Автоматизация НПС-21 'Сковородино'
Введение
перекачка нефть автоматизация
Магистральный трубопроводный
транспорт является важнейшей составляющей топливно-энергетического комплекса
России. Значимость трубопроводного транспорта определяется значительной
удаленностью основных месторождений нефти и газа от потребителей, а также
высокой долей нефти, нефтепродуктов и газа в экспортном балансе России.
Автоматизация процесса перекачки
нефти необходима для:
регулирования и оперативного
управления технологическими процессами;
контроля состояния технологического
оборудования и его защиты от аварийных параметров;
сбора информации о параметрах
протяжённого объекта;
измерения количества и показателей
качества перекачиваемой нефти.
Внедрение автоматизации на
нефтеперекачивающей станции (НПС) обеспечивает непрерывность процесса
перекачки, за счет автоматического включения резерва (АВР) оборудования, а так
же предотвращение аварийных ситуаций, связанных с пожаром или экологическим
загрязнением. Снижаются затраты на простой оборудования и ликвидацию последствий
аварии, что несомненно является актуальной проблемой.
Цель данного дипломного проекта -
усовершенствование системы автоматизации НПС.
Задачами дипломного проекта
являются:
изучение технологии перекачки нефти;
подбор средств автоматизации для
параметров контроля;
улучшение метрологических и
эксплуатационных характеристик системы измерения расхода.
При работе над проектом были
использованы материалы ООО «Востокнефтепровод» (отраслевой регламент по
автоматизации технологического процесса перекачки нефти, руководящий документ
по автоматизации и телемеханизации магистральных нефтепроводов).
1. Технология перекачки
нефти на НПС-21 «Сковородино»
.1 Назначение НПС-21
«Сковородино»
Перекачка нефти осуществляется
посредством последовательно расположенных нефтеперекачивающих станций.
Нерюнгринское районное нефтепроводное управление (РНУ) является филиалом ООО
«Востокнефтепровод». Перекачку нефти по трубопроводам в зоне ответственности
Нерюнгринского РНУ осуществляют НПС: №14 «Олекминск», №17 «Алдан», №21 «Сковородино»,
«Джалинда».
Основной задачей НПС-21 является
обеспечение приема, транспортировки и сдачи нефти с минимальными затратами, в
соответствии с заданиями ООО «Востокнефтепровод». НПС-21 «Сковородино»
предназначена для перекачки восточно-сибирской товарной нефти по магистральному
нефтепроводу «Восточная Сибирь - Тихий океан». НПС-21 «Сковородино» позволяет
осуществлять следующие операции:
- подачу
нефти из магистрального нефтепровода на площадку наливной железнодорожной
эстакады с одновременным приемом в резервуарный парк (основной режим);
- поддержание давления в линейной
части перед станцией с помощью регулятора давления для предотвращения
образования газовой полости за перевальными точками;
перекачку нефти по магистральному
нефтепроводу через емкость;
перекачку нефти по магистральному
нефтепроводу с подключенной емкостью;
- перекачку нефти по схеме «через
емкость» на площадку наливной железнодорожной эстакады;
временное хранение нефти;
- защиту линейной части от
превышения давления;
внутрипарковые перекачки нефти
подпорным насосом;
оперативный учет количества
перекачиваемой нефти;
пуск и прием средств очистки и
диагностики.
1.2 Состав НПС
В состав НПС-21 входит оборудование
основное и вспомогательное:
- камеры
пуска приема средств очистки и диагностики (КПП СОД);
- фильтры-грязеуловители
(ФГУ);
- система
предохранительных клапанов (ПК);
- узлы
регулирования давления (УРД);
- магистральная
насосная станция (МНС);
- подпорная
насосная станция (ПНС);
- резервуарный
парк (РП);
- технологические
трубопроводы;
- системы
водоснабжения, теплоснабжения, вентиляции, канализации, пожаротушения,
электроснабжения, автоматики, телемеханики, связи, производственно-бытовые
здания и сооружения.
1.3 Описание
технологических процессов
Технологический процесс перекачки
осуществляется согласно утвержденным технологическим картам нефтепровода и
технологическим режимам перекачки. Физико-химические свойства нефти: плотность
843,7 кг/м3; вязкость 22 мм2/с; массовая доля серы 0,7%;
давление насыщенных паров при 200С - 19 кПа; массовая доля воды
0,26%; температура начала кипения 56 0С.
Основной схемой технологического
процесса перекачки нефти НПС с емкостью является перекачка с «подключенными
резервуарами» или «через резервуары».
Рассмотрим технологическую схему
НПС-21 «Сковородино», приведенную на рисунке 1.1.
Рисунок 1.1 - Технологическая схема НПС-21 «Сковородино»
Нефть с НПС-17 «Алдан» через камеру
приема-пуска средств очистки и диагностики (КПП СОД) поступает на блок
фильтров-грязеуловителей (ФГУ) проходя очистку от механических примесей.
Перепады давления в фильтрах-грязеуловителях необходимо регистрировать раз в 12
часов, а после проведения работ на линейной части не реже одного раза в час.
При превышении максимального перепада давления на фильтре-грязеуловителе более
или равном 0,05 МПа он должен быть отключен и очищен, предварительно должен
быть подключен резервный фильтр-грязеуловитель. Далее нефть проходит первый
блок предохранительных клапанов, предназначенных для защиты от повышенного
давления, как трубопровода, так и объектов станции. В случае срабатывания
предохранительных клапанов, происходит сбрасывание давления, и избыток нефти
поступает в резервуары аварийного сброса (РАС) нефти. После сброса нефти от
предохранительных клапанов сбросные линии должны быть освобождены от нефти.
Утечки и дренаж направляются в подземные емкости сбора утечек объемом 40 м³.
Очищенная от механических примесей,
через открытую задвижку №1, нефть поступает в первый узел регулирования
давления, на выходе из которого нефть через ПК3 поступает в КПП СОД для
отправки по трубопроводу диаметром 720 мм на приемо-сдаточный пункт (ПСП)
«Сковородино». А по трубопроводу диаметром 1220 мм через УРД-2 и ПК2, в
зависимости от режима работы НПС, может поступать как в резервуары вертикальные
стальные с понтоном и алюминиевой куполообразной крышей объемом 50000 м³ так и непосредственно на
вход подпорного насосного агрегата (ПНА).
Откачка нефти из резервуаров и
подача ее в магистральный нефтепровод осуществляется подпорным насосным
агрегатом.
Нефть из резервуара по отпускному
трубопроводу через открытую задвижку поступает во всасывающий коллектор
подпорных насосных агрегатов. Далее нефть подпорными агрегатами через
нагнетательный коллектор при открытой задвижке подается в магистральную
насосную станцию, через блок ПК4. Магистральные насосные агрегаты (МНА)
повышают давление в зависимости от режима работы. После МНС нефть направляется
в узел приема-пуска скребка, далее в магистральный нефтепровод и
транспортируется до НПС «Джалинда».
1.4 Состав
технологического оборудования
Магистральная насосная станция
В помещении МНС установлены три
магистральных насосных агрегата. Магистральные центробежные насосы «Sulzer»
HPDM (High Pressure Double volute, horizontally split) 600-615-1d/27
предназначены для перекачки нефти по трубопроводу на заданное расстояние до
следующей нефтеперекачивающей станции. Насосные агрегаты обвязаны
трубопроводами-отводами, которые соединяют их приемные и напорные патрубки с
общим коллектором. Магистральные насосные агрегаты предназначены для
транспортирования по магистральным трубопроводам нефти с температурой от минус
5 до плюс 80°С, с содержанием механических примесей по объему не более 0,05% и
размером не более 0,02 мм. Электродвигатели 4АЗМВ-2500. В процессе подготовки к
пуску магистральных насосных агрегатов выполняются следующие операции:
- включается маслосистема,
производится контроль температуры и давления масла, температура масла в маслобаке
контролируется автоматически при помощи электронагревателя, не ниже 20°С.
- включается система охлаждения
статора электродвигателя МНА, производится контроль температуры и давления
охлаждающей жидкости;
- включается система затвора двойных
торцевых уплотнений магистрального насоса, производится контроль температуры и
давления затворной жидкости);
включается система подпора воздуха в
корпусе электродвигателя, производится контроль избыточного давления в корпусе
электродвигателя;
включается приточная вентиляция,
производится контроль избыточного давления в воздухопроводе приточной
вентиляции;
- открываются электроприводные
задвижки на входе и выходе магистральных агрегатов, подпорных агрегатов,
фильтрах грязеуловителях, трубопроводах подключения технологических
резервуаров, трубопроводах подключения резервуаров аварийного сброса,
технологических трубопроводах НПС, трубопроводах подключения блоков
предохранительных клапанов, (в зависимости от схемы запуска), производится
сброс воздуха из корпусов агрегатов;
- система автоматического
регулирования оборотов привода (ЧРП) настраивается на рабочее давление на входе
и выходе НПС по карте технологических режимов [1].
Сообщение о
готовности (неготовности) НПС к пуску отображается на экране монитора
автоматизированного рабочего места (АРМ) оператора НПС и АРМ диспетчера РДП с
указанием, при неготовности конкретной вспомогательной системы или единицы
оборудования. Сообщение о готовности НПС к пуску фиксируется в оперативном
журнале.
При неготовности
вспомогательных систем или оборудования, подготовка к пуску оборудования НПС
прекращается до устранения неисправности.
Системы
автоматизации и телемеханизации, система диспетчерского контроля и управления
позволяют управлять основным и вспомогательным оборудованием НПС как по месту
(в автоматическом, или ручном режиме при возникновении нештатной ситуации), так
и с АРМ оператора НПС.
Магистральные и
насосные агрегаты могут находиться в одном из следующих состояний:
в работе;
в «горячем» резерве
(агрегат исправен, готов к пуску в любой момент);
в «холодном»
резерве (агрегат исправен, при необходимости его пуска или перевода в «горячий»
резерв требуется проведение подготовительных работ;
в ремонте.
Для того чтобы МНА,
находящийся в «горячем» резерве был запущен в работу, должна сработать
автоматика АВР - автоматического включения резервного агрегата при отключении
собственной защитой работающего агрегата.
В зависимости от
пусковых характеристик электродвигателя, схем электроснабжения и системы
разгрузки уплотнений могут применяться различные программы пуска насосного
агрегата, отличающиеся положением задвижки на выходе насосного агрегата в
момент пуска электродвигателя:
на открытую
задвижку;
на открывающуюся
задвижку.
Автоматика
магистрального насосного агрегата обеспечивает возможность пуска по
вышеуказанным программам по выбору оператора НПС.
Программа пуска «на
открытую задвижку» является предпочтительной. Её применение возможно, если
пусковые характеристики электродвигателя и схемы электроснабжения рассчитаны на
соответствующий режим. Следует отметить, что при пуске на открытую задвижку
проходит глубокая посадка напряжения.
Программа пуска «на
открывающуюся задвижку» используется при невозможности применения
предшествующей программы. Помимо двух основных программ, рассмотренных выше,
применяется программа «на открывающуюся задвижку на приёме насосного агрегата и
на открывающуюся задвижку на выходе насосного агрегата». Пуск агрегата по этой
программе можно производить при заполненном нефтью насосе. Промежуток времени
между началом открытия задвижек и пуском насоса определяется индивидуально для
каждой НПС. Автоматический ввод резервного магистрального насосного агрегата
осуществляется на полностью открытые задвижки, возможность плавного изменения
крутящего момента электродвигателя при «тяжелом пуске», на полностью открытые
задвижки, во всем диапазоне скоростей осуществляется применением ЧРП с
трансформаторами-преобразователями.
Следует отметить,
что во всех режимах работы магистрального нефтепровода регулирование давления
осуществляется с помощью УРД и ЧРП МНА на НПС путём установки нужных параметров
с АРМ оператора НПС или диспетчера РНУ.
Изменение
производительности для заданного количества работающих МНА на НПС в диапазоне
расходов от Qmin до Qmax и возврат на Qmin осуществляется изменением заданного
давления на выходе НПС, вследствие одновременного изменения частоты вращения
всех МНА на НПС. Основные постоянно контролируемые параметры работы МНА
приведены в таблице 1.1.
Таблица 1.1 - Основные постоянно
контролируемые параметры МНА
Наименование контролируемого параметра
|
Значения уставок защит
|
|
предельная
|
аварийная
|
Температура подшипников скольжения насоса (с полевой и приводной
сторон),°С
|
65
|
75
|
Температура упорных подшипников насоса,°С
|
65
|
75
|
Температура корпуса насоса,°С
|
50
|
60
|
Температура подшипников скольжения мультипликатора,°С
|
65
|
75
|
Температура упорного подшипника мультипликатора,°С
|
65
|
75
|
Температура подшипников электродвигателя,°С
|
65
|
75
|
Температура обмоток статора электродвигателя,°С
|
110
|
115
|
Температура горячего воздуха на выходе из статора,°С
|
95
|
100
|
Максимальная температура масла в коллекторе системы смазки,°С
|
|
60
|
Давление масла в коллекторе системы смазки минимальное, кПа
|
|
25
|
Вибрация подшипников скольжения насоса, мм/с
|
6
|
7,1
|
Вибрация подшипников электродвигателя, мм/с
|
6
|
7,1
|
Вибрация подшипников мультипликатора, мм/с
|
6
|
7,1
|
Агрегатные защиты МНА должны
обеспечивать остановку данного МНА. Перечень параметров контроля состояния МНА
и порядок работы защит приведен в приложении Б (таблица Б.1). Параметры
контроля состояния МНА должны уточняться в соответствии с требованиями
изготовителей оборудования.
Алгоритм функционирования агрегатной
защиты работающего МНА в соответствии c режимом управления должен предусматривать:
- автоматическую остановку МНА;
отключение индивидуальных
вспомогательных систем МНА.
Для остановленного МНА в случае
срабатывания агрегатной защиты, алгоритм которой в соответствии с приложением Б
(таблица Б.1) требует закрытия задвижек на входе и выходе МНА, должно
выполняться закрытие задвижек на входе и выходе данного МНА. Закрытие задвижек
на входе и выходе МНА, отключение индивидуальных вспомогательных систем МНА
выполняется только после подтверждения отключения высоковольтного включателя
(ВВ) привода МНА.
При наличии соответствующих
требований, после подтверждения отключения ВВ привода МНА агрегатной защитой
системой автоматизации без выдержки времени должен выполняться АВР МНА
(автоматический пуск МНА, находящегося в режиме «резервный»). АВР МНА
выполняется только в том случае, если защита, требующая АВР, сработала на
работавшем МНА. АВР МНА не производится в случае срабатывания агрегатной защиты
во время выполнения программы пуска МНА.
Агрегатные кнопки «Стоп» для
аварийной остановки МНА размещаются:
- в операторной НПС на панели блока
ручного управления;
на агрегатной приборной стойке в
насосном зале.
Агрегатная кнопка «Стоп» должна
иметь надпись «СТОП МНА» с указанием технологического номера агрегата.
Подключение кнопок «Стоп» аварийной
остановки МНА к системе автоматизации и к системе энергоснабжения НПС должно
обеспечивать отключение ВВ привода МНА как по каналам управления системы
автоматизации, так и без их участия напрямую с кнопки.
Датчики виброскорости для МНА должны
быть установлены на всех подшипниковых опорах насоса и электродвигателя и
выполнять измерение вертикальной и горизонтальной составляющих
среднеквадратичного значения виброскорости подшипниковой опоры.
Датчик контроля осевого смещения
ротора насоса должен устанавливаться на подшипниковой опоре насосного агрегата
со стороны радиально-упорного подшипника.
От момента включения ВВ привода МНА
и до момента его отключения должна функционировать защита «Аварийная
максимальная вибрация. Порог 2».
Защита «Аварийная максимальная
вибрация. Порог 2» должна формироваться с выдержкой времени 2 секунды при
превышении виброскорости в любой точке контроля МНА значения 18,0 мм/с.
Через 30 секунд после подачи команды
на включение ВВ привода МНА и до его отключения должна дополнительно к защите
«Аварийная максимальная вибрация. Порог 2» функционировать защита «Аварийная
максимальная вибрация. Порог 1».
Защита «Аварийная максимальная
вибрация. Порог 1» должна формироваться с выдержкой времени 5 секунд при
превышении виброскорости в любой точке контроля МНА значения 7,1 мм/с.
Защита «Аварийная максимальная
вибрация. Порог 1» отключается для всех МНА при пуске одного из МНА данной НПС
на время 30 секунд от момента включения ВВ привода.
Общестанционные защиты НПС при
срабатывании должны осуществлять один из алгоритмов остановки МНА и ПНА:
- одновременная остановка всех
работающих МНА, ПНА;
одновременная остановка всех
работающих МНА;
последовательная остановка всех
работающих МНА, начиная с первого по потоку нефти работающего МНА;
остановка одного (первого по потоку
нефти) из работающих МНА;
последовательная остановка всех
работающих МНА (начиная с первого по потоку нефти МНА), с одновременной
остановкой всех работающих ПНА с выдержкой времени до 5 секунд после
подтверждения отключения всех ВВ приводов работавших МНА.
Алгоритм одновременной остановки
МНА, ПНА должен предусматривать одновременную подачу команд остановки всех
работающих МНА, ПНА.
Алгоритм последовательной остановки
МНА должен предусматривать последовательную остановку работающих МНА, начиная с
первого по потоку нефти. Интервал времени между командами остановки МНА должен
составлять три секунды.
Одновременная остановка всех
работающих насосных агрегатов без выдержки времени от момента срабатывания
защиты должна выполняться только для защит:
- «Пожар» на технологических
объектах;
аварийная остановка МНС кнопкой
«СТОП МНС»;
аварийная остановка ПНС кнопкой
«СТОП ПНС».
При срабатывании общестанционных
защит, связанных с аварийным состоянием вспомогательных систем, производится
последовательная остановка насосных агрегатов МНС.
Подпорная насосная станция.
Подпорная насосная станция
представлена тремя ПНА с насосами марки «Sulzer». Центробежные насосы марки
«Sulzer» VCRD 18х30х30BN, двухступенчатые, с вертикальным корпусом, с закрытыми
узлами всасывающего стакана, закрытыми рабочими колёсами, с одинарными
торцовыми уплотнениями патронного типа фирмы Burgmann, предназначены для подачи
нефти плотностью от 800 до 950 кг/м3, температурой от минус 100°С до плюс 50°С,
из вертикальных стальных резервуаров на прием магистральных насосов и создания
необходимого кавитационного запаса (4 м) для их работы, в качестве подпорных
насосов, а так же в зависимости от технологической схемы, для раскачки
резервуаров в которые производится сброс нефти из системы предохранительных
устройств защиты нефтепровода от превышения давления, в качестве
вспомогательных насосов. Основные контролируемые параметры работы ПНА приведены
в таблице 1.2. Подпорные насосы на НПС комплектуются программным управлением
агрегатом (ПУА), устанавленным в операторной [2].
Системы автоматизации и телемеханизации,
система диспетчерского контроля и управления позволяют управлять основным и
вспомогательным оборудованием НПС как по месту (в автоматическом, или ручном
режиме при возникновении нештатной ситуации), так и с АРМ оператора НПС.
Таблица 1.2 - Основные постоянно
контролируемые параметры работы ПНА
Наименование контролируемого параметра
|
Значения уставок защит
|
|
предельная
|
аварийная
|
Вибрация подшипников насоса и подшипников электродвигателя,
мм/сек;
|
6
|
7,1
|
Максимальное давление утечки нефти через торцевое уплотнение
ПНА, МПа
|
0,5
|
1
|
Температура масла в маслянном картере подшипника насоса: -
минимальная, °С - максимальная, °С
|
|
10 40
|
Минимальная температура воздуха в корпусе двигателя, °С
|
|
-20
|
Максимальная температура обмоток статора электродвигателя, °С
|
|
45
|
Аварийно минимальное давление на выходе работающего ПНА, МПа
|
|
0,5
|
Перепад давления на фильтре-решетке ПНА: - минимальный, МПа -
максимальный, МПа
|
|
0,03 0,05
|
Системы автоматизации и
телемеханизации, система диспетчерского контроля и управления позволяют
управлять основным и вспомогательным оборудованием НПС как по месту (в
автоматическом, или ручном режиме при возникновении нештатной ситуации), так и
с АРМ оператора НПС.
Подпорные насосные агрегаты могут
находиться в одном из следующих состояний:
в работе;
в «горячем» резерве (агрегат
исправен, готов к пуску в любой момент);
в «холодном» резерве (агрегат
исправен, при необходимости его пуска или перевода в «горячий» резерв требуется
проведение подготовительных работ;
в ремонте.
Управляемая остановка подпорного
насоса может быть осуществлена дистанционно с АРМ оператора НПС, системой
автоматики в аварийном режиме, а так же по месту обслуживающим персоналом.
Аварийная остановка насоса по месту производится путём нажатия кнопки «Стоп».
Контроль аварийной остановки осуществляется системой автоматики.
Система защиты от повышения
давления.
Система предохранительных клапанов
предназначена для защиты нефтепровода от гидравлического удара, превышения
допустимого давления. При превышении в нефтепроводе давления настройки (Рн -
давление настройки срабатывания клапана DANFLO), устройство начнёт сбрасывать
нефть. Сброс будет осуществляться до тех пор, пока давление в нефтепроводе не
достигнет давления несколько ниже настроечного (допускается до 0,9 Рн).
Защиту НПС от превышения давления в
магистральном трубопроводе диаметром 1220 мм обеспечивает узел
предохранительных клапанов №1. Давление настройки узла предохранительных
клапанов №1 5,45 МПа.
Защиту трубопроводов РП НПС от
превышения давления обеспечивает узел предохранительных клапанов №2. Давление
настройки узла предохранительных клапанов №2 0,8 МПа. При повышении давления
перед узлом предохранительных клапанов №2 до 1,0 МПа микропроцессорная система
автоматики (МПСА) НПС-21 автоматически открывает задвижку для сброса нефти в
РАС. Защиту трубопровода подачи нефти на наливную железнодорожную эстакаду от
превышения давления обеспечивает узел предохранительных клапанов №3. Давление
настройки узла предохранительных клапанов №3 2,0 МПа. При повышении давления
перед узлом предохранительных клапанов №3 до 2,25 МПа МПСА НПС-21 автоматически
открывает задвижку для сброса нефти в РАС. Параметры работы предохранительных
клапанов приведены в таблице 1.3.
Таблица 1.3 - Параметры работы
предохранительных клапанов
Параметр
|
Значение
|
Давление номинальное Рн (максимальное рабочее
давление), МПа
|
6,3
|
Давление при котором ПК должен полностью открыться, не более
|
1,15 Рн
|
Давление настройки, МПа
|
от 1,5 до 4,5
|
Шаг измерения давления настройки, МПа
|
0,1
|
Давление закрытия Р3, не более
|
0,9 Рн
|
Расход, сбрасываемый через узел сброса, м3/ч
|
9600
|
Узел предохранительных клапанов
состоит из клапанов DANFLO (до 4 штук) с пневматической системой управления, стойкой для
баллонов, стойкой для клеммных коробок и ресиверов. Всё оборудование смонтировано
на единой раме. Каждый клапан с помощью шкафа управления настраивается на
давление срабатывания (Рн) индивидуально (независимо) путём задания
давления газа (Рг) в газовой полости поршня клапана. Подача газа в
шкаф осуществляется от стойки газовыми баллонами. Баллоны объединены в 2
группы, основную и резервную, по 8 штук в группе. Стойка для баллонов общая для
всех клапанов устройства. Поэтому израсходование газа из двух групп баллонов
приведёт к выводу из рабочего состояния всех клапанов.
Шкаф управления предназначен для
индивидуального задания давления газа в газовой камере клапана (до 4-х
клапанов). Значение давления задаётся с помощью редукторов управляемых или
ручных. С одного входа газ подаётся на четыре панели с одной группу баллонов,
называемой основной, а с другого - через соленоидный клапан из резервной группы
баллонов. При снижении давления газа в основной группе баллонов ниже 6 МПа, по
команде датчика давления соленоидный клапан переключит подачу газа из основной
группы баллонов на резервную, а в операторную будет подан сигнал о наступлении
данного события. При снижении давления газа в резервной группе баллонов ниже 6
МПа, по команде другого, аналогичного, датчика давления в операторную будет
подан сигнал о наступлении этого события.
Значение давления в газовой камере
клапана контролируется с помощью датчиков Fisher Rosemount, с выдачей сигнала
постоянным током в пределах 4-20 мА. При этом, 4 мА соответствуют давлению 0
(ноль) МПа, 20 мА - 5,52 МПа.
Существует два возможных режима
управления давлением срабатывания предохранительных клапанов:
дистанционная настройка (основной);
настройка по месту (аварийный режим
работы).
Дистанционная настройка предполагает
настройку давления срабатывания клапана Danflo с помощью редуктора ER3000 из операторной НПС.
В качестве управляющего сигнала, на ER3000 подаётся калиброванный постоянный ток 4-20 мА. Зависимость
давления в полости клапана от тока - линейная.
Настройка по месту применяется при
неисправности редуктора ER3000 и предполагает использование ручного редуктора
давления Tescom.
Система автоматического
регулирования давления.
Затворы дисковые поворотные
(заслонки) предназначены для регулирования давления жидких сред, а также в
качестве запорно-регулирующих устройств трубопроводов.
Регулятор давления (рисунок 1.2)
представляет собой круглую дисковую заслонку с уплотнением, позволяющим
обеспечить перекрытие потока. Уплотнение затвора обеспечивается смещением оси
вращения диска и применением уплотняющего резинового шнура или наплавленного
уплотнения. Управление затворами дисковыми осуществляется с помощью
электропривода МИРД-600 («МИРД» - механизм исполнительный регулятора давления).
Работа узла регулирования давления
«до себя» №1 на НПС-21 производится заслонками диаметром 400 мм по одной из
следующих схем:
регулирование по последовательной
схеме двумя заслонками;
- регулирование по параллельной
схеме двумя заслонками;
регулирование одной заслонкой.
- фланец; 2 - дисковая заслонка; 3 -
уплотнитель; 4 - вал привода заслонки
Рисунок 1.2 - Конструкция регулятора
давления
Значение давления «до себя», которое
должен поддерживать узел регулирования №1 НПС-21, передается контроллером
единой системы управления (ЕСУ) в МПСА НПС-21. Значение прикрытия заслонок для
поддержания заданного значения давления «до себя» определяется МПСА НПС-21 по
ПИД-закону регулирования, который должен учитывать схему работы узла. Заслонки
регулирования имеют диапазон пропорциональности от 13° до 75°. Диапазон
регулирования положением заслонки ПИД-закона регулирования от 13° до 90°.
Программа МПСА НПС-21 при
формировании задания положения заслонок УРД №1 НПС-21 должна удовлетворять
следующим требованиям:
- при подаче уставки регулирования
давления от контроллера ЕСУ в МПСА равной 10 МПа производится закрытие заслонки
по линейному закону в течение 15 секунд;
при сохранении уставки в 10 МПа
заслонка удерживается в полностью закрытом положении;
при подаче уставки меньшей 10 МПа
при полностью закрытой заслонке производится её открытие до 13° по линейному закону
в течение 15 секунд;
- при открытии заслонки по
ПИД-закону более 75° производится полное открытие заслонки;
- при полностью открытой заслонке
заслонка удерживается в полностью открытом положении до снижения величины
регулирования ПИД-законом до 70°;
в остальных случаях положение
заслонки определяется величиной регулирования ПИД-закона.
Положение заслонки в 0° означает её
полное закрытие, в 90° - полное открытие. Отображение положения заслонки на АРМ
диспетчера должно выполняться в процентах закрытия.
Работа узла регулирования давления
«до себя» №2 на НПС-21 производится заслонками диаметром 400 мм по одной из
следующих схем:
- регулирование по параллельной
схеме двумя заслонками;
регулирование одной заслонкой.
Значение давления «до себя», которое
должен поддерживать узел регулирования №2 НПС-21, передается контроллером ЕСУ в
МПСА НПС-21. Значение прикрытия заслонок для поддержания заданного значения
давления «до себя» определяется МПСА НПС-21 по ПИД-закону регулирования,
который должен учитывать схему работы узла. Заслонки регулирования имеют
диапазон пропорциональности от 16° до 75°. Диапазон регулирования положением
заслонки ПИД-закона от 16° до 90° (при положении заслонок УРД №1 НПС-21 больше
или равном 13°) или от 32° до 90° (при положении заслонок УРД №1 НПС-21 меньше
13°).
Программа МПСА НПС-21 при
формировании задания положения заслонок УРД №2 НПС-21 должна удовлетворять
следующим требованиям:
- при открытии заслонки по
ПИД-закону более 75° производится полное открытие заслонки;
при полностью открытой заслонке
заслонка удерживается в полностью открытом положении до снижения величины
регулирования ПИД-законом до 70°;
в остальных случаях положение
заслонки определяется величиной регулирования ПИД-закона.
При работе алгоритмов управления
технологическим участком №2 предусматриваются алгоритмы перехода узлов УРД №1
НПС-21, УРД №2 НПС-21 из параллельной схемы на работу одной заслонкой и обратно
и перехода узла УРД №1 НПС-21 из последовательной схемы на работу одной
заслонкой и обратно.
Резервуарный парк.
Автоматизация РП должна
предусматривать:
автоматическую защиту
технологического оборудования РП;
автоматическую защиту РП при
поступлении сигнала «Пожар в резервуаре» от автоматизированной системы
управления пожаротушением (АСУ ПТ);
контроль параметров работы
технологического оборудования РП;
централизацию управления
резервуарным парком;
регистрацию и отображение информации
о работе оборудования РП.
Для централизованного управления
резервуарным парком система автоматизации должна выполнять функции:
- измерение уровня нефти в каждом
резервуаре;
измерение средней температуры нефти
в каждом резервуаре;
измерение температуры окружающего
воздуха на площадке РП;
измерение температуры нефти в
пристенном слое резервуара;
контроль скорости заполнения и
скорости опорожнения резервуара;
сигнализацию верхнего аварийного,
верхнего допустимого, верхнего нормативного, нижнего аварийного, нижнего
допустимого, нижнего нормативного уровня во всех резервуарах;
сигнализацию уровня аварийного
запаса в резервуарах, используемых для приема аварийного сброса нефти;
сигнализацию минимального
допустимого уровня, обеспечивающего безаварийную эксплуатацию системы размыва
донных отложений;
сигнализацию достижения предельной
максимальной скорости заполнения, аварийной максимальной скорости заполнения,
предельной максимальной скорости опорожнения, аварийной максимальной скорости
опорожнения;
сигнализацию превышения давления в
трубопроводах резервуарного парка;
дистанционное управление и контроль
режима работы системы размыва донных отложений в резервуарах;
дистанционное и автоматическое
управление задвижками резервуарного парка и сигнализацию их положения.
Автоматическая защита оборудования и
сооружений резервуарного парка должна предусматриваться по параметрам,
указанным в приложении Б (таблица Б.1).
Для защиты резервуара от
переполнения система автоматизации подает команды на закрытие всех коренных
задвижек приемо-раздаточных патрубков (устройств) резервуара при достижении в
резервуаре верхнего допустимого уровня нефти. Данная защита «Верхний допустимый
уровень в резервуаре» имеет выдержку времени 3 секунды и выполняет все функции.
Для формирования сигнала «Верхний
допустимый уровень в резервуаре» должен использоваться сигнализатор уровня, не
связанный с измерителем уровня.
Условием формирования защиты
«Верхний допустимый уровень в резервуаре» является получение системой
автоматизации сигнала хотя бы от одного сигнализатора верхнего допустимого
уровня.
Для защиты резервуара при понижении
уровня до нижнего допустимого уровня в резервуаре система автоматизации подает
команды на закрытие всех коренных задвижек приемо-раздаточных патрубков
(устройств) резервуара. Данная защита «Нижний допустимый уровень в резервуаре»
имеет выдержку времени 3 секунды и выполняет все функции, указанные в
приложении Б (таблица Б.1).
Настройка верхнего аварийного,
верхнего допустимого, верхнего нормативного, нижнего аварийного, нижнего
допустимого, нижнего нормативного уровня во всех резервуарах и уровня
аварийного запаса в резервуарах, используемых для приема аварийного сброса
нефти, должна производиться по утвержденным технологическими картами на
резервуары и резервуарные парки.
Сигнализация верхнего аварийного,
верхнего нормативного, нижнего аварийного, нижнего допустимого, нижнего
нормативного, минимального уровня, уровня, обеспечивающего безопасную работу
системы размыва донных отложений во всех резервуарах и уровня аварийного запаса
в резервуарах, используемых для приема аварийного сброса нефти, должна
формироваться на основании измерений, полученных системой измерения уровня
нефти в резервуаре.
В системе автоматизации при контроле
скоростей заполнения и опорожнения должна предусматриваться сигнализация:
«Предельная максимальная скорость
заполнения резервуара»;
«Предельная максимальная скорости
опорожнения резервуара»;
«Аварийная максимальная скорость
заполнения резервуара»;
«Аварийная максимальная скорость
опорожнения резервуара».
В качестве контролируемого параметра
должно учитываться усреднённое значение скорости заполнения или опорожнения
резервуара на основании измерений, полученных системой измерения уровня нефти в
резервуаре.
Аварийная максимальная скорость
заполнения резервуара устанавливается равной максимально допустимой скорости
заполнения резервуара. Предельная максимальная скорость заполнения резервуара
устанавливается равной 0,95 указанной величины.
Аварийная максимальная скорость
опорожнения резервуара устанавливается равной максимально допустимой скорости
опорожнения резервуара. Предельная максимальная скорость опорожнения резервуара
устанавливается равной 0,85 максимально допустимой скорости опорожнения
резервуара.
Срабатывание защиты «Аварийная
максимальная скорость заполнения резервуара» должно выполняться с выдержкой
времени 20 секунд. Система автоматизации подает команду на открытие задвижки на
линии приема нефти в резервуар, используемый для приема аварийного сброса
нефти, и выполняет остальные функции, указанныев приложении Б (таблица Б.1).
Действия системы автоматизации РП
при срабатывании защиты «Аварийная максимальная скорость заполнения резервуара»
для резервуара, используемого для приема аварийного сброса нефти, также
приведены приложении Б (таблица Б.1).
Срабатывание защиты «Аварийная
максимальная скорость опорожнения резервуара» должно выполняться с выдержкой
времени 20 секунд. Система автоматизации подает команду остановки первого по
ходу МНА на всех МНС, находящихся на линии откачки нефти из этого резервуара
(РП) и выполняет остальные функции.
Действия системы автоматизации РП
при срабатывании защиты «Аварийная максимальная скорость опорожнения
резервуара» для резервуара, используемого для приема аварийного сброса нефти.
Срабатывание защит:
- «Верхний допустимый уровень в
резервуаре, используемом для приема аварийного сброса нефти»;
«Аварийная максимальная скорость
заполнения в резервуаре, используемом для приема аварийного сброса нефти».
Должно формировать команды закрытия
задвижек на входе в РП и команды автоматической остановки МНА участка МН,
подключенного к РП.
Для защиты технологических
трубопроводов резервуарного парка от превышения давления должен выполняется
сброс нефти в резервуар аварийного сброса или в резервуар, предназначенный для
аварийного сброса.
При достижении давления в
технологических трубопроводах резервуарного парка значения «Давление открытия
первого предохранительного клапана», определенного в соответствии с
требованиями «Методики расчета требуемого количества предохранительных
клапанов, устанавливаемых на НПС с резервуарным парком», должна формироваться
сигнализация «Предельное максимальное давление в трубопроводах РП».
При достижении давления в
технологических трубопроводах значения на 0,05 МПа больше давления «Полного
открытия всех предохранительных клапанов», рассчитанного в соответствии с
требованиями «Методики расчета требуемого количества предохранительных
клапанов, устанавливаемых на НПС с резервуарным парком», должна формироваться
защита «Аварийное максимальное давление в трубопроводе РП». При этом
выполняется автоматическое открытие задвижки на линии приема в резервуары
аварийного сброса, установленной параллельно ПК.
В случае снижения давления в
технологических трубопроводах ниже «Предельного максимального давления в
трубопроводе РП» система автоматизации РП должна:
автоматически деблокировать защиту
«Аварийное максимальное давление в трубопроводе РП»;
сформировать команду на остановку
задвижки на линии приема нефти в резервуары аварийного сброса, установленной
параллельно ПК для прекращения ее открытия.
Датчик измерения давления в
технологических трубопроводах РП устанавливается перед (по потоку нефти)
задвижкой на линии подачи нефти в резервуар аварийного сброса нефти.
Для систем размыва донных отложений
с винтовыми перемешивающими устройствами в системе автоматизации необходимо
предусматривать:
контроль состояния электропривода
системы размыва;
контроль силы потребляемого тока
электропривода (при наличии требований завода-изготовителя и технической
возможности);
контроль виброскорости (при наличии
требований завода-изготовителя и технической возможности);
контроль вращения вала (при наличии
требований завода-изготовителя и технической возможности);
дистанционное отключение
электропривода.
Система автоматизации РП должна
обеспечивать отключение (блокировку включения) систем размыва донных отложений
в случаях, когда:
- уровень нефти в резервуаре выше
верхнего нормативного уровня или ниже минимального уровня, обеспечивающего
безопасную эксплуатацию системы размыва донных отложений;
получен сигнал «Пожар в резервуаре».
Минимальный уровень, обеспечивающий
безопасную работу системы размыва донных отложений для резервуаров составляет
5,0 м [3].
Вспомогательные системы.
Система приточно-вытяжной вентиляции
предназначена для вентиляции помещения насосной, а также для поддержания
температуры в насосном зале. На входе приточной вентиляции для этого установлен
калорифер.
Система включается (отключается при
отсутствии загазованности) от общей команды на пуск (отключение)
вспомогательных систем, поданной оператором с клавиатуры или из РДП по каналам
телемеханики (при условии, что вентиляторы находятся в режиме автоматического
управления). В этом случае приточно-вытяжная вентиляция включается для продувки
насосного отделения перед запуском станции и для работы во время работы
станции. Вентиляторы включаются (отключаются) также по команде из операторной
на включение (отключение) данного вентилятора.
Система вентиляции включается так же
автоматически (если она по каким-то причинам была отключена) при возникновении
загазованности в общем укрытии или маслоприямке, при этом дополнительно
автоматически на параллельную работу включается резервный вытяжной вентилятор.
Система автоматики приточно-вытяжной
вентиляции предназначена для контроля за работой вентиляции, пуска и останова
вентиляции.
В состав системы автоматизации
входят следующие элементы:
датчик загазованности ДГО;
датчик-реле давления;
датчик температуры TGP - 100P.
Датчик давления разряжения
устанавливается после вентиляторов для контроля давления на выходе
вентиляторов. Если давление не развивается за
заданный промежуток времени или
исчезает во время работы, то система переходит на резервный вентилятор.
При снижении температуры в насосной
ниже 20°С к системе приточной вентиляции подключается калорифер для поднятия
температуры.
Датчик температуры теплоносителя,
предназначен для контроля температуры воды в радиаторе калорифера, так как при
понижении температуры в зимнее время возможно замерзание калорифера.
Маслосистема предназначена для
принудительной смазки и охлаждения подшипников насосов и электродвигателей
магистральных агрегатов.
В состав маслосистемы входят:
основной насос Allweiler Screw Pump;
вспомогательный насос с
электроприводом;
масляный бак емкостью 4 м³;
дуплексный фильтр;
теплообменник.
Во время работы маслосистемы
осуществляется контроль следующих параметров:
давление масла на всасывании и
нагнетании насоса;
температура масла на сливе из
подшипников;
температура воздуха в системе
охлаждения двигателя.
2. Патентная проработка
.1 Выбор и обоснование
предмета поиска
В дипломном проекте поставлена
задача анализа системы автоматизации, установленной на НПС-21 «Сковородино».
Основным показателем, характеризующим работу станции, является количество
перекачиваемой нефти. Для ведения оперативного учета нефти применяют
расходомеры на входе и выходе НПС. С целью улучшения показателей надежности
системы измерения расхода было принято решение об установке дополнительного
расходомера на входе НПС. При выборе средства измерения расхода предпочтение
было отдано ультразвуковым расходомерам с несколькими измерительными лучами.
2.2 Регламент патентного
поиска
Патентный поиск проводился с
использованием фондов УГНТУ по источникам патентной документации Российской
Федерации.
Поскольку технические средства
автоматизации развиваются быстрыми темпами, была выбрана глубина поиска 5 лет
(2006-2010 гг.).
Поиск проводился по индексу МПК G 01
F 1/66 «Измерение объема или массы жидкостей, газов или сыпучих тел путем
пропускания их через измерительные устройства непрерывным потоком c измерением
частоты, фазового сдвига, времени распространения электромагнитных или других
волн, например ультразвуковые расходомеры)».
При этом были использованы следующие
источники патентной информации:
· полные описания к патентам Российской Федерации;
· документы справочно-поискового аппарата;
- официальный бюллетень Российского
Агентства по патентам и товарным знакам «Изобретения» (2006 г.);
официальный бюллетень Российского
Агентства по патентам и товарным знакам «Изобретения. Полезные модели»
(2006-2010 гг.).
2.3 Результаты поиска
Результаты просмотра источников
патентной документации приведены в таблице 2.1.
Таблица 2.1 - Результаты патентного
поиска
Страна
|
Индекс МПК
|
Номера просмотренных патентов
|
Выявленные аналоги
|
Россия
|
G 01 F 1/66
|
2281648-2398191
|
№2319933 «Измеритель объема жидкости, транспортируемой по
нефтепроводу» №2353905 «Ультразвуковой расходомер» №2392588 «Система
многопутевого ультразвукового измерения параметров потока частично развитых
профилей потока»
|
2.4 Анализ результатов
патентного поиска
Анализ просмотренных устройств
показал, что измерение расхода происходит за счет измерения времени прохождения
ультразвуковой волны по направлению потока и против него. Для определения
характера потока (ламинарный, турбулентный, переходный) применяется измерение
различных скоростей по профилю потока. Рассмотрим аналоги, приведенные в
таблице 2.1, более подробно.
Измеритель объема жидкости,
транспортируемой по нефтепроводу (№2319933) содержит первый и второй
электроакустические преобразователи, первый фазовый детектор, первый счетчик
электрических импульсов, первый цифроаналоговый преобразователь. Особенность
расходомера в том, что с целью повышения точности и надежности измерения, он
снабжен дополнительными четырьмя формирователями электрического импульсного
сигнала заданной постоянной длительности, двумя формирователями импульсного
электрического сигнала, длительность которого управляется входным электрическим
сигналом.
Ультразвуковой расходомер (№2353905)
содержит управляемый коммутатор, генератор зондирующих импульсов,
приемно-усилительный тракт, компаратор, схему формирования уровня, схему
измерения времени. Особенность расходомера в том, что происходит излучение
ультразвуковой волны по потоку и против него и преобразование ультразвуковой
волны в электрический синусоидальный сигнал с последующим преобразованием его в
последовательность прямоугольных импульсов. Величину исходного уровня опорного
сигнала устанавливают ниже амплитуды первой полуволны синусоидального сигнала.
Система многопутевого
ультразвукового измерения параметров потока частично развитых профилей потока
(№2392588) содержит: ультразвуковой расходомер с множеством пар датчиков,
сконфигурированных для формирования множества путей измерения в трубе, при этом
множество путей измерения размещается асимметрично относительно осевой линии
трубы; и блок управления. Множество пар датчиков соединено с блоком управления,
содержащим процессор и запоминающее устройство. Причем запоминающее устройство
хранит программу, имеющую инструкции для определения скорости потока текучей
среды на основе модели потока. Модель потока выбирается па основе сравнения оцененного
числа Рейнольдса текучей среды с выбранным диапазоном чисел Рейнольдса.
Таким образом, использование
приборов, позволяющих измерять расход на основе применения свойств ультразвука,
вполне актуально.
3. Автоматизация НПС-21
«Сковородино»
.1 Структура системы
автоматизации
Структурная схема системы
автоматизации приведена на рисунке 3.1. Она скомплектована стойкой центрального
процессора НПС, расположенной в шкафу устройства связи с объектом (УСО) 1.0. В
котором расположены два контроллера с горячим резервированием, соединенным со
шкафами УСО 1.1.1 - УСО 1.1.5 для контроля давления на приеме и выкиде НПС, для
сигнализации об уровне нефти в емкости сбора утечек ЕП-40, для сигнализации о
прохождении очистных устройств и т.д. Так же в операторной находятся:
контроллер РП и ПНС (УСО 2.0), контроллер АСУ ПТ (УСО 1.0П), контроллер
аварийных защит (КАЗ), АРМ НПС, ПНС и РП (основное и резервное), АРМ линейной
части, АРМ АСУ ПТ, серверный шкаф «А», серверный шкаф «В». Постоянство работы
шкафов УСО и контроллеров обеспечивается за счет шкафов источников
бесперебойного питания. Серверные шкафы через аппаратуру связи имеют соединение
с территориальным диспетчерским пунктом (ТДП), шкафами линейной телемеханики. GPS антенна здесь является
резервным средством связи.
Первичные приборы расположены в
общих укрытиях основных и вспомогательных систем НПС. Вторичные приборы
контроля технологических параметров насосной станции размещаются в приборных
шкафах, которые расположены в операторной, ЗРУ - 10 кВ, в помещении насосной.
Связь между УСО
осуществляется через блок для соединения оптического кабеля ШКО-Н-СТ (по месту)
и ШКО-Н-ГИ (операторная) по дублированному оптическому кабелю ОКБс-нг-0.7
(62.5) - 8. Связь и передача данных между контроллерами осуществляется по сети FTE. Передача данных на
верхний уровень (АРМ операторов) осуществляется также по сети FTE.
АРМ системы контроля за нормативными
параметрами установлено в помещении операторной и подключено к системе
диспетчерского контроля и управления (СДКУ).
.2 Функции системы
автоматизации
Система автоматизации основной и
подпорной насосной НПС-21 «Сковородино» обеспечивает выполнение следующих
функций:
пуск и остановка магистральных и
подпорных насосных агрегатов из операторной, РДП, ТДП;
защита оборудования НПС;
контроль и управление оборудованием
НПС;
регулирование технологических
параметров;
контроль и анализ заданных режимов
работы;
отображение информации;
регистрация информации;
составление отчетов и сводок;
ведение архива;
работа в составе СДКУ;
информационный обмен с другими
системами контроля и управления;
самоконтроль и самодиагностика
аппаратных средств.
3.3 Функциональная схема
автоматизации магистрального насосного агрегата
Магистральный
насосный агрегат состоит из магистрального насоса, мультипликатора,
электродвигателя. Спецификация приборов контроля нормативных параметров работы
МНА приведена в таблице 3.1. Защита МНА по параметрам перекачиваемой жидкости
обеспечивается датчиками давления (поз. 10-2, 11-1), контролирующими давление
во всасывающем и нагнетательном трубопроводах. Давление во всасывающем
трубопроводе ниже минимально допустимого характеризует кавитационный режим
работы насоса. Защита по минимальному давлению всасывания (поз. 8),
осуществляется с выдержкой времени 15 с, благодаря чему исключается реакция
схемы защиты на кратковременное снижение давления при включении насосов и
прохождении по трубопроводу небольших воздушных пробок. Датчик на всасывающем
трубопроводе дает сигнал в схему управления агрегатом, прерывая процесс запуска
в случае отсутствия требуемого давления после открытия задвижки на всасывающем
трубопроводе. Датчик давления на нагнетательном трубопроводе обеспечивает
автоматическую остановку агрегата, если давление на нагнетательном трубопроводе
превышает максимально допустимое.
Таблица 3.1 -
Спецификация оборудования
Позиция
|
Наименование
|
Количество
|
1
|
Термопреобразователь ТСМУ-205
|
1
|
2
|
Виброконтроллер СВКА-1-02
|
1
|
3-1, 3-2, 15-1, 15-2, 16-1, 16-2
|
Датчик температуры Метран 243 (50М)
|
6
|
4
|
Датчик температуры СгТ-04
|
1
|
5, 18
|
Датчик температуры ТСПУ
|
2
|
6
|
Датчик температуры ТСМ
|
6
|
7, 14
|
Измеритель ОМь-4.04
|
2
|
8
|
Контроллер ЭЛЕСИ
|
1
|
9
|
Блок управления задвижкой БУ-50
|
2
|
10-1, 11-2, 17-2
|
Манометр показывающий Метран
|
3
|
10-2, 11-1
|
Датчик давления Honeywell ST 3000
|
2
|
12
|
АРМ оператора
|
1
|
13
|
Прибор контроля утечек OMUV 05-04
|
1
|
17-1
|
Реле давления TRIPOINT
|
1
|
Система также
контролирует давление масла подшипников насоса, мультипликатора и
электродвигателя (поз. 17), контроль осуществляется взрывозащищенными реле
давления.
Контроль утечек из торцевых
уплотнений насосов (поз. 13), осуществляемый датчиком контроля утечек необходим
в связи с тем, что превышение допустимого уровня утечек служит сигналом
разрушения торцевых уплотнений.
Для контроля температуры подшипников
МНА применяются датчики температуры Метран 243 (50М). Температура корпуса
насоса (поз. 4) контролируется датчиком температуры СгТ-04. Температура
подшипников МНА, а также корпуса насоса требует постоянного контроля, т.к. в
процессе непрерывной перекачки нефти возможны нарушения в работе
технологического оборудования (отказ маслонасосов), из-за чего может произойти
расплавление подшипников, как следствие повысится вибрация, нарушится торцовое
уплотнение. Это может привести к выбросу нефти и возгоранию.
Температура подшипников контролируется:
у насоса (поз. 3-1);
у мультипликатора датчиками (поз.
15-1);
у электродвигателя датчиками (поз.
16-1).
Также в систему температурного
контроля насосного агрегата входит контроль:
температуры железа и меди статора
электродвигателя (поз. 6);
температуры холодного и горячего
воздуха корпуса электродвигателя (поз. 5-1, 18-1).
Контроль вибрации насоса и
электродвигателя позволяет установить нарушения в работе агрегата, вызываемые
некачественной сборкой, появлением дисбаланса, износом подшипников и др.
Контроль вибрации осуществляется на передних и задних подшипниках (поз. 2-1)
системой вибродиагностики СВКА-1-02 (поз. 2-2). Датчики контроля вибрации
контролируют вибросмещение и виброускорение в точке контроля электродвигателя и
насоса.
Контролируемыми параметрами по
насосному агрегату, кроме рассмотренных выше, являются: активная и реактивная
мощности на валу электродвигателя и ток двигателя, измеряются цифровым
преобразователем мощности (поз. 7, 14) типа ОМь.
Противоаварийная защита производит
отключение работающего агрегата и подает команду на запуск агрегата,
находящегося в состоянии «горячего» резерва. Обеспечение выдержки времени и
управление работой агрегата осуществляется на базе контроллера типа ЭЛЕСИ().
Отображаемый на АРМ оператора (поз.
12) формат воспроизводит технологические узлы магистрального насосного агрегата
(насос, электродвигатель, задвижки на всасывании и нагнетании, технологические
линии вспомогательных систем). Отображаемый формат содержит следующую
переменную информацию:
текущее значение давления на выходе
насосного агрегата, МПа;
достижение минимального аварийного
значения давления на линии подачи масла к электродвигателю агрегата;
достижение минимального аварийного
значения давления на линии подачи масла к насосу агрегата;
достижение максимального аварийного
и максимального значения вибрации агрегата;
текущее значение температуры
подшипников насоса, электродвигателя и возбудителя;
текущее значение температуры корпуса
насоса;
текущее значение температуры обмоток
и воздуха электродвигателя;
текущее значение температуры в зоне
горячего воздуха электродвигателя;
текущее значение вибрации на
переднем подшипнике вала насоса;
текущее значение вибрации на заднем
подшипнике вала электродвигателя насоса;
текущее значение вибрации на переднем
подшипнике вала электродвигателя;
текущее значение вибрации на заднем
подшипнике вала электродвигателя;
текущее значение активной мощности
электродвигателя;
текущее значение реактивной мощности
электродвигателя;
текущее значение силы тока
электродвигателя;
разрешение на пуск магистрального
насосного агрегата с ручной панели;
пуск магистрального насосного
агрегата с ручной панели;
текущее состояние задвижек на приеме
и нагнетании агрегата (открыта, открывается, закрыта, закрывается, в
промежуточном положении, неисправна, авария);
объем утечек из торцовых уплотнений
насоса.
3.4 Виброконтроллер
СВКА-1-02
В состав устройства виброконтроля
входят:
вибропреобразователь АНС-066-02
(рисунок 3.3);
блок электронный СВКА-1-02 (рисунок
3.4)
коробка распределительная КР-11.
Устройство выдает сигнал:
по постоянному напряжению от 0,1 до
5 В, заданный среднеквадратичным детектором в полосе рабочих частот. Выходной
сигнал обеспечивается на нагрузке не менее 100 кОм при емкости не более 10000
пФ. Предусмотрена цифровая индикация выходного сигнала с автоматическим или
ручным переключением измерительного канала;
по постоянному току в шкале 4-20 мА.
Выходной сигнал обеспечивается при сопротивлении нагрузки 0-500 Ом и емкости
нагрузки 20 нФ;
по переменному напряжению от 0,1 до
5 В, пропорциональный мгновенным значениям виброскорости в полосе рабочих
частот;
цифровой выход - интерфейс RS 485.
Устройство имеет двухуровневую
сигнализацию. Диапазон регулирования порогов срабатывания сигнализации:
предельный 3-12 мм/с;
аварийный 5-15 мм/с.
Погрешность срабатывания
сигнализации не более ± 5%. Электропитание устройства осуществляется от
источника постоянного тока напряжением (27±5) В, или источника переменного тока
220 В.
3.5 Прибор контроля
утечек ОМЮВ 05-04
Данный прибор является так
называемым прибором выключения уровня в сосуде с постоянным давлением, который
в случае свободного течения может применяться и для сигнализации потока
жидкости.
Блок обработки сигнала 1 крепится на
фланце 2. В поплавковой камере находятся поплавок 3 и зонд 4. Поплавок,
сваренный под защитным газом аргон из стали марки КО-36 перемещается вверх и
вниз по зонду в зависимости от уровня жидкости. Внутри поплавка расположен
кольцевой магнит, который на определенных уровнях включает заключенные в
пластмассовую оболочку магнитные выключатели. Основной размер: 250 мм, по
отдельному заказу размер может быть изменен.
При таком применении из системы
можно выпустить воздух с помощью вентиля, встроенного в корпус поплавковой
камеры.
3.6 Датчик контроля
герметичности камер ДГК-1
Датчик контроля герметичности камер
пуска-приема средств очистки и диагностики ДГК-1 (рисунок 3.4) предназначен для
непрерывного автоматического контроля герметичности узлов пуска и приема
очистных и диагностических устройств линейной части магистральных и
межпромысловых нефтепроводов и примыкающей к ним запорной арматуры, в том числе
нарушения герметичности, вызванные несанкционированным доступом к этим узлам.
При возникновении утечки датчик герметичности камер обнаруживает ее и передает
информацию об этом в автоматизированную систему управления нефте- или
продуктопроводом. В приборе реализован непрерывный самоконтроль исправности,
входящих в его состав блоков и, в случае появления неисправности, информация об
этом передается в автоматизированную систему управления.
Датчик герметичности камер
устанавливается на камерах пуска-приема без нарушения их целостности (на
внешней поверхности стенки камеры) на один слой пленочной изоляции. Датчик
герметичности камер имеет блочное исполнение и состоит из: датчика
акустического, коробки соединительной и блока питания и реле.
В комплект прибора может входить от
одного до трех акустических датчиков и, соответственно, от одного до трех
коробок соединительных. Характеристики датчика герметичности ДГК-1 приведены в
таблице 3.2.
Таблица 3.2 - Характеристики датчика
герметичности ДГК-1
Параметр
|
Значение
|
Пороговая чувствительность в зоне 50 м по расходу нефти, не хуже
|
50 л/ч
|
Время обнаружения утечки с момента ее возникновения, мин
|
2
|
Электрическое питание от сети переменного тока
|
(220 ± 22) В; 50Гц
|
Потребляемая мощность
|
не более 7ВА
|
Режим функционирования
|
непрерывный (круглосуточный)
|
Максимальное удаление датчиков от блока питания и реле
|
не более 1000 м
|
Условия эксплуатации блока питания и реле
|
от -20° до +40°С
|
Условия эксплуатации акустического датчика
|
от -50° до +50°С
|
Средняя наработка на отказ
|
не менее 15000 часов
|
Устройство и работа прибора.
Датчик акустический структурно
содержит приемный преобразователь и предварительный полосовой усилитель.
Конструктивно датчик акустический
выполнен в виде герметичного корпуса, на котором закреплена плита с постоянными
магнитами, служащими для установки датчика на стенку камеры. От корпуса через
герметизированный кабельный вывод отходит кабель, соединяющий акустический
датчик с соединительной коробкой. Для улучшения акустического контакта между
приемным преобразователем и стенкой камеры применяется консистентная контактная
смазка.
Соединительная коробка содержит три
элемента: анализатор, вспомогательный индикатор и клеммную колодку.
Схема анализатора преобразует
поступающий на его вход с датчика акустического аналоговый сигнал в
широтно-модулированные сигналы, несущие информацию об интенсивности
акустических сигналов, регистрируемых датчиком акустическим. Детектор исправности,
входящий в состав анализатора сравнивает по уровню сигнал, поступающий с
основного полосового усилителя с некоторым эталонным значением. Если уровень
сигнала превышает эталон, формируется сигнал «контроль» («исправность»),
который поступает на блок питания и реле.
Микропроцессорный контроллер в
составе узла коммутации БПР производит анализ сигналов, поступающих на вход
блока и на их основе, вырабатывает сигналы «Утечка» и «Исправность».
Блок питания и реле вырабатывает
напряжение питания для аппаратуры всех каналов контроля герметичности камер
пуска-приема очистных устройств. При этом обеспечивается искрозащита цепей
питания в соответствии с ГОСТ Р51330.10-99 «Искробезопасная электрическая
цепь». Герконовые реле блока обеспечивают гальваническую развязку электрических
цепей от цепей линейной телемеханики.
Принцип работы прибора основан на
регистрации сигналов акустической эмиссии (акустического шума), возникающей при
истечении жидкости в камерах пуска-приема очистных устройств и в прилегающей
запорной арматуре при наличии внутри избыточного давления свыше 0,3 МПа.
Сигналы акустической эмиссии являются результатом:
турбулентных пульсаций
сопровождающих истечение жидкости;
кавитации, т.е. образованием и
схлопыванием газовых пузырьков, обусловленным сильным локальным понижением
давления в жидкости в местах возникновения утечки.
Кавитация сопровождается мощным
излучением звука, которое в месте возникновения утечки более чем на 40 дБ
превышает фоновые значения акустического сигнала в диапазоне частот от 10 до
100 кГц. Это позволяет с высокой достоверностью обнаруживать даже очень малые
утечки нефти и нефтепродуктов.
Акустический сигнал с помощью
преобразователя 1 преобразуется в электрический сигнал, который усиливается
предварительным полосовым усилителем 2 и поступает для дальнейшей обработки в
соединительную коробку. Преобразователь 1 и усилитель 2 входят в состав датчика
акустического. Сигнал, поступающий на аттенюатор 3 соединительной коробки,
может быть подвергнут различной (в зависимости от режима работы прибора)
степени ослабления. К выходу аттенюатора подключен основной полосовой усилитель
4, который обеспечивает усиление сигнала до уровня, необходимого для надежного
срабатывания компаратора 5. С выхода компаратора на счетный вход
счетчика-делителя 6 поступают импульсы, появление которых обусловлено
превышением амплитуды сигнала с выхода усилителя 4 над уровнем срабатывания
компаратора 5. Средняя частота импульсного сигнала на выходе компаратора 5
определяется интенсивностью акустического сигнала регистрируемого
преобразователем акустического датчика и, в свою очередь определяет частоту и
период импульсного сигнала на выходе сигнала делителя 6. Этот сигнал несет
информацию о возможной утечке в данном канале.
Сигнал с выхода счетчика-делителя 6
через ключевой формирователь 8 подается на микропроцессорный контроллер.
Микропроцессорный контроллер способен одновременно производить временной анализ
сигналов от 3-х подключенных каналов регистрации.
В основу принципа анализа сигналов
положено представление последовательности входных сигналов как некоторых
событий, обладающих определенными временными характеристиками и имеющих свою
предысторию развития в виде предыдущих событий. При отсутствии в канале
регистрации акустических помех отсутствует и предыстория событий, при этом, в
случае появления утечки, время принятия решения о подаче сигнала «Утечка»
минимально. Если акустические помехи, присутствуют в данном канале регистрации
и (или) в соседних каналах, то с учетом их интенсивности возрастает время
принятия решения о подаче сигнала «Утечка».
Кроме сигналов, несущих информацию о
возможных утечках, параллельно по 3-м каналам на микропроцессорный контроллер,
поступают сигналы подтверждения исправности регистрирующей аппаратуры каналов.
Для контроля герметичности камер
пуска-приема очистных и диагностических устройств и участков открытых
трубопроводов, когда акустические датчики пространственно разнесены и сигнал от
утечки не может одновременно регистрироваться двумя или тремя акустическими
датчиками. Необходимое количество подключенных к одному блоку питания и реле
акустических датчиков и соответственно соединительных коробок должно быть 2 или
3. При этом движок переключателя SA1 в блоке питания и реле на плате коммутации
должен быть в положение 1, а движок переключателя SA2 - в положение 2. Во всех
других случаях (для контроля герметичности закрытых грунтом участков
трубопроводов, для контроля задвижек) движок переключателя SA1 должен быть в
положении ON, движок переключателя SA2 в положение 2.
.7 Интеллектуальные датчики
ST 3000 фирмы Honeywell
Существует множество моделей
интеллектуальных датчиков ST 3000 для измерений, включающих один из основных типов давления:
- дифференциальное давление;
избыточное давление;
абсолютное давление.
Датчик измеряет давление процесса и
выдает выходной сигнал пропорциональный измеряемой величине 4-20 мА. Основные
компоненты - корпус электроники и корпус чувствительного элемента.
Датчик серии ST 3000 может выдавать
выходной сигнал либо аналоговый 4-20 мА, либо цифровой с использованием
протокола DE для непосредственной цифровой связи с системой TPS, ПЛК Allen
Bradley и другими системами управления. Кроме переменной процесса датчик также
выдает температуру корпуса чувствительного элемента в виде вторичной
переменной, которая доступна как параметр только для чтения через SFC, когда
датчик работает в аналоговом режиме.
Основой любой модели датчика
давления Honeywell является тензочувствительный элемент. Это, как правило,
четыре идентичных тензорезистора, имплантированных в канавки, которые вытравлены
на поверхности кремниевой мембраны и соединены по мостовой схеме. Внешнее
давление вызывает деформацию мембраны, что приводит к разбалансировке моста.
Значение создаваемого напряжения рассогласования (полезный сигнал) прямо
пропорционально приложенному давлению. Этот принцип заложен в основу работы
любого датчика Honeywell, однако этим сходство между приборами ограничивается.
Любой датчик измеряет разницу
давлений, подведенных с разных сторон мембраны. Как правило, одно из них
прилагается через порт подвода со стороны тензорезистивного моста мембраны.
Давление с противоположной стороны мембраны является опорным и определяет тип
датчика. Компания Honeywell производит датчики для измерения всех существующих
типов давления: абсолютного, дифференциального, избыточного и вакуумного.
По типу выходного сигнала датчики
давления Honeywell можно разделить на четыре группы: 1 - базовые, 2 -
термокомпенсированные, 3 - термокомпенсированные с нормализованным выходным
сигналом, 4 - электромеханические реле давления.
Базовая структура датчиков самая
простая и недорогая. Ее недостаток - сильная зависимость передаточной
характеристики от температуры и большой разброс напряжения смещения от образца
к образцу. Несмотря на это, Honeywell выпускает несколько семейств приборов по
базовой схеме. Высокий спрос на такие приборы обусловлен тем, что во многих
приложениях нет необходимости в точном измерении, а требуется лишь грубая
оценка. Другая причина - специфические требования к датчику по точности,
стабильности, типу выходного сигнала и конструктивному исполнению. Решить
проблему можно, спроектировав собственное уникальное изделие на основе базового
преобразователя.
Термокомпенсированные датчики
давления отличаются от базовых моделей более сложной структурой чувствительного
элемента. Они содержат набор тонкопленочных термисторов и резисторов с
сопротивлением, которое подгоняется лазером в процессе изготовления сенсора. В
установленном диапазоне рабочих температур (как правило, 0-85°C) выходной
сигнал значительно стабильнее, а разброс напряжения смещения не превышает ±1 мВ
при размахе выходного напряжения 70-100 мВ. Датчики, имеющие температурную
компенсацию и калибровку, наиболее популярны благодаря оптимальному соотношению
«цена / стабильность» и простоте схем. Еще одно преимущество данной категории
датчиков - возможность замены вышедшего из строя устройства без перекалибровки.
Эти приборы в среднем на 30-35% дороже базовых датчиков.
Датчики с температурной компенсацией
и нормализованным выходным сигналом, кроме цепей термокомпенсации и калибровки
смещения, оснащены схемой линеаризации передаточной характеристики и
преобразователем. Преобразователь формирует один из стандартных типов выходного
сигнала:
- пропорциональный выход по
напряжению: размах выходного напряжения во всем диапазоне измеряемых давлений
линейно зависит от напряжения питания;
24-х или 34-х проводной токовый
выход: 4-20 мА при напряжении источника питания от 9 до 35 В;
- стабилизированный выход, где
размах выходного напряжения во всем диапазоне давлений лежит в пределах от1 до
6 В и не зависит от напряжения источника питания;
частотный выход, как правило, от 1
до 6 кГц (частота следования импульсов пропорциональна величине давления).
Большинство датчиков содержат схемы
подавления шумов источника питания, защиты от случайной смены полярности
питания и его резких выбросов. Электромеханические реле давления предназначены
для коммутации силовых или малосигнальных электрических цепей. Когда
подведенное к датчику давление достигает пороговой величины, происходит размыкание
(или замыкание) контактов датчика.
3.8 Расходомер Uniflow 990 DVN фирмы
«Controlotron»
Приборы измерения расхода нефти
предназначены для контроля количества перекачиваемой нефти и обнаружения утечек
нефти и использования этих данных в цепях автоматики.
Система измерения расхода нефти Uniflow 990 DVN - представляет из себя
поточный накладной двухканальный ультразвуковой расходомер. Обладая
способностью измерения скорости распространения звука в жидкости и измерения
температуры система позволяет определять плотность перекачиваемой жидкости.
Расходомер служит для:
контроля количества перекачиваемой
нефти;
обнаружения утечек.
Рассчитанная на трубы диаметром от
1,25 до 240 дюймов, система может работать со всеми типами жидкостей
(независимо от толщины стенок). Система включает в себя:
·
комплект кабелей серии 992CN для подключения
датчиков (на каждый канал);
·
температурный датчик серии 991TS;
·
кабель серии 992ECN для подключения температурного датчика;
·
узел крепления температурного датчика, серия 992EMTN;
·
контроллер расхода серии Uniflow 990VN;
·
приставку контроля и вывода данных для подключения и ручного
управления.
Относительная погрешность системы
0,5% при подлинной калибровке. Чувствительность 0,03 м/сек даже при нулевом
расходе.
Датчики расхода одной серии
настраиваются парами, перед установкой необходимо убедиться, что их серийные
номера совпадают. Датчики собираются на направляющей планке, закрепляются
нержавеющими полосами к трубе, на предварительно зачищенное место установки.
Установленные датчики находятся в герметичных колодцах (кессонах).
Контроллер устанавливается в
обогреваемом ящике и соединяется с датчиками коаксиальными кабелями через
соединительные коробки. Контроллеры питаются от сети переменного тока 220 В.
Тумблеры включения питания контроллеров и обогрева коробок находятся в
операторной НПС. Настройка параметров узла, установка системы Uniflow 990VN
выполняется с помощью меню на дисплее ручной приставки. С помощью встроенного
жидкокристаллического дисплея на крышке контроллера Uniflow 990DVN фиксируется
мгновенный объемный расход и с помощью накладного термометра - температура
нефти в градусах цельсия.
С помощью переносной приставки
контроля вывода данных (CDU) возможно снятие показаний:
объемного расхода в кубических
метрах в час;
температуры нефти в градусах
цельсия;
индикаторы статуса и сигнализаций и
направление потока;
аналоговые столбчатые диаграммы;
аналоговые полосные диаграммы,
выбранные данные и периодичность отчета;
цифровой регистратор данных,
выбранные данные и периодичность отчета.
4. Улучшение
метрологических и эксплуатационных характеристик системы измерения расхода
.1 Обоснование
необходимости замены и выбора расходомера
В соответствии с техническим
заданием Нерюнгринского РНУ на выходе первого УРД был установлен накладной
ультразвуковой расходомер PT868 фирмы Panametrics, выполняющий роль
дублирующего для основного расходомера. Основной расходомер Uniflow 990 DVN
фирмы Controlotron выполнен в виде накладных ультразвуковых первичных
преобразователей расхода (ППР), прикрепленных к трубопроводу с помощью
металлической ленты, и вторичной аппаратуры, установленной в шкафу. Основной
расходомер установлен на входе НПС на магистральном нефтепроводе диаметром 1220
мм перед КПП СОД. Необходимость установки дублирующего расходомера вызвана
недостоверностью показаний основного расходомера после прохождения через него
средств очистки и диагностики, что проявляется как непродолжительные
отрицательные значения показаний расходомера.
Дублирующий ультразвуковой
расходомер фирмы Panametrics своей конструкцией аналогичен основному
расходомеру фирмы Controlotron. При установке накладных расходомеров основным
условием является однородность потока жидкости по скорости в месте установки.
Для выполнения этого условия расходомер устанавливают на прямом участке
трубопровода на расстоянии в 10 диаметров трубы после источника возмущения
потока и на расстоянии в 5 диаметров трубы перед ним, либо перед расходомером
устанавливают струевыпрямители для выравнивания профиля потока. В соответствии
с техническим заданием дублирующий расходомер установлен на расстоянии в 2
метра после регулятора давления с диаметром трубы 400 мм. Очевидно, что условие
однородности потока не выполняется. При запланированном объеме перекачки в 30
миллионов тонн в год средний расход нефти на входе НПС составляет 3500 т/ч или
4200 м³/ч, при диаметре трубы
400 мм скорость движения жидкости составляет 9 м/с.
Кроме того немаловажным фактором
является вибрация. ППР накладного расходомера устанавливаются на направляющей
планке и фиксируются на участке трубопровода металлической лентой или
фиксирующим устройством. При значении вибрации выше заданного возможно смещение
ППР относительно друг друга. Таким образом изменяется выдержанное расстояние
между ППР, что приведет к ухудшению точности измерения расхода, за счет
изменения времени прохождения ультразвука от одного ППР до другого.
Исходя из изложенного выше, следует
рассмотреть замену накладного ультразвукового расходомера PT868 фирмы
Panametrics, расположенного на первом УРД. Замена накладного расходомера
Uniflow 990 DVN фирмы Controlotron нецелесообразна вследствие следующих
факторов:
замена может быть произведена только
на бесконтактный расходомер, не имеющий внутри трубопровода выступающих частей,
для обеспечения беспрепятственного прохождения СОД;
текущий расходомер обеспечивает
заданную точность оперативного учета нефти с погрешностью ±1%;
установка врезного расходомера
диаметром 1220 мм нерентабельна, т.к. работы по монтажу займут времени больше
чем выделено на плановую остановку трубопровода и потребуют значительных
денежных затрат.
Как было отмечено ранее, наиболее
целесообразна установка врезного расходомера. Рассмотрим наиболее подходящие
типы врезных расходомеров.
Расходомер переменного перепада
давления (дроссельный).
Принцип действия таких расходомеров
основан на измерении величины перепада давления на сужающем устройстве.
Перепад давления в данном случае
зависит от расхода жидкости напрямую. В качестве сужающих устройств применяют:
диафрагмы, сопла, трубки Вентури. Диапазон измерения зависит от конструкции
сужающего устройства. Диафрагма закрепляется между двумя фланцами (камеры
диафрагмы). Камера 1 первая по ходу движения нефти, с давлением как в
трубопроводе до сужающего устройства. Камера 2 находится после диафрагмы под
давлением меньшим, чем до диафрагмы на величину перепада. Перепад давления на
диафрагме измеряется в камерах 1 и 2 дифференциальным манометром. С выхода
дифференциального манометра сигнал в виде изменения сопротивления поступает в
блок преобразования сигнала, где преобразуется в унифицированный выходной
сигнал постоянного тока. Внешний вид дроссельного расходомера показан на
рисунке 4.3 [4].
Положительными качествами данного
расходомера являются:
возможность установки в неоднородном
потоке;
не требуются прямолинейные участки
трубопровода до и после расходомера;
широкий диапазон измерения расхода
(в зависимости от конструкции сужающего устройства).
Отрицательные качества данного
расходомера:
безвозвратная потеря давления на
сужающем устройстве;
нельзя использовать при вибрации
более 6 мм/сек;
высокая погрешность измерения
расхода, ± 2%;
для изменения диапазона измерения
необходима замена диафрагмы.
Очевидно, что данный тип
расходомеров не подходит в качестве замены расходомера PT868 фирмы Panametrics
не только из-за несоответствия условиям эксплуатации, но и потому что давление
на выходе УРД-1 поддерживается регулятором давления «до себя» УРД-2 на уровне
1,3 МПа. То есть давление в камере 2 дроссельного расходомера будет постоянно
поддерживаться равным 1,3 МПа. Таким образом, измеряемый перепад давления на
диафрагме не будет отражать достоверное значение расхода жидкости.
Применение данного типа расходомеров
невозможно, рассмотрим следующий тип расходомеров.
Кориолисовый расходомер.
Кориолисовые расходомеры - приборы,
использующие для измерения массового расхода жидкостей, газов эффект Кориолиса.
Принцип действия основан на изменениях фаз механических колебаний U образных
трубок, по которым движется измеряемая среда. Сдвиг фаз пропорционален величине
массового расхода.
Привод заставляет трубки
вибрировать. Электромагнитный привод состоит из катушки, соединенной с одной
трубкой, и из магнита, соединенного с другой трубкой. Когда поток отсутствует
(в расходомере с двумя трубками) и происходит вибрация, различия в показаниях
двух датчиков отсутствуют. Если есть поток жидкости и привод создает вибрацию
трубок, то силы Кориолиса создают вторичную изгибающую вибрацию, которая
проявляется в небольшой разнице фаз относительных движений трубок. Это
обнаруживается датчиками в двух точках. Отклонение трубок, вызываемое силой
Кориолиса, имеет место только в том случае, когда одновременно присутствует
поток жидкости и вибрация трубок. Вибрация без потока или поток без вибрации не
дают каких-либо показаний прибора.
Достоинствами данного типа
расходомеров являются:
малая погрешность измерения (±
0,2%);
измерение объемного и массового
расхода, измерение плотности жидкости. Плотность жидкости может быть определена
путем измерения резонансной частоты колебаний трубок;
стойкость к вибрации за счет
сбалансированной измерительной системы;
монтаж без необходимости входных и
выходных прямых участков трубопровода.
Недостатки:
малый диаметр трубопровода (50 мм);
малый предел измерения (70 т/ч).
Не смотря на все достоинства
кориолисовых расходомеров, данный тип расходомеров в данном случае применять
невозможно вследствие малого предела измерения.
Турбинный расходомер.
Турбинные расходомеры используются в
трубопроводах диаметром от 4 до 750 мм, с давлением до 250 МПа, температурой от
минус 240 до плюс 700°С. Преобразователи расхода жидкости могут быть с
аксиальной турбинкой (рисунок 4.5) и с тангенциальной крыльчаткой. У первых
лопасти расположены по винтовой линии, а ось совпадает с осью потока. У вторых
ось перпендикулярна к направлению потока, а прямые лопасти расположены
радиально по отношению к оси. Крыльчатки применяют лишь при небольших диаметрах
труб, обычно до 50 мм.
Аксиальные турбинки весьма
чувствительны к вектору движения потока, поэтому в большинстве случаев на
входе, а иногда и на выходе в их конструкции предусматриваются неподвижные
лопатки, направляющие поток параллельно оси трубы. Изменением угла наклона хотя
бы одной из этих лопаток можно воздействовать на частоту вращения турбинки.
Турбинные расходомеры нельзя устанавливать рядом с местными сопротивлениями.
Наибольшее влияние на показания ряда
турбинных преобразователей расхода оказывают местные сопротивления, создающие
сильное одностороннее пережатие потока, а также сопротивления, вызывающие
винтовое движение. Применение мелкоячеистых сеток и других типов
струевыпрямителей на входе перед турбинным преобразователем оказывается также
весьма эффективным для устранения деформаций потока, вызываемых местными
сопротивлениями.
Большое значение для обеспечения не
только стабильности статической характеристики преобразователя расхода, но и
длительного срока его службы имеет надежная работа опор. Условия их работы
весьма тяжелые - высокая частота вращения турбинок, доходящая до нескольких
сотен оборотов в секунду, и отсутствие в большинстве случаев подачи смазочного
материала к подшипникам [5].
Турбинный расходомер серии API с самым большим
пределом измерения 3406 м³/ч не подходит в качестве замены, т.к. предел измерения
недостаточен для измерения данного расхода в 4200 м³/ч.
Ультразвуковой расходомер.
Рассмотрим возможность установки в
качестве дублирующего средства измерения ультразвуковой трех лучевой расходомер
UFM
3030 фирмы «KROHNE».
Три измерительных луча UFM 3030
воспроизводят трехмерный профиль распределения скоростей движения среды или
профиль потока, движущийся по измерительной трубе. Измерительные лучи
располагаются таким образом, что результаты измерений практически не зависят от
изменений профиля потока.
Для трубы диаметром 400 мм и
скорости потока 9 м/с диапазон измерения будет находиться в пределах от 202 до
7000 м³/ч, с погрешностью ±0,5%.
Третий измерительный луч позволяет
UFM 3030 учитывать условия измерений во всех режимах измерений (ламинарном и
турбулентном).
Благодаря тому, что измерительные
трубы приборов UFM 3030 выполнены из нержавеющей стали и не имеют подвижных
частей - не создается дополнительных потерь давления. Также эти преимущества
расходомера позволяют избежать повреждений, которые возникают в результате
абразивного эффекта из-за трения мелких частичек в продукте, что позволяет не
устанавливать фильтры на входе прибора.
Концептуальное улучшение
эксплуатационных характеристик прибора стали возможными благодаря применению
новаторской электронной технологии в комбинации с алгоритмом цифровой обработки
сигнала, что позволило получить стабильные и надежные измерения. Прибор имеет
улучшенную точность измерений и менее критичен к изменениям профиля потока, а
также присутствию в рабочем продукте твердых частиц и воздушных включений [6].
Расходомеры компактного исполнения
включают в свой состав моноблок, состоящий из ППР и сигнального конвертера.
Расходомеры устанавливается непосредственно на трубопроводе. ППР
устанавливается непосредственно на трубопроводе, а СК может быть отнесен в
удобное для эксплуатации место. СК представляет собой электронный блок, имеющий
дисплей с трехстрочным выводом информации. Электронный блок конвертера состоит
из 4 основных функциональных модулей.
Модуль 1 генерирует ультразвуковые
сигналы, контролирует работу сенсоров и управляет процессом высокоточного
измерения времени прохождения сигналов с помощью цифровой обработки сигнала DSP
(digital signal processor).
Модуль 2 принимает данные, прошедшие
цифровую обработку в DSP и обрабатывает с помощью микропроцессора μР2 в соответствии с
назначением, настройками прибора и параметрами ультразвуковых сенсоров,
установленными на заводе-изготовителе. Данные с DSP и данные с гальванически
развязанных входов используются для расчета параметров потока. При сбое
питания, последние данные измерения будут записаны в память EEPROM 2 (electrically erasable programmable read-only memory) - электрически стираемое
программируемое запоминающее устройство. В тоже самое время настройки прибора и
данные проверки работоспособности будут записаны в память EEPROM 1. Оба
устройства памяти предназначены на период хранения информации до 10 лет при
отсутствии питания.
Модуль 3 гальванически развязан от
всех остальных модулей. В его состав входят различные выходные и входные
сигналы. Все входные и выходные цепи имеют один общий вывод.
Модуль 4 - блок питания
расходомеров. Блок питания выполнен по импульсной схеме. Импульсный блок
питания SMPS (switching mode power supply) имеет широкий диапазон входного
переменного напряжения. Существует 2 различных варианта блока питания. Один
рассчитан на высокое входное переменное напряжение от 85 до 264 В, другой на
низкое напряжение 24 В постоянного или переменного тока [7].
Эксплуатационные характеристики
расходомера UFM 3030 позволяют измерять расход на входе НПС с заданной точностью.
Значение измеряемого расхода лежит в диапазоне измерения данного расходомера.
Использование трех лучей для измерения расхода позволяет измерять расход
жидкости в неоднородном потоке. Благодаря исполнению пар ППР в виде моноблока
исключается их смещение за счет воздействия вибрации. Следовательно,
рассмотренный расходомер может быть установлен взамен расходомера PT868 фирмы
Panametrics.
4.2 Методика поверки
расходомера UFM 3030
Операции поверки.
При проведении первичной и
периодических поверок должны быть выполнены следующие операции:
- проверка комплектации;
внешний осмотр;
опробование расходомера;
установка нулевой точки расходомера;
определение метрологических
характеристик.
Средства поверки.
При проведении поверки расходомеров
должны быть применены следующие средства поверки:
- установка поверочная,
соответствующая по диапазону расхода поверяемому расходомеру и имеющая
относительную погрешность не более ±0,15%;
частотомер электронно-счетный Ф-5035
ТУ 25-04.3092;
секундомер-таймер СТИ-1 ТУ 25-07
1363-77;
термометр ГОСТ 27544-87, диапазон
измерения от 0 до 100°С;
манометр, показывающий класса
точности 0,4 ГОСТ 2405-80. Предел измерения выбирается в соответствии с
рабочими условиями;
барометр-анероид БАММ ТУ
25-04-1618-72;
счетчик импульсов программный реверсивный
Ф-5007 ТУ 25-04-2271 -75;
частотомер 43-38 ЕЭ2.721.087 ТУ.
Условия проведения поверки.
При проведении поверки должны
соблюдаться следующие условия.
Окружающая среда - воздух с
параметрами:
·температура от 20 до 35°С;
·относительная влажность воздуха от
30 до 80%;
·атмосферное давление от 84 до 106,7
кПа;
Поверочная среда - вода по ГОСТ Р
51232 со следующими параметрами:
·температура от 10 до 30°С
·давление в трубопроводе не ниже 0,6
МПа;
Изменение температуры поверяемой
среды в процессе поверки ± 2°С. Конструкция поверочной установки и условия
поверки расходомера должны исключать возможность попадания воздуха в
трубопровод. Режим движения потока поверочной среды должен быть стационарным.
Изменение
среднего значения расхода в процессе поверки не должно превышать ±2,5% от
установившегося значения.
Проведение поверки.
Определение относительной
погрешности расходомера проводится при значениях расхода: Qmin; 0,25*Qmax; 0,5*Qmax (расход устанавливается с допуском ±10%).
При поверке методом измерения объема
в качестве значения образцового объема V0u используется значение объема жидкости, набранного в объемную меру
поверочной установки (или показания образцового счетчика). Значение образцового
расхода Qvo определяется по формуле:
(4.1)
где Vou - значение
образцового объема, измеренное объемной установкой, м; Тпр - время
налива жидкости, ч.
Показания объемной меры
установки (мерника)
необходимо
привести к 20°С по формуле:
(4.2)
где Voui - объем воды,
измеренное мерником, м3;
t - температура воды,°С;
β -
коэффициент объемного расширения воды, 1/°С;
i - индекс измерения.
При поверке методом
измерения массы, объем
определяется
по формуле:
(4.3)
где m0 - образцовая масса жидкости (показания весов), кг;
р - плотность жидкости, кг/м3.
Перед началом поверки на поверочной
установке с весовыми устройством необходимо определить по контрольному
манометру среднее давление жидкости, а по термометру - температуру в
трубопроводе испытательного стенда поверочной установки. На основании
измеренных значений температуры и давления по таблицам определяется плотность
поверочной жидкости. Значение образцового объемного расхода рассчитывается по
формуле (6.1).
Для снятия результатов
измерения среднего объемного расхода и объема с дисплея расходомера выполняются
следующие процедуры. Кнопкой на лицевой панели расходомер устанавливается в
режиме индикации поверяемого параметра. Перед каждым измерением в поверочной
точке производится регистрация начального значения объема VH. После пропуска жидкости через ППР
в данной поверочной точке регистрируется конечное значение объема Vк. По разности показаний рассчитывается измеренное значение объема
жидкости
:
(4.4)
где Vи - измеренное значение объема по устройству индикации, м3;
По импульсному выходу значение
объема, измеренное расходомером, определяется по показаниям частотомера,
подключенного к соответствующему импульсному выходу расходомера. Перед началом
измерения частотомер устанавливают в режиме счета и обнуляется. По стартовому сигналу
импульсы с выхода расходомера начинают поступать на вход частотомера. Объем
жидкости Vи прошедшей через
преобразователь расхода, определяется по формуле:
(4.5)
где N - количество импульсов,
подсчитанное частотомером;
К - коэффициент преобразования
расходомера, который равен:
(4.6)
Определение относительной
погрешности расходомера при измерении объема жидкости выполняется по формуле:
(4.7)
Измеренный средний
расход жидкости
,
прошедшей через расходомер, определяется по формуле:
(4.8)
где QVср - среднее значение объемного расхода, м3/ч;
Quj - значение расхода при j-ом измерении, м³/ч;
n - количество измерений.
Определение
относительной погрешности расходомера
при измерении среднего
объемного расхода жидкости выполняется по формуле:
(4.9)
Результаты поверки считаются
положительными, если относительные погрешности расходомера при измерении
объема, среднего объемного расхода жидкости не превышает ±0,5%.
Минимально необходимый объем
жидкости, пропускаемой через ППР при одном измерении, при регистрации показаний
с импульсного выхода расходомера должен быть таким, чтобы набрать не менее 500
импульсов. При регистрации показаний с дисплея необходимо набрать не менее 500
единиц младшего разряда. При невозможности выполнить поверку с остановкой
потока в трубопроводе, а также для сокращения времени поверки допускается
выполнять определение относительной погрешности расходомера при измерении
объема только по импульсному выходу.
4.3 Обработка
результатов поверки расходомера UFM 3030
При проведении поверки расходомера UFM 3030 фирмы «KROHNE» согласно утвержденной
методики поверки для ультразвуковых расходомеров диаметром до 400 мм, были
получены значения расхода: действительный расход воды в установке; расход,
измеренный поверяемым расходомером.
Среднее значение объемного расхода
было получено при помощи формулы (6.8). Во время поверки проводилось по две
группы измерений для каждого установленного значения расхода. В соответствии с
формулой (6.9) была посчитана относительная погрешность результата измерения
расхода на поверочной установке.
Результаты поверки расходомера UFM 3030 приведены в таблице
4.1. Анализируя результаты поверки можно обнаружить, что при поверке на эталоне
с номером 2984, относительная погрешность результата измерения величиной 0,52%
превышает заявленную производителем 0,5%. Превышение рассчитанной относительной
погрешности над заявленной производителем наблюдается только один раз. Данный
факт свидетельствует о наличии грубой погрешности в результате измерения.
Грубая погрешность в результате измерения возникает при нарушении условий
проведения поверки по какому-либо влияющему фактору. Результат измерения с
грубой погрешностью должен быть исключен при анализе метрологических
характеристик.
Таблица 4.1 - Результаты поверки
расходомера UFM 3030
Дата время
|
№ опыта
|
Хд
|
Номер эталона
|
|
|
|
2969
|
2970
|
2982
|
2984
|
2987
|
|
|
|
Х, м³/ч
|
δ, %
|
Х, м³/ч
|
δ, %
|
Х, м³/ч
|
δ, %
|
Х, м³/ч
|
δ, %
|
Х, м³/ч
|
δ, %
|
30.01.2008 10:03
|
1
|
55.2029
|
55.17365
|
-0.05
|
55.156
|
-0.08
|
-0.10
|
55.1814
|
-0.04
|
55.1244
|
-0.14
|
30.01.2008 10:07
|
2
|
55.1703
|
55.18207
|
0.02
|
55.15526
|
-0.03
|
55.15351
|
-0.03
|
55.14512
|
-0.05
|
55.14218
|
-0.05
|
30.01.2008 10:13
|
1
|
30.4456
|
30.42972
|
-0.05
|
30.43894
|
-0.02
|
30.43689
|
-0.03
|
30.44235
|
-0.01
|
30.43104
|
-0.05
|
30.01.2008 10:18
|
2
|
30.4299
|
30.42662
|
-0.01
|
30.42824
|
-0.01
|
30.43232
|
0.01
|
30.42464
|
-0.02
|
30.41333
|
-0.05
|
30.01.2008 10:24
|
1
|
4.23595
|
4.23697
|
0.02
|
4.23567
|
-0.01
|
4.23483
|
-0.03
|
4.23577
|
0.00
|
4.23583
|
0.00
|
30.01.2008 10:29
|
2
|
4.21741
|
4.23474
|
0.41
|
4.23529
|
0.42
|
4.23308
|
0.37
|
4.23136
|
0.33
|
4.23222
|
0.35
|
30.01.2008 10:35
|
1
|
0.797813
|
0.79886
|
0.13
|
0.80048
|
0.33
|
0.79923
|
0.18
|
0.79989
|
0.26
|
0.79997
|
0.27
|
30.01.2008 10:39
|
2
|
0.797748
|
0.79959
|
0.23
|
0.79999
|
0.28
|
0.79924
|
0.19
|
0.79938
|
0.20
|
0.79967
|
0.24
|
30.01.2008 10:47
|
1
|
0.324603
|
0.32529
|
0.21
|
0.32597
|
0.42
|
0.32609
|
0.46
|
0.32587
|
0.39
|
0.32553
|
0.29
|
30.01.2008 10:53
|
2
|
0.326366
|
0.32587
|
-0.15
|
0.32696
|
0.18
|
0.32721
|
0.26
|
0.32805
|
0.52
|
0.32699
|
0.19
|
30.01.2008 10:59
|
1
|
0.165713
|
0.16535
|
-0.22
|
0.16569
|
-0.01
|
0.16495
|
-0.46
|
0.16602
|
0.19
|
0.16543
|
-0.17
|
30.01.2008 11:05
|
2
|
0.165584
|
0.1652
|
-0.23
|
0.1649
|
-0.42
|
0.16511
|
-0.29
|
0.16564
|
0.04
|
0.16499
|
-0.36
|
30.01.2008 11:13
|
1
|
0.080637
|
0.08029
|
-0.44
|
0.08044
|
-0.24
|
0.08008
|
-0.69
|
0.08045
|
-0.23
|
0.08022
|
-0.50
|
30.01.2008 11:19
|
2
|
0.080496
|
0.08031
|
-0.23
|
0.08042
|
-0.09
|
0.08029
|
-0.26
|
0.08057
|
0.09
|
0.08063
|
0.16
|
В целом, значение относительной
погрешности не превышает официально заявленного значения в 0,5%. Соответственно
можно сделать вывод о том, что данное средство измерения пригодно для
эксплуатации и его метрологические характеристики не превышают заданных.
5. Безопасность и
экологичность на НПС
Темой данного дипломного проекта,
как уже отмечено ранее, является модернизация системы автоматики НПС-21
«Сковородино».
С целью обеспечения безопасности
производства при монтаже, эксплуатации и ремонте средств автоматизации, в
данном разделе необходимо дать характеристику производственной среды, в которой
будет произведена модернизация системы автоматики, и провести анализ опасных и
вредных производственных факторов.
Безопасность производства и
экологическая безопасность должны соблюдаться по всем видам работ, связанных с
монтажом, эксплуатацией и ремонтом средств автоматизации.
Нарушение требований правил техники
безопасности производства при монтаже, эксплуатации и ремонте средств
автоматизации может привести к авариям и производственным травмам, а
экологической безопасности - к загрязнению окружающей среды.
Вследствие того, что
нефтеперекачивающая насосная станция является вредным и опасным
производственным объектом, в данном разделе будут рассматриваться мероприятия
по безопасной эксплуатации оборудования и будет произведен анализ безопасной
работы средств автоматизации.
5.1 Анализ
производственных опасностей и вредностей
В предыдущих разделах дипломного
проекта рассматривалась технологическая схема НПС-21 «Сковородино» и система
автоматического управления технологическими процессами.
Первичные приборы контроля состояния
технологического процесса (датчики давления, уровня, температуры, расхода,
загазованности и т.д.) устанавливаются непосредственно в насосной, где в
процессе эксплуатации рабочей средой является нефть, попутный газ и возможно
возникновение взрывоопасных смесей, характеристики которых приведены в таблице
5.1.
Таблица 5.1 - Взрывопожароопасные и
токсические свойства веществ в рассматриваемой производственной среде
Наименование вещества на рассматриваемом объекте
|
Агрегатное состояние
|
Класс опасности веществ
|
Температура, 0С
|
Концентрационный предел взрываемости, % объем
|
Характеристика токсичности (воздействие на организм человека)
|
Предельно допустимая концентрация веществ в воздухе рабочей зоны
производственных помещений
|
|
|
|
вспышки
|
воспламенения
|
самовоспламенения
|
нижний
|
верхний
|
|
|
Нефть сырая
|
Ж(п)
|
4
|
-18
|
-
|
233
|
1,1
|
7,4
|
наиболее сильное влияние на ЦНС
|
10,0
|
Попутный нефтяной газ
|
Г
|
4
|
-
|
-
|
405…580
|
6,0
|
13,5
|
отравление организма
|
50
|
Пары нефтепродуктов действуют,
главным образом, на центральную нервную систему. Признаки отравления чаще всего
проявляются в головокружении, сухости во рту, головной боли, тошноте,
сердцебиении, общей слабости и потери сознания.
Попутный газ - бесцветная смесь
легких углеводородных паров, легко воспламеняется, обладает вредным воздействием
на организм человека и в зависимости от концентрации может произойти отравление
организма разной степени тяжести (ОБУВ составляет 50 мг/м3).
На быстроту поступления паров
нефтепродуктов из воздуха в кровь влияет их растворимость в воде, близкая к растворимости
в крови.
Нефтепродукты практически
нерастворимы в воде. Углеводороды способны растворяться в поту и жировом
покрове кожи, а затем всасываться через кожу и поступать в кровь. При этом
начинается головокружение, тошнота.
Перекачиваемая нефть легко
испаряется и способна образовывать взрывоопасную смесь. Нефтепродукты относятся
к легковоспламеняющимся веществам. Их пары с воздухом образуют взрывоопасную
смесь. Это выдвигает повышенные требования к надежности и эффективности пожаро-
и взрывозащиты. Пары нефтепродуктов способны создавать опасность воспламенения
от источника огня. Блуждающие пары тяжелее воздуха, поэтому они стелятся по
поверхности пола в цехе, затекают с воздухом и образуют горючие и взрывоопасные
смеси.
Пожароопасность технологических
процессов в значительной степени определяется физико-химическими свойствами
нефтепродуктов.
Классификация сооружений по НПБ
105-03 и ПУЭ приведена в таблице 5.2.
При обслуживании первичных датчиков
в насосном зале, возникает опасность воздействия на человека шума и вибрации,
источником которых является оборудование магистральных насосов и
электродвигателей.
Таблица 5.2 - Взрывопожарная и
пожарная опасность, санитарная характеристика производственных зданий,
помещений и наружных установок
Наименование производственных зданий, помещений, наружных
установок
|
Категории взрывопожароопасной и пожарной опасности зданий и
помещений (НПБ 105-03)
|
Классификация зон внутри и вне помещений
|
|
|
Класс взрывопожароопасной или пожароопасной зоны (ПУЭ и ПБ
08-624-03)
|
Категория и группа взрывопожароопасных смесей (ГОСТ 12.1.011-78)
Р51330.5-99 Р51330.11-99
|
Насосная
|
А
|
В-1а
|
IIA-T3
|
Операторная
|
Д
|
-
|
-
|
Длительное воздействие вибрации
высоких уровней на организм человека приводит к развитию преждевременного
утомления, нарушению вестибулярного аппарата, снижению остроты слуха, нередко к
возникновению профессиональной патологии - вибрационной болезни. Допустимые
уровни шума на рабочих местах нормируются документами СН 2.2.4/2.1.8.562-96
«Шум на рабочих местах, в помещениях жилых, общественных зданий и на территории
жилой застройки» и СНиП 23-03-2003 «Защита от шума» и не должны превышать 80
дБ.
Помещение насосной НПС содержит три
насосных агрегата HPDM 600-615-1d/27 фирмы «Sulzer» с синхронными
электродвигателями. Согласно ГОСТ 12.1.019-96, помещение насосной относится к
помещениям с повышенной опасностью, так как имеет токопроводящие полы,
возможно, одновременное прикосновение человека к соединяемым с землей
технологическим аппаратам с одной стороны и к металлическим корпусам средств
автоматизации с другой.
В процессе эксплуатации средств
автоматизации существует опасность поражения электрическим током. Приборы и
средства автоматизации находятся под напряжением 24 В постоянного тока. Так как
насосный зал имеет токопроводящие полы, то возможно, одновременное
прикосновение человека к соединяемым с землей технологическим аппаратом с одной
стороны и к металлическим корпусам средств автоматизации с другой.
Удар электрическим током вызывает
рефлекторную реакцию со стороны центральной нервной системы и ведет к нарушению
нормального ритма работы сердца. В результате наблюдается нарушение или полное
прекращение деятельности органов дыхания и кровообращения.
При монтаже, наладке, эксплуатации и
ремонте систем автоматики производственные опасности и вредности могут быть
обусловлены следующими факторами:
недостаточная освещенность насосного
зала при работе в темное время суток, вызывающая повышенную утомляемость,
замедляющая реакцию, что может явиться причиной травм;
воздействием атмосферного электричества
в насосном зале в летнее время. Прямой удар молнии, при котором ток может
достигать 200 кА, напряжение 100 кВ, а температура в канале молнии
приблизительно 25000 0С, вызывает разрушения большой силы;
при перекачке нефтепродуктов
создаются условия для накопления статического электричества с потенциалом до 80
кВ. Это является причиной нарушения технологических процессов, снижения
точности показания приборов автоматики, неблагоприятно отражается на здоровье
рабочих;
наличием давления в аппаратах трубопровода
до 10 МПа, в которых эксплуатируются приборы и средства автоматизации
производственных процессов. В случаях разгерметизации, отказа регулирующих
органов и приборов контроля системы автоматизации, а также при несоблюдении
требований ГОСТ 12.2.085-2002 «ССБТ. Сосуды, работающие под давлением. Клапаны
предохранительные», возможно возникновение аварийной ситуации;
воздействием движущихся и
вращающихся частей оборудования насосов при монтаже, демонтаже и эксплуатации
приборов и средств автоматизации;
воздействием шума и вибрации, как на
приборы, так и на обслуживающий персонал.
5.2 Мероприятия по
обеспечению безопасных и безвредных условий труда
В данном разделе рассмотрены правила
и требования, которые необходимо соблюдать, чтобы избежать воздействия вредных
и опасных производственных факторов, возникающих при монтаже, эксплуатации и
ремонте системы автоматизации НПС-21 «Сковородино» нефтепровода «Восточная
Сибирь - Тихий океан».
Мероприятия по технике безопасности
при эксплуатации объектов НПС-21 «Сковородино».
Согласно регламентам и правилам ПТЭ,
ПТБ, ПУЭ и РД 153-39.4-056-00, во избежание несчастных случаев при обслуживании
оборудования, направляемый на работу персонал должен иметь соответствующую
подготовку, пройти производственный инструктаж, ознакомиться с правилами
внутреннего распорядка, общими правилами техники безопасности и должностной
инструкцией на поручаемом ему для обслуживания участке или агрегате, а также с
методами оказания первой помощи. По окончании инструктажа направляемые на работу
сдают экзамен по технике безопасности в соответствии с ПБ 08-624-03 и другими
руководящими нормативными документами и получают удостоверение с присвоением
квалификационной группы. Инструктажи допуска персонала к самостоятельной работе
соответствуют требованиям ГОСТ 12.0.004-90 (1999) «ССБТ. Организация обучения
безопасности труда. Общие положения». Перед ремонтом оборудования должны быть
назначены ответственные лица за организацию и проведение ремонта, подготовку к
нему аппаратуры, оборудования и коммуникаций, выполнение мероприятий по
пожарной безопасности и охране труда, предусматриваемых планом организации и
проведения работ.
Для защиты от поражения
электрическим током при монтаже, эксплуатации и ремонте средств автоматизации,
согласно ГОСТ 12.1.030-81 (2001) «ССБТ. Электробезопасность. Защитное
заземление. Зануление» предусматриваются следующие мероприятия:
защитное заземление металлических
нетоковедущих частей в сетях до 1000 В. Сопротивление, оказываемое заземляющим
устройством R≤4 Ом;
зануление в сетях до 1000 В;
защитное отключение при появлении
напряжения на корпусе оборудования;
предупредительная сигнализация,
блокировка, знаки безопасности;
ограждение неизолированных
токоведущих частей.
Для предотвращения возникновения
зарядов статического электричества согласно ГОСТ 12.1.018-93 (2001) «ССБТ.
Пожаровзрывобезопасность статического электричества». Общие требования» все
металлические и электропроводные неметаллические части технологического
оборудования должны быть заземлены. Сопротивление защитного устройства от
статического электричества не должно превышать 100 Ом.
Во избежание утечек в насосной
НПС-21 «Сковородино» важнейшим фактором при перекачке нефтепродуктов является
герметизация основного насосного оборудования и системы трубопроводов.
Герметизация обеспечена за счет сварного соединения стыковочных мест. Гибкие
связи, в системе технологических трубопроводов, герметизируются при помощи
хомутов с использованием герметика марки МГ-5.
Основными мероприятиями для
предотвращения превышения давления больше допустимого являются:
постоянный контроль за режимом
работы насосов, автоматизация процесса при превышении разрешенного давления
автоматически останавливается насос;
своевременное и качественное
проведение технического обслуживания оборудования и контроль за состоянием
торцевых уплотнений насосов, фланцевых соединений трубопроводов;
периодическое прохождение
обслуживающим персоналом инструктажа и обучение безопасным методам работы.
Мероприятия по промышленной
санитарии.
К ним относятся требования к спецодежде,
освещению, микроклимату, требования к организации и оборудованию рабочего
места.
Требования к спецодежде. Обеспечение
работников специальной одеждой и обувью выполняется согласно ГОСТ 12.4.011-89
(2001) ССБТ «Средства защиты работающих. Общие требования и классификация»
(таблица 5.3), а также в соответствии с «Правилами обеспечения работников
спецодеждой, спецобувью и другими средствами индивидуальной защиты» М., 1999 г.
Таблица 5.3 - Средства
индивидуальной защиты
Виды происшествий, приводящие к несчастным случаям
|
Средства индивидуальной защиты
|
Воздействие вредных веществ (отравление, воздействие на кожу)
|
Фильтрующие противогазы марки АБКФ, шланговые противогазы ПШ-1 и
ПШ-2
|
Поражение электрическим током
|
Диэлектрические перчатки, калоши, коврики, указатели низкого
напряжения, инструменты с изолированными рукоятками
|
Падение с высоты
|
Спец. одежда, спец. обувь, защитные каски
|
Выдаваемые работникам средства
индивидуальной защиты, должны соответствовать характеру, условиям работы и
обеспечивать безопасность труда.
ребования к освещению. В дневное
время суток освещение естественное. В ночное предусмотрено местное и общее
освещение. В насосном цехе применяются светильники взрывозащищенного исполнения
ВЗГ-200, кроме того, предусмотрено аварийное освещение, независимое от
основного.
В качестве источников света при
искусственном освещении операторной следует применять преимущественно
люминесцентные лампы типа ЛД и компактные люминесцентные лампы. Для обеспечения
нормируемых значений освещенности в помещении операторной и насосном цехе
следует проводить чистку стекол и светильников не реже двух раз в год и
проводить своевременную замену перегоревших ламп.
Освещенность местного и основного
освещения в насосном цехе согласно СНИП-23-05-95* должна быть равна 75 Лк.
Освещенность рабочих поверхностей мест производства работ, расположенных в
операторной равна 200 Лк.
Требования к микроклимату.
Показателями, характеризующими микроклимат, являются:
температура воздуха;
относительная влажность воздуха;
скорость движения воздуха.
В помещении операторной должны
соблюдаться оптимальные величины параметров воздуха согласно ГОСТ 12.1.005-88:
температура 21-23°С в холодный
период года, 22-24°С - в теплый;
относительной влажности 40-60%;
скорости движения 0,1 м/с в холодный
период года, 0,2 м/с - в теплый.
Микроклимат в помещении операторной
согласно СНиП 41-01 2008 от 01.01.2008 г. «Отопление, вентиляция и
кондиционирование» поддерживается отоплением, приточно-вытяжной вентиляцией и
кондиционированием. Для повышения влажности воздуха в помещениях с ПЭВМ следует
применять увлажнители воздуха, заправляемые ежедневно дистиллированной или
прокипяченной питьевой водой.
Содержание вредных химических
веществ в производственных помещениях, работа на ПК в которых является основной
(диспетчерские, операторские и др.), не должно превышать «Предельно допустимых
концентраций загрязняющих веществ в атмосферном воздухе населенных пунктов».
Методы борьбы с шумом и вибрацией
сводятся к уменьшению их возникновения. Для снижения или исключения вибрации
СНиП 23-03-2003 предусматривает следующие меры:
правильное проектирование оснований
под оборудование, с учетом динамических нагрузок и изоляция их от несущих
конструкций и инженерных коммуникаций;
- центровка и балансировка
вращающихся частей агрегатов.
В качестве индивидуальных средств
защиты от шума используются наушники или антифоны.
Рабочие, подвергающиеся воздействию
вибрации должны регулярно проходить медосмотр.
Мероприятия по пожарной
безопасности.
Пожарная безопасность на
электроустановках, находящихся в помещении НПС соблюдается в соответствии с ППБ
01-03 «Правила пожарной безопасности в Российской федерации» и ГОСТ 12.1.004-91
(1999) «ССБТ. Безопасность. Общие требования»:
вспомогательное оборудование,
электродвигатели, аппараты управления должны иметь степень защиты,
соответствующее классу зоны, а также должны иметь аппараты защиты от коротких
замыканий и перегрузок;
запрещается использовать
электрические аппараты и приборы в условиях, не соответствующих рекомендациям
предприятий изготовителей или неисправных, создающие угрозу возникновения
пожара, а также электропровода и кабели с поврежденной или потерявшей защитные
свойства изоляцией;
запрещается пользоваться розетками,
рубильниками и другими средствами с открытыми контактами;
запрещается пользоваться
электронагревательными приборами;
во взрывоопасных зонах работать
только инструментом в искробезопасном исполнении;
смазочные материалы хранятся в
специальных металлических лотках бочках с плотно закрывающимися крышками,
промасленная ветошь собирается в специально отведенные места;
запрещается курить и разводить
открытый огонь в необорудованных для этого местах, для предупреждения
вывешиваются предупредительные плакаты «НЕ КУРИТЬ».
Все первичные приборы контроля и
регулирования, установленные по месту, в зонах возможного возникновения
загазованности предусматривается выполнять в искробезопасном исполнении 2 Ехi
II АТ2 и 1 Ехd II АТЗ, что позволяет производить измерение во взрывоопасной среде.
Насосная станция оснащена системой
автоматического пенного пожаротушения, позволяющей тушить возможные очаги
пожара автоматически.
Вентиляция в насосном зале
установлена приточно-вытяжная кратностью воздухообмена 4:1 для удаления
взрывоопасной смеси воздуха с парами нефти.
В дополнение к этому
предусматривается установка обратных клапанов на трубопроводе, срабатывающие
термоэлементы для включения системы автоматического пожаротушения, установка
дверей и окон, открывающихся наружу, заземление металлического оборудования от
статического и атмосферного электричества. Соединение насосов и
электродвигателей осуществляется через специальные отверстия в герметизирующей
камере фрамуги разделительной стенки, к которому подается чистый воздух для
создания пневмозащиты. При аварийном нарушении герметичности трубопроводов и
оборудования, автоматически отключается вышедший из строя агрегат.
Система автоматического пенного
пожаротушения оборудована резервным питанием, а на станции пенотушения
установлен дизель-генератор на случай отсутствия электроэнергии.
Система автоматического пенного
пожаротушения управляется контроллером сигнальным автоматического
пожаротушения, осуществляющим контроль за состоянием насосной станции. В
насосной станции установлены инфракрасные датчики контроля «Ясень». При
возникновении пожара, на объектах охраны контроллер КСАП автоматически
запускает пенный насос и открывает соответствующие задвижки на насосную, сигнал
с контроллера КСАП поступает в пожарное депо где находятся две дежурные
пожарные машины и пожарный расчет. На каждом из входов (два) в насосную
устанавливаются ручные пожарные извещатели.
Для ликвидации небольших очагов
возгорания, на территории предусмотрена установка щитов с пожарным инвентарем,
песок, кошма, багор, лом, ведра, огнетушители серии ОХП-10 и ОУ - 8. Пожарный
инвентарь окрашивается в красный цвет [8].
5.3 Расчет минимально
необходимого числа вертикальных электродов
Расчет защитного заземления имеет
целью определить необходимое число вертикальных электродов при принятых их
размерах и размещении на плане электроустановки, длину соединительной полосы,
исходя из условия, что общее сопротивление растеканию тока заземляющего
устройства не превысит допустимых ПУЭ значений R3. Исходные данные для расчета приведены в таблице 5.4.
Таблица 5.4 - Исходные данные
Параметр
|
Значение
|
Напряжение электроустановки, В
|
380
|
Мощность питающих трансформаторов, кВт
|
80
|
Расчетный ток замыкания на землю, А
|
-
|
Форма вертикальных электродов
|
труба
|
Длина электродов, м
|
2
|
Диаметр электродов, м
|
0,05
|
Глубина заложения, м
|
-
|
Расстояние между вертикальными электродами, м
|
4
|
Форма соединительной полосы
|
Полоса
|
Размер полосы, м
|
0,04
|
Род грунта
|
глина
|
Климатическая зона
|
2
|
Конфигурация заземлителя
|
Стержневое круглое сечение
|
Допустимое нормативное сопротивление
заземляющего устройства.
Допустимое нормативное сопротивление
заземляющего устройства R3 должно быть не более 10
Ом, так как мощность питающих трансформаторов меньше 100 кВт.
Расчет удельного сопротивления
грунта.
Удельное сопротивление
грунта
для
вертикальных электродов, определим по формуле:
(5.1)
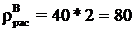
, (5.2)
,
где
-
коэффициент сезонности для горизонтальной соединительной полосы.
Сопротивление одиночного
заземлителя.
Сопротивление одиночного
заземлителя R0 вычислим по формуле:
, (5.3)
R0=(80/(2∙3,14∙2))∙ln (4∙2/0,05) =32,3,
где
-
длина вертикального заземлителя, м;
- диаметр вертикального
заземлителя, м.
Необходимое количество
вертикальных электродов.
Необходимое количество
вертикальных электродов
можно
определить по формуле:
(5.4)
n1=32,3/10=3,23,
где R3 - допустимое нормативное сопротивление заземляющего
устройства.
Округлим в большую
сторону необходимое количество вертикальных электродов:
n1=4.
(5.5)
Коэффициент
использования вертикальных электродов.
Коэффициент
использования вертикальных электродов hв
для найденного количества вертикальных электродов с учетом их расположения и
отношения расстояния между электродами к их длине при n1
= 4 и при отношениях 4/2=2 получим:
hв
= 0,83. (5.6)
Сопротивление группы
вертикальных электродов.
Сопротивление группы
вертикальных электродов Rгрв
определим по формуле:
, (5.7)
Rгрв
=32,3/(4∙0,83)=9,73.
Длина горизонтальной
соединительной полосы.
Длину горизонтальной
соединительной полосы Ln
для электродов расположенных в ряд определим по формуле:
Ln=1,05∙a∙(n1-1),
(5.8)
Ln=1,05∙4∙3=12,6,
где
-
расстояние между вертикальными электродами равное 4 м.
Сопротивление растекания
тока соединительной полосы.
Сопротивление растекания
тока соединительной полосы Rn′
определим по формуле:
(5.9)
Rn′=280/(2∙3,14∙12,6)×ln (4∙12,6/0,04)=25,26.
Коэффициент
использования соединительной полосы.
Коэффициент
использования горизонтальной соединительной полосы hг
для найденного числа n1
электродов:
hг
= 0,8. (5.10)
Сопротивление
соединительной полосы Rn
с учетом коэффициента использования определим по формуле:
(5.11)
Rn=25,26/0,8=31,575.
Результирующее
сопротивление растекания тока.
Результирующее
сопротивление растекания тока всего заземлявшего устройства Rзу определяется по формуле:
, (5.12)
Rзу=31,575*9,73/(31,575+9,73)=7,43.
Сравним вычисленное
значение сопротивление растекания тока всего заземлявшего устройства с
допустимой величиной Rз.
Rзу < Rз, (5.13)
,43<10.
Следовательно, необходимое число
вертикальных электродов равно 4.
5.4 Экологичность
проекта
В связи с тем, что НПС является
опасным производственным объектом, который во время эксплуатации может выделять
в окружающую среду вредные производственные факторы, в данном разделе мы
рассмотрим экологичность проекта.
Основная часть загрязнителей при
нормальном режиме работы поступает в атмосферу в виде пара, газа из
технологических аппаратов и при ремонтных работах на трубопроводе и запорной
арматуре.
Значительно испарение нефти при
хранении в резервуарах. В качестве загрязнителя в данном случае выступают
сложные смеси большого количества индивидуальных углеводородных компонентов.
При хранении легковоспламеняющихся жидкостей в резервуарах различают два вида
потерь: от так называемых малых и больших «дыханий». Эти выбросы дополняются
потерями от «обратного выдоха» и от вентиляции газового пространства
резервуаров.
Сокращение потерь нефти и
нефтепродуктов, предотвращение загрязнения атмосферы достигают с помощью
организационно технических мероприятий и специальных технических средств.
Первые рационализируют эксплуатацию всего комплекса резервуарного хозяйства,
установок и трубопроводных коммуникаций, обеспечивают строго соблюдение всех
правил по уход за технологическим оборудованием.
Основополагающим условием
экологической безопасности в данном случае является высокое качество
герметизации всей системы транспорта и хранения нефти и нефтепродуктов.
К специальным технологическим
средствам снижения потерь при хранении нефти и нефтепродуктов относят:
применение резервуаров с уменьшенным
объемом газового
пространства, применение понтонных и плавающих крыш;
хранение нефтепродуктов под
повышенным давлением;
применения газоуравнительных систем
и установок по улавливанию паров нефтепродуктов и нефти;
использование отражательно тепловой
защиты резервуаров от солнечной радиации для уменьшения диапазона изменения
температуры газового пространства.
Отрицательное тепловое воздействие
солнечной радиации резко ограничивают посредством соответствующей окраски
наружной и внутренних поверхностей резервуаров, устройством экранов -
отражателей, орошением, крыши резервуаров.
Одним из перспективных направлений в
снижении потерь легко испаряющихся нефтепродуктов является использование заглубленных
и подземных резервуаров.
Система автоматизации насосной
станции состоит из комплекса программно-технических средств, таких как,
датчики, контроллеры мониторы и т.д. Система автоматизации при работе не имеет
вредных отходов и выбросов, все приборы монтированы в металлических шкафах
исключающих воздействие магнитных и электрических полей.
При ремонте и эксплуатации средств
автоматизации, а так же в процессе монтажа, могут произойти различные аварийные
ситуации и несчастные случаи, связанные с выбросом вредных производственных
веществ.
Одним и основных источников
загрязнения окружающей среды в нормальных условиях являются сточные воды.
Сточные воды с высокими концентрациями токсичных веществ способны нанести
непоправимый ущерб поверхностным и подземным водам, другим объектам окружающей
среды.
Сточные воды, как наиболее
существенный загрязнитель на перекачивающих станциях и наливных пунктах,
подразделяются на:
пластовые;
подтоварные;
промывочные воды резервуаров, и
линейной части, используемые для промывки и опресовки технологического
оборудования резервуаров и линейной части трубопровода;
атмосферные;
производственные сточные.
В период дождей и таяния снега,
атмосферные воды скапливаются в пределах обвалованной территории резервуаров
котельной и на территории технологического оборудования.
Все технологические площадки НПС
имеют бетонное или асфальтное покрытие с уклоном к канализационным трапам и
ограждаются по периметру бордюром, для исключения растекания воды за пределы
технологических площадок.
Для защиты земель и водных ресурсов
на открытых технологических площадках и резервуаров нефти для котельной
предусмотрена производственно-дождевая канализация для приема дождевых стоков.
С поверхности технологических
площадок дождевые стоки собираются при помощи планировки поверхности и
дождеприемных колодцев, затем Самотечной канализационной сетью через
существующую канализационную сеть подаются на песколовку и нефтеловушки, а
затем в пруды-накопители.
Для удаления разлившихся
нефтепродуктов используются природные и Искусственные сорбенты: торф,
полимерные материалы, песок. На пути движения потока нефтепродукта оборудуются
ямы, накопители, дренажные канавы.
В процессе эксплуатации очистных
сооружений применяются меры к уменьшению количества сточных вод путем введения
внутристанционного оборота производственной воды.
Основными компонентами загрязнений
воздушной среды выбросами нефтебаз являются углероды, окись углерода, окислы
серы, азота, взвешенные вещества. Поэтому в процессе эксплуатации резервуарного
парка особое внимание обращают на техническое состояние оборудования, которое
может явиться источником загрязнения атмосферы:
резервуары для светлых
нефтепродуктов;
дыхательные клапаны на резервуарах
для светлых нефтепродуктов.
Техническое обслуживание резервуаров
включает периодический осмотр резервуаров, оборудования и арматуры, а также
периодическую приборную дефектоскопию сварных соединений, состояния стенок и
днища резервуаров, контроль формы, размеров резервуара.
6. Оценка экономической
эффективности модернизации системы автоматизации
.1 Основные
финансово-экономические показатели ОАО «АК «Транснефть»
Основным видом деятельности ОАО «АК
«Транснефть» является оказание услуг в области транспортировки нефти, газа и
продуктов их переработки по системе магистральных трубопроводов в Российской
Федерации и за ее пределами, диспетчеризация поставок нефти.
Помимо основной деятельности по
транспортировке нефти по территории Российской Федерации ОАО «АК «Транснефть»
обеспечивает планирование и управление транспортировкой нефти на территории
зарубежных стран, контроль за размещением нефти и её сдачей на зарубежных
приемо-сдаточных пунктах, организовывает сбор и обобщение информации. Выручка
компании от основных видов деятельности приведена в таблице 6.1.
Таблица 6.1 - Выручка от продажи
товаров (работ, услуг)
Вид выручки
|
2009 год, тыс. руб.
|
2008 год, тыс. руб.
|
Изменение, тыс. руб.
|
Изменение, %
|
Услуги по транспортировке российской нефти
|
292 319 421
|
235 228 999
|
57 090 422
|
24,3
|
Услуги по транспортировке транзитной нефти
|
11 904 538
|
7 835 803
|
4 068 735
|
51,9
|
Компаундирование
|
3 972 244
|
3 061 659
|
910 585
|
29,8
|
Сдача имущества в аренду
|
3 099 252
|
2 505 721
|
593 531
|
23,7
|
Строительство
|
6 126 599
|
-
|
6 126 599
|
-
|
Прочее
|
1 096 747
|
638 116
|
458 631
|
71,9
|
Итого
|
318 518 801
|
249 270 298
|
69 248 503
|
27,8
|
Изменение выручки от продажи товаров
(работ, услуг) Компании в 2009 году по сравнению с 2008 годом произошло в
результате:
роста выручки за услуги по
транспортировке нефти, что обусловлено индексацией тарифов;
роста выручки за услуги по компаундированию
нефти в связи с увеличением объемов оказанных услуг;
увеличения выручки от сдачи
имущества в аренду, что связано в основном с увеличением стоимости услуг по
договору в связи с дооценкой сдаваемых в аренду объектов;
получением выручки по строительству
в связи с выполнением контрактных обязательств ОАО «АК «Транснефть» по
государственному контракту на строительство и разработку проектной и рабочей
документации, а также строительство и реконструкцию объектов инфраструктуры
(нефтепровода и продуктопровода) в рамках реализации инвестиционного проекта
«Комплекс нефтеперерабатывающих и нефтехимических заводов в г. Нижнекамске» в
соответствии с распоряжением Правительства Российской Федерации от 30.11.2006
№1708-р.
Себестоимость товаров, работ и услуг
приведена в таблице 6.2.
Таблица 6.2 - Себестоимость товаров
(работ, услуг)
Себестоимость услуг по видам выручки
|
2009 год, тыс. руб.
|
2008 год, тыс. руб.
|
Изменение, тыс. руб.
|
Изменение, %
|
Услуги по транспортировке российской нефти
|
286 112 996
|
220 360 790
|
65 752 206
|
29,8
|
Услуги по транспортировке транзитной нефти
|
9 934 107
|
10 724 415
|
790 308
|
7,4
|
Компаундирование
|
2 383 668
|
1 831 362
|
552 306
|
30,2
|
Сдача имущества в аренду
|
2 614 026
|
2 249 029
|
364 997
|
16,2
|
Строительство
|
6 136 519
|
-
|
6 136 519
|
-
|
Прочее
|
166 756
|
88 555
|
78 201
|
88,3
|
Итого
|
307 348 072
|
235 254 151
|
72 093 921
|
30,6
|
Изменение себестоимости проданных
товаров (работ, услуг) в 2009 году по сравнению с 2008 годом произошло в
результате:
увеличения расходов по договорам
подряда на транспортировку нефти с дочерними обществами в связи с ростом
расходов по эксплуатации магистральных нефтепроводов, затратами, связанными с
реконструкцией и модернизацией действующих нефтепроводов;
роста расходов по компаундированию
нефти в связи с увеличением объемов оказанных услуг;
увеличения расходов по сдаче
имущества в аренду, что связано с увеличением амортизационных отчислений по
объектам основных средств, сданным в аренду, в результате проведенной на
01.01.2009 до оценки;
возникновению в 2009 году расходов,
связанных с выполнением строительных работ по государственному контракту;
увеличения себестоимости прочих
выполненных работ, оказанных услуг.
Прибыль и активы ОАО «АК
«Транснефть» приведены в таблице 6.3.
Таблица 6.3 - Прибыль и активы
Компании
Наименование показателя
|
2009 год
|
2008 год
|
Изменение
|
Валовая прибыль, тыс. руб.
|
11 170 729
|
14 016 147
|
2 845 418
|
Чистая прибыль, тыс. руб.
|
3 893 243
|
3 681 621
|
211 622
|
Стоимость чистых активов, тыс. руб.
|
113 028 984
|
116 554 035
|
3 525 051
|
Снижение валовой прибыли в 2009 году
по сравнению с 2008 годом обусловлено в основном снижением валовой прибыли,
полученной от реализации услуг по транспортировке нефти.
Увеличение чистой прибыли в 2009
году по сравнению с 2008 годом произошло в основном в результате снижения в
2009 году отрицательного эффекта от курсовых разниц по операциям в иностранной
валюте.
Увеличение стоимости чистых активов
связано с получением ОАО «АК «Транснефть» чистой прибыли по результатам 2009
года в сумме 3 893 243 тыс. руб., выплатой в 2009 году дивидендов по итогам
работы за 2008 год в сумме 368 163 тыс. руб., а также снижением доходов будущих
периодов на конец 2009 года по сравнению с началом года.
6.2 Методика расчета
экономической эффективности проекта
Для оценки эффективности
инвестиционных проектов применяются методы дисконтированной оценки, которые
базируются на учете временного фактора. Они учитывают временной фактор с
позиции стоимости денег в будущем.
Чистый дисконтированный доход (ЧДД)
находится путем оценки чистого дохода за определенный промежуток времени. Он
определяется как сумма текущих эффектов за весь расчетный период.
На практике часто
пользуются следующей формулой для определения ЧДД:
, (6.1)
где Rt - результаты, достигаемые на t-ом
шаге расхода;
Зt - затраты, осуществляемые на том же шаге;
Т - горизонт расчета
(равный номеру шага расчета, на котором амортизация полностью проведена);
Е - норма дисконта.
В качестве начального
года расчетного периода принимается год начала финансирования работ по
разработке проекта.
Если ЧДД инвестиционного
проекта положителен, проект является эффективным (при данной норме дисконта).
Если: ЧДД > 0,
проект следует принимать;
ЧДД = 0, проект ни
прибыльный, ни убыточный;
ЧДД < 0, проект
убыточный и его следует отвергнуть.
Индекс доходности дисконтированных
инвестиций - отношение суммы дисконтированных элементов денежного потока от
операционной деятельности к абсолютной величине дисконтированной суммы
элементов денежного потока от инвестиционной деятельности. Индекс доходности
равен увеличенному на единицу отношению ЧДД к накопленному дисконтированному
объему инвестиций.
Формула для определения индекса
доходности имеет следующий вид:
. (6.2)
Если: ИД > 1 -
проект эффективен; ИД < 1 - проект неэффективен.
В отличие от ЧДД
индекс доходности является относительным
показателем, что
позволяет осуществлять выбор одного проекта из ряда альтернативных, имеющих
приблизительно одинаковое значение ЧДД.
Внутренней нормой доходности (ВНД)
называется такое положительное число Ев, что при норме дисконта Е равной Ев ЧДД
проекта обращается в 0, при всех больших значениях Е - отрицательна, при всех
меньших значениях Е - положительна. Если не выполнено хотя бы одно из этих
условий, считается, что ВНД не существует.
ВНД определяется из
равенства:
. (6.3)
Величина ВНД,
найденная из этого равенства, сравнивается с заданной инвестором величиной
дохода на капитал. Если рассчитанная внутренняя норма доходности больше
заданной инвестором, то проект эффективен. Смысл расчета этого
коэффициента при анализе эффективности планируемых инвестиций заключается в
следующем: ВНД показывает максимально допустимый относительный уровень расходов
при реализации проекта.
6.3 Расчет экономической
эффективности проекта
Капитальные вложения на внедрение
расходомера UFM 3030 фирмы «KROHNE» включают в себя единовременные денежные затраты, которые
приведены в таблице 6.4. Строительно-монтажные работы ведутся персоналом НПС за
время плановой остановки трубопровода (8 часов) численностью рабочих согласно
нормативным документам (5 человек). Пусконаладочные работы могут проводиться на
работающем оборудовании персоналом численностью 2 человека.
Таблица 6.4 - Расчет капитальных
вложений
Вид затрат
|
Сумма, тыс. руб.
|
Стоимость прибора
|
448,9
|
Материалы и оборудование
|
75
|
Строительно-монтажные работы
|
6,815
|
Пусконаладочные работы
|
2,726
|
Прочие затраты
|
5
|
Капитальные вложения
|
538,441
|
Годовые эксплуатационные затраты,
связанные с обслуживанием и эксплуатацией приборов, средств или систем
автоматизации, рассчитываются по следующей формуле:
З эк = З
вспом + З рем + З обор + З ам + З
пот + З пр, (6.4)
где З вспом
- затраты на вспомогательные материалы;
Зрем -
затраты на ремонт;
Зобор -
затраты на обслуживание оборудования, т.е. на заработную плату работника
(работников), занимающегося обслуживанием;
Зам -
амортизационные отчисления по приборам, средствам автоматизации, внедряемому
оборудованию;
Зпот -
затраты, связанные с потреблением электроэнергии;
Зпр -
прочие затраты.
Затраты на
вспомогательные материалы составляют 20% от стоимости капитальных вложений:
Звспом =
0,2*К, (6.5)
где К - капитальные
вложения.
Затраты на ремонт
оборудования составляют 25% от капитальных вложений:
Зрем =
0,25* К. (6.6)
Затраты на
содержание и эксплуатацию оборудования составляют 40% от капитальных вложений:
Зобор =
0,4* К. (6.7)
Затраты на
амортизацию составляют 10 процентов от капитальных вложений, т.к.
эксплуатационный срок оборудования 10 лет:
Зам = Nа
*K, (6.8)
где Nа -
норма амортизации.
Затраты на
электроэнергию рассчитываются по формуле:
Зпот
=365*24* Сэ*Р, (6.9)
где Р -
потребляемая мощность (0,01 кВт);
Сэ -
стоимость электроэнергии (2,4 руб./кВт*ч).
Величина прочих
затрат принимается равной 25% от суммы численных выше затрат:
Зпр
=0,25 *(З вспом + З рем + З обор + З ам
+ З пот) (6.10)
Результаты расчета
эксплуатационных затрат приведены в таблице 6.5.
Таблица 6.5 - Эксплуатационные
затраты
Наименование затрат
|
Сумма, тыс. руб.
|
Вспомогательные материалы
|
107,688
|
Ремонт
|
134,610
|
Содержание и эксплуатация
|
215,376
|
Затраты на электроэнергию
|
0,210
|
Амортизация
|
53,844
|
Прочие
|
125,684
|
Эксплуатационные затраты
|
637,41
|
Устанавливаемый прибор показывает
количество нефти перекачиваемой НПС, а так же позволяет своевременно обнаружить
наличие утечки из магистрального нефтепровода, что влечет за собой сокращение
затрат на устранение последствий аварии. Рассматриваемый прибор используется
как дублирующий для расходомера установленного на входе НПС, вероятность
безотказной работы которого равна 0,99.
Расходы на восстановление и
упущенную прибыль Ру из-за несвоевременного обнаружения утечки при отказе основного
расходомера найдем по формуле:
Ру=Рч*Квос*Рут((1-Рраб)*365*24),
(6.11)
Ру=97,5*2,75*0,05
((1-0,99)*365*24)=1174,4,
где Рч - прибыль от часа
работы НПС, тыс. руб.;
Рраб - вероятность
безотказной работы основного оборудования;
Квос - коэффициент затрат
на восстановление;
Рут - вероятность
возникновения утечки при отказе основного расходомера.
Результаты расчетов сведены в
таблицы 6.6 и 6.7.
Таблица 6.6 - Расчет налога на
имущество, тыс. руб.
Показатель
|
Год
|
|
1
|
2
|
3
|
4
|
5
|
6
|
7
|
8
|
9
|
10
|
Стоимость основных фондов на начало года
|
538,44
|
484,60
|
430,75
|
376,91
|
323,07
|
269,22
|
215,38
|
161,53
|
107,69
|
53,85
|
Амортизационные отчисления
|
53,84
|
53,84
|
53,84
|
53,84
|
53,84
|
53,84
|
53,84
|
53,84
|
53,84
|
53,84
|
Стоимость основных фондов на конец года
|
484,60
|
430,75
|
376,91
|
323,07
|
269,22
|
215,38
|
161,53
|
107,69
|
53,85
|
0,00
|
Среднегодовая стоимость основных фондов
|
511,52
|
457,68
|
403,83
|
349,99
|
296,14
|
242,30
|
188,46
|
134,61
|
80,77
|
26,92
|
Налог на имущество
|
10,23
|
9,15
|
8,08
|
5,92
|
4,85
|
3,77
|
2,69
|
1,62
|
0,54
|
Таблица 6.7 - Расчет эффективности проекта
Показатель
|
Год
|
|
0
|
1
|
2
|
3
|
4
|
5
|
6
|
7
|
8
|
9
|
10
|
Капитальные вложения, тыс. руб.
|
538,44
|
-
|
-
|
-
|
-
|
-
|
-
|
-
|
-
|
-
|
-
|
Выгоды, тыс. руб.
|
-
|
1174,40
|
1174,40
|
1174,40
|
1174,40
|
1174,40
|
1174,40
|
1174,40
|
1174,40
|
1174,40
|
1174,40
|
Эксплуатационные затраты, тыс. руб.
|
-
|
637,41
|
637,41
|
637,41
|
637,41
|
637,41
|
637,41
|
637,41
|
637,41
|
637,41
|
637,41
|
в т.ч амортизация, тыс. руб.
|
-
|
53,84
|
53,84
|
53,84
|
53,84
|
53,84
|
53,84
|
53,84
|
53,84
|
53,84
|
53,84
|
Налог на имущество, тыс. руб.
|
-
|
10,23
|
9,15
|
8,08
|
7,00
|
5,92
|
4,85
|
3,77
|
2,69
|
1,62
|
0,54
|
Валовая прибыль, тыс. руб.
|
-
|
526,76
|
527,84
|
528,91
|
529,99
|
531,07
|
532,14
|
533,22
|
534,30
|
535,37
|
536,45
|
Налог на прибыль, тыс. руб.
|
-
|
105,35
|
105,57
|
105,78
|
106,00
|
106,21
|
106,43
|
106,64
|
106,86
|
107,07
|
107,29
|
Чистый операционный доход, тыс. руб.
|
-
|
475,25
|
476,11
|
476,97
|
477,84
|
478,70
|
479,56
|
480,42
|
481,28
|
482,14
|
483,01
|
Сальдо денежного потока от операционной деятельности, тыс. руб.
|
-
|
529,10
|
529,96
|
530,82
|
531,68
|
532,54
|
533,40
|
534,26
|
535,13
|
535,99
|
536,85
|
Сальдо денежного потока от инвестиционной деятельности, тыс.
руб.
|
-538,44
|
-
|
-
|
-
|
-
|
-
|
-
|
-
|
-
|
-
|
-
|
чистые денежные поступления проекта, тыс. руб.
|
-538,44
|
529,10
|
529,96
|
530,82
|
531,68
|
532,54
|
533,40
|
534,26
|
535,13
|
535,99
|
536,85
|
Коэффициент дисконтирования
|
1
|
0,87
|
0,76
|
0,66
|
0,57
|
0,50
|
0,43
|
0,38
|
0,33
|
0,28
|
0,25
|
Чистые дисконтированные денежные поступления проекта, тыс. руб.
|
-538,44
|
460,31
|
402,77
|
350,34
|
303,06
|
266,27
|
229,36
|
203,02
|
176,59
|
150,08
|
134,21
|
Чистые дисконтированные денежные поступления проекта нарастающим
итогом, тыс. руб.
|
-538,44
|
-78,13
|
324,64
|
674,98
|
978,04
|
1244,31
|
1473,67
|
1676,69
|
1853,29
|
2003,36
|
2137,57
|
Найдем показатели эффективности
проекта и результаты представим в таблице 6.8.
Таблица 6.8 - Эффективность проекта
Показатель
|
Значение
|
Инвестиции, тыс. руб.
|
538,441
|
Расчетный период, лет
|
10
|
Годовые выгоды, тыс. руб.
|
1174,40
|
Ставка дисконтирования, %
|
15
|
Чистый дисконтированный доход, тыс. руб.
|
2137,57
|
Индекс доходности, дол. ед.
|
4,97
|
Внутренняя норма доходности, %
|
100
|
Срок окупаемости, лет
|
1,6
|
Как видно из расчетов, установка
оборудования для предприятия выгодна, т.к. дисконтированный денежный поток по
проекту положительный, внутренняя норма доходности выше цены капитала, а индекс
рентабельности больше 1.
Заключение
В ходе дипломного проектирования
рассмотрена технология перекачки нефти на НПС-21 «Сковородино», определены
основные показатели, влияющие на транспорт нефти, приведены нормы
технологического процесса, произведен выбор и обоснование технологического
оборудования. Выбраны средства автоматизации, приведено обоснование выбора
параметров контроля и регулирования. Рассмотрен и проанализирован существующий
уровень автоматизации на нефтеперекачивающей станции и предложена модернизация
системы автоматизации за счет усовершенствования системы измерения расхода. По
результатам патентного поиска и анализу выявленных аналогов уже существующих
патентов сделан вывод о рентабельности в применении предложенной системы
измерения расхода. Произведен анализ результатов поверки рассматриваемого
расходомера. В рамках проекта рассмотрены производственные вредности и
потенциальные опасности. Представлены обоснования и требования к мероприятиям
по устранению вредных воздействий на окружающую среду. Определена экономическая
эффективность от модернизации системы автоматизации на нефтеперекачивающей
станции.
Внедрение рассмотренных улучшений
системы автоматизации позволит:
повысить показатели надежности
технологического оборудования и средств автоматизации;
сократить затраты связанные с
обслуживанием системы автоматизации;
минимизировать последствия аварий
линейной части магистрального нефтепровода.
Список использованных
источников
1 Колпаков, Л.Г. Насосы нефтеперекачивающих станций // Кавитация,
режимы работы, регулирование. - 1982. - С. 20-25.
Мастобаев, Б.Н. Эксплуатация насосных станций / Б.Н. Мастобаев,
И.М. Руфанова. - М.: Нефтяная промышленность. - 2000. - 135 с.
3 Певзнер, В.Б. Основы автоматизации нефтегазопроводов и нефтебаз.
- М.: Недра, 1995. - 240 с.
4 Фарзане, Н.Г. Технологические измерения и приборы / Н.Г.
Фарзане, Л.В. Ильясов, А.Ю. Азим-заде // Высшая школа. - 1989. - 456 с.
Исакович, Р.Я. Технологические измерения и приборы // Измерение
расхода. - М.: Недра, 1986. - 344 с.
Интеллектуальный преобразователь ST 3000. Руководство по
эксплуатации. - М., 2003. - 158 с.
Семенов, М.Р. Измерение расхода // Трехлучевое измерение [Электронный
ресурс]. - 2010. - http: // www.krohne.ru
Лисин, Ю.В. Система организации работ по охране труда и
промышленной безопасности на нефтепроводном транспорте. - М.: Недра, 1999. -
172 с.