бака, в котором размещены два насоса ЭЦНГ-10с76,
ограничен нервюрами № 8 и 9. Для сообщения предрасходного отсека с остальной
частью бака в стенке нервюрами № 8 установлены четыре обратных клапана. На
верхней панели бака установлены чаши, в которых размещены: поплавковый клапан
заправки и датчик топливомера-между нервюрами № 4 и 5; заливная горловина-между
нервюрами № 5 и 6; по одному датчику топливомера-между нервюрами № 7 - 8 и № 8
- 9. Здесь же выполнены два люка подхода внутрь бака. На нижней панели между
нервюрами № 8 и 9 установлены кран слива топлива и кран слива конденсата. На
задней стенке бака размещены три сигнализатора СДУ2А-О,3: между нервюрами № 4 и
5 - сигнализатор закрытия крана заправки; между нервюрами № 8 и 9 - два
сигнализатора работы перекачивающих насосов.
Резервный бак второй группы располагается в центроплане крыла и занимает
объем кессона, ограниченный стенками переднего и заднего лонжеронов и нервюрами
№ 0 и 3. Стенкой среднего лонжерона бак разделен на две части, сообщение между
которыми осуществляется с помощью трех больших и четырех малых обратных
клапанов, установленных в нижней части стенки лонжерона. Предрасходный отсек
располагается в задней части бака и занимает отсек, ограниченный стенками
среднего и заднего лонжеронов, а также стенками нервюры № 2 и нервюры № 3. С
остальной частью бака предрасходный отсек сообщается через один большой и три
малых обратных клапана, установленных в стенке нервюры № 2. Не стенке нервюры №
2 установлен струйный топливный насос, перекачивающий топливо в предрасходный
отсек бака. На передней стенке бака между нервюрами № 1 и 2 размещен
перекрывной топливный кран (кран кольцевания) с электромеханизмом МПК-13А-5. На
задней стенке бака установлены три сигнализатора СДУ2А-0.3: между нервюрами № 0
и 1 - сигнализатор закрытия крана заправки и сигнализатор работы одного из
насосов перекачки, между нервюрами № 2 и 3 - сигнализатор работы второго насоса
перекачки топлива. На нижней панели бака между нервюрами № 2 и 3 находятся два
стакана, внутри которых размещаются насосы ЭЦНГ-10с76. Кран слива топлива из
резервного бака установлен на стакане одного из насосов перекачки топлива. На
верхней панели бака размещены: два датчика топливомера-между нервюрами № 0 и 1;
поплавковый клапан и датчик-сигнализатор уровня ДСМК-3 между нервюрами № 1 и 2;
заливная горловина и два датчика топливомера - между нервюрами № 2 и 3. На
верхней панели бака, в его передней и задней частях, выполнены два закрываемых
крышками лючка для подхода внутрь бака. Для перемещений внутри бака аналогичные
люки-лазы выполнены и в нервюрах № 1 и 2 (по два люка в каждой).
Топливные баки третьей группы конструктивно выполнены аналогично бакам
второй группы. Различия относятся к бакам ЗГ и 2Г и состоят в том, что в баке
ЗГ не устанавливается топливный насос постоянного тока ЭЦН-14Б и,
следовательно, нет сигнализатора работы насоса и перекрывного крана подачи
топлива от насоса. Топливные баки четвертой группы полностью аналогичны
топливным бакам первой группы.
2.2.2 Топливный насос ЭЦНГ -10с76
Электроприводной центробежный насос ЭЦНГ-10с76 является насосом внутрибакового
расположения. Привод насоса осуществляется электродвигателем мокрого типа
ЭТМ-100А, работающим на трехфазном переменном токе напряжением 200 В ± 5% и
частотой 400 + 2гц. Рабочее положение насоса - вертикальное, электродвигателем
вверх. Чередование фаз прямое.
Насос состоит из насосной части и электродвигателя, смонтированных как
одно целое. Насосную часть составляет корпус, улитка, крыльчатка и осевое
колесо. Электродвигатель к корпусу насоса крепится при помощи колпака и винтов.
Между корпусом и электродвигателем проложено уплотнительное резиновое кольцо. В
корпусе насоса запрессовано манжетное уплотнение, предотвращающее попадание
топлива в полость электродвигателя. Для обеспечения работоспособности
манжетного уплотнения при малом количестве топлива в баке (работа манжеты
всухую не допускается) в улитке и корпусе насоса предусмотрены специальные
каналы, подводящие топливо из улитки к манжетному уплотнению. Одновременно по
этим же каналам топливо подается в полость между колпаком и электродвигателем,
охлаждая электродвигатель независимо от уровня топлива в баке. Крыльчатка имеет
двухсторонний вход. Перед крыльчаткой со стороны нижнего входа установлено
осевое колесо.
На входе в насос расположены предохранительные сетки, не допускающие
попадания в насос крупных механических частиц. Для слива топлива в насосе
установлен сливной клапан. Топливо, которое просачивается через манжетное
уплотнение, отводится через дренажные каналы в корпусе насоса и в улитке.
Типовым креплением насоса является его крепление к установочному фланцу
топливного бака двенадцатью болтами через прижимное кольцо. Такое крепление
осуществлено во всех топливных баках, за исключением резервных баков двигателей
2 и 3, где насосы крепятся к стаканам топливных баков без применения прижимных
колец. При монтаже насоса на самолете под фланец насоса устанавливается
уплотнительная прокладка толщиной 1,5 мм из резины 3826, между выходным
штуцером насоса в переходным патрубком перекачивающей магистрали
устанавливается уплотнительное кольцо, поставляемое вместе с насосом.
Электропроводка двигателя насоса подключается к электрической сети
самолета с помощью клеммной колодки. Клеммные колодки перекачивающих насосов
баков 2Р и ЗР крепятся на приливах в нижней части установочных стаканов,
колодки насосов перекачки других баков устанавливаются в углублениях
установочных фланцев топливных баков и закрываются специальными крышками [7].
Так как перекачивающие насосы баков 2Р и ЗР размещены в закрытых отсеках
самолета, то у каждого из них предусмотрено специальное устройство для отвода
дренажируемого топлива за борт самолета, в связи с чем два болта крепления
каждого из этих насосов, используемые также для крепления скобы с
топливозаборным штуцером, отличаются от десяти других стандартных болтов.
Рис. 16 Топливный насос ЭЦНГ-10с76 [8]
Работа: Топливо из топливного бака поступает на крыльчатку через верхний и нижний
входы, при этой со стороны нижнего входа топливо вначале проходит через осевое
колесо. В каналах осевого колеса и крыльчатки давление топлива повышается, из
крыльчатки топливо подается в кольцевой сборник-улитку и далее в выходной
патрубок, на смазку манжетного уплотнения и на охлаждение электродвигателя [7].
Рис. 17 Схема работы топливного насоса [8]
.2.3 Дренажный бак
Дренажный бак занимает отсек кессона крыла, ограниченный нервюрами № 38 и
39 и передним и задним лонжеронами. Через герметизированную нервюру № 38 внутрь
бака выведена концы трех трубопроводов магистралей основного и дополнительного
дренажа и трубопровод перекачки топлива из дренажного бака. Магистраль
дополнительного дренажа со стороны бака заканчивается поплавковым и вакуумным
клапанами. Внутри дренажного бака размещены датчик-сигнализатор уровня ДСМК-3, закрепляемый
в чаше, расположенной на нижней поверхности бака, и внутрибаковая часть
патрубка воздухозаборника дренажа. Вне бака, в отсеке крыла между нервюрами №
39 и 40, размещены перекачивающий топливный насос ЭЦН-87, внешняя часть
воздухозаборника дренажа, топливный фильтр 8Д2.966.118 и сигнализатор давления
СДУ2А-0.2. На нижней панели дренажного бака имеется кран для слива остатков
топлива из бака, овальный люк для подхода в топливный отсек, люк для подхода к
датчику-сигнализатору уровня (между нервюрами № 38 и 39) в люк для подхода к
топливному фильтру (у нервюры № 40). На верхней панели бака выполнен люк
прямоугольной формы для подхода к трубопроводу дополнительного дренажа (у
нервюры № 38) и люк квадратной формы для подхода к топливному насосу (у нервюры
№ 39). Воздухозаборник дренажа состоит из трех патрубков: заборного, клапанного
и внутрибакового. Конец заборного патрубка, выведенный
Рис. 18 Дренажный бак [8]
под нижнюю панель крыла, имеет срез под углом 46° к направлению
набегающего в полете потока воздуха. В расточках четырех приливов клапанного
патрубка установлены три вакуумных клапана, и один предохранительный.
Вакуумные клапаны служат для сообщения дренажной магистрали с атмосферой,
если перекроется заборный патрубок и в надтопливном пространстве баков
образуется разрежение, предохраннтельный клапан сообщает дренажную магистраль с
атмосферой при повышении давления в магистрали. Внутрибаковый патрубок
воздухозаборника соединяется с клапанным фланцевым патрубком, установленным в
вырезе нижней часта стенки нервюры № 39. Второй конец внутрибакового патрубка
выведен в верхнею часть бака и закреплен на стенке нервюры № 38 с помощью
кронштейна и стяжного хомута. Для повышения взрывобезопасности дренажный бак
заполнен пенополиуретановыми блоками. Для обеспечения работоспособности
агрегатов, расположенных в дренажном баке в нем установлены ограждения,
отделяющие агрегаты от пенополиуретановых блоков [6],[7].
2.2.4 Топливный насос. Тип ЭЦН-87
Насос ЭЦН-87 является электроприводным центробежным топливным насосом
внебакового расположения, предназначенным для перекачки топлива,
скапливающегося в дренажном баке.
Привод насоса осуществляется электродвигателем МТ-25. На высотах полета
от 0 до 15000 м при наддуве бака до 0,06 атм насос обеспечивает
производительность перекачки 1200 л/час и перепад давления не менее 0,25
кГ/см2. Электродвигатель насоса работает на трехфазном переменном токе
напряжением 200 В +10%, частотой 400 + 8 гц, потребляемый им ток 0,28 А.
Топливный насос состоит из насосной части и электродвигателя МТ-25,
смонтированных совместно. Основными рабочими деталями насосной части являются
корпус, горловина и крыльчатка.
Корпус насоса служит одновременно сборником-улиткой. К нему со стороны
входа рабочей жидкости шестью шпильками крепится горловина. Между горловиной и
корпусом установлено резиновое уплотнительное кольцо для предотвращения течи
рабочей жидкости. Корпус и горловина образуют рабочую полость насоса, в которой
расположена восьмилопастная крыльчатка, установленная на валу электродвигателя,
являющимся одновременно и валом насоса. К корпусу насоса четырьмя шпильками
крепится электродвигатель. Для создания герметичности между полостями насоса и
электродвигателя в корпус насоса запрессована резиновая армированная манжета.
Чтобы предохранить электродвигатель от проникновения рабочей жидкости при
недостаточной герметичности манжеты, в насосе установлены центробежный
отражатель, насаженный на вал, и втулка, образующая щелевой фильтр. Для отвода
в атмосферу рабочей жидкости, просочившейся через манжету, в корпусе насоса
выполнен дренажный канал и установлен дренажный штуцер. С рабочей магистралью
насос соединен штуцером, ввернутым в выходной патрубок корпуса. Крепится насос
к стенке дренажного бака через шесть отверстий во фланце горловины насоса.
Насос устанавливается на шпильки, ввернутые в фланец топливозаборного патрубка,
который приклепан к стенке нервюры № 39. Между фланцами насоса и
топливозаборного патрубка установлена уплотнительная резиновая прокладка.
Работа: При подаче напряжения на обмотку статора электродвигателя
Рис. 19 Топливный насос ЭЦН-87 [8]
начинает вращаться вал двигателя. Одновременно с валом вращается
крыльчатка насоса и сообщает топливу, поступающему к ней из дренажного бака,
окружную скорость. Под действием возникающих при этом центробежных сил топливо
через щелевой диффузор поступает в сборник-улитку, который заканчивается
выходным патрубком. В щелевом диффузоре и улитке за счет потери скорости кинетическая
энергия топлива преобразуется в статическое давление, с которым топливо
поступает в магистраль перекачки [7].
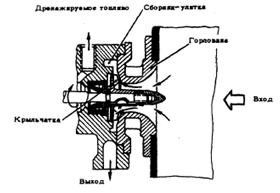
Рис. 21 Установка топливного насоса ЭЦН-87 [8]
.2.5 Сигнализатор давления. Тип СДУ2А-0.2
Сигнализатор давления СДУ2А-О.2 замыкает цепь питания насоса ЭЦН-87
(после его включения датчиком-сигнализатором уровня) и удерживает насос под
напряжением до полной перекачки топлива из дренажного бака.
На самолете установлены два сигнализатора (по одному на каждый дренажный
бак). Конструктивно сигнализатор состоит из литого основания с деталями,
чувствительного элемента и корпуса. Чувствительным элементом сигнализатора
является упругая мембранная коробка, которая состоит из двух сваренных между
собой по периметру мембран. Давление во внутреннюю полость коробки подводится
через трубопровод, проходящий в приемном штуцере. Для предохранения коробки от
разрушения при действии перегрузочного давления служит специальный упор,
ввернутый на резьбе в верхнюю часть кронштейна.
Контактное устройство сигнализатора состоит из нижней и верхней пружин с
контактами. Обе пружины смонтированы на кронштейне. Связь мембранной коробки с
нижней контактной пружиной осуществляется через изоляционный наконечник и шток,
который свободно перемещается во втулке, запрессованной в отверстие упора.
Контактные пружины с помощью гибких проводников соединяются с клеммами
штепсельной вилки. Положение контактов в нерабочем состоянии сигнализатора
СДУ2А-0.2 (как и всех сигнализаторов этого типа с индексом "А") -
нормально-разомкнутое.
Рис. 22 Сигнализатор давленияСДУ2А-0.2 [8]
Работа: Действие сигнализатора основано на функциональной зависимости между
имеющимся давлением в системе и упругими деформациями чувствительного элемента.
После включения насоса ЭЦН-87 датчиком-сигнализатором уровня в трубопроводе
откачки топлива из дренажного бака возникает давление. Это давление передается
во внутреннюю полость мембранной коробки, вызывая ее деформацию. Перемещение
верхней мембраны коробки передается через шток на нижнюю пружину контактного
устройства, в результате чего зазор между контактами верхней и нижней пружин
уменьшается.
Рис. 23 Принципиальная схема работы сигнализатора давления [8]
Когда давление достигает 0,2 кГ/см2, контакты пружин
замыкаются, замыкается цепь питания постоянным током контактора включения
насоса и цепь зеленой лампы сигнализации работы насоса. При падении давления в
трубопроводе ниже 0,2 кГ/см2 после окончания перекачки топлива
уменьшается прогиб мембраны чувствительного элемента, шток освобождает нижнюю
пружину и контакты пружин размыкаются. Одновременно выключается насос и гаснет
зеленая сигнальная лампа [5].
2.2.6 Топливный фильтр. Тип 8Д2. 966.118
Фильтр предназначен для очистки топлива от механических частиц размером
более 40 мк. Максимальный расход топлива - 1500 л/час. Максимальное рабочее
давление 40 кГ/см2. Гидравлическое сопротивление фильтра при расходе
топлива 1500 л/час и температуре окружающей и рабочей среды +25°С - не более
0,15 кГ/см2.
Фильтр состоит из крышки, стакана, фильтроэлемента и сливного крана.
Соединение стакана с крышкой и сливного крана со стаканом - резьбовое, разъемы
между ними уплотнены резиновыми кольцами. Крышка имеет входное и выходное
отверстия, в которые вворачиваются штуцера. Внутри крышки расположено
уплотнительное кольцо, предназначенное для обеспечения герметичности между
крышкой и фильтроэлементом. В верхней части крышки монтируется перепускной
клапан. Стакан фильтра цилиндрической формы, имеет резьбу для соединения с
крышкой, кольцевую канавку под уплотнительное кольцо, отверстие для сливного
крана и шестигранник под гаечный ключ. Во внутренней части стакана находится
пружина, которая поджимает фильтроэлемент к крышке. Фильтроэлемент -
двухслойный гофрированный цилиндр, внутри которого помещен металлический
каркас. Внутренняя сетка цилиндра - каркасная, наружная сетка - фильтрующая.
Сверху к цилиндру приварен фланец, которым фильтроэлемент вставляется в крышку,
снизу приварено днище. При монтаже на самолете фильтр устанавливается на две
шпильки, ввернутые в специальный кронштейн на стенке нервюры № 40.
Рис. 24 Топливный фильтр 8Д2.966.118 [8]
Рис. 25 Установка топливного фильтра [8]
Работа: В процессе работы топливо поступает во входную полость крышки, затем во
внутреннюю полость стакана. Проходя через фильтрующую сетку, топливо очищается
от механических примесей, затем поступает во внутреннюю полость фильтроэлемента
и выходит в выходную полость крышки [7].
При засорении фильтра, когда перепад давления на фильтроэлементе будет
равен 0,5+0.2» кГ/см2, открывается перепускной клапан и топливо,
минуя фильтроэлемент, из входной полости крышки поступает в ее выходную
полость.
.2.7 Насос. Тип РНМ-1
Ручной насос мембранного типа РНМ-1 служит для откачки конденсата из
топливных баков самолета. Насос обеспечивает производительность не менее 9
л/мин при 100 двойных ходах рукоятки. Давление, создаваемое насосом, 1-1,4
кГ/см2.
Насос состоит из корпуса, крышки, узла мембраны, рукоятки, а также
всасывающего, нагнетающего и редукционного клапанов. Узел мембраны составляет
три слоя мембранного полотна, заключенные между двумя дисками. Мембраны
скреплены с дисками болтом и гайкой с замком. Мембрана зажата между корпусом и
крышкой восемью болтами и служит одновременно уплотнением разъема. Рукоятка
насоса, приводящая мембрану в колебательное движение, соединена с мембраной при
помощи двуплечего рычага. Средняя часть рычага закреплена на оси в крышке
насоса. Один конец рычага надет на ось болта мембраны (в его нерезьбовой
части), второй конец с помощью шлиц соединен с рукояткой. На дне корпуса насоса
в цилиндрических расточках расположены узлы всасывающего, нагнетающего и
редукционного клапанов. Конструкция клапанов принципиальных различий не имеет и
включает в себя: корпус клапана, который фиксируется в корпусе насоса разрезным
стопорным кольцом; тарелку, притертую к седлу корпуса клапана; пружину,
прижимающую тарелку к седлу корпуса клапана; пружинодержатель; прокладки.
Детали всасывающего и нагнетающего клапанов полностью взаимозаменяемы.
Для крепления насоса на обшивке обтекателя шасси предусмотрен специальный
кронштейн, установленный с помощью четырех болтов. Насос крепится тремя
болтами, вворачиваемыми в резьбовые гнезда с торцевой стороны насоса. Под
головки болтов устанавливаются контровочные шайбы, на верхний болт (удлиненный)
устанавливается распорная втулка для увеличения жесткости крепления.
Для подключения к насосу трубопровода самолетной магистрали слива
конденсата в его входной патрубок вворачивается конусный переходник и штуцер. В
выходной патрубок насоса вворачивается второй конусный переходник, который
служит для установки крана слива, управляемого вручную.
Рис. 26 Насос
РНМ-1 [8]
Работа: Для откачки топлива из бака необходимо сделать несколько двойных ходов
рукояткой насоса. При движении рукоятки в одну сторону происходит открытие
всасывающего клапана и объем насоса, заключенный между мембраной и дном
корпуса, заполняется топливом. По окончании процесса всасывания всасывающий
клапан закрывается. При движении рукоятки в обратную сторону создающимся давлением
открывается нагнетающий клапан и топливо выталкивается в выходной патрубок. При
увеличении давления на выходе из насоса более 1-1,4 кГ/см2
открывается редукционный клапан и излишек топлива перепускается на линию
всасывания [5,7].
.2.8 Электрокран слива конденсата
Кран служит для поочередного сообщения с ручным насосом РНМ-1 шести
магистралей слива конденсата из топливных баков одного полукрыла. Кран
кулачкового типа с дистанционным управлением, семиходовой (шесть рабочих и одно
закрытое положение). Вращение кулачка крана осуществляется электромеханизмом
МПР-ЗБ, а остановка его в определенном положении - с помощью блока
микровыключателей ПКМ7-1.
Основными частями крана слива конденсата являются: клапанный механизм,
электромеханизм МПР-3, блок микровыключателей ПКМ7-1, соединительные детали
(переходный фланец, кронштейн крепления электромеханизмов).
Клапанный механизм крана состоит из корпуса, штуцерной крышки, шести
клапанов и валика с кулачком. Корпус клапанного механизма отливается из сплава
Ал9-Т4. Задняя часть корпуса пустотелая и служит сливной камерой крана. Для
отвода топлива от сливной камеры в ее боковой стенке имеется конусное отверстие
с резьбой, в которое вворачивается штуцер для присоединения трубопровода. В
центральную расточку днища сливной камеры запрессована бронзовая втулка,
являющаяся одной из опор клапанного механизма. В передней части корпуса
выполнены шесть гнезд, сообщающихся со сливной камерой крана. В гнездах
размещаются клапаны крана. Клапаны механизма цилиндрической формы. Цилиндрическая
часть клапана пустотелая, на ее боковой поверхности выполнены три сквозных окна
овальной формы. В проточку цилиндрической части клапана завулканизирована
резиновая прокладка, через которую клапан прижимается к седлу. Штоки клапанов
выведены в сливную камеру. На средней части штока каждого клапана установлена
пружина, прижимающая клапан к седлу. Для ограничения боковых отклонений штоков
при набегании на них кулачка механизма концы штоков размещены в направляющих
сверлениях, выполненных в шести приливах на внутренней стенке сливной камеры.
Свободные концы штоков клапанов, на которые воздействует кулачок механизма,
сферические.
Рис. 27 Электрокран слива конденсата [8]
Валик клапанного механизма выполнен из стали. В средней части валика
имеется поясок с резьбой, на которую наворачивается и контрится отгибной
пластиной кулачок. В передней части валика имеется пружина, служащая для выбора
люфтов валика с тем, чтобы исключить возможность упора движущегося кулачка в
боковую поверхность штока какого-либо клапана. На задней часта валика, за
задней опорой, установлена шестерня с 40 зубьями, через которую приводится во
вращение валик блока микровыключателей. Шестерня крепится шплинтом,
установленный в сквозное сверление в валике и ступице шестернии. В торцевой
части валика сделан паз для соединения с выходным валом электромеханизма
МПР-ЗБ.
Корпус клапанного механизма спереди закрывается крышкой, в которую
ввернуты шесть штуцеров для присоединения трубопроводов подвода топлива из
топливных баков. Соединяется штуцерная крышка с корпусом механизма двенадцатью
болтами через переходный фланец с тремя проушинами, служащий для крепления
крана слива на самолете. Для обеспечения правильного монтажа трубопроводов
штуцера крышки пронумерованы цифрами от 1 до 6.
Для того, чтобы при установке крана обеспечить совпадение штуцеров с
соответствующим гнездом клапанного механизма, верхняя часть крышки отмечена
надписью «Верх». Аналогичная надпись нанесена на фланце корпуса клапанного
механизма. Для установки электромеханизма. МПР-ЗБ и блока микровыключателей
ПКМ7-1 к заднему фланцу корпуса клапанного механизма крепится кронштейн, во
внутренней полости которого имеется расточка, являющаяся второй опорой валика
клапанного механизма, в кольцевые канавки расточки установлена фторопластовая
шайба и два резиновых уплотнительных кольца. На задний фланец кронштейна
установлена крышка с двумя отверстиями для прохода валов блока
микровыключателей и электромеханизма МПР-ЗБ.
В блоке микровыключателей ПКМ7-1 расположены семь пар нормально замкнутых
контактов. Шесть пар контактов соответствуют шести магистралям слива топлива и
клапанам крана; седьмая пара определяет закрытое положение крана. На валу блока
с помощью шлицевого соединения равномерно по окружности установлены семь
кулачков соответственно каждой паре контактов. Привод вала блока осуществляется
шестерней, находящейся в зацеплении с шестерней, клапанного механизма.
Семиходовой кран слива конденсата устанавливается на стенке хвостовой части
нервюры № 6 СЧК и крепится к ней через проушины переходного фланца тремя
болтами с самоконтрящимися гайками.
Работа: В нерабочем положении крана, когда переключатель управления установлен в
позицию «ЗАКР» кулачок клапанного механизма находится между штоками клапанов,
соответствующих штуцерам 1 и 6 (или между штоками клапанов соответствующих
магистралям слива из баков 1Р и 2Р в левом полукрыле, или магистралям слива из
баков ЗР и 4Р в правом полукрыле). В блоке микровыключателей один из кулачков
размыкает пару контактов, соответствующих закрытому положению крана; остальные
контакты находятся в замкнутом положении. При установке переключателя в одно из
рабочих положений напряжение бортовой сети по отдельной цепи, через включенную
в эту цепь пару контактов блока микровыключателей, поступит на обмотку
электромеханизма МПР-ЗБ. Электромеханизм приходит во вращение и начинает
проворачивать валик и кулачок клапанного механизма крана. Одновременно
проворачивается и валик блока микровыключателей. Поворот будет происходить до
момента, когда соответствующий кулачок блока разомкнет контакты, через которые
подается питание на обмотку электромеханизма. В результате электромеханизм
остановится в таком положении, при котором кулачок клапанного механизма отожмет
от седла клапан, соответствующий той магистрали слива, которая выбрана
переключателем. Через открывшийся клапан выбранная магистраль соединится со
сливной камерой клапанного механизма. В этом положении производится откачка
конденсата топлива из выбранного бака. По окончании откачки переключатель
управления переводится в положение "Закр", механизм срабатывает как и
при установке переключателя в рабочее положение и возвращается в исходное
(нерабочее) положение [7.].
.2.9 Нажимной кран слива конденсата
Кран предназначен для слива конденсата из топливных и дренажных баков и
состоит из корпуса, клапана и крышки. Корпус крана представляет пустотелый
цилиндр с окнами для прохода топлива и фланцем у основания. На внутренней
стенке цилиндра (вверху) выполнена резьба для заворачивания крышки. Во фланце
корпуса имеются четыре отверстия, через которые производится крепление крана в
топливном баке. Расточка в центральной части основания корпуса является седлом
клапана крана. Клапан в собранном виде состоит из штока, пружины, которая
надевается, на шток, резиновой уплотнительной шайбы и болта, которым шайба
крепится к штоку. Клапан устанавливается внутрь корпуса крана таким образом,
что резиновая шайба ложится на седло в корпусе крана. Сверху в корпус крана
вворачивается крышка, которая является опорой пружины клапана и направляющей
его штока.
Рис. 28 Нажимной кран слива конденсата [8]
Кран устанавливается в топливном баке с помощью стакана, упора и гайки.
Крепежный стакан помещается в вырез на нижней панели бака. Изнутри бака на
стакан устанавливается упор и наворачивается гайка. Для обеспечения
герметичности между фланцем стакана и нижней поверхностью панели бака
прокладывается резиновая прокладка. Во внутренних приливах стакана выполнены 4
резьбовых сверления для болтов крепления крана слива конденсата. Под головки
болтов крепления крана устанавливаются контровочные шайбы, под фланец корпуса
крана - резиновая уплотнительная прокладка.
Работа: Открытие крана и слив конденсата производятся с помощью приспособления 9910-910.
Для этого упор приспособления вводится в сферическую выемку болта клапана и
производится отжатие клапана от седла корпуса крана. При этом топливо через
окна в корпусе вытекает из бака и по трубе приспособления стекает в какую-либо
емкость [5,7].
Рис. 29 Приспособление для слива конденсата [8]
.2.10 Бортовой штуцер заправки топливом под давлением
Штуцер представляет собой стандартный узел, служащий для присоединения
стандартного наконечника шланга от наземного топливозаправщика. Штуцер имеет
клапан, который герметично закрывает входное отверстие, когда наконечник
заправочного шланга отсоединен. Штуцер состоит из литого алюминиевого корпуса,
клапана и крышки. Посадочные места корпуса механически обработаны. К нижней
части корпуса крепится восемью винтами стальной фланец, который используется
как седло клапана. Фланец имеет три выступа для крепления и удержания
наконечника топливного шланга. Соединение фланца с корпусом уплотняется
резиновым кольцом. В верхней части корпуса имеется направляющая клапана,
выполненная как одно целое с корпусом и поддерживаемая тремя ребрами. В
отверстие направляющей запрессована стальная втулка. Клапан удерживается на
своем седле пружиной. Для повышения герметичности соединения на тарелке клапана
установлено уплотнительное кольцо. В нерабочем положении входное отверстие
штуцера закрыто крышкой, которая предохраняет штуцер от загрязнения и утечки
топлива. Крышка в сборе состоит из корпуса крышки и фланца с винтом и ручкой.
Корпус крышки имеет вырезы, позволяющие надеть ее на фланец штуцера. Отверстие
в центре корпуса крышки служит направляющей для винта. Винт одной стороной
завальцован во фланец. Ручка на другом конце винта позволяет плотно прижать
фланец к штуцеру. Для повышения герметичности соединения на фланце установлено
уплотнительное кольцо. Открытая крышка удерживается на цепочке, другой конец
цепочки закреплен в ушке под одним из болтов крепления.
Работа: При повороте ручки на крышке штуцера против часовой стрелки фланец
освобождается и позволяет снять крышку со штуцера. При присоединении
стандартного наконечника шланга топливозаправщика и повороте его рукоятки
вправо выдвигается клапан наконечника, который нажимает на клапан штуцера и
открывает его, давая возможность топливу поступать в систему заправки cамолета
[5,7].
Рис. 30 Бортовой штуцер заправки топливом под давлением [8]
2.2.11 Магистральный кран заправки
Магистральный кран является перекрывным краном и устанавливается в
магистральном трубопроводе системы централизованной заправки на участке между
бортовыми штуцерами заправки и электрогидравлическими клапанами топливных
баков. Кран управляется дистанционно, имеет поворотную заслонку, перемещающуюся
на угол 90° с помощью электромеханизма МПК-9. Диаметр проходного сечения крана
100 мм, рабочее давление до 8 кГ/см2.
Основные детали крана - корпус с патрубком, валик, заслонка и
электромеханизм МПК-9. Корпус крана, отлитый из алюминиевого сплава АЛ9-Т4,
имеет фланец для соединения с трубопроводом, отводящим топливо от крана, и
фланец для крепления электромеханизма МПК-9. Со стороны входа топлива на
внутренней поверхности корпуса имеется резьба для вворачивания патрубка.
Патрубок, выполненный из стальной трубы, имеет фланец для соединения крана с трубопроводом,
подводящим топливо к крану. Патрубок фиксируется контргайкой, которая, в свою
очередь, контрится проволокой. Под контргайку установлено резиновое
уплотнительное кольцо. Внутренняя поверхность части патрубка, входящей в
корпус, имеет сферическую форму, притерта и отхромирована. К этой поверхности
заслонка прилегает при закрытом положении крана. Поверхность заслонки, которой
она соприкасается с патрубком, сферическая. Для обеспечения герметичности по
внешнему контуру заслонки с помощью прижимной шайбы установлена уплотнительная
резиновая мембрана. С помощью двух проушин заслонка устанавливается на валике
крана. Валик выполнен ив стали, имеет два пояска под проушины заслонки. На
одном пояске имеется лыска под шпонку для фиксации заслонки. Одним концом валик
соединяется с помощью шлицев с выходным валом электромеханизма МПК-9. На эти же
шлицы устанавливается упор, ограничивающий угол поворота валика и заслонки.
Опорами валика являются втулки из сплава БрАЖМц, установленные на резьбе в
расточки корпуса крана. Для предохранения электромеханизма от попадания в него
топлива в двух кольцевых канавках валика проложены резиновые уплотнительные
кольца. Для отвода топлива, просачивающегося через уплотнение валика, в корпусе
крана имеются отверстия с резьбой, в одно из которых ввернут штуцер для
присоединения топливоотводящей трубки (второе отверстие заглушено).
Рис. 31 Магистральный кран заправки [8]
Электромеханизм МПК-9 крепится к фланцу корпуса крана четырьмя болтами.
Между ними устанавливается шайба, с помощью которой регулируется осевой люфт
валика крана. Основными узлами электромеханизма являются реверсивный
электродвигатель постоянного тока Д-75ТМ, планетарный редуктор, фрикционная
муфта, блок концевых выключателей и штепсельный разъем. На наружную поверхность
корпуса, окрашенную желтой эмалью, нанесены номер чертежа крана (6154.100.00) и
стрелка, указывающая направление прохода топлива через кран. Кран соединяется с
трубопроводами магистрали заправки и крепится к конструкции самолета с помощью
двух стяжных кронштейнов, отлитых из алюминиевого сплава АЛ9-Т4. Нижняя часть
кронштейна крепятся к конструкции самолета, верхняя часть - съемная. Обе
половины кронштейна соединяется стяжными болтами. Углубления во внутренней поверхности
обеих половин кронштейна имеют наклонные боковые поверхности, которые
обеспечивают необходимое для герметичности соединения натяжение между фланцами
крана и трубопроводов. Между фланцами крана н трубопроводов устанавливаются
прокладки [5,7].
Рис. 32 Установка магистрального крана заправки [8]
Работа: Реверсивный электродвигатель поворачивает выходной вал электромеханизма в
одном или другом направлении в зависимости от того, на какую обмотку будет
подано напряжение. Одновременно с ним поворачивается находящийся в зацеплении
валик крана, который поворачивает заслонку на открытие или закрытие канала, по
которому топливо подводится к крану. В крайних положениях электромеханизм
замыкает концевые выключатели, через которые напряжение подается на включение
сигнальных ламп открытого или закрытого положения крана.
.2.12 Электрогидравлический клапан заправки
Электрогидравлический клапан заправки предназначен для сообщения (и
разобщения) магистрали заправки самолета топливом с внутренним объемом
топливного бака. Клапан имеет дистанционное комбинированное управление:
основное - при помощи электромагнита 921.000Н-Т и дополнительное - от
поплавкового клапана, автоматически прекращающего заправку при достижении
определенного уровня топлива в баке. Рабочее давление клапана - до 8 кГ/см2;
продолжительность непрерывной работа электромагнита под током - до 90 мин;
нормальное напряжение питания электромагнита - 27+2,7В; максимальный ток при
включении - не более 10 А, ток удержания - не более 0,5 А.
Основные детали электрогидравлического клапана заправки - корпус,
клапан-поршень, клапан-демпфер, узел управляющего клапана с сальниковым
устройством, электропривод управления. В передней части корпуса клапана имеется
цилиндрический входной патрубок, на наружной поверхности которого выполнены две
кольцевые канавки под уплотнительные кольца. В боковой поверхности корпуса
выполнены четыре овальных окна слива. В задней части корпуса имеется фланец с
двенадцатью отверстиями для крепления электрогидравлического клапана на
самолете и крепления крышки корпуса.
Внутри корпуса размещается клапан-поршень, состоящий из соединенных между
собой на резьбе клапана грибкового типа и поршня. В проточку грибковой части
клапана завулканизирована резиновая прокладка, которой клапан-поршень опирается
на седло входного патрубка. В задней части клапана-поршня, в канавке фланца
поршня с помощь вкладыша и гайки установлена резиновая манжета, создающая
уплотнение между поршнем и корпусом. В грибковой части клапана-поршня выполнены
шесть отверстий для подвода топлива к клапану-демпферу. В цилиндрической части
клапана-поршня выполнены четыре окна для отвода топлива, перепускаемого
клапаном-демпфером.
Клапан-демпфер размещается во внутренней полости клапана-поршня. Его
пустотелый шток перемещается в расточке выступающей передней части днища
поршня. Открытый в торцевой части конец штока выходит в полость
электрогидравлического клапана, находящуюся за поршнем. Для обеспечения
герметичности в кольцевых канавках расточки поршня установлены два
уплотнительных резиновых кольца. Тарелка клапана-демпфера усилием пружины
прижимается через привулканизированную прокладку к седлу в передней части
грибкового клапана (со стороны его внутренней полости). В центральной части
тарелки клапана-демпфера выполнено дроссельное отверстие диаметром 8 мм, через
которое внутренняя полость входного патрубка постоянно сообщается с полостью
клапана, находящейся за поршнем.
На фланце в задней части корпуса электрогидравлического клапана
установлена и закреплена шестью болтами крышка. Между крышкой и
клапаном-поршнем (в полости за поршнем) установлена пружина, усилием которой
клапан-поршень прижимается к седлу входного патрубка клапана. В крышке
выполнены каналы и установлен штуцер, по которым топливо из полости за поршнем
электрогидравлического клапана отводится через поплавковый клапан в верхнее
свободное от топлива пространство топливного бака.
Во внутреннюю расточку крышки на резьбе ввернут узел управлявшего клапана
с сальниковым устройством. Управлявший клапан разобщает и сообщает сливные
каналы в крышке. Клапан с помощью штифта соединяется со штоком, который вторым
концом связан с якорем электромагнита. Для предохранения электромагнита от
попадания топлива шток управлявшего клапана помешается в специальное
сальниковое устройство, состоящее из корпуса, манжеты, шайбы, втулки, пружины и
гайки. Корпус сальника имеет фланец четырехугольной формы, на который
устанавливается электромагнит. В кольцевую канавку фланца корпуса сальника
устанавливается уплотнительное резиновое кольцо.
При монтаже электрогидравлического клапана на самолете его внутрибаковая
часть помещается внутри специального корпуса, укрепленного со стороны
топливного бака на стенке заднего лонжерона крыла. Внутрибаковый корпус имеет
два патрубка - для подвода к клапану топлива от магистрали заправки и отвода от
него топлива в бак. Для обеспечения герметичности между наружной поверхностью
входного патрубка электрогидравлического клапана и внутренней поверхностью
входного патрубка внутрибакового корпуса в кольце вне канавки входного патрубка
клапана устанавливаются два уплотнительных кольца. Крепится
электрогидравлический кран к стенке заднего лонжерона шестью болтами, которые
вворачиваются в резьбовые гнезда, выполненные в установочном корпусе. Под
головки болтов устанавливаются шайбы, головки всех шести болтов контрятся общей
проволокой. Под фланец электрогидравлического клапана прокладывается резиновая
прокладка. На стенке заднего лонжерона рядом с электрогидравлическим клапаном
наносится его номер в соответствии с электросхемой управления заправкой.
Рис. 33 Электрогидравлический клапан заправки [8]
Работа: При подаче напряжения на обмотку электромагнита якорь под действием
электромеханических сил отводит от седла клапан, управляющий сливом топлива из
полости за поршнем. При этом поршень остается прижатым к своему седлу лишь
усилием пружины, расположенной в полости за поршнем. Открывается клапан-поршень
под воздействием давления топлива, возникающего в магистрали заправки,
соединенной со входным патрубком клапана. При этом клапан-поршень перемещается
назад, сжимая пружину, и открывает сливные окна, сообщая заправочную магистраль
с полостью топливного бака. Одновременно некоторое количество топлива через отверстия
в грибковой головке клапана-поршня и дроссельное отверстие в клапане-демпфере
заполняет полость за поршнем и уходит по каналам крышки в топливный бак через
сливной штуцер, сливную трубку и поплавковый клапан заправки.
При снятии напряжения с обмотки электромагнита якорь под действием
пружины прижимает управляющий клапан к его седлу, разобщая сливные каналы в
крышке корпуса клапана. Слив топлива из полости за поршнем в бак прекратится,
давление за поршнем выравнивается с давлением топлива на входе в электрогидравлический
клапан. Вследствие этого клапан-поршень под действием усилия пружины
переместится вперед и перекроет входной канал. После соприкосновения с седлом
клапан дополнительно прижмется к седлу силой гидравлического давления за счет
разности площадей сечений поршня и входного отверстия. Если в процессе заправки
электрическое управление не срабатывает, при достижении определенного уровня
топлива в баке слив топлива из полости за поршнем будет прекращен поплавковым
клапаном установленным в конце магистрали слива. Закрывается
электрогидравлический клапан при этом так же, как и при электрическом
управлении.
В случае резких скачков давления в магистрали заправки (выше 9 кГ/см2)
при закрытом электрогидравлическом клапане топливо через отверстия в грибковой
головке клапана-поршня поступает к клапану-демпферу, отжимает его от седла,
проходит во внутреннюю полость клапана-поршня и сливается через сливные окна на
его цилиндрической части [5,7].
.2.13 Поплавковый клапан заправки
Поплавковый клапан заправки перекрывает магистраль слива топлива из
полости за поршнем электрогидравлического клапана заправки при достижении
определенного уровня топлива в баке.
Поплавковый клапан заправки состоит из корпуса, крышки и поплавкового
устройства. В приливах под фланцем корпуса установлены девять самоконтрящихся
гаек для крепления к нему крышки и самого клапана к топливному баку. В нижнюю
расточку корпуса ввернут и законтрен контргайкой угольник для крепления трубки,
подводящей топливо от электрогидравлического клапана. В верхнюю расточку
корпуса входит цилиндрическая часть крышки клапана с расточкой, являющейся
продолжением расточки корпуса. Между корпусом и цилиндрической часть на кране
установлены два уплотнительных кольца. В боковом приливе центральной части
крана просверлен канал, выводящий топливо в топливный бак. На боковой
поверхности центральной части крышки имеются две проушины, через которые с
крышкой соединяется поплавковое устройство и устанавливается ось,
ограничивающая опускание поплавка.
Поплавковое устройство состоит из поплавка, рычага и управляющего
клапана. Поплавок выполнен из пенопласта ПХВ-1. Сквозь среднюю часть поплавка
проведена и развальцована по концам трубка, через которую проходит ось,
соединяющая поплавок с рычагом. Рычаг передним концом соединяется с проушинами
крышки. Между боковинами рычага, в передней части имеется перемычка с резьбовым
отверстием, в которое вворачивается управляющий клапан, перекрывающий выходной
топливный канал крышки.
Рычаги поплавковых клапанов по форме выполнены двух видов - прямые (в
баках 2Р и ЗР) и с изгибом (в остальных баках).
Управляющий клапан фиксируется в перемычке контргайкой, наворачиваемой на
его шток. К тарелочке управляющего клапана привулканизирована резиновая
уплотнительная прокладка. Поплавковый клапан заправки устанавливается в
специальной чаше топливного бака, которая одновременно предназначена для
установки датчика топливомера. Корпус клапана устанавливается внутри бака и
крепится к фланцу чаши тремя болтами, пропущенными сверху. Между корпусом
клапана и фланцем чаши прокладывается резиновая прокладка. Крышка клапана
устанавливается сверху чаши и крепится к корпусу клапана шестью болтами. Между
фланцами крышки и чаши прокладывается уплотнительная прокладка.
Для исключения касания поплавков о стенки близрасположенных нервюр
поплавковые клапаны заправки в топливных баках ГГ (4Г), 1Р (4Р), 2Г (ЗГ)
устанавливаются так, что оси их поплавков составляют угол 10° с направлением
осей ребер верхнее панели крыла.
В баках 1Д (4Д), 2Д (ЗД), 2Р (ЗР) оси поплавков совпадают с направлением
осей близрасположенных ребер верхней панели крыла. Кроме того на поплавках в
баках 1Г (4Г),2Г (ЗГ), 2Д (ЗД) установлены ограничители, устраняющие вращение
поплавков.
Рис. 34 Поплавковый клапан заправки и его установка [8]
Работа: При уровне топлива в баке ниже максимально допустимой величины поплавок и
рычаг с управлявшим клапаном занимают такое положение, при котором выходное
отверстие бокового канала крышки открыто. При этом топливо, поступавшее из
полости за поршнем электрогидравлического клапана в процессе заправки, проходит
каналы корпуса, крышки и свободно сливается в топливный бак. Когда уровень
топлива достигает максимально допустимой величины, управляющий клапан
перекрывает выходное отверстие канала крышки и слив топлива из полости за
поршнем электрогидравлического клапана заправки прекратится и клапан закроется
[5,7].
.2.14 Топливный насос ЭЦН-14Б
Топливный насос ЭЦН-14Б предназначен для подачи топлива к двигателе
вспомогательной силовой установки. При отсутствии в бортовой сети самолета
напряжения переменного тока насос ЭЦВ-14Б может быть использован как
подкачивающий для запуска двигателей. ЭЦН-14Б является электроприводным
одноступенчатый центробежным насосом внутрибакового расположения. Приводом
агрегата служит электродвигатель МТП-18СИ2 смешанного возбуждения. Питается
электродвигатель от электросети самолета напряжением 27в +10в.
Агрегат ЭЦН-14Б состоит на насосной части и электродвигателя МТП-18СИ2,
смонтированных совместно. Основными деталями насосной части являются корпус,
крыльчатка и горловина. В корпусе насоса выполнены два канала, один для дренажа
топлива, которое может просочиться черев уплотнения, другой для вентиляции
полости электродвигателя и прокладки проводов.
Вход топлива в насос закрыт защитной латунной сеткой. Через отверстие в
центре корпуса насоса проходит вал электродвигателя. Для предотвращения
попадания топлива в электродвигатель на валу из рабочей полости насоса в
корпусе установлена и закреплена стопорным кольцом резиновая уплотнительная
манжета, на которую надета пружина.
Горловина насоса крепится к корпусу семью винтами. Одновременно с
корпусом горловина образует рабочую полость насоса, в которой расположена
крыльчатка. Крыльчатка имеет восемь лопаток. Вместе с регулировочными шайбами
крыльчатка неподвижно закреплена на валу электродвигателя шпонкой и гайкой.
Снизу насос закрывается крышкой, в которой установлена заглушка для слива
водного конденсата. Сверху на корпусе насоса с помощью крепежного кольца и
десяти винтов укреплен электродвигатель. На крепежном кольце установлен
обтекатель для создания специального профиля полости между колпаком
электродвигателя и внутрибаковым кожухом.
Электродвигатель МТП-18СИ2 состоит из корпуса, двух щитов, якоря и
защитного колпака. Корпус представляет собой стальной цилиндр с четырьмя
полюсами, на которые надеты катушки возбуждения. В щитах установлены
шарикоподшипники, в которых вращается якорь электродвигателя. На одном из щитов
расположены также четыре щеткодержателя для подвода тока к обмотке якоря через
коллектор, напрессованный на вал. К бортовой сети самолета электродвигатель
подключается при помощи свободно выступающих электропроводов.
Рис. 35 Топливный насос ЭЦН-14Б [8]
В топливном баке насос ЭЦН-14Б устанавливается в специальный кожух
укрепленный на нижней панели бака. В нижней части корпуса кожуха выполнены пять
окон для подвода топлива к насосу. В верхней части кожуха, в штуцере имеются
два канала: торцовый-для подачи топлива в магистральный трубопровод, боковой -
для отвода топлива к сигнализатору давления СДУ. Крепится насос через свой
фланец шестью болтами, вворачиваемыми в резьбовые футорки, установленные в
корпусе внутрибакового кожуха [5,7].
Работа: При подаче напряжения к электродвигателю приходит во вращение его вал и
одновременно неподвижно насаженная на вал крыльчатка насоса. Под действием
центробежных сил давление топлива, поступавшего из бака в рабочие каналы
крыльчатки, возрастает. Из каналов крыльчатки топливо попадает в направлявшую
полость с расширяющимся каналом, образованную в корпусе насоса. Здесь скорость
движения топлива уменьшается, а его давление повышается. Далее топливо
поступает в полость, образованную обтекателем, электродвигателем и
внутрибаковым кожухом. Из этой полости, играющей роль сборника-улитки, топливо
направляется в выходной патрубок, где также продолжает снижаться скорость
движения топлива и увеличиваться давление.
Рис. 36 Схема работы насоса ЭЦН-14Б [8]
.2.15 Блок электромагнитных кранов
Блок электромагнитных кранов состоит из двух кранов. Для подачи топлива к
ВСУ используется один из этих кранов, который в соответствии с электросхемой
имеет маркировку№ 364 а/ 5. Блок электромагнитных кранов объединяет перекрывные
краны магистралей подачи топлива к двигателю вспомогательной силовой установки
и к генератору нейтрального газа. В соответствии с электросхемой управления
краны имеют маркировку: № 364 а/ 5 - кран подачи топлива к двигателю ВСУ и №
364 б/5 - кран подачи топлива к генератору нейтрального газа.
Блок электромагнитных кранов состоит из корпуса, двух электроприводов и
двух отводящих штуцеров. Корпус блока, отлитый из алюминиевого сплава АЛ-9Т4,
имеет фланец овальной формы с восемью отверстиями для крепления на самолете. В
корпус на резьбе устанавливается два электропривода и два штуцера, к которым
присоединяются трубопроводы, отводящие топливо от блока. Отводящие штуцера
выполнены из алюминиевого сплава Д16Т. Каждый штуцер имеет резьбовую часть,
которой он вворачивается в корпус блока, резьбовую часть для присоединения
трубопровода и шестигранник под ключ.
Каждый из электроприводов блока состоит из электромагнита 921000А-Т и
клапанного узла. Конструктивно электропривод блока электромагнитных кранов
выполнен так же, как и электропривод электрогидравлического клапана заправки.
Для монтажа блока электромагнитных кранов в стенке переднего лонжерона
крыла сделан вырез, который со стороны топливного бака перекрывается фланцем,
приклепанным к стенке лонжерона. Внутрибаковый фланец имеет патрубок изогнутой
формы, к которому присоединяется трубопровод, подводящий топливо от магистрали
кольцевания. Блок электромагнитных кранов устанавливается на восемь шпилек,
ввернутых во внутрибаковый фланец.
Под корпус блока прокладывается резиновое уплотнительное кольцо, к
отводящему штуцеру присоединяется трубопровод топливной магистрали ВСУ (нижний
штуцер). Под корпус блока прокладывается резиновое уплотнительное кольцо, к
отводящим штуцерам присоединяются трубопроводы топливных магистралей ВСУ
(нижний штуцер) и ГНГ (верхний штуцер).
Рис. 37 Блок электромагнитных кранов [8]
Работа: При закрытом положении перекрывного крана клапан электропривода под
действием пружины перекрывает внутренний канал штуцера, отводящего топливо от
блока. При подаче напряжения на обмотку электропривода его якорь под действием
электромагнитных сил отходит от штуцера блока и соединяет магистраль подачи
топлива к двигателю ВСУ с магистралью кольцевания.
При закрытом положении перекрывных кранов клапаны электроприводов под
действием пружин перекрывают внутренние каналы штуцеров, отводящих топливо от
блока. При подачи напряжения на обмотку какого-либо электропривода его якорь
под действием электромагнитных сил отходит от соответствующего штуцера блока и
соединяет магистраль подачи топлива к двигателю ВСУ или к ГНГ с магистралью
кольцевания [5,7].
2.3
<C:\Users\Тарас\AppData\С флешки (14 Гб)\Академия (5,79 Гб)\Дипломники
(1,32Гб)\Дипломы (970 Мб)\Диплом РОГОВ\ДР рОГОВА В. В. -2013.ИЗМЕН.doc>Особенности
эксплуатации топливной системы самолета ИЛ-76
Автоматы
защиты сети - выключатели «Автомат, перекачка баков» выключены.
Не
включать питание бортовой электросети при включенных АЗС - выключателях
«Автомат, перекачка баков », так как в этом случае при небольшом количестве
топлива в резервных баках возможно включение насосов перекачки в дополнительных
баках, а при небольших количествах топлива в резервных и дополнительных баках -
преждевременное включение насосов перекачки в главных баках.
Исходное
положение
1.
Пожарные краны закрыты.
.
Сигнальные лампы пожарных кранов горят.
.
Насосы подкачки выключены.
.
Сигнальные лампы насосов подкачки не горят.
.
Краны кольцевания закрыты.
.
Сигнальные лампы кранов кольцевания не горят.
.
Насосы перекачки выключены.
.
Сигнальные лампы насосов перекачки не горят.
.
Сигнальная лампа «Включи перекачку» не горит.
.
Табло «Мин. давл. топлива» горит.
.
Табло «Топл. фильтр» и табло «Ост. топл. 2000 кг» не горят.
.
Насос подкачки постоянного тока выключен.
.
Лампы «Подкачка идет», «Кран открыт» и табло «Контроль ВСУ» не горят. 35
.
Переключатель топливомера «Показание в кабине - заправка» в положении
«Показание в кабине».
.
Галетный переключатель топливомера в положении «С».
.
Указатели топливомера «I двиг.», «II двиг.», «III двиг.», «IV двиг.», «Сумма»
указывают соответственно количество топлива в баках 1, 2, 3 и 4 двигателей и
суммарное количество топлива в системе.
Перед
запуском двигателей
Во
избежание выхода из строя манжетных уплотнений в топливных насосах не включать
насосы, если в баках нет топлива.
.
Проверить работу насосов перекачки. Насос перекачки топлива из левого
дренажного бака кратковременно включить и проверить, что загорелась сигнальная
лампа насоса перекачки. При отсутствии топлива в дренажном баке работу насоса
проверить на слух с кратковременным (до 3 с) включением насоса. 2. Выполнить
аналогичные операции для насосов перекачки топлива из правого дренажного бака и
тех топливных баков, в которые залито топливо.
.
Проверить работу насосов подкачки (непосредственно перед запуском). Второй
насос подкачки двигателя включить и проверить, что загорается сигнальная лампа
насоса подкачки. Выполнить то же для всех насосов подкачки.
.
Проверить работу кранов кольцевания: Левый кран кольцевания открыть и
проверить, что загорается сигнальная лампа крана кольцевания. Закрыть кран.
Аналогичное произвести для центрального и правого кранов кольцевания.
.
Проверить работу пожарных кранов (непосредственно перед запуском). Пожарный
кран двигателя № 1 открыть и проверить, что гаснет сигнальная лампа крана.
Аналогично проверить все пожарные крапы.
.
Проверить правильность показаний топливомера: а) указатель топливомера «Сумма»
показывает общее количество топлива в системе; б) галетный переключатель
топливомера установить в положении «Р». Проверить, что указатели топливомеров
«I двиг.», «II двиг.», «III двиг.», «IV двиг.» показывают соответственно
количество топлива в баках IP, 2Р, 3Р, 4Р; в) галетный переключатель
топливомера установить последовательно в положения «Д», «Г», «С». Проверить,
что указатели топливомеров «I двиг.», «II двиг.», «III двиг.», «IV двиг.»
указывают соответственно количество топлива: в баках 1Д, 2Д, 3Д и 4Д при
установке переключателя в положение «Д», в баках 1Г, 36 2Г, 3Г, 4Г при
установке переключателя в положение «Г», суммарное количество топлива на
двигатель 1, 2, 3, 4 при установке переключателя в положение «С».
.
Проверить работоспособность измерительной части топливомера; а) кнопку «Н»
указателя топливомера «Сумма» нажать и проверить, что стрелка указателя «Сумма»
перемещается к нулевой отметке; б) кнопку «Р» указателя «Сумма» нажать и
проверить, что стрелка указателя «Сумма» перемещается к максимальной отметке;
в) аналогично проверить остальные указатели топливомеров, поочередно устанавливая
галетный переключатель в положения «Р», «Д», «Г» и «С».
.
Если при запуске двигателей возникает необходимость использовать подкачивающий
насос постоянного тока, то его включение и открытие перекрывного крана
топливной магистрали ВСУ производить с панели управления ВСУ:
а)
главный тумблер включить и проверить, что табло «Кран открыт» загорается; б)
выключатель «Насос подкачки» двигателей и ВСУ установить в верхнее положение и
проверить, что табло «Подкачка идет» загорается.
После
запуска первого двигателя (двигатель № 2) включить основные подкачивающие
насосы, после чего выключить подкачивающий насос постоянного тока и закрыть
перекрывной кран топливной магистрали ВСУ.
После
запуска двигателей
1.
Включить перекачку топлива: а) если заправлены только главные баки всех
двигателей, включить насосы перекачки баков 1Г, 2Г, 3Г, 4Г. б) если заправлены
главные баки всех двигателей и дополнительные баки крайних двигателей, включить
насосы перекачки баков 1Д, 2Г, 3Г, 4Д; в) если заправлены главные и
дополнительные баки всех двигателей, включить насосы перекачки баков 1Д, 2Д,
3Д, 4Д; г) если заправлены главные и дополнительные баки всех двигателей и
резервные баки крайних двигателей, включить насосы перекачки баков IP, 2Д, 3Д,
4Р; д) если заправлены главные, дополнительные и резервные баки всех
двигателей, включить насосы перекачки баков IP, 2P, 3Р, 4Р. После включения
насосов проверить загорание сигнальных ламп насосов.
.
АЗС - выключатели «Автомат, перекачка баков» включить.
После
взлета
Если
резервные баки (всех или только крайних двигателей) заправлены топливом,
проверить, что сигнальная лампа «Включи перекачку резервных баков» не горит.
Если сигнальная лампа «Включи перекачку...» горит, 37 включить насосы перекачки
резервных баков, в которых имеется топливо, и проверить, что загорелись
сигнальные лампы включенных насосов, а сигнальная лампа «Включи перекачку»
погасла.
В
полете
1.
Контролировать работу насосов подкачки по горению сигнальных ламп. На самолетах
с повышенным давлением в расходных отсеках главных топливных баков (с № 0101 по
0402) при скорости полета 380 км/ч и более могут гореть лампы сигнализации не
работающих (выключенных или неисправных) насосов подкачки баков 1Г и 4Г
(двигателей № 1 и 4). Поэтому работоспособность этих насосов в полете может
быть проверена только при скорости полета ниже 380 км/ч.
.
Контролировать процесс перекачки топлива. После окончания перекачки топлива из
резервного бака какого-либо двигателя (сигнальные лампы насосов перекачки этого
бака погасли): а) проверить, что сигнальные лампы работы насосов перекачки
дополнительного бака этого двигателя горят; б) насосы перекачки топлива из
резервного бака выключить. При разгоне самолета после выработки топлива из
резервных баков могут кратковременно загораться сигнальные лампы не работающих
насосов перекачки этих баков, а также сигнальная лампа «Включи перекачку».
После окончания перекачки топлива из дополнительного бака какого- либо
двигателя (погасли сигнальные лампы насосов перекачки этого бака) проверить,
что сигнальная лампа работы насоса перекачки главного бака этого двигателя
горит.
.
Если после автоматического выключения насосов перекачки топлива из резервных
или дополнительных баков возникает необходимость полнее выработать остатки
топлива в них, то включение насосов перекачки этих баков производить в
следующей последовательности: а) АЗС - выключатели автоматики насосов перекачки
выключить; б) насосы перекачки включить; в) проверить загорание сигнальных ламп
и работы насосов; г) АЗС - выключатели автоматики насосов перекачки включить;
д) после окончания перекачки (гаснут сигнальные лампы работы насосов)
выключатели насосов перекачки выключить.
.
В случае крайней необходимости, если потребная дальность или продолжительность
полета требуют полного использования запаса топлива, в конце полета (при
остатке топлива по 2000 кг на каждый двигатель) переведите все насосы перекачки
на ручное управление и перекачайте в расходные отсеки главных баков топ ливо,
оставшееся в резервных и дополнительных баках после автоматического выключения
насосов. Для этого после загорания сигнальных табло «Остаток топл. 2000 кг»: 38
а) выключатели насосов перекачки главных баков установить в положение «Вкл.»;
б) АЗС - выключатели автоматики всех насосов перекачки выключить; в)
выключатели насосов перекачки резервных и дополнительных баков установить в
положение «Вкл.» и проверить, что сигнальные лампы насосов загорелись; г)
внимательно контролировать ход перекачки топлива. Вы- ключение каждого насоса
производить вручную немедленно после того, как окончательно погаснет его
сигнальная лампа. Во избежание выхода насоса из строя не допускать, чтобы он
работал после погасания сигнальной лампы.
.
В процессе полета периодически переводите галетный переключатель топливомера из
положения «С» в положения «Р», «Д», «Г» и обратно для контроля за
распределением остатка топлива между баками двигателей. При остатке топлива по
3500 кг на двигатель галетный переключатель топливомера установить в положение
«Г».
После
посадки и выключения двигателей
Элементы
управления агрегатами топливной системы установить в исходное положение.
Агрегаты электросистемы управления перекачкой топлива приводятся в исходное
положение после окончания полетов выключением всех АЗС - выключателей «Автомат,
перекачка баков». Во избежание несрабатывания автоматики системы перекачки в
полете не производить заправку баков топливом при включенных АЗС - выключателях
«Автомат, перекачка баков » [1,4,11].
3. Анализ эксплуатационной надежности самолета Ил-76
Эксплуатационная надёжность - важнейшее свойство изделий, определяющее их
способность нормально функционировать в заданных условиях эксплуатации. Анализ
эксплуатационной надёжности служит основой для обоснования мероприятий по
совершенствованию технологических процессов ТО и Р. При статистическом анализе
надежности АТ используется установленная нормативными документами номенклатура
ее показателей, их фактические, нормативные и контрольные значения. Фактические
значения показателей надежности АТ определяют в соответствии с утвержденными
методиками, на основе учитываемой информации об отказах, неисправностях и
повреждениях.
Нормативные значения показателей надежности устанавливаются техническими
требованиями на разработку АТ, их включают в ЭД и технические условия на
поставку АТ. Контрольные значения показателей надежности задаются по
согласованию с организациями промышленности, включаются в ЭД и служат для
определения тенденций и степени изменения надежности АТ в конкретных условиях
эксплуатации. При статистическом анализе надежности сравнивают фактические
значения показателей надежности с нормативными или контрольными, определяя
влияние эксплуатационных факторов на динамику технического состояния АТ и ее
надежности.
Существует два подхода к анализу надежности объекта. Первый рассматривает объект как
невосстанавливаемый, эксплуатируемый до первого отказа. Второй подход
предполагает, что отказавшие объекты восстанавливают, устраняют неисправности.
Объект эксплуатируется, практически, неограниченное время.
Задачи анализа, решаемые при установлении причин возникновения отказов,
раскрываются наиболее полно при рассмотрении находящихся в эксплуатации
объектов как невосстанавливаемых.
Анализ эксплуатационной надёжности служит основой для обоснования
мероприятий по совершенствованию технологических процессов ТО и Р и конструкции
объектов. Результаты выполнения анализа во многом зависят от представительности
собранных статистических данных об отказах и неисправностях заданного объекта.
На основе статистических данных, проводится качественный анализ
надёжности объекта [11].
3.1
Анализ распределения отказов топливной системы самолета Ил-76
В
таблице 5 показаны отказы самолетов Ил-76 по топливной системе в период с 2013
по 2015 год.
Таблица
5
Отказы
самолетов по топливной системе в период с 2013 по 2015 года
Системы самолета
|
2013
|
2014
|
2015
|
Итого
|
система перекачки топлива
|
12
|
34
|
13
|
59
|
система слива конденсата
|
2
|
4
|
1
|
7
|
система дренажа
|
9
|
17
|
5
|
31
|
система заправки топливных
баков
|
11
|
31
|
15
|
57
|
всего отказов
|
34
|
86
|
34
|
154
|
3.1.1 Классификация отказов
Отказ - событие, заключающееся в нарушении работоспособного состояния
объекта.
Так как, работоспособность самолета характеризуется совокупностью
значений некоторых параметров, то признаком возникновения отказа является выход
значения любого из этих параметров за пределы допусков.
Основа классификации отказов - характер возникновения и особенности
протекания процессов, приводящих к отказу.
По характеру изменения параметра различают:
внезапный отказ (отказ, характеризующийся скачкообразным изменением
значений одного или нескольких параметров объекта);
постепенный отказ (отказ, возникающий в результате постепенного изменения
значений одного или нескольких параметров объекта).
Однако четкой границы между внезапными и постепенными отказами провести
не удается. Это связано с тем, что механические, физические и химические
процессы протекают, которые составляют причины отказов, как правило, протекают
во времени достаточно медленно, а собственно отказ, вызванный этими процессами,
возникает внезапно.
В процессе эксплуатации самолетов Ил-76 возникают как внезапные, так и
постепенные отказы.
По связи между отказами объекта различают:
зависимый отказ (отказ, обусловленный другими отказами);
независимый отказ (отказ, необусловленный другими отказами).
По наличию внешних проявлений отказа различают:
явный отказ (отказ, обнаруживаемый визуально или штатными методами и
средствами контроля и диагностирования при подготовке объекта к применению или
в процессе его применения по назначению);
скрытый отказ (отказ, не обнаруживаемый визуально или штатными методами и
средствами контроля и диагностирования, но выявляемый при проведении
технического обслуживания или специальными методами диагностики).
В процессе эксплуатации самолетов Ил-76 возникают явные и скрытые отказы.
Явные отказы, как правило, выявляются в процессе выполнения осмотров самолетов.
К наиболее распространенным явным отказам относятся негерметичность
трубопроводов, механические повреждения элементов конструкции самолета. Скрытые
отказы в свою очередь выявляются при выполнении регламентных и периодических
работ, т.к. данные работы выполняются со снятием наиболее важных элементов
конструкции самолета и с применением неразрушающих методов контроля. К наиболее
распространенным скрытым отказам относятся трещины силового набора крыла, ниш
шасси.
По устойчивости отказы подразделяются на:
сбой (самоустраняющийся отказ или однократный отказ, устраняемый
незначительным вмешательством оператора);
перемежающийся отказ (многократно возникающий самоустраняющийся отказ
одного и того же характера).
В процессе эксплуатации самолетов Ил-76 возникают сбои и перемежающиеся
отказы.
Отличительным признаком сбоя является то, что восстановление
работоспособного состояния объекта может быть обеспеченно без ремонта путем
воздействия оператора. Примерами могут служить сбои автоматического
радиокомпаса АРК. Примером перемежающегося отказа может быть периодически
повторяющееся кратковременное отключение индикаторов.
По причине возникновения отказы подразделяются на:
конструктивный отказ (отказ, возникающий по причине, связанной с несовершенством
или нарушением установленных правил и (или) норм проектирования и
конструирования);
производственный отказ (отказ, возникший по причине, связанной с
несовершенством или нарушением установленного процесса изготовления или
ремонта, выполняемого на ремонтном предприятии);
эксплуатационный отказ (отказ, возникший по причине, связанной с
нарушением установленных правил и (или) условий эксплуатации);
деградационный (отказ, обусловленный естественными процессами старения,
изнашивания, коррозии и усталости при соблюдении всех установленный правил и
(или) норм проектирования, изготовления и эксплуатации).
Классификация отказов по причинам возникновения введена с целью
установления, на какой стадии или существования объекта следует провести
мероприятия для устранения причин отказов.
покупные комплектующие изделия.
Допускается выделить отказы комплектующих изделий, изготовляемых не на
том предприятии, где производится объект в целом. Отказы комплектующих
элементов также могут быть конструктивными, производственными и
эксплуатационными.
По периоду эксплуатации, на котором возник отказ, различают:
отказы при испытаниях;
приработочный (отказ периода приработки);
отказ периода нормальной эксплуатации;
отказы последнего периода эксплуатации.
Последние происходят на заключительной стадии эксплуатации объекта, когда
вследствие естественных процессов старения, изнашивания и т. п. объект или его
составные части приближаются к предельному состоянию по условиям физического
износа.
Основной причиной возникновения отказов являются некачественный ремонт на
авиаремонтных предприятиях. Так же, в процессе эксплуатации самолетов Ил-76
имели место быть эксплуатационные отказы, причинами возникновения которых
явились:
нарушения (упущения) в инженерно-авиационном обеспечении полетов;
нарушения правил хранения АТ;
не соблюдение технологий выполнения видов ТО АТ.
Наибольшее количество эксплуатационных отказов было выявлено при
выполнении следующих работ на АТ:
подготовки к повторному вылету;
регламентных работ [11].
3.1.2 Определение средней наработки на отказ
Под средней наработкой на отказ понимают математическое ожидание
наработки эксплуатируемого изделия между отказами (математическое ожидание
времени безотказной работы) и оцениваемое как отношение суммарной наработки
эксплуатируемого объекта к суммарному числу его отказов в течение этой
наработки.
ТС= (Nm-1) ∑ (1)
i=1
где:
ТС- средняя наработка на отказ;
m-
количество зафиксированных отказов за отчетный период;
ti - наработка изделий за рассматриваемый период;
N
- количество изделий, за которыми велось наблюдение.
В приведенной ниже таблице № 6 показаны отказы собранные в период с 2013
года по 2015 год в топливной системе и средний налет на отказ.
Таблица 6
Распределение отказов в топливной системе самолетов Ил-76
Системы самолета
|
2013
|
2014
|
2015
|
Итого
|
Система перекачки топлива
|
12
|
34
|
13
|
59
|
дренажная система
|
9
|
17
|
5
|
31
|
система централизованной
заправки
|
11
|
31
|
15
|
57
|
всего отказов
|
32
|
82
|
33
|
147
|
налет, часов по годам
|
574
|
1109
|
1092
|
|
Тс - средний налет на отказ
|
18.0
|
13.5
|
32.8
|
|
|
|
|
|
|
|
|
Анализ отказов и неисправностей собранных в таблице 6 показывает, что
средний налет на отказ Тс вырос в результате совершенствования систем
самолета Ил-76, внесении изменений в конструкцию и мероприятий по устранению
дефектов и выполнению рекомендаций, указанных в актах испытаний, рекламационных
актах эксплуатирующих организаций [9,10].
.2 Простои самолетов и коэффициент готовности
Ниже в таблицах №№ 7, 8, 9, приведены статистические данные за последние
три года по простою самолетов Ил-76 в результате отказов, неисправностей,
планового периодического технического обслуживания, доработок и ремонта в
топливной системе.
Таблица 7
Простои самолетов Ил-76 в 2013 году
Борт
|
01
|
02
|
03
|
04
|
05
|
06
|
07
|
08
|
09
|
10
|
11
|
12
|
Итого
|
RF 64400
|
31
|
29
|
31
|
30
|
31
|
30
|
31
|
31
|
30
|
31
|
30
|
31
|
366
|
RF 64273
|
0
|
0
|
0
|
0
|
1
|
1
|
19
|
5
|
6
|
9
|
12
|
31
|
84
|
RF 64215
|
31
|
29
|
31
|
30
|
31
|
30
|
31
|
28
|
17
|
8
|
3
|
0
|
269
|
RF 64265
|
31
|
29
|
18
|
0
|
18
|
7
|
10
|
8
|
0
|
5
|
6
|
163
|
RF 64264
|
14
|
22
|
1
|
0
|
11
|
13
|
0
|
0
|
18
|
12
|
11
|
6
|
108
|
RF 64263
|
4
|
1
|
12
|
4
|
8
|
3
|
4
|
13
|
14
|
24
|
30
|
31
|
148
|
итого
|
110
|
106
|
82
|
82
|
95
|
92
|
87
|
93
|
84
|
91
|
91
|
105
|
1138
|
Коэффициент готовности = 48,2% (с учетом всех форм ПТО и плановых
доработок)
Таблица 8
Простои самолетов Ил-76 в 2014 году
Борт
|
01
|
02
|
03
|
04
|
05
|
06
|
07
|
08
|
09
|
10
|
11
|
12
|
Итого
|
RF 64400
|
31
|
28
|
31
|
21
|
0
|
0
|
0
|
0
|
0
|
28
|
30
|
31
|
200
|
RF 64273
|
0
|
1
|
31
|
14
|
1
|
7
|
3
|
20
|
7
|
6
|
11
|
31
|
132
|
RF 64215
|
31
|
28
|
31
|
26
|
26
|
7
|
1
|
1
|
2
|
14
|
30
|
16
|
188
|
RF 64265
|
0
|
1
|
31
|
14
|
1
|
7
|
3
|
20
|
7
|
6
|
11
|
31
|
132
|
RF 64264
|
0
|
0
|
0
|
0
|
0
|
0
|
19
|
31
|
30
|
31
|
30
|
31
|
172
|
RF 64263
|
31
|
28
|
31
|
22
|
4
|
11
|
9
|
0
|
8
|
0
|
0
|
0
|
144
|
итого
|
93
|
86
|
155
|
97
|
7
|
32
|
35
|
72
|
54
|
85
|
112
|
140
|
968
|
Коэффициент готовности = 56,0% (с учетом всех форм ПТО и плановых
доработок)
Таблица 9
Простои самолетов Ил-76 в 2015 году
Борт
|
01
|
02
|
03
|
04
|
05
|
06
|
07
|
08
|
09
|
10
|
11
|
12
|
Итого
|
RF 64400
|
12
|
0
|
31
|
21
|
4
|
0
|
0
|
14
|
0
|
27
|
0
|
28
|
137
|
RF 64273
|
0
|
1
|
3
|
14
|
31
|
17
|
3
|
10
|
7
|
5
|
11
|
31
|
133
|
RF 64215
|
31
|
28
|
14
|
8
|
26
|
31
|
1
|
1
|
2
|
14
|
20
|
16
|
168
|
RF 64265
|
0
|
31
|
31
|
14
|
1
|
7
|
3
|
20
|
7
|
6
|
11
|
31
|
172
|
RF 64264
|
31
|
0
|
1
|
0
|
10
|
0
|
22
|
11
|
28
|
15
|
12
|
20
|
150
|
RF 64263
|
10
|
28
|
31
|
22
|
4
|
11
|
7
|
0
|
8
|
0
|
14
|
1
|
136
|
итого
|
53
|
58
|
111
|
69
|
46
|
66
|
36
|
66
|
52
|
67
|
68
|
127
|
896
|
Коэффициент готовности =62,0% (с учетом всех форм ПТО и плановых
доработок)
В приведенном ниже рисунке 38 показано, как в результате принимаемых мер
разработчика и изготовителя уменьшается время простоя самолетов Ил-76.
Рис. 38 Меры по уменьшению простоя самолетов Ил-76 [8]
3.3 Мероприятия по устранению выявленных недостатков
По результатам приемо-сдаточных испытаний самолета и на основании
утвержденных актов испытаний разрабатываются мероприятия по устранению дефектов
и выполнению рекомендаций, указанных в актах испытаний. Согласование с
представителем заказчика, МО РФ проводится в процессе разработки этих
мероприятий.
Конструктивно-производственные недостатки, выявленные в процессе
эксплуатации в течение отработки назначенного ресурса (срока службы), связанные
с некачественным изготовлением (разработкой) изделий собственного производства
(ОАО «АВИАСТАР-СП») устраняются по обязательным бюллетеням, силами и за счет
средств (ОАО «АВИАСТАР-СП») в соответствии с ГОСТ 31270-2004.
Проведена разработка новых конструкторских и технологических решений в
процессе производства и испытаний самолёта.
В процессе эксплуатации самолета введено множество временных изменений в
Регламент технического обслуживания (РТО), регламент технической эксплуатации
(РТЭ) и регламент летной эксплуатации (РЛЭ).
4. Особенности технической эксплуатации самолета Ил-76
в осенне-зимний период
.1 Технология подготовки самолета Ил-76 к
осенне-зимнему периоду
Зимний период эксплуатации АТ является суровым
испытанием и для личного состава и для АТ. Отрицательные температуры, частые
осадки, высокая влажность, условия обледенения откладывают определенный
отпечаток на работу АТ и авиационных специалистов.
Эксплуатация АТ в зимний период имеет следующие
особенности:
низкие отрицательные температуры;
большой перепад температур (от - до +);
осадки в виде снега, мокрого снега, дождя, инея,
обледенения.
Все это приводит к неблагоприятным условиям
эксплуатации АТ. Это приводит:
к обледенению самолета, к образованию на его
поверхности снежного покрова;
к примерзанию подвижных элементов систем управления
самолетом и двигателей;
при перепаде температур, на внутренней поверхности
планера, кессон-баков, блоков АО и РЭО образуется иней, который при нагреве
преобразуется в конденсат.
Устранение всех этих факторов приводит к увеличению
времени подготовки самолета к полету.
Совокупность этих факторов требует от летного и
инженерно-технического состава строгого соблюдения технологии выполнения всех
видов подготовок самолета, повышенного внимания и соблюдения мер безопасности.
ОБЩИЕ ВОПРОСЫ
1. Произвести углубленный контрольный осмотр самолета.
составить дефектную ведомость и устранить выявленные замечания;
. Проверить соответствие формуляров, паспортов
установленным агрегатам;
. Очистить от пыли и грязи самолет, двигатели,
агрегаты и приборы, подкрасить снаружи фюзеляж, шасси, крыло, стабилизатор и
киль;
. Нанести контрольные метки на приборах, агрегатах,
шлангах, замках;
. Обновить сигнальные вымпелы на чехлах самолета,
приемниках воздушного давления, заглушках, заземлений самолета, проверить их
исправность;
. Проверить состояние и маркировку инструмента.
Произвести клеймение инструмента согласно Приложения 3.23.НИАО-90;
. Просушить самолет и оборудование;
. Проверить состояние переносного противопожарного
оборудования самолета.
ПЕРЕЧЕНЬ РАБОТ
1. Произвести слив отстоя из всех сливных точек
топливной, масляной, гидравлической систем;
. Произвести опробование двигателей согласно графика
пробы с проверкой герметичности топливной, масляной, гидравлической систем,
системы отбора воздуха на самолетные нужды;
. Проверить работоспособность подкачивающих и
перекачивающих топливных насосов;
. Проверить состояние и чистоту дренажных отверстий
самолета и его систем;
. Осмотреть подпольное пространство фюзеляжа, ниш шасси.
Убедится, что нет следов влаги, коррозии и нарушения лакокрасочного покрытия;
. Проверить работоспособность системы обогрева
гермокабины на земле при работающих двигателях;
. Осмотреть вспомогательную силовую установку (ВСУ),
узлы подвески, воздушные, топливные и масляные коммуникации. Убедиться, что нет
течи и повреждений. Проверить надежность соединений трубопроводов и креплений
агрегатов;
. Выпустить закрылки.Осмотреть обшивку закрылков, узлы
их навески и крепления. При выпущенных закрылках осмотреть валы трансмиссии,
карданы. Убедиться в их исправности и надежности крепления;
. Слить конденсат с влагоотстойников гидросистемы;
. Проверить натяжение тросов управления самолетом и
двигателями, при необходимости произвести натяжку;
. Проверить зарядку азотом гидроаккумуляторов;
. Произвести целевой осмотр деталей управления
самолетом и двигателями: тяги, качалки, роликовые направляющие, рычаги, упоры,
ролики, шарнирные соединения, кронштейны, подшипники в узлах навески рулей
элеронов, карданов. Убедится в их исправности и отсутствии коррозии;
. Проверить работоспособность противооблединительной
системы самолета и двигателей. Убедиться в исправности системы сигнализации,
исправности кранов отбора воздуха на самолетные нужды;
. Возобновить смазку во всех узлах самолета;
. Произвести чистку и ремонт бытового оборудования.
Промыть обшивку багажников и вспомогательных помещений.
ЗАКЛЮЧИТЕЛЬНЫЕ РАБОТЫ
1. Осмотреть самолет на отсутствие посторонних
предметов;
. Произвести облет самолета;
. Произвести запись в формуляре самолета по форме:
" Произведена подготовка самолета, двигателей, АО, РЭО к эксплуатации в
осенне-зимнем периоде согласно обязательному перечню работ".
ПРИ НИЗКИХ ТЕМПЕРАТУРАХ НАРУЖНОГО
ВОЗДУХА
Место стоянки самолёта очистите от снега и льда.
Колёса шасси должны устанавливаться на чистую сухую площадку. В случае
обледенения поверхности самолёта необходимо:
. Смести иней и сухой снег волосяными щётками.
. Изморозь, примёрзший снег или лёд удалить следующими
способами:
а) Нанесением жидкости «Арктика» или её заменителя. В
качестве противообледенительных жидкостей можно использовать ПОЖ «OCTAFLO EG»,
(тип. 1), SAEAMS1424, ISO 11075, производства ООО АВИАФЛЮИД Интернешнл», г.
Москва; «Арктика» ТУ6-00-5763445-10-89 производства Московского филиала ООО «Тюменпетрол»;
«Арктика-ДГ» ТУ1-595-25-512-97, производства НПП «Арктон», г. Нижнекамск, в
соответствии с инструкциями по их применению. В отдельных случаях, при
отсутствии жидкости «Арктика», разрешается удалять ледяные отложения с фюзеляжа
и крыла водой, подогретой до температуры не более + 50°С, а хвостовое оперение
обдуть горячим воздухом. При этом контроль за состоянием поверхности самолёта
должен производиться вплоть до исполнительного старта.
Рис. 39 Схема зачехления самолета в зимний период
эксплуатации [8]
б) Надеть чехлы на переднюю кабину, СЧК, ОЧК и
хвостовое оперение (фиг. 19-1) и подать под чехлы теплый воздух, имеющий на
выходе из рукавов подогревателя температуру не более +50°С. Сразу же после
удаления обледенения протереть поверхность самолёта насухо чистой ветошью.
Тёплый воздух подаётся с помощью тепловой машины МП-300. ПРЕДУПРЕЖДЕНИЕ
ПОСЛЕ УДАЛЕНИЯ С ПОВЕРХНОСТИ САМОЛЁТА ЛЬДА, ИНЕЯ, СНЕГА, ИЗМОРОЗИ НЕОБХОДИМО
ОСМОТРЕТЬ ЩЕЛЕВЫЕ ЗАЗОРЫ РУЛЕЙ, ЭЛЕРОНОВ, ТРИММЕРОВ, СПОЙЛЕРОВ, ЗАКРЫЛКОВ,
ПРЕДКРЫЛКОВ, ИХ КРОНШТЕЙНЫ, ПОДВЕСКИ, УЗЛЫ И ДЕТАЛИ ШАССИ, УБЕДИТЬСЯ В
ОТСУТСТВИИ НА НИХ ЛЬДА И ПРОВЕРИТЬ, ЧТО РУЛИ ВЫСОТЫ И ПОВОРОТА, СТАБИЛИЗАТОР,
ЭЛЕРОНЫ, ТРИММЕРЫ, СПОЙЛЕРЫ, ЗАКРЫЛКИ И ПРЕДКРЫЛКИ ПОЛНОСТЬЮ ОТКЛОНЯЮТСЯ В КРАЙНИЕ
ПОЛОЖЕНИЯ.
3) Если чехлы примёрзли к поверхности самолёта, то,
прежде чем их снять, необходимо подать под чехлы тёплый воздух и отогреть
примёрзшие места. ПРЕДУПРЕЖДЕНИЕ. ЗАПЕРЩАЕТСЯ СНИМАТЬ ЧЕХЛЫ, ПРИМЁРЗШИЕ К
ПОВЕРХНОСТИ САМОЛЁТА, ВО ИЗБЕЖАНИЕ ПОВРЕЖДЕНИЯ ЛАКОКРАСОЧНОГО ПОКРЫТИЯ.
4) Обледенение с приёмника воздушного давления удалять
воздухом, подогретым до температуры + 60°С на выходе из рукава наземного
источника [1,4,12].
.2 Особенности эксплуатации топливной системы в
осенне-зимний период
При заправке самолета топливом необходим тщательный
контроль топлива, топливозаправщиков. При отрицательных температурах вода,
находящаяся в топливе кристаллизуется. попадание такого топлива в баки самолета
может привести к закупорке топливных фильтров, топливной автоматики, отказу
авиадвигателей. поэтому перед заправкой самолета топливом старшему бортовому
технику (нач. Технико-эксплуатационной части (ТЭЧ) отряда) необходимо проверить
на топливозаправщике:
наличие и правильность оформления контрольного талона
на топливо ( в контрольном талоне должны быть запись о содержании в топливе не
менее 0,1%по объему жидкости "И", подпись лаборанта службы
горюче-смазочных материалов (ГСМ);
наличие отметки представителя инженерно-авиационной
службы (ИАС) о допуске топливозаправщика к применению, при отсутствии данной
подписи необходимо произвести проверку топлива на отсутствие воды (инея) и
механических примесей. Проба берется из самой емкости и из топливного фильтра.
после заправки необходимо произвести отбор пробы топлива из баков самолета в
количестве 0,5-1,0 л из каждой точки слива. при обнаружении в отстое топлива
механических примесей, воды, кристаллов льда слив производить до полного
удаления загрязненного топлива.
Еще одной особенностью в большей степени касается инженерно-
технического состава. Зимой нужно уделять внимание чистоте дренажных отверстий
самолета. Если этого не делать, то вода, попадающая в полости самолета
скапливается там, замерзает, что приводит к замерзанию топливных насосов,
отказу агрегатов, разрыву трубопроводов, трещинам обшивки.
Конденсация и замерзание влаги в системах силовой установки может
привести к закупорке трубопроводов и отказа агрегатов, что особенно опасно для
топливных систем. Для уменьшения конденсации влаги и образования инея и льда,
необходимо при хранении воздушного судна (ВС) удерживать баки полностью
заправленные топливом. Вместе с этим при обслуживании топливной системы при
низких температурах внешнего воздуха нужен тщательный контроль качества топлива
и предупреждения образования льда в топливе, особенно на топливных фильтрах,
что может прекратить подачу топлива в двигатели.
Для предотвращения образования кристаллов льда применяют ряд способов
исключения воды из топлив как в наземных емкостях, так и в баках самолетов. В
емкостях делают выморожение топлива, отстаивание в специальных отстойниках или
с применением центрифуг, обезвоживание топлива электрическим полем совместно с
центробежным способом, массообмен при контакте топлива с воздухом (азотом) при
определенной температуре и давлении в надтопливном пространстве емкостей
(барботажный продув воздуха); фильтрацию с применением специальных пористых
перегородок и т.д.
Для обеспечения надежной работы ВС при низких температурах внешнего
воздуха ежегодно в осенний период проводят подготовку личного состава и
авиационной техники (сезонное обслуживание) к зимней эксплуатации,
организовывая техническую учебу и проверку знаний летного и
инженерно-технического состава по особенностям эксплуатации и технического
обслуживания ВС в зимний период. Сезонное обслуживание ВС обычно соединяют с
периодической формой технического обслуживания, а готовность к зимней
эксплуатации проверяет комиссия В/Ч [1].
.3 Оценка технологического времени выполнения операций при подготовке к
осенне - зимнему периоду эксплуатации
Тр Тх Tn1 Tn2 Tn2
Tц ∑Tn =
Tn1 + Tn2 + Tn3
T=Tц + ∑Tn
Рис. 40 Схема производственного процесса
Тц - оперативное время. Называется временем цикла и
определяется как затраты времени исполнителя на выполнения операций.
Оно включает основное время и вспомогательное время.
Основное время - это время затраченное на выполнение
работ;
Вспомогательное время - это цикловые потери.
∑Tn - внецикловые потери;
Tn1- потери на подготовку и приведение в порядок рабочего
места и материальных средств;
Tn2 - Отдых;
Tn3 - время затраченное на ожидание операций.
При переводе АТ к осенне-зимнему периоду эксплуатации
выполняется перечень работ указанных в пооперационной ведомости перевода АТ:
. Помывка АТ;
. Проверка полноты заправки самолета спецжидкостями
при необходимости их замена);
. Уборка салона;
. Замена смазок в подвижных соединениях;
. Проветривание АТ;
. Проверка работоспособности и исправности систем
самолета;
. Выполнение газовки АТ.
На перевод авиационной техники (АТ) отводят 14 дней (
две недели ), в течение которых приведенный перечень работ должен быть выполнен
в отведенный срок, два выходных дня включатся в общее время перевода. После
выполнения перевода ИТС войсковой части (в/ч) проводит приемку АТ и по
результатам углубленных осмотров допускает ее к дальнейшему осенне-зимнему
периоду эксплуатации.
Ниже приведен расчет времени затраченного на
выполнение производственного процесса.
=Tц + ∑Tn (2);
где ∑Tn определяем по формуле:
∑Tn = Tn1 + Tn2 + Tn3, (3).
Время начала рабочего дня начинается с 8:45 утра с
построения, в 8:55 ИТС убывает к рабочим местам. В 9:30 ИТС прибывает к АТ и
приводит в порядок рабочее место, подготавливает необходимый инструмент, подгоняет
средства наземного обслуживания к самолету, подключает самолет к
электропитанию.
С 10:00 до 12:00 проходит помывка самолета и уборка
салона. С 12:00 до 13:00 проветривание самолета. С 13:00 до 14:00 (технический
перерыв-обед) С 14:00 до 14:30 проведение технического инструктажа по
дальнейшему ходу выполнения работ, с 14:30 ИТС приступает к дальнейшему
выполнению перевода АТ. С 14:40 до 16:00 ИТС проводит замену смазок в подвижных
соединениях. С 16:10 до 17:20 специалисты ИТС по специальностям приступают к
проверки работоспособности всех систем самолета. В 17:25 инженер эскадрильи
докладывает вышестоящему командованию о выполнении перевода на данном самолете
и подготовки его к газовке. Таким образом на один самолет тратится один день.
После завершения выполнения работ по переводу АТ, отводится два дня на газовку
самолетов по завершению которой старшие инженеры по специальностям в четырех
дневный срок выполняют приемку самолетов и принимают решение о допуске АТ
осенне-зимнему периоду эксплуатации
Рассчитаем время технологического процесса для одного
самолета по приведенному выше распорядку работ:
Тр = 330 минут (5 часов 30 минут);
Отсюда следует, что Тц= 330 мин + 60 мин = 390 ( 6
часов 30 минут) - время цикла.
Далее определяем внецикловые потери для одного
самолета:
Тn1= 30 минут;
Тn2= 60 минут;
Тn3= 75 минут.
∑Tn= 30 мин + 60 мин +75 мин =165 минут ( 2 часа
45 минут ) - время внецикловых потерь.
Таким образом найдя цикловые и внецикловые потери
определяем время производственного процесса ИТС на выполнение:
=Tц + ∑Tn (3)
Т(1) = 330 мин + 165 мин = 495 минут ( 8 часов 15
минут ). Определив время производственного процесса для одного самолета,
определяем его для шести:
Т(6) = 495 Х 6 = 2970 минут (49 часов 30 минут )
Из проведенного расчета времени производственного
процесса мы определили, что на выполнение работ по переводу АТ затрачено 6 дней
(одна неделя).
Вторая часть перевода заключается в выполнении газовок
и приемки воздушных судов старшими инженерами части.
Выводы и рекомендации
При выполнении данной работы было приведено общее
описание самолета Ил-76, его назначение, составные части, летно-технические
характеристики. Подробно рассмотрено назначение топливной системы самолета, ее
состав и конструкция агрегатов. Проведён многосторонний анализ проблем
топливной системы самолета возникающих по причине отказов отдельных узлов и
элементов, которые приводят к простою самолета, который в свою очередь ведет к
срыву полетных заданий, кратковременному выводу самолета из парка исправных
воздушных судов, затрат времени, труда и ресурсов для восстановления
исправности АТ Было предложено табличное описание количества отказов
произошедших в период с 2013 по 2015 года и соответственно простоев ВС.
Показаны мероприятия по улучшению эксплуатационных
характеристик и повышению надёжности топливной системы самолёта при переводе к
осенне-зимнему периоду эксплуатации, а также в процессе повседневной рабочей
обстановке в условиях низких температур.
И в заключении дипломной работы был произведен расчет
времени технологического процесса затраченного на перевод к зимнему периоду
эксплуатации АТ, в ходе которого образовался простой ВС.
По итогам работы следует ВЫВОД: На данный момент
топливная система (ТС) самолета Ил-76 является одной из самых надежных систем
установленных на ВС ВТА. Ее относительная простота конструкции и минимальное
наличие электроники дает возможность удобства в обслуживании и ремонте,
эксплуатации самолета в различных климатических условиях. Для повышения
надежности и лучшей работоспособности ТС при низких температурах необходимо
проводить ряд мероприятий, таких как своевременное добавление
противокристализующих жидкостей, зачехление самолета, а при необходимости
прогрев теплым воздухом отдельных агрегатов, наиболее подверженных влиянию
минусовых температур.
Для уменьшения простоя самолетов при выполнении
перевода из расчетной части определения времени технологического процесса можно
сделать следующий ВЫВОД: Для уменьшения общего времени технологического
процесса затраченного на выполнение работ на АТ следует уменьшить время
затраченное на инструктаж, подготовку рабочего места, и последующую приемку ВС
инженерами по специальностям. Снизив в разумных пределах время внецикловых
потерь, мы тем самым ускорим выполнение подготовки самолета к осенне-зимнему
периоду эксплуатации и уменьшим простои ВС возникающие из-за организационных
мероприятий.
Список использованной литературы
1. Самолет Ил-76ТД. Часть III. Инструкция по технической
эксплуатации [Тескт]: Гл.31, 1978. 250 с.
. Регламент технического обслуживания самолета Ил-76ТД
[Текст]: М.: ДВТ МТ РФ, 1994. 105 с.
. Самолет Ил-76Т. Технология выполнения регламентных работ
[Текст]: 1981. 90 с.
. Наставление по технической эксплуатации и ремонту
авиационной техники в ГА (НТЭРАТ ГА - 93) [Текст]: М.: Воздушный транспорт,
1995. 350 с.
. Корнеев, В.М., Конструкция и летная эксплуатация самолета
ИЛ-76: Учебное пособие [Текст]: 2015. 80 с.
. Шмаков, Ю.И., Семенов, В.А., Конструкция и летная
эксплуатация самолета ИЛ-76 [Текст]: М.: Машиностроение, 1981. 98 с.
. Инструкция по технической эксплуатации самолета ИЛ-76
[Текст]: Часть IV., 1978. 76 с.
8. Руководство по лётной эксплуатации
самолёта ИЛ-76 [Текст]:1977. 220 с.
9. Базилович, Е.Ю., Статистические методы оценки состояния
авиационной техники [Текст]: М. Транспорт, 1987. 240 с.
. Чинючин, Ю.М., Смирнов, Н.Н. Основы теории эксплуатации
авиационной техники: Пособие по проведению практических занятий Расчет
единичных показателей и оценка эксплуатационной технологичности летательных
аппаратов [Текст]: М.: МГТУ ГА, 2011. 112 с.
. Смирнов, Н.Н., Эксплуатационная технологичность летательных
аппаратов [Текст]: Учебное пособие для вузов. М.: Транспорт, 1998. 256 с.
. ГОСТ Р 53863-2010 Система технического обслуживания и
ремонта авиационной техники [Текст]. 100 с.