Проектирование и исследование механизмов
Введение
В данной курсовой работе необходимо спроектировать привод скребкового
конвейера сроком службы 6 года. Для этого необходимо провести расчеты
вала-шестерни, ведомого вала, зубчатого колеса и корпуса редуктора, сделать
подбор шпонок, подшипников качения, проверить долговечность подшипников,
определить расстояние между линиями действия сил зацепления и реакции опор, а
также определить скорости и ускорения отдельных деталей привода.
1. Выбор
электродвигателя. Кинематический расчет привода
Двигатель является одним из основных элементов машинного агрегата. От
типа двигателя, его мощности, частоты вращения и других параметров зависят
конструктивные и эксплуатационные характеристики рабочей машины и её привода.
Электродвигатель выбирают после определения его мощности и частоты вращения
вала.
Потребляемая мощность привода:

Общий КПД привода определяют как произведение частных значений КПД
отдельных составляющих элементов:
где
i- число пар подшипников качения; i=2
Из
табл. 1.1:
КПД
ременной передачи
КПД
пары цилиндрических зубчатых колес
КПД
муфты
КПД
одной пары подшипников качения (опоры барабана)
Общий
КПД привода:
Требуемая
мощность электродвигателя:
Диаметр
звёздочки:

Частота
вращения приводного вала:
Определяем общее передаточное число привода:
Частота
вращения вала электродвигателя:

Полученное значение должно находиться в интервале:
Электродвигатель АИР 112МВ6/950
ТУ 16-525.564-84
Мощность
двигателя 
,
Синхронная
частота вращения 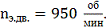
Кинематические расчеты
Определяем фактическое передаточное отношение:
На схеме одноступенчатый цилиндрический косозубый редуктор, поэтому
Уточняем передаточное число ременной передачи:
Частота
вращения ведущего вала редуктора:
Частота
вращения ведомого вала:
Определение
моментов и скоростей на валах редуктора
Угловые
скорости ведущего и ведомого валов:
Вращающий
момент на приводном валу барабана ленточного транспортера:
Вращающий момент на ведомом валу редуктора:
Вращающий
момент на ведущем валу редуктора:
Таблица 1.3.1 - Результаты кинематического расчета привода
Вал
|
Т, Н·м
|
n, об/мин
|
ω, рад/с
|
Ведущий (1)
|
104,26
|
279,4
|
29,24
|
Ведомый (2)
|
505,6
|
55,88
|
5,84
|
2. Расчет
зубчатых колес редуктора
Расчёты на прочность металлических цилиндрических эвольвентных зубчатых
передач внешнего зацепления с модулем от 1 мм и выше регламентированы ГОСТ
21354-87.
Из двух зубчатых колёс находящихся в зацеплении, меньшее называется
шестернёй (ведущее звено, индекс «1»), большее - колесом (ведомое звено, индекс
«2»).
.1 Выбор
материалов и термической обработки
Материалы для изготовления зубчатых колёс подбирают по таблице.
Передачи со стальными зубчатыми колёсами имеют минимальную массу и
габариты, тем меньше, чем выше твердость рабочих поверхностей зубьев, которая,
в свою очередь зависит от марки стали и от варианта термической обработки (ТО).
Чем выше твердость рабочей поверхности зубьев, тем выше допускаемые напряжения
и тем меньше размеры передачи.
Твёрдость
- сопротивление материала местной пластической деформации, возникающей при
внедрении в него более твёрдого тела - наконечника (индентора). Для
равномерного изнашивания зубьев колёс и лучшей их прирабатываемости друг к
другу, твёрдость шестерни
назначают больше твёрдости колеса
на 20…50 единиц.
Для
шестерни и колеса выбираем сталь 40Х, термообработку - улучшение и закалка ТВЧ.
По
табл. 2.1 выбираем твердость зубьев на поверхности по Роквеллу - 48…53HRC.
Соотношение единиц твердости по Роквеллу (HRC) и единиц
твердости по Бринеллю (НВ) принимаем по табл. 2.2.
2.2
Определение допускаемых напряжений
Средняя твердость рабочих поверхностей зубьев:
Базовые
числа циклов нагружений:
· при расчете на контактную прочность
· при расчете на изгиб
Время
работы передачи в часах
Действительные числа циклов перемены напряжений
· для шестерни
· для колеса
Коэффициент долговечности при расчете по контактным напряжениям для
шестерни:
Т.к.
, то принимаем
Для
колеса:
Т.к.
, то принимаем
Коэффициент
долговечности при расчете на изгиб для шестерни:
Т.к.
, то принимаем
Для
колеса:
Т.к.
, то принимаем
По
табл. 2.3 рассчитываем предел контактной выносливости зубьев
Предел
выносливости зубьев при изгибе:
Определяем допускаемые контактные напряжения для шестерни и колеса:
Допускаемые
напряжения изгиба для шестерни и колеса:
Допускаемое
рабочее контактное напряжение косозубых колес:
Допускаемое
рабочее напряжение изгиба для косозубых колес:
2.3 Расчет
зубчатой передачи
Определяем предварительное значение межосевого расстояния:
Коэффициент ширины зубчатого колеса при симметричном расположении опор:
Определяем коэффициент ширины в долях диаметра:
По
табл. 2.4
Рассчитываем
коэффициент неравномерности распределения нагрузки:
мм
По
таблице из стандартного ряда межосевых расстояний округляем
до ближайшего значения в большую сторону по ГОСТ
2185-66 (в мм): 40,50,63,71,80,90,100,112,125,160,200,250,280,315 [1].
После
округления принимаем
Предварительные
основные размеры колес.
Нормальный
модуль зацепления принимают по следующей рекомендации:
при
твердости поверхности зубьев колес
при
твердости
(как в нашем случае):
Модуль
принимаем из ряда стандартных значений (ГОСТ 9563-80):
-й
ряд (предпочтительный): 1,0;1,25;1,5;2,0;3,0;4,0;5,0;6,0;8,0;10,0.
-q
ряд: 1,125;1,375;1,75;2,25;2,75;3,5;4,5;5,5;7,0;9,0.
Принимаем
стандартный
мм.
Предварительно
принимаем угол наклона зубьев колес:
Количество зубьев на шестерни:
Для немодифицированного зубчатого зацепления число зубьев шестерни должно
быть не меньше 17.
Т.к.
в нашем случае
, то уменьшаем величину модуля.
Принимаем
модуль передачи
.
Вновь
определяем число зубьев шестерни:
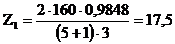
Число
зубьев колеса:
После
округления принимаем
Уточняем угол наклона зуба:
Рассчитываем делительные диаметры шестерни и колеса
Диаметры вершин зубьев
Диаметры
впадин зубьев
Ширина
колеса:
По
табл. 2.5 принимаем
.
Ширина
шестерни:
Окружная
скорость шестерни и колес
2.4
Определение сил в зацеплениях
Рис. 2.4.1 - Схема действия сил и моментов в цилиндрической косозубой
передаче
Найдем окружную силу:
Определяем
радиальную силу:
Определяем
осевую силу:
2.5
Проверочный расчет передачи
.5.1 Проверка
зубьев передач по контактным напряжениям
Расчетное контактное напряжение:
Для
косозубых колес:
[2.5.2]
Для
косозубых и шевронных колес при твердости зубьев >350 HB:
Коэффициент,
учитывающий неравномерность распределения нагрузки по длине контактных линий
определяем по табл. 2.8 [2].
Принимаем
Определяем
расчетное контактное напряжение
Проверим
условие прочности:
2.5.2
Проверка зубьев передач по напряжениям изгиба
Расчетное напряжение изгиба в зубьях колеса:
Для
косозубых колес принимаем коэффициент, учитывающий распределение нагрузки между
зубьями:
при
степени точности, равной 9 по табл. 2.7.
Коэффициент,
учитывающий внутреннюю динамическую нагрузку, для косозубых колес при твердости
>350 HB:
Определяем
коэффициент, учитывающий неравномерность распределения нагрузки по длине
контактных линий:
Определяем
коэффициент, учитывающий наклон зуба:
Определяем
приведенное число зубьев колеса:
[2.5.8]
По
табл. 2.10 коэффициент формы зуба
Расчетное
напряжение изгиба в зубьях шестерни:
Приведенное
число зубьев шестерни:
По
табл.
Т.к.
соблюдаются требования:
то
условие прочности по изгибающим напряжениям выполнено.
3. Эскизное
проектирование редуктора
.1
Предварительный расчет валов
Основными материалами для валов и осей служат углеродистые и легированные
стали. Для осей и валов, диаметры которых определяются, в основном, жесткостью,
применяют углеродистые конструкционные стали Ст4, Ст5 без термообработки. В
ответственных и тяжело нагруженных конструкциях, когда основным критерием
является прочность, используют термически обрабатываемых среднеуглеродистые и
легированные стали 40, 45, 40Х, 40ХН и др.
Для
компенсации изгибающих напряжений и других неучтенных факторов, принимают
значительно пониженные значения допускаемых напряжений кручения, например
МПа. Меньшие значения допускаемых напряжений кручения
принимают для быстроходных валов, большие значения - для тихоходных валов.
Определяем
диаметр ведущего вала:
Принимаем
по табл. 2.5 стандартное значение диаметра вала:
Определяем
диаметр ведомого вала:

подшипник скребковый
конвейер комбайн
3.2 Выбор
подшипников
Посадочные диаметры под подшипники ведущего и ведомого валов:
Посадочный
диаметр под зубчатое колесо:
По
посадочным диаметрам
и
выбираем
из табл. 3.1 радиальные шариковые подшипники.
Рис.
3.2.1 - Подшипник шариковый радиальный
Таблица
3.2.1 - Основные параметры выбранных подшипников
Вал
|
Условное обозначение
подшипника
|
Размеры, мм
|
Грузоподъемность, кН
|
|
|
d
|
D
|
В
|
Динамическая, С
|
Статическая, С0
|
Ведущий (1)
|
309
|
45
|
100
|
25
|
52,7
|
30,0
|
Ведомый (2)
|
310
|
50
|
110
|
27
|
65,8
|
36,0
|
4.
Конструктивные размеры вала-шестерни, ведомого вала и зубчатого колеса
Цилиндрическая поверхность выходного конца вала является посадочной
поверхностью под полумуфту
Для
ведущего вала (для
) по табл. 4.1:
Определяем
диаметр буртика под подшипник:
Принимаем
Для
ведомого вала (для
) по табл. 4.1:
Определяем
посадочный диаметр под колесо:
Принимаем
Определяем
диаметр буртика под подшипник:
Принимаем
Зазор между поверхностями вращающихся деталей редуктора и внутренними
поверхностями стенок его корпуса:
Расстояние
между внешними поверхностями деталей передач:
Принимаем
и
Расстояние
между торцами подшипников вала-шестерни:
Длина
ступени вала-шестерни под уплотнение крышки с отверстием и подшипника:
Длину
выходного конца вала-шестерни под шкив ременной передачи выбираем по диаметру
из табл. 4.1: принимаем
Длина
выходного конца ведомого вала под полумуфту выбираем по табл. 9.2:
Определяем
длину шпоночного паза на выходном участке вала-шестерни:
Длина
шпоночного паза на выходном конце ведомого вала
Диаметр
ступицы колеса:
Принимаем
Длину
ступицы колеса принимаем равной ширине колеса:
Толщина
обода:
Принимаем
Толщина
диска зубчатого колеса:
Принимаем
Длину
посадочной поверхности под зубчатое колесо на ведомом валу назначаем на (2…3)
мм меньше
.
Принимаем
.
5. Основные
конструктивные размеры корпуса редуктора
Корпус редуктора предназначен для размещения и координации, организации
системы смазки деталей зубчатых передач и защиты их от загрязнения. Корпусом
воспринимаются силы, возникающие в зубчатом зацеплении, реакции опор.
Толщину стенки редуктора назначают равной 6 мм и более, согласно
требованиям технологии литья и условиям необходимой прочности и жесткости.
Определяем толщину стенки корпуса редуктора:
Принимаем
Диаметр
винтов крепления крышки редуктора к основанию корпуса:
Принимаем
(т.е. с резьбой М10).
Диаметр
винтов крепления редуктора к фундаменту (или раме):
Принимаем
Длина
фланца корпуса редуктора:
Ширина
фланца корпуса редуктора
Принимаем
Расстояние
между дном корпуса редуктора и нижней точкой поверхности колеса:
6. Проверка
долговечности подшипников
Пригодность
подшипника определяют сопоставлением долговечности в часах
соответствующего выбранного подшипника с заданным
сроком службы (в часах) всего редуктора
, т. е.
подшипник считают годным, если выполняется условие:
.1
Определение расстояний между линиями действия сил в зацеплении и реакций опор
Радиальную реакцию подшипника считают приложенной к оси вала в точке
пересечения с ней нормали, проведенной через середину контактной площадки. Для
радиальных подшипников эта точка расположена на середине ширины подшипника
При
установке радиальных подшипников расстояние
от
плоскости приложения сил в зацеплении до точки приложения радиальной реакции в
опоре определяется по формуле:
· на ведущем валу
· на ведомом валу
6.2
Определение реакций опор
Рис.6.2.1 - Расчетные схемы ведущего и ведомого валов
Быстроходный вал:
В плоскости YOZ:
Проверка:
В
плоскости XOZ:
Проверка:
Результирующие
реакции в опорах 1 и 2 определяем по теореме Пифагора (см. рис. 4.4):
Тихоходный
вал:
Плоскость
YOZ:
Проверка
Плоскость
XOZ:
Проверка:
Результирующие
реакции в опорах 3 и 4:
.3
Определение суммарных реакций
На выходные концы валов действуют консольные нагрузки со стороны
ременных, цепных передач, соединительных муфт и т.д.
Рис.6.3.1
- Схема к определению реакций, возникающих в опорах ведущего вала от консольной
силы
На
выходной конец ведомого вала со стороны зубчатой муфты действует изгибающий
момент:
Реакции
опор 3 и 4 от момента
:
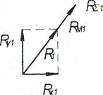
Рис. 6.3.2 - Схемы к определению полных реакций в
каждой опоре ведущего вала
Суммарные реакции опор ведущего вала:
Суммарные
реакции опор ведомого вала:
.4
Определение долговечности подшипников
Ведущий вал
Проверяем
подшипник шариковый 309, с динамической грузоподъёмностью С=52,7 кН; и
статической
Определяем
отношение:
По
табл. 7.1 этому отношению соответствует
.
Отношение:
По
этому эквивалентная нагрузка определяется по формуле:
Долговечность
в млн.об:
Долговечность
в часах:
Что
больше срока службы всего редуктора
.
Т.е.
подшипник 309 пригоден для ведущего вала.
Ведомый
вал
Наиболее
нагружена опора 4.
Внешняя
осевая сила:
.
Радиальная
нагрузка:
.
Определяем
отношение:
Эквивалентная
нагрузка:
Долговечность
в млн.об:
Долговечность
в часах:
что
больше срока службы всего редуктора
ч.
Т.е.
подшипник 310 пригоден для ведомого вала.
7. Проверка
прочности шпоночных соединений
Шпоночное соединение образуют вал, шпонка и ступица насаженной на вал
детали (зубчатого колеса, шкива, звездочки и т.п.). Предназначено для передачи
вращающего момента между валом и ступицей.
Рис. 7.1 - Шпоночные соединения с призматическими
шпонками
Напряжение смятия и условие прочности определяют по формуле:
При
стальной ступице допускаемые напряжения смятия принимают в интервале:
Шпонка
на ведущем валу (
) по табл. 8.1:
Напряжение
смятия шпоночного соединения «быстроходный вал-ведущий шкив»:
Условие
прочности выполнено.
Шпонка
(
):
Напряжение
смятия шпоночного соединения «тихоходный вал-зубчатая муфта»:
Условие
прочности выполнено.
Шпонка
(
):
Напряжение
смятия шпоночного соединения «тихоходный вал-зубчатое колесо»:
Условие
прочности выполнено.
8. Выбор муфт
Муфтами приводов называют устройства, соединяющие валы совместно
работающих агрегатов и передающие вращающий момент.
Муфты выбирают по большему диаметру концов соединяемых валов и
номинальному моменту, передаваемому муфтой. На выходном конце ведущего вала
редуктора устанавливают большой шкив ременной передачи.
На выходном конце ведомого вала устанавливают муфту зубчатую (ГОСТ
5006-83) (табл. 9.2):
Рис.
8.1 Муфта зубчатая
9. Выбор
посадок основных соединений
Посадка - характер соединения двух деталей, определяемый величиной
получающихся в нём зазоров или натягов.
Различают посадки трёх типов: с зазором, с натягом и переходные. При
передаче вращающего момента шпоночным соединением, применение посадок колеса на
вал с зазором недопустимо, а посадок переходных - крайне нежелательно, так как
происходит обкатывание со скольжением поверхностей вала и отверстия колеса,
которое приводит к износу. Поэтому на посадочных поверхностях вала и отверстия
колеса следует создавать натяг.
Поле допуска вала под внутренним кольцом подшипника - k6.
Поле допуска вала под резиновыми манжетами (уплотнениями) - h11.
Поле допуска вала корпуса редуктора под внешним кольцом подшипника - Н7.
Посадка зубчатое колесо - вал - Н7/s6.
Посадка стакан - корпус редуктора - Н7/h8.
Посадка дистанционная втулка - вал - D9/k6.
Посадка полумуфта - конец вала - Н7/p6.
Посадка боковая поверхность шпонки - вал - Р9/h9.
10 Выбор
смазочного материала
Для уменьшения потерь мощности на трение и снижения интенсивности износа
трущихся поверхностей, а также для предохранения их от заедания, задиров,
коррозии и лучшего отвода теплоты трущиеся поверхности деталей должны иметь
надежную смазку.
Для смазки зубчатых передач применяют картерную систему смазки.
Рекомендуемая вязкость масла для зубчатых колес при 50ºС 60·10-6 м2/с (по табл. 8.1), сорт
масла по табл. 8.3 - Индустриальное И-70 А.
Подшипники смазывают тем же маслом, что и детали передач.
Предельно допустимые уровни погружения колес цилиндрического редуктора в
масляную ванну:
Заключение
По данным задания на курсовую работу был спроектирован привод скребкового
конвейера для транспортировки породы и для опоры перемещения комбайна,
представляющий собой электродвигатель, одноступенчатый цилиндрический косозубый
редуктор.
В процессе проектирования подобран электродвигатель АИР 112МВ6/950,
произведен расчет зубчатых колес редуктора, для этого выбраны материалы для
изготовления зубчатых колес и термической обработки, определены допускаемые
напряжения, также сделаны расчеты зубчатой передачи и сил зацепления, проверены
зубья по контактному напряжению и по напряжению изгиба. В данной работе
произведен расчет валов, выбраны подшипники, муфты, посадки основных
соединений, смазочный материал, рассчитаны основные конструктивные размеры
вала-шестерни, ведомого вала, зубчатого колеса и корпуса редуктора, также
проверены долговечности подшипников, прочности шпоночных соединений и определены
расстояния между линиями действий сил зацепления и реакции опор.
Список
использованной литературы
1. Дунаев
П.Ф., Леликов О.П. Детали машин. Курсовое проектирование: Учеб. пособие для
машиностроит. спец. техникумов. - М.: Высш. шк., 1984. - 336 с., ил.
. А.Е.
Шейнблит «Курсовое проектирование деталей машин», Москва, «Высшая школа»,1991г.
. Методические
указания по курсовому проектированию. Магнитогорск, 2003.
. В.С.
Блинов, Л. С. Белевский, Е. Е, Блинов «Методическое указание: Руководство по курсовому
проектированию деталей машин», Магнитогорск, 2005 г.