Разработка электропривода сушильной установки растительного сырья АО 'Шымкентмай'
1 Научно-исследовательская часть
.1 Физико-механические свойства растительного
сырья
Важным физико-механическим свойством
растительного сырья как объекта сушки является сыпучесть, характеризующаяся
углом естественного откоса. Определяющее значение на сыпучесть семян
подсолнечника оказывают влажность семян, содержание посторонних примесей и их
характер, а также поверхность, по которой перемещаются семена. Угол
естественного откоса сухих семян подсолнечника колеблется от 27 до 35°, влажных
- до 42°, что значительно выше, чем у злаковых культур. Эти особенности семян
подсолнечника вызывают определенные трудности при их поточной обработке.
Легковесные семена, имея повышенный коэффициент внутреннего трения, на
некоторых участках технологической схемы передвигаются медленнее, чем зерно
колосовых культур или кукурузы. Поэтому при работе с семенами подсолнечника
трубы зерносушилок должны иметь больший диаметр и их устанавливают под большим
углом наклона.
Наличие воздушной прослойки между ядром и
плодовой оболочкой семян, а также значительное содержание жира является
причиной более низкой скорости витания семян подсолнечника, чем для зерна.
Поэтому во избежание выноса полноценных семян из коробов шахты и камеры нагрева
сушилки скорость агента сушки должна быть ниже, чем при сушке зерновых культур.
Удлиненная форма семянок подсолнечника и
сравнительно шероховатая поверхность обусловливают большую скважистость. Так,
скважистость подсолнечника колеблется в пределах 60-80%, а риса 50-65, пшеницы
35-45 и кукурузы 35-55%. Следовательно, семена подсолнечника, имея большую
скважистость, оказывают меньшее сопротивление при прохождении агента сушки в
сушилках и сушатся быстрее, чем семена других культур.
Гигроскопичность - одно из важнейших свойств
зерна, определяющих режимы его хранения и сушки. Для семян подсолнечника как
капиллярно-пористых коллоидных тел характерны все формы связи, которые, по
классификации академика Л.А. Ребиндера, подразделяются на химическую,
физико-химическую и механическую. В процессе сушки семян их основные физические
и химические свойства должны сохраниться, следовательно, химически связанную
влагу не надо удалять.
Влажность семян подсолнечника, при которой
остается химически и адсорбционно связанная влага, часто называют критической.
Эта влага не участвует в жизненных процессах, не может быть использована
большинством микроорганизмов для поддержания своей жизнедеятельности и поэтому
не влияет на стойкость семян подсолнечника в процессе хранения. Следовательно,
сушить семена необходимо до такой влажности, чтобы в них оставалась
преимущественно адсорбционно связанная вода.
Равновесная влажность семян подсолнечника, т.е.
влажность, при которой семена не отдают и не поглощают влагу, зависит от
температуры, относительной влажности атмосферного воздуха, масличности.
При всех равных условиях равновесная влажность
масличных культур в 2 раза меньше, чём зерновых. Это объясняется меньшим
содержанием в семенах масличных культур гидрофильных коллоидов и наличием
большого количества жира. С увеличением содержания масличности в семенах
равновесная влажность подсолнечника уменьшается, так как с повышением
масличности уменьшатся содержание гидрофильных веществ и соответственно
увеличивается содержание гидрофобных.
Значительное содержание оболочки в подсолнечнике
и ее высокая гигроскопичность являются предпосылками для разработки
рациональных осциллирующих режимов - чередования сушки, охлаждения и
отволаживания. Например, применение чередования интенсивной продувки и
отволаживания, во время которого влага концентрируется в оболочке, приводит к
интенсификации влагоотдачи при сушке, так как влагопроводность оболочки выше,
чем ядра, и зона испарения находится у поверхности.
Равновесная влажность составных частей семян
неодинакова: она больше у оболочки и меньше у ядра. Содержащиеся в массе семян
подсолнечника органические и сорные примеси обладают большой гигроскопичностью.
При одной и той же относительной влажности и температуре воздуха равновесная
влажность органических сорных примесей больше равновесной влажности семян в 1,8
раза.
Основными теплофизическими характеристиками,
определяющими теплообменные свойства масличных семян, являются теплоемкость,
коэффициенты теплопроводности и температуропроводности. Теплофизические
характеристики, определяющие скорость протекания процессов нагрева и
охлаждения, различны для отдельных семянок и семенной массы, но в обоих случаях
зависят прежде всего от размеров семянок, их влажности, химического состава,
масличности, лузжистости и температуры. На теплофизические показатели семенной
массы большое влияние оказывают количество и состав содержащихся в ней
примесей.
При увеличении влажности семян подсолнечника до
17,8% теплоемкость возрастает по линейному закону. Повышение влажности да 11 %
приводит к увеличению коэффициента теплопроводности, дальнейшее повышение
влажности не влияет на изменение величины этого коэффициента. Коэффициент
температуропроводности семян при увеличении влажности до 11% возрастает, а при
дальнейшем увеличении снижается.
1.2 Технология сушки семян
пецифические свойства семян подсолнечника как
объекта сушки, неоднородность семянки (наличие ядра, плодовой и семенной
оболочек), естественная неоднородность семян по размерам, массе и влажности,
низкая прочность плодовой оболочки, влагоинерционность, низкая теплопроводность,
термолабильность белковой и липидной частей системы, повышенная пожарная
опасность предъявляют особые требования к способу сушки и к конструкции
сушильных устройств. При сушке не должно ухудшаться качество и уменьшаться
выход масла, не должно происходить растрескивания лузги и увеличения масличной
примеси. Не допускается увеличение в процессе сушки кислотного и йодного чисел
жира, изменение вкусовых и пищевых достоинств подсолнечного масла.
Одним из наиболее рациональных методов улучшения
технологических свойств, сохранения качества и повышения стойкости семян
подсолнечника в процессе хранения является тепловая сушка.
При сушке семян подсолнечника большое значение
имеет не только температура нагрева семян, но и продолжительность ее
воздействия. Значения коэффициентов теплопроводности, температуропроводности
для единичной семянки значительно отличаются от тех же показателей для плотного
слоя. Для быстрого нагрева семян необходима такая конструкция сушильного
аппарата, в котором бы обеспечивался нагрев каждой единичной семянки в
отдельности. В этом случае можно значительно поднять температуру агента сушки
при снижении продолжительности нагрева до нескольких секунд. Кратковременное
высушивание семян подсолнечника при более высокой температуре предпочтительнее,
чем медленное высушивание при низкой.
При сушке семян подсолнечника необходим
обоснованный выбор температурных режимов. Сушка должна протекать с минимальными
затратами тепла и электроэнергии, с максимальной скоростью удаления влаги при
наилучших технологических свойствах высушенного материала.
Сушка представляет собой комплекс одновременно
протекающих и влияющих друг на друга явлений. Это - перенос тепла от агента
сушки к высушиваемому материалу через его поверхность, испарение влаги,
перемещение влаги внутри материала, перенос влаги с поверхности материала в
сушильную зону.
На испарение влаги влияют в основном два
процесса: влаго-проводность и термовлагопроводность, которые характеризуют
внутренний тепло- и влагоперенос во влажном материале. При испарении влаги
поверхностные слои подсушиваются. Создается градиент влагосодержания, т. е.
внутри материала влаги больше, чем на поверхности. Это явление приводит к
перемещению влаги из внутренних слоев к поверхностным слоям и называется
влаопроводностью. Причем это перемещение тем интенсивнее, чем выше температура
материала. Отсюда вытекает основное правило сушки: необходимо в начале
сушильного процесса поддерживать максимально допустимую температуру материала,
при которой не наблюдается ухудшения пищевых, технологических, семенных и
других достоинств семян подсолнечника.
Но влага перемещается не только благодаря
градиенту влагосодержания, она перемещается и благодаря градиенту температур
(термовлагопроводности), т. е. влага перемещается от малонагретого участка к более
нагретому, или, иными словами, влага перемещается по направлению потока тепла.
Применение того или иного способа сушки может
способствовать в одном случае совпадению направления перемещения влаги как в
результате влагопроводности, так и термовлагопроводности, а в другом случае
процесс испарения влаги в результате влагопроводности тормозит процесс
испарения влаги в результате термовлагопроводности. В первом случае процесс
испарения влаги будет протекать значительно интенсивнее, чем во втором. Для
того чтобы эти процессы испарения влаги совпадали по направлению, необходимо,
чтобы температура поверхности семянки подсолнечника была ниже температуры
внутри ядра. Сушка будет значительно тормозиться, когда температура поверхности
семянки выше температуры внутри ядра.
При сушке семян подсолнечника в шахтных
прямоточных сушилках явление термовлагопроводности препятствует перемещению
влаги изнутри к поверхности и интенсивность потока влаги равна разности между
интенсивностью потока влаги в результате влагопроводности и интенсивностью
потока влаги в результате термовлагопроводности. При рециркуляционной сушке
влага испаряется как под воздействием процесса влагопроводности, так и под
воздействием термовлагопроводности.
Температура материала в процессе сушки не, равна
температуре агента сушки. В первом периоде сушки температура материала равна
температуре смоченного термометра, поэтому можно применять высокие температуры
агента сушки. Например, при температуре воздуха 200° С и влагосодержании его
0,008 кг/ кг температура смоченного термометра, а следовательно, и температура
материала равна 47° С. При повышении температуры воздуха до 350° С при данном
влагосодержании температура смоченного термометра увеличивается до 60° С.
При кратковременном нагреве материала температуру
агента сушки можно значительно повысить. Пределом является температура, при
которой температура испарения (температура смоченного термометра) будет равна
или близка к допустимой температуре нагрева материала.
При высокой температуре агента сушки прогрев
семян до допустимых температур и испарение влаги с поверхности происходят в
течение нескольких секунд. Дальнейший подвод тепла нецелесообразен. Таким
образом, для максимального использования тепла и сохранения качества семян
рекомендуется применять максимально возможные температуры агента сушки при
небольшой продолжительности нагрева.
На предприятиях масложировой промышленности
используются стационарные сушильные установки: шахтные, барабанные, газовые
рециркуляционные, с «кипящим» слоем семян и др. Сушилки состоят из сушильной и
охладительной камер.
При сушке семян подсолнечника в шахтных
сушильных аппаратах необходима их первоначальная очистка от сорных примесей,
поскольку они могут привести к засорению сушилки и её возгоранию. Семена,
имеющие высокую влажность, в таком сушильном аппарате могут подвергаться двух-,
а, нередко, и трёхкратной сушке. Поточность обработки при этом нарушается, что
вызывает затруднения в работе с вновь поступающими семенами. В результате
неравномерного движения по шахтным сечениям при их обработке горячим воздухом,
семечки прогреваются неравномерно, температурная разница может составлять до 10
градусов. Это связано с тем, что у стенок шахт семена перемещаются медленнее,
чем в центре. Кроме того, недостаточная пропускная способность сушилки может
привести к перегреву части семечек.
Рециркуляционные сушильные аппараты, в отличие
от прямоточных, позволяют высушивать семечки с различной влажностью за один
цикл. Технология сушки семечек в рециркуляционных сушильных аппаратах с камерами
нагрева в падающем слое заключается в чередовании краткосрочного нагрева семян
в восходящем потоке горячего воздуха при температуре 250-350°С, отлежки
нагретых семян, их охлаждении и рециркуляции. При данном способе одновременно с
сушкой семян происходит и их очистка от сорных примесей. При высушивании семян
подсолнечника в сушилках рециркуляционного типа очень важно равномерно
распределять семена по всему сечению камеры, а также не допускать скопления
масличной пыли в камере нагрева и устранять попадание искр из топки в камеру
нагрева, поскольку сушилки данного типа являются пожароопасными.
Преимуществом вентилируемых бункеров является их
простота и продолжительный срок эксплуатации. Мягкие режимы сушки не допускают
травмируемость семян подсолнечника. Однако такой способ сушки намного
продолжительнее остальных по времени, и характеризуется неравномерностью
просушивания семян. Чтобы этого избежать, вентилятор периодически необходимо
отключать, а семенатехнологи - тщательно перемешивать.
Чаще всего на предприятиях применяются
барабанные сушильные аппараты с различными режимами сушки, зависящими от
влажности сырых семян. Температура сушильного агента (нагретого воздуха) при
этом должна быть настолько выше, насколько выше влажность семян подсолнечника.
Высушивание семечек в сушилках барабанного типа осуществляется в пересыпающемся
слое семян, при его продуве горячим воздухом. Вначале сушки температура
сушильного агента, в зависимости от влажности семян, удерживается на уровне
250-350 °С, на выходе из сушилки - 50-80°С. В среднем, сушка семян
подсолнечника в барабанных сушилках продолжается 15-20 минут.
По сравнению с другими типами сушилок барабанные
сушилки обладают рядом преимуществ: возможность полной автоматизации процесса;
универсальность; высокое качество сушки за счет интенсивного перемешивания
материала; возможность сушить высоковлажный, засоренный материал; простота
монтажа (для запуска в работу не требуется капитальных сооружений); надежность
работы (исключается образование застойных зон); приемлемая цена; низкое
потребление электроэнергии.
Исходя из этого выбираем сушилку барабанного
типа.
2 Технологическая часть. Краткое описание
технологии производства и конструкции механизма
На предприятии АО "Шымкентмай"
добывание масла включает следующие стадии: подготовка сырья; форпрессование;
фильтрация сырого масла; экстракцию масла из жмыха; раздельная рафинация
форпрессового и экстракционного масел.
На этапе подготовки семян к извлечению масла
производится их очистка от загрязнений и мусора, калибрование по размерам.
Далее следует обрушивание семян, дробление рушанки, размельчение ядра.
Следующий этап это форпрессование.
Форпрессование это получение растительного масла из очищенных и измельченных
семян, путем отжима (прессования). На данном этапе можно извлечь от 60% до 85%
масла. Такой отжим называется «холодным отжимом», а полученное масло называется
сырым. Далее масло отстаивают и производят фильтрацию для освобождения масла от
суспендированных в нем частиц.
Сущность фильтрации заключается в продавливании
масла через поры полупроницаемой перегородки, через которую проходит жидкая
среда (масло) и не проходит (или почти не проходит) суспендированные частицы.
Жмых полученный после фопрессирования отправляют
на экстракцию. В основе процесса экстракции лежит способность растительных
масел растворяться в органических растворителях. На предприятии АО
"Шымкентмай" в качестве растворителей для извлечения масла из
растительного сырья применяют экстракционный бензин марки «А» и нефракс.
Рафинация состоит из следующих стадий:
гидратация, нейтрализация, отбеливание, вымораживание, дезодорация.
Основная цель гидратации - извлечение из
нерафинированного масла фосфатидов и некоторых гидрофильных веществ. Масло
обрабатывают раствором лимонной или фосфорной кислоты, а затем производят
разделение фаз с использованием сепараторов или емкостных аппаратов с
перемешивающим устройством - нейтрализаторов.
Нейтрализация включает процесс обработки масла
щелочью для удаления жирных кислот.
Отбеливание используется для проведения адсорбционной
очистки от различных пигментов и остатков фосфатидов и мыла после щелочной
нейтрализации. В качестве адсорбента, как правило, используют кислотно
активированную отбельную землю (глину) - природный минерал монтмориллонит.
Вымораживание (винтеризация) используется для
удаления из масел воскоподобных веществ. Проводится в специальных аппаратах -
кристаллизаторах и экспозиторах. В процессе вымораживания масло смешивают с
кизельгуром, либо перлитом и медленно охлаждают до температуры 5-8 оС, затем выдерживают
несколько часов и отправляют на фильтрацию.
Дезодорация является завершающей стадией. Масло
находящееся в дезодораторе обрабатывается острым паром при температурах 225 -
260 оС, и остаточном давлении 1-3 мм. рт. ст. В результате производится удаление
одорирующих веществ, пестицидов, гербицидов и жирных кислот.
В технологической схеме производства
растительного масла на АО Шымкентмай не предусмотрено сушение сырья перед
добыванием масла.
Сушка семян позволяет заметно улучшить качество
растительного масла, а так же увеличивает сроки хранения на складах, так как
семена с влажностью более 7 процентов быстро портится. Исходя из этого, я
считаю необходимым внедрить в процесс производства специальную установку для
сушки сырья.
Рассмотрим выбранную сушилку барабанного типа. В
барабанных сушилках основным рабочим органом является вращающийся пустотелый
стальной цилиндр, называемый барабаном. Внутри по окружности укреплены
изогнутые лопасти, которые при вращении барабана захватывают семена,
находящееся внизу, и поднимают его. По мере подъема лопастей семена ссыпается с
них и распределяется по расположенным внутри барабана полочкам, которые могут
иметь различную форму. При вращении барабана семена пересыпается с полочки на
полочку и таким образом равномерно распределяется по всему сечению его; при
этом оно пронизывается агентом сушки, движущимся вдоль барабана. Для
перемещения семян вдоль барабана его устанавливают с небольшим наклоном.
Движение агента сушки обычно происходит в направлении движения семян, что
способствует ускорению его выхода из барабана. Барабан опирается на ролики; при
небольших размерах его цапфы, укрепленные с обоих торцов, опираются на
подшипники. Барабанные сушилки работают под разрежением во избежание утечки
агента сушки через неплотности наружу. Со стороны поступления семян в барабан и
со стороны выхода из него предусматривают скользящие лабиринтовые уплотнения,
которые, не мешая вращению, в то же время препятствуют прохождению воздуха
внутрь. При многократном пересыпании семян с полки на полку во время вращения
барабана оно хорошо перемешивается и равномерно просушивается. Семена находится
в барабане в разрыхленном состоянии, поэтому сушка его значительно ускоряется
(в 2-3 раза) по сравнению с сушкой семян, лежащего плотным слоем в шахтных
сушилках; снижение влажности его за один пропуск через барабан при условии
сохранения качества составляет 4-5%. Заполнение объема барабана составляет (20-
25%), количество испаряемой в нем влаги (влагонапряжение) при температуре
агента сушки 150-200° находится в пределах 20- 40 кг/м3 в час.
Выбираем сушилку стационарную зерновую сушилку
барабанного типа СЗСБ-8. Рассмотрим процесс сушки и конструкцию сушилки этого
типа (рисунок 2.1). Сырые семена из приемного бункера, поднимаемое скребковым
транспортером, по самотечной трубе попадает в барабан диаметром 1600 мм и
длиной 8000 мм, который опирается на четыре пары роликов и делает 8 об/мин.
- скребковый транспортер сырого зерна; 2 -
самотечная труба; 3 - барабан; 4 - вентилятор; 5 - отводящая камера; 6 -
скребковый транспортер для сухого зерна; 7 - шнек; 8 - вентилятор холодного
воздуха; 9 - охладительная колонка; 10 - шлюзовой затвор.
Рисунок 2.1. Барабанная зерносушилка СЗСБ-8
Семена, поступившие во время вращения, распределяется
равномерно по секторам и полочкам внутри барабана. Агент сушки отсасывается из
смесительной камеры топки, проходит через барабан, продувая пересыпающееся по
полочкам семена, и вентилятором (на одной оси с электродвигателем)
выбрасывается наружу. Семена из барабана поступает в отводящую камеру, из
которой через шлюзовой затвор ссыпается на скребковый транспортер и подается им
на шнек, служащий для загрузки охладительной колонки. Излишек семян из шнека
ссыпается по самотечной трубе под охладитель.
Охладительная колонка состоит из двух
вертикальных цилиндров с перфорированными стенками. Диаметр внутреннего
цилиндра колонки 760 мм, наружного 1260 мм, высота колонки 2750 мм.
Пространство между стенками цилиндров заполняется просушенными семенами. Атмосферный
воздух входит через отверстия в стенке наружного цилиндра, продувает слой семян
и поступает во внутренний цилиндр, откуда отсасывается вентилятором (также на
одной оси с электродвигателем) и выбрасывается наружу. Семена из охладительной
колонки выпускают через шлюзовой затвор.
Топка сушилки на жидком топливе состоит из двух
вертикальных цилиндров, из которых внутренний служит камерой сгорания. В нижней
части ее устанавливают форсунку игольчатого типа. Топливо подается к форсунке
насосом и распыляется воздухом, который нагнетается вентилятором высокого
давления с приводом от электродвигателя. В верхней части камеры сгорания
установлен отражатель. Воздух для охлаждения стенок камеры сгорания поступает
снизу в кольцевое пространство между цилиндрами. Этот воздух смешивается с
топочными газами при выходе их из камеры сгорания. Для снижения температуры
агента сушки наружный воздух подводится через окна.
Для уменьшения потерь тепла в окружающую среду и
во избежание ожогов обслуживающего персонала топку огораживают цилиндрическим
кожухом. Над топкой установлена смесительная коробка, на которой смонтирована
растопочная труба. В коробке имеется дверка для регулирования впуска воздуха.
Заслонка для переключения агента в сушилку, а также заслонка растопочной трубы
сблокированы так, что при открывании одной из них другая закрывается.
.1 Выбор типа электропривода механизма и
предварительный расчет мощности электродвигателей
.1.1 Предварительный расчет мощности и выбор
двигателя
При вращении правильно собранного и нормально
работающего барабана мощность его приводного электродвигателя расходуется в
большей мере на полезную работу: подъем материала на определенную высоту,
сползая с которой, он перемешивается и постепенно перемещается к разгрузочному
концу, и в меньшей мере - на преодоление вредных сопротивлений. К вредным
сопротивлениям относится трение скольжения между поверхностями цапф опорных
роликов и вкладышей подшипников, трение качения бандажей по опорным роликам,
трение в приводном механизме и трение концов корпуса барабана о поверхности
деталей уплотнительных устройств.
Потребная мощность на вращение барабана можно
определить по формуле:
кВт, (2.1)
где N1 - мощность, расходуемая на подъем
материала. - мощность, расходуемая на преодоление трения в подшипниках опорных
роликов и трения бандажей по опорным роликам;
ŋ - коэффициент, учитывающий мощность,
которая расходуется на преодоление трения в приводном механизме и в
уплотнительных устройствах.
Просушиваемое сырьё располагается не симметрично
относительно вертикали, проходящей через центр сечения печи, поэтому он
вызывает постоянно действующий и направленный в сторону, противоположную
вращению барабана, момент силы GM веса материала (рисунок 2.2). Плечом этой
силы а является расстояние от центра тяжести материала до вертикали, проходящей
через центр сечения барабана. Следовательно, мощность, необходимая для подъема
материала, равна:
(2.2)
или
,
где FM - площадь сечения материала (кругового
сегмента) в м2;- длина корпуса в м;
Ум - объемный вес материала в т/м3',- окружная
скорость центра тяжести площади сечения материала в м/сек.
Чтобы по приведенному уравнению можно было
определить полезно расходуемую мощность, необходимо знать количество
находящегося в барабане материала или его среднюю площадь сечения, объемный вес
материала и его угол естественного откоса при движении.
Рисунок 2.2 Схема расположения сырья в барабане
Так как по мере перемещения материала вдоль
барабана его физические свойства непрерывно изменяются и у теплообменников, а
также у порога, если корпус барабана составлен из частей разного диаметра,
происходит скопление материала, определение средней скорости его движения и
площади сечения теоретическим путем связано с очень большими трудностями.
Предложенные для этой цели уравнения, отличаясь сложностью, не отличаются к
тому же нужной точностью по результатам произведенных по ним вычислений.
Поэтому при излагаемом ниже выводе уравнения, определяющего мощность,
необходимую для подъема материала, принимаем, исходя из практических данных,
что:
коэффициент заполнения барабана материалом к3 ==
0,25.
средний объемный вес материала YM == 0,47 т/м3 ;
угол естественного откоса материала (семена
подсолнечника) при движении φ == 42°.
Так как площадь сечения материала в барабане по
форме является круговым сегментом, окружная скорость его центра тяжести при
вращении равна:
м/сек, (2.3)
Неизвестной величиной в приведенном уравнении
является лишь угол а, равный половине центрального угла, опирающегося на хорду
кругового сегмента, его можно найти из уравнения:
(2.4)
которое выражает площадь кругового сегмента.
Подставляя в это уравнение вместо FM принятую для нее числовую величину,
соответствующую коэффициенту заполнения =0,25, получаем:
(2.5)
,
откуда а=65°
v0=0,283
, =5,24квт.
Трение качения бандажа по роликам незначительно
по сравнению с трением скольжения цапф роликов о вкладыши подшипников, поэтому
нет необходимости его вычислять отдельно, а целесообразнее учитывать повышением
коэффициента трения скольжения. Тогда мощность, необходимая на преодоление
трения в подшипниках роликов и бандажей о ролики, может быть найдена из
уравнения
квт (2.6)
Сила трения и окружная скорость цапф
соответственно равны:
(2.7)
и
(2.8)
Подставив в уравнение (2.6) приведенные значения
для силы трения Ртр окружной скорости цапфы vц и произведя сокращения, имеем:
(2.9)
где f - коэффициент скольжения между цапфами
роликов и вкладышами подшипников;ц - радиус цапф роликов в м;- число оборотов
барабана в минуту;- диаметр бандажей в м;- диаметр опорных роликов в м;= (G1 +
G2) - общий вес вращающейся части барабана в т. = 8 тонн - вес барабана= 1,9
тонны - вес сырья в барабане.
По этому уравнению определяется общая мощность,
потребная для вращения барабана с корпусом одного диаметра по всей длине. Если
корпус состоит из зон разного диаметра, то потребная мощность вычисляется для
каждой зоны отдельно и затем суммируется.
Для подшипников опорных роликов картерного типа
с бронзовыми вкладышами и непрерывной подачей масла на цапфы рекомендуется
коэффициент трения выбирать равным 0,02-0,04. С учетом трения качения бандажей
по роликам приведенные значения необходимо повысить до 0,03-0,06.
Расход мощности на преодоление трения в
приводном механизме и уплотнительных устройствах учитывается КПД установки.
Величина его зависит от конструкции приводного механизма, правильности его
монтажа и эксплуатации и в среднем равна 0,9 - для механизма закрытого типа,
0,85 - для смешанного и 0,8 - для открытого.
При определении необходимой мощности для
вращения барабана в расчетное уравнение подставляют нормальное число оборотов.
Но при эксплуатации барабан часто вращается с повышенным числом оборотов, на
что требуется и повышенная мощность. В момент пуска барабана также необходима
мощность выше нормальной на преодоление силы инерции вращающегося барабана.
Учитывая это, мощность электродвигателя барабана следует выбирать на 20-25%
выше той, которая определяется по уравнению.
Применяя формулы, производим расчет мощности
электродвигателя.
Мощность, расходуемая на подъем материала:
,=5,24квт.
Мощность трения барабана на роликах и бандажах:
Общая мощность:
=8,08
Мощность необходимая для пуска электродвигателя
учитывается без массы семян Nп- мощность пустого барабана равна
(2.10)
Учитывая и инерционную мощность барабана,
которая должна быть на 20- 25% выше рабочей мощности, окончательно получаем:
двигателя = 8,08*1,2 =9,7 кВт.
Выбираем трехфазный асинхронный двигатель серии
АИР 160S6 мощность - 11 кВт, синхронная скорость вращения - 1000 об/мин,
скольжение - 3%. С учетом скольжения номинальная частота вращения nном=970
об/мин. Технические характеристики двигателя АИР 160S6 представлены в таблице
2.1.
Таблица 2.1
Технические характеристики двигателя АИР 160S6
Электро-двигатель
|
Мощность
|
Об/мин.
|
Ток
при 380В, А
|
KПД,
%
|
Kоэф.
мощн.
|
Iп/
Iн
|
Мп/Мн
|
Мmax/Мн
|
Момент
инерции, кг*м2
|
Масса,
кг
|
АИР160S6
|
11
кВт
|
970
|
24,5
|
87,5
|
0,78
|
6,5
|
1,7
|
2,1
|
0,0700
|
125
|
Определение вращающих моментов на валах привода.
Вращающий момент на барабане:
(2.11)
Н*м
Вращающий момент на валу подвенцовой шестерни:
(2.12)
где iЦ - передаточное число зубчатой передачи,
принимаем iЦ =10,
ŋ1=0,94ч0.96 - КПД цилиндрической передачи,
принимаем ŋ1=0,95
В численном значении получаем:
.3, Н*м (2.13)
Вращающий момент на первичном валу редуктора (на
валу электродвигателя) Мn1:
(2.14)
Н/м
Вращающий момент пустого барабана равен:
(2.15)
Вращающий момент на первичном валу редуктора (на
валу электродвигателя) Мпn1:
-коэффициент
передачи шестерни и редуктора = 120
Мп пустого барабана равна 68,35 Н*м
.1.2 Кинематический расчет
Целью кинематического расчета барабанной сушилки
является определение общего передаточного отношения от вала электродвигателя до
вала ведущего звена исполнительного механизма; распределение общего
передаточного отношения всей кинематической цепи привода между отдельными
передаточными механизмами, составляющими цепь; определение конструктивных
параметров зубчатой передачи барабанной сушилки; определение частот вращения
валов передаточных механизмов кинематической цепи.
Определение передаточного числа привода.
Кинематическая схема привода показана на рисунке
2.3.
Общее передаточное число привода определяем из
соотношения:
(2.17)
где nБ=8 мин-1 - частота вращения барабана;
- электродвигатель; 2,4- муфты; 3- редуктор; 5-
подвенцовая шестерня; 6- венцовая шестерня; 7- барабан.
Рисунок 2.3. Кинематическая схема привода
Распределение общего передаточного числа
привода.
Для многоступенчатых передач:
, (2.18)
где i1, i2, i3 - передаточные числа отдельных
ступеней.
Учитывая предполагаемое устройство механизма, а
также стремясь обеспечить соразмерность деталей привода, в частности диаметр
подвенцовой шестерни должен вписываться в размеры сторон торца редуктора.
Передаточное число редуктора будет равно:
(2.19)
Определение частоты вращения валов.
Частота вращения вала электродвигателя, а,
следовательно, и быстроходного вала редуктора
Частота вращения тихоходного вала редуктора
определяется так:
; (2.20)
Частота вращения подвенцовой шестерни:
об/мин
Полученные значения частот вращения сведены в
таблицу 2.2.
Таблица 2.2
Частоты вращения валов (барабана)
Вал
электродвигателя
|
Быстроходный
вал
|
Тихоходный
Вал
|
Подвенцовая
шестерня
|
Барабан
|
970
|
970
|
80
|
80
|
8
|
Проектный расчет зубчатой цилиндрической
передачи.
Определение допускаемого контактного напряжения.
Расчет ведем по [7].
Допускаемое контактное напряжение определяется
по зависимости:
где - предел контактной выносливости зуба,
соответствующий эквивалентному числу циклов, МПа;
коэффициент безопасности; для зубчатых колес с
однородной структурой материала [7];
коэффициент, учитывающий шероховатость
сопряженных поверхностей зубьев, для зубчатых передач 9 степени точности
;
коэффициент, учитывающий окружную скорость; при
;
коэффициент, учитывающий влияние смазки; из-за
недостаточности экспериментальных данных принимается равным единице,
;
коэффициент, учитывающий размер зубчатого
колеса; ориентировочно принимаем
,
Предел контактной выносливости зуба,
соответствующий эквивалентному числу циклов:
; (2.22)
где - допускаемое контактное напряжение,
соответствующее базовому числу циклов напряжений;
коэффициент долговечности при расчете на
контактную выносливость.
Допускаемое контактное напряжение, соответствующее
базовому числу циклов напряжений:
; (2.23)
где - средняя твердость для двух предельных
значений твердости колес.
В численном значении получаем:
;
.
Коэффициент долговечности при расчете на
контактную выносливость:
(2.24)
где - базовое число циклов перемены напряжений
соответствующее длительному пределу выносливости;
эквивалентное число циклов перемены напряжений.
Базовое число циклов перемены напряжений
соответствующее длительному пределу выносливости:
; (2.25)
;
.
При постоянной нагрузке и зацеплении с одним
колесом:
; (2.26)
где - полное число часов работы за расчетный
срок службы, принимаем
;
частота вращения.
В численном значении получаем:
;
Так как
,
то
.
Предел контактной выносливости зуба,
соответствующий эквивалентному числу циклов:
;
.
Подставляя полученные значения в формулу (2.21)
получим:
;
Для прямозубых колес в качестве принимается
допускаемое контактное напряжение того зубчатого колеса, для которого оно
меньше. Таким образом
Определение межосевого расстояния.
Определяем межосевое расстояние венцового
зацепления по формуле
; (2.27)
где - крутящий момент на шестерне;
коэффициент, учитывающий распределение нагрузки
по ширине;
вспомогательный коэффициент, для прямозубых
передач
;
коэффициент ширины колес относительно межосевого
расстояния; принимаем
.
Коэффициент выбираем в зависимости от
относительной ширины зубчатого венца шестерни
:
; (2.28)
.
Тогда в соответствии с [7]
Значение межосевого расстояния по формуле
(2.27):
мм
Согласно [7] полученное значение округляем до
ближайшего стандартного значения
.
Определение модуля передачи.
Значение модуля m для улучшенных колес
определяется из следующего выражения:
; (2.29)
.
Согласно [7] принимаем стандартное значение
модуля
.
Суммарное число зубьев:
; (2.30)
Число зубьев шестерни и колеса.
Число зубьев шестерни:
. (2.31)
Значение z1 округляем в ближайшую сторону до
целого числа. Принимаем z1=18.
Число зубьев колеса определяем по формуле:
; (2.32)
Фактическое передаточное число.
Находим фактическое передаточное число:
; (2.33)
Отклонение фактического передаточного от
номинального
что допустимо [7, стр. 30].
Расчет основных геометрических параметров.
Определяем делительный диаметр шестерни:
; (2.34)
Определяем делительный диаметр колеса:
; (2.35)
.
Определяем диаметр начальной окружности
шестерни:
; (2.36)
Определяем диаметр начальной окружности
шестерни:
; (2.37)
Определяем диаметр окружности вершин шестерни:
; (2.38)
где: у - коэффициент воспринимаемого смещения.
где а - делительное межосевое расстояние.
;
;
Определяем диаметр окружности вершин колеса:
; (2.40)
.
Определяем диаметр впадин зубьев шестерни:
; (2.41)
.
Определяем диаметр впадин зубьев колеса:
; (2.42)
.
Рабочая ширина венца шестерни:
; (2.43)
.
Высота зуба:
; (2.44)
.
Определение окружной скорости и назначение
степени точности.
Окружная скорость шестерни определяется по
формуле:
; (2.45)
Руководствуясь [7, табл.3.8, стр. 36] для
открытых тихоходных передач с пониженным требованием точности с назначается 9
степень точности.
Основные параметры шестерни и колеса:
Модуль зацепления
;
Число зубьев: подвенцовой шестерни
;
Венцовой шестерни
;
Нормальный исходный контур по СТ СЭВ 308 - 76
Коэффициент смещения: подвенцовой шестерни
;
Венцовой шестерни
;
Делительный диаметр: подвенцовой шестерни
;
Венцовой шестерни
;
Начальный диаметр: подвенцовой шестерни
;
Венцовой шестерни
;
Диаметр вершин зубьев: подвенцовой шестерни
;
Венцовой шестерни
;
Диаметр впадин зубьев: подвенцовой шестерни
;
Венцовой шестерни
;
Межосевое расстояние
;
Ширина зубчатого венца
;
Высота зуба
;
Степень точности
.
.2 Расчет статических режимов электропривода
При расчете статического режима работы
электропривода необходимо построить статические характеристики элементов
позволяющие определить количественные и качественные показатели статических
режимов системы.
Механические характеристики двигателя и
производственного механизма.
Номинальная частота вращения:
(2.46)
Синхронная частота вращения:
(2.47)
Номинальный момент:
(2.48)
Критическое скольжение:
(2.49)
Критический момент асинхронного двигателя:
(2.50)
Зависимость скольжения от частоты вращения:
(2.51)
Уравнение механической характеристики АД(формула
Клосса):
(2.52)
Мс = M0 +(Mс.ном −М0 )⋅(
ω/ωном)х (2.53)
где Мс - момент сопротивления производственного
механизма при скорости ω; M0- момент
трения в движущихся частях механизма; Мс.ном - момент сопротивления при
номинальной скорости ωном; х -
показатель степени, характеризующий изменение момента при изменении скорости.
Барабанная сушилка относится к механизму не зависящей от скорости.При этом х=0
и момент сопротивления Mc не зависит от скорости ω .
Пуск двигателя барабанной сушилки происходит при
не заполненном барабане поэтому
Пусковые моменты АД общепромышленных серий на
естественной механической характеристике невелики и составляют (0,3 - 2,0)Mн. А
токи ротора и статора чрезвычайно велики и достигают (5 - 10)Iн.
Пусковой момент двигателя:
(2.54)
Пусковой ток двигателя:
(2.55)
Расчет и построение графиков производим на ЭВМ,
используя программу Excel. Рассчитанные данные запишем в таблицу 2.3
Таблица 2.3.
Рассчитанные механические характеристики
ω
|
|
|
|
0
|
184,1072
|
68,35
|
115,7572
|
25
|
168,8057
|
68,35
|
100,4557
|
40
|
165,0309
|
68,35
|
96,68094
|
50
|
166,5043
|
68,35
|
98,15425
|
80
|
182,3424
|
68,35
|
113,9924
|
92,32
|
227,5
|
68,35
|
159,15
|
93
|
227,1398
|
68,35
|
158,7898
|
95
|
220,9225
|
68,35
|
152,5725
|
95
|
220,9225
|
68,35
|
152,5725
|
99
|
173,072
|
68,35
|
104,722
|
100
|
151,2857
|
68,35
|
82,93567
|
101
|
125,2391
|
68,35
|
56,88907
|
102
|
95,23261
|
68,35
|
26,88261
|
103
|
61,92705
|
68,35
|
-6,42295
|
103,3
|
51,43504
|
68,35
|
-16,915
|
103,6
|
40,76794
|
68,35
|
-27,5821
|
103,9
|
29,96046
|
68,35
|
-38,3895
|
104,2
|
19,04891
|
68,35
|
-49,3011
|
104,5
|
8,07079
|
68,35
|
-60,2792
|
104,72
|
0
|
68,35
|
-68,35
|
Рисунок 2.4.Механические характеристики АД и
механизма.
Номинальные потери мощности для двигателя
АИР160S6
(2.56)
Вт
Переменные потери мощности:
α=0.6
(2.57)
Вт
(2.58)
(2.59)
Номинальное скольжение:
(2.60)
(2.61)
Потери мощности в роторе в номинальном режиме:
(2.62)
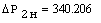
После подстановки получаем:
После упрощения получаем:
Находим корни квадратного уравнения:
Принимаем значение
=
0,3668
Ток ротора:
(2.63)
Построение ЕМХ при f равной 10,25,50,60 Гц.
Вычисления и построение графиков проводим в
программе Excel используем формулы:
(2.64)
(2.65)
(2.66)
(2.67)
(2.68)
(2.69)
α=0.044
(2.70)
Рассчитанные данные заносим в таблицы 2.4, 2.5.
Рисунок 2.5. Механические характеристики АД при
изменении частоты по закону U/f=const.
Таблица 2.4
Расчет данных для построения МХ при f=10, 25,
50, 60 Гц
f
|
Uф'
|
ω1
|
Sк
|
ωк
|
Мк
|
Мп
|
10
|
44
|
20,944
|
0,592
|
8,545152
|
227,4478
|
112,9586
|
25
|
110
|
52,36
|
0,2368
|
39,96115
|
227,4478
|
167,5913
|
50
|
220
|
104,72
|
0,1184
|
92,32115
|
227,4478
|
184,1332
|
60
|
264
|
125,664
|
0,098667
|
113,2652
|
227,4478
|
186,107
|
Таблица 2.5
Расчетные данные для построения графиков МХ
s
|
M(10Гц)
|
M
(25Гц)
|
M
(50Гц)
|
M
(60Гц)
|
0,0001
|
0,08
|
0,19
|
0,38
|
0,46
|
0,002
|
6,91
|
7,68
|
7,68
|
9,22
|
0,01
|
74,71
|
56,72
|
38,15
|
45,64
|
0,02
|
137,94
|
74,71
|
74,71
|
88,57
|
0,04
|
183,42
|
137,94
|
137,94
|
158,39
|
0,07
|
211,02
|
163,03
|
199,28
|
214,68
|
0,1
|
224,24
|
219,15
|
224,24
|
227,45
|
0,1184
|
227,45
|
227,45
|
227,45
|
208,82
|
0,22
|
163,77
|
216,98
|
218,66
|
177,50
|
0,5
|
148,35
|
208,77
|
167,51
|
157,23
|
0,8
|
122,05
|
176,28
|
170,70
|
168,59
|
1
|
112,96
|
167,59
|
184,13
|
186,11
|
.3 Расчет динамических режимов электропривода
Рассчитывается приведенный момент инерции
системы «электродвигатель - рабочая машина» относительно вала электродвигателя
(2.71)
где К2=1,2 - коэффициент, учитывающий
момент инерции редуктора между электродвигателем и валом рабочей машины.
Находим моменты инерции для
электродвигателя и рабочей машины. По каталожным значениям махового момента
определяем
дв = 0,123 кг*м2.м =
, =8000*0,82/2=2560
кг*м2 (2.72)
где m-масса барабана сушилки;радиус
барабана.
Используя построенные механические
характеристики электродвигателя
и рабочей машины
, графически
определяются значения динамического момента равные разности
(2.73)
График динамического момента
разбивается на ряд участков по оси
, для которых динамический момент
можно принять постоянным. Точность тем выше, чем на большее число участков
разделен график динамического момента.
Полученные на отдельных участках
значения динамических моментов откладываются вверх по оси
от начала
координат (рисунок. 2.6). Так, для первого участка получается отрезок
. Точку
соединяют с
точкой
, которая
расположена от начала координат на расстоянии, равном в масштабе величине момента
инерции системы
.
Параллельно
проводят
прямую
из начала
координат. Прямая
характеризует
искомую функцию
для первого
интервала
. Полная
продолжительность пуска равна сумме интервалов. Проведя аналогичное построение
для всех последующих участков, по результирующей кривой определяется искомое
время пуска электропривода tn.
Рисунок 2.6. Графоаналитическое
решение уравнения движения электропривода
Используя построенные механические
характеристики электродвигателя, рабочей машины и динамического (избыточного)
момента, можно без построения функции
аналитически рассчитать искомое
время пуска привода
.
Цена деления t=
= 5,8 сек.
(2.74)
Продолжительность разгона
электропривода на каждом интервале частот вращения рассчитывают по выражению
(2.75)
Полная продолжительность пуска равна
сумме частичных продолжительностей
(2.76)
где
- средний динамический момент на
участке
характеристики, принимаемый постоянным,
.
Расчет потерь энергии при пуске и
торможении.
Потери энергии при пуске
асинхронного электродвигателя определяются электрическими потерями энергии в
его обмотках, которые прямо пропорциональны квадрату силы тока.
Потери энергии при пуске
асинхронного электродвигателя с нагрузкой (Дж) рассчитываются по формуле:
(2.77)
где
- продолжительность пуска
электродвигателя, с;
- кратность
пускового тока асинхронного электродвигателя;
- коэффициент равный отношению
постоянных потерь мощности двигателя к переменным. Принять
.
Определяем время самоторможения
двигателя и строим график зависимости скорости от времени рис.2.7.
с; (2.78)
Рисунок 2.7. Зависимость скорости от
времени
Рисунок 2.8. Нагрузочная диаграмма
барабанной сушилки
где: t0 - время простоя барабанной
сушилки, (профилактические работы),п - запуска пустого барабана (32,26 с)з -
загрузки семян, (согласно технологическому процессу) р - работы (длительный
режим),пп - прекращения подачи семян,т - время торможения. (37,94 с).
Для расчёта и построения графиков
времени пуска при частотном управлении электродвигателем, используем программу
Excel. Расчетные данные записываем в таблицу 2.6.
Таблица 2.6
Расчет основных параметров привода
при пуске механизма с использованием частотного преобразователя
t
|
f
|
ω1
|
Sk
|
ω
k
|
ω
n
|
nном
|
Pпотреб
|
Uф
|
Мп
|
Мс
|
Pпот
|
КПД
|
I
|
0
|
9
|
18,85
|
0,66
|
6,451
|
15,7
|
149,6
|
1697,44
|
39,6
|
105,2
|
68,35
|
1116,5
|
0,34
|
53,5
|
1
|
10
|
20,94
|
0,59
|
8,545
|
17,8
|
169,6
|
1924,45
|
44
|
113
|
68,35
|
1139,3
|
0,41
|
45,8
|
2
|
11
|
23,04
|
0,54
|
10,64
|
19,8
|
189,6
|
2151,46
|
48,4
|
119,9
|
68,35
|
1157,9
|
0,46
|
41,1
|
3
|
12
|
25,13
|
0,49
|
12,73
|
21,9
|
209,7
|
2378,46
|
52,8
|
126,2
|
1173,4
|
0,51
|
38
|
4
|
13
|
27,23
|
0,46
|
14,83
|
24
|
229,7
|
2605,47
|
57,2
|
131,8
|
68,35
|
1186,5
|
0,54
|
35,7
|
5
|
14
|
29,32
|
0,42
|
16,92
|
26,1
|
249,7
|
2832,47
|
61,6
|
136,8
|
68,35
|
1197,7
|
0,58
|
34
|
6
|
15
|
31,42
|
0,39
|
19,02
|
28,2
|
269,7
|
3059,48
|
66
|
141,3
|
68,35
|
1207,5
|
0,61
|
32,7
|
7
|
16
|
33,51
|
0,37
|
21,11
|
30,3
|
289,7
|
3286,48
|
70,4
|
145,3
|
68,35
|
1216
|
0,63
|
31,7
|
8
|
17
|
35,6
|
0,35
|
23,21
|
32,4
|
309,7
|
3513,49
|
74,8
|
148,9
|
68,35
|
1223,5
|
0,65
|
30,8
|
9
|
18
|
37,7
|
0,33
|
25,3
|
34,5
|
329,7
|
3740,5
|
79,2
|
152,2
|
68,35
|
1230,2
|
0,67
|
30,1
|
10
|
19
|
39,79
|
0,31
|
27,39
|
36,6
|
349,7
|
3967,5
|
83,6
|
155,1
|
68,35
|
1236,2
|
0,69
|
29,5
|
11
|
20
|
41,89
|
0,3
|
29,49
|
38,7
|
369,7
|
4194,51
|
88
|
157,7
|
68,35
|
1241,6
|
0,7
|
28,9
|
12
|
21
|
43,98
|
0,28
|
31,58
|
40,8
|
389,7
|
4421,51
|
92,4
|
160,1
|
68,35
|
1246,4
|
0,72
|
28,5
|
13
|
22
|
46,08
|
0,27
|
33,68
|
42,9
|
409,8
|
4648,52
|
96,8
|
162,3
|
68,35
|
1250,9
|
0,73
|
28,1
|
14
|
23
|
48,17
|
0,26
|
35,77
|
45
|
429,8
|
4875,52
|
101,2
|
164,2
|
68,35
|
1254,9
|
0,74
|
27,7
|
15
|
24
|
50,27
|
0,25
|
37,87
|
47,1
|
449,8
|
5102,53
|
105,6
|
166
|
68,35
|
1258,6
|
0,75
|
27,4
|
16
|
25
|
52,36
|
0,24
|
39,96
|
49,2
|
469,8
|
5329,53
|
110
|
167,6
|
68,35
|
1262
|
0,76
|
27,1
|
17
|
26
|
54,45
|
0,23
|
42,06
|
51,3
|
489,8
|
5556,54
|
114,4
|
169,1
|
68,35
|
1265,2
|
0,77
|
26,9
|
18
|
27
|
56,55
|
0,22
|
44,15
|
53,4
|
509,8
|
5783,55
|
118,8
|
170,4
|
68,35
|
1268,1
|
0,78
|
26,6
|
19
|
28
|
58,64
|
0,21
|
46,24
|
55,5
|
529,8
|
6010,55
|
123,2
|
171,6
|
68,35
|
1270,8
|
0,79
|
26,4
|
20
|
29
|
60,74
|
0,2
|
48,34
|
57,5
|
549,8
|
6237,56
|
127,6
|
172,7
|
68,35
|
1273,3
|
0,8
|
26,2
|
21
|
30
|
62,83
|
0,2
|
50,43
|
59,6
|
569,8
|
6464,56
|
132
|
173,8
|
68,35
|
1275,7
|
0,8
|
26,1
|
22
|
31
|
64,93
|
0,19
|
52,53
|
61,7
|
589,9
|
6691,57
|
136,4
|
174,7
|
68,35
|
1277,9
|
0,81
|
25,9
|
23
|
32
|
67,02
|
0,18
|
54,62
|
63,8
|
609,9
|
6918,57
|
140,8
|
175,6
|
68,35
|
1279,9
|
0,82
|
25,8
|
24
|
33
|
69,12
|
0,18
|
56,72
|
65,9
|
629,9
|
7145,58
|
145,2
|
176,4
|
68,35
|
1281,9
|
0,82
|
25,6
|
25
|
34
|
71,21
|
0,17
|
58,81
|
68
|
649,9
|
7372,59
|
149,6
|
177,2
|
68,35
|
1283,7
|
0,83
|
25,5
|
26
|
35
|
73,3
|
0,17
|
60,91
|
70,1
|
669,9
|
7599,59
|
154
|
177,9
|
68,35
|
1285,4
|
0,83
|
25,4
|
27
|
36
|
75,4
|
0,16
|
63
|
72,2
|
689,9
|
7826,6
|
158,4
|
178,5
|
68,35
|
1287
|
0,84
|
25,3
|
28
|
37
|
77,49
|
0,16
|
65,09
|
74,3
|
709,9
|
8053,6
|
162,8
|
179,1
|
68,35
|
0,84
|
25,2
|
29
|
38
|
79,59
|
0,16
|
67,19
|
76,4
|
729,9
|
8280,61
|
167,2
|
179,7
|
68,35
|
1290
|
0,84
|
25,1
|
30
|
39
|
81,68
|
0,15
|
69,28
|
78,5
|
749,9
|
8507,61
|
171,6
|
180,2
|
68,35
|
1291,4
|
0,85
|
25
|
31
|
40
|
83,78
|
0,15
|
71,38
|
80,6
|
769,9
|
8734,62
|
176
|
180,7
|
68,35
|
1292,7
|
0,85
|
24,9
|
32
|
41
|
85,87
|
0,14
|
73,47
|
82,7
|
790
|
8961,63
|
180,4
|
181,1
|
68,35
|
1293,9
|
0,86
|
24,8
|
33
|
42
|
87,96
|
0,14
|
75,57
|
84,8
|
810
|
9188,63
|
184,8
|
181,5
|
68,35
|
1295,1
|
0,86
|
24,7
|
34
|
43
|
90,06
|
0,14
|
77,66
|
86,9
|
830
|
9415,64
|
189,2
|
181,9
|
68,35
|
1296,3
|
0,86
|
24,7
|
35
|
44
|
92,15
|
0,13
|
79,75
|
89
|
850
|
9642,64
|
193,6
|
182,3
|
68,35
|
1297,4
|
0,87
|
24,6
|
36
|
45
|
94,25
|
0,13
|
81,85
|
91,1
|
870
|
9869,65
|
198
|
182,7
|
68,35
|
1298,4
|
0,87
|
24,5
|
37
|
46
|
96,34
|
0,13
|
83,94
|
93,2
|
890
|
10096,7
|
202,4
|
183
|
68,35
|
1299,4
|
0,87
|
24,5
|
38
|
47
|
98,44
|
0,13
|
86,04
|
95,2
|
910
|
10323,7
|
206,8
|
183,3
|
68,35
|
1300,3
|
0,87
|
24,4
|
39
|
48
|
100,5
|
0,12
|
88,13
|
97,3
|
930
|
10550,7
|
211,2
|
183,6
|
68,35
|
1301,2
|
0,88
|
24,4
|
40
|
49
|
102,6
|
0,12
|
90,23
|
99,4
|
950
|
10777,7
|
215,6
|
183,9
|
68,35
|
1302,1
|
0,88
|
24,3
|
41
|
50
|
104,7
|
0,12
|
92,32
|
102
|
970
|
11004,7
|
220
|
184,1
|
68,35
|
1302,9
|
0,88
|
24,2
|
Потери энергии при частотном пуске асинхронного
электродвигателя с нагрузкой (Дж) рассчитываются по формуле:
, Дж (2.79)
где ∆tn - продолжительность
пуска электродвигателя при не низменной частоте, с;
кратность
пускового тока асинхронного электродвигателя;
- коэффициент равный отношению
постоянных потерь мощности двигателя к переменным. Принять
.
Таблица 2.7
Расчет потерь энергии ∆W1 при частотном
пуске на каждом интервале времени.
t
|
P
потреб
|
Uф
|
КПД
|
I
|
∆W1
|
0
|
1697,44
|
39,6
|
0,34
|
53,5
|
3623
|
1
|
1924,45
|
44
|
0,41
|
45,8
|
2654
|
2
|
2151,46
|
48,4
|
0,46
|
41,1
|
2140
|
3
|
2378,46
|
52,8
|
0,51
|
38
|
1826
|
4
|
2605,47
|
57,2
|
0,54
|
35,7
|
1616
|
5
|
2832,47
|
61,6
|
0,58
|
34
|
1466
|
6
|
3059,48
|
66
|
0,61
|
32,7
|
1354
|
7
|
3286,48
|
70,4
|
0,63
|
31,7
|
1268
|
8
|
3513,49
|
74,8
|
0,65
|
30,8
|
1200
|
9
|
3740,5
|
79,2
|
0,67
|
30,1
|
1144
|
10
|
3967,5
|
83,6
|
0,69
|
29,5
|
1098
|
11
|
4194,51
|
88
|
0,7
|
28,9
|
1059
|
12
|
4421,51
|
92,4
|
0,72
|
28,5
|
1026
|
13
|
4648,52
|
96,8
|
0,73
|
28,1
|
996,9
|
14
|
4875,52
|
101,2
|
0,74
|
27,7
|
972
|
15
|
5102,53
|
105,6
|
0,75
|
27,4
|
950,1
|
16
|
5329,53
|
110
|
0,76
|
27,1
|
930,8
|
17
|
5556,54
|
114,4
|
0,77
|
26,9
|
913,5
|
18
|
5783,55
|
118,8
|
0,78
|
26,6
|
898
|
19
|
6010,55
|
123,2
|
0,79
|
26,4
|
884
|
20
|
6237,56
|
127,6
|
0,8
|
26,2
|
871,3
|
21
|
6464,56
|
132
|
0,8
|
26,1
|
859,8
|
22
|
6691,57
|
136,4
|
0,81
|
25,9
|
849,2
|
23
|
6918,57
|
140,8
|
0,82
|
25,8
|
839,5
|
24
|
7145,58
|
145,2
|
0,82
|
25,6
|
830,6
|
25
|
7372,59
|
149,6
|
0,83
|
25,5
|
26
|
7599,59
|
154
|
0,83
|
25,4
|
814,7
|
27
|
7826,6
|
158,4
|
0,84
|
25,3
|
807,6
|
28
|
8053,6
|
162,8
|
0,84
|
25,2
|
801
|
29
|
8280,61
|
167,2
|
0,84
|
25,1
|
794,8
|
30
|
8507,61
|
171,6
|
0,85
|
25
|
789
|
31
|
8734,62
|
176
|
0,85
|
24,9
|
783,6
|
32
|
8961,63
|
180,4
|
0,86
|
24,8
|
778,5
|
33
|
9188,63
|
184,8
|
0,86
|
24,7
|
773,7
|
34
|
9415,64
|
189,2
|
0,86
|
24,7
|
769,2
|
35
|
9642,64
|
193,6
|
0,87
|
24,6
|
764,9
|
36
|
9869,65
|
198
|
0,87
|
24,5
|
760,9
|
37
|
10096,7
|
202,4
|
0,87
|
24,5
|
757
|
38
|
10323,7
|
206,8
|
0,87
|
24,4
|
753,4
|
39
|
10550,7
|
211,2
|
0,88
|
24,4
|
749,9
|
40
|
10777,7
|
215,6
|
0,88
|
24,3
|
746,7
|
41
|
11004,7
|
220
|
0,88
|
24,2
|
743,5
|
|
|
|
|
|
45478
|
Потери мощности при частотном пуске
составляют
при прямом
пуске (как уже было рассчитано раннее ) ∆W1 = 1084 кДж
Рисунок 2.9. График зависимости
пускового тока от времени
Рисунок 2.10. График зависимости
частоты от времени пуска
Рисунок 2.11. График зависимости Мс
и Мд от времени при частотном пуске
2.4 Описание схем и выбор аппаратуры управления
.4.1 Выбор преобразователя
Способ регулирования скорости вращения двигателя
выбираем частотный, так как этот способ обеспечивает плавное регулирование
скорости в необходимом диапазоне, а получаемые характеристики обладают высокой
жесткостью. Определение напряжения и частоты необходимы для работы двигателя в
заданной точке, сводиться к уточнению возможности обеспечение преобразователя
уровня напряжения и частоты при различных нагрузках и колебаниях напряжения
питающей сети. При питании асинхронного двигателя от преобразователя частоты в
процессе преобразуется напряжение промышленной частоты. В напряжение
регулировки амплитуды и регулировки частоты возникают потери напряжения и
мощности преобразователя. Обычно преобразователь имеет внутреннее обратные
связи, и при изменении нагрузки двигателя выходное напряжение и частота
практически не изменяться. Поэтому в дальнейшем напряжение и частота на статоре
электродвигателя будем сочетать независимыми от нагрузки. Синхронная скорость
двигателя зависит от частоты питающей сети и числа пар полюсов.
(2.80)
Для устойчивой работы двигателя
необходимо изменение частоты поддерживать перегружавшую способность двигателя,
что обеспечиваться регулированием напряжения на статоре по различным законам.
Зависимость от частоты и от характера изменения статического момента. Эти
особенности необходимо учитывать при расчете частоты и амплитуды напряжения.
Наиболее распространенный закон изменения амплитуды напряжения пропорционально
частоте в виде закона: U/f=const, при таком законе максимальный момент
постоянен и не зависит от частоты.
Также не зависит от частоты:
(2.81)
Это позволяет в расчетах
использовать прием параллельного переноса естественной механической
характеристики. При этом естественная характеристика перемешаться вдоль оси «w»
и устанавливаться в т.Wзад, Mзад.
Из паспортных данных
преобразователей частоты следует, что:
(2.82)
Номинальный ток преобразователя
частоты должен быть не менее:
(2.83)
По IПЧ выбирается преобразователь
частоты c учетом требования тех. задания мощность преобразователя частоты
должна превышать мощность двигателя на 20%.
Тогда
(2.84)
Выбираем преобразователи частоты
серии Powtran серии PI7800. Его характеристики приведены в таблице 2.8, а
внешний вид представлен на рисунке 2.12.
Таблица 2.8
Характеристики частотного
преобразователя PI7800 015G3
Модель
|
Мощность,
КВт
|
Ток,
А
|
Масса
нетто, кг
|
Масса
брутто, кг
|
Габариты
|
Установочные
размеры
|
|
|
|
|
|
L/W/H,
мм
|
a/b/d,
мм
|
PI7800
015G3
|
15.0
|
32
|
10
|
12
|
360/235/207
|
340/150/Ш10
|
Рисунок 2.12 Внешний вид преобразователя частоты
PI7800 015G3
Проверочный расчет из условия, что
преобразователь частоты обеспечивает перегрузочный пусковой момент 136% от
номинального.
Мах. момент на валу двигателя
АИР160S6
(2.85)
где : Iном = 32 А - номинальный ток
преобразователя частоты; ном dv = 24,42 А - ном. ток двигателя
- условие выполняется
Окончательно выбираем
преобразователь015G3, P = 15 кВт, Iном = 32 А.
.4.2 Выбор аппаратуры управления
Наряду с аппаратами ручного
управления широкое применение получила релейно-контактная аппаратура,
позволяющая управлять электродвигателями и другими электроустановками
дистанционно, т. е. на расстоянии, с помощью кнопок управления. К этой
аппаратуре, прежде всего, относятся магнитные пускатели и контакторы.
В нашем случае применяется частотный
преобразователь PI7800 015G3, который может оснащаться как местным так и
дистанционным пультом управления. Пульт управления частотного преобразователя
PI7800 015G3 представлен на рисунке 2.13.
Пульт местного управления размещен
на лицевой панели блока. Он содержит кнопки управления и настройки параметров
работы, светодиоды для отображения режимов работы и пятиразрядный цифровой
индикатор.
Нажатие какой-либо кнопки на пульте,
если команда принята, отображается изменением состояния соответствующих
светодиодов, расположенных, как правило, рядом с кнопкой. Команды управления с
местного или удаленного пульта управления имеют следующее назначение:
Кнопкой САУ - выбор типа системы
управления. Разомкнутая САУ - без обратной связи. Замкнутая САУ - с обратной
связью (используется внутренний программный ПИ-регулятор технологической
переменной). Частотный преобразователь выполняет функцию локального автомата.
Рисунок 2.13. Пульт управления
частотного преобразователя PI7800 015G3
.4.3 Схема включения частотного
преобразователя
Схема включения частотного
преобразователя представлена на рисунке 2.14.
Автоматические выключатель - при
подаче напряжения на инвертор автоматический может защитить цепь
электроснабжения.
Реактор переменного тока -
применение реактора переменного тока способно погасить высшие гармоники в сети
на входе в преобразователь частоты и улучшить коэффициент реактивной мощности
преобразователя. Применение реактора переменного тока рекомендуется в следующих
случаях:
если мощность источника в 10 и более
раз превышает мощность инвертора.
если тиристорные переключатели и
компенсаторы реактивной мощности подключены к тому же источнику питания, что и
преобразователь частоты.
если существует большой дисбаланс
напряжения в фазах (более 3%).
Фильтр подавления помех - фильтр
используется для подавления электромагнитных помех, производимых конвертером и
препятствует их прохождению в сеть. При выборе электромагнитного фильтра
необходимо согласовать его тип с системой электроснабжения - 3-х фазная 3-х
проводная, 3-х фазная 4-х проводная или однофазная. Кабель заземления должен
быть как можно короче. Располагать фильтр необходимо как можно ближе к
преобразователю частоты.
Контактор - может использоваться в
качестве прерывателя подачи электропитания в целях защиты от распространения
аварии. Нельзя использовать контактор для включения и выключения двигателя.
Выходной электромагнитный фильтр -
фильтр ограничивает шум и утечки тока на выходе из прибора.
Выходной реактор переменного тока -
если протяженность линии между инвертором и двигателем более 20 м, реактор
может ограничить сверхтоки от инвертора и ёмкостные токи от протяжённых
проводов между инвертером и двигателем.
К пусковой низковольтной аппаратуре
относятся различные рубильники, переключатели, автоматические выключатели.
Номинальный ток рубильника должен быть не менее трехкратного номинального тока
электродвигателя:
Н.РУБ.= 3IНДВ (2.86)
где IНДВ - номинальный ток
электродвигателя (А).
При установке рубильников,
переключателей или пакетных выключателей, а также для разрыва цепи в случае
возникновения токов короткого замыкания применяют предохранители.
Автоматические выключатели служат
для автоматического размыкания перегруженных электрических цепей и в случае других
ненормальностей, а также для включений и отключений в нормальных условиях.
Рисунок 2.14. Схема включения PI7800
015G3
Выбор автомата защиты для
трехфазного асинхронного электродвигателя с короткозамкнутым ротором.
Каталожные данные двигателя
АИР160S6: Рн =11 кВт; IH = 24,4 А при Uн = 220 В; nн = 970 об/мин; КПД = 87,5%;
cos jH =0,74;
кратность пускового тока К1 =6,5;
Пусковой ток:
(2.87)
При использовании преобразователя
частоты максимальный ток при пуске электродвигателя по Таблице 2.6, Imax=53,5
А.
Определим ток уставки теплового
расцепителя:
Н.УСТ = 1,25*IН= 1,25*53,5 = 66,9 А.
(2.88)
Выберем автомат Iавт = 25 А и
установим ток теплового расцепителя регулятором на 80 А. Модель S203 B 25А
6000, Фирма производитель ABB.
Определим необходимый ток
электромагнитного расцепителя
эм расц= 1,25 * Imax = 1,25 *53,5
=66,9 А. (2.89)
Проверим выбранный автомат по току
срабатывания электромагнитного расцепителя.
По условиям пуска автомат выбран
правильно, поскольку
срэм.расц > Iэм.PАCЦ т.е. 80 >
66,9
Проверим коммутационную способность
автомата. Эффективное значение допустимого тока короткого замыкания для
выбранного автомата при напряжения 220 В (Iф кор зам =1500 А) должно быть
больше Iф кор зам сети.
Выбор защитного аппарата.
Для защиты проводов и кабелей
электрических сетей напряжением до 1000 В от токов короткого замыкания
устанавливают предохранители. Защитным элементом предохранителя является
плавкая вставка, включаемая последовательно в цепь тока. При увеличении тока
линии выше определенной величины плавкая вставка расплавляется, цепь тока
разрывается, предохраняя провод от недопустимого перегрева.
Расчетный ток линии равным
номинальному току двигателя: IДЛ =24,4 А. Выбрав номинальный ток плавкой
вставки по длительному току линии (IВ > Iдл), получим соотношение IВ >
24,4 А.
При выборе плавкой вставки по
пусковому току двигателя
Согласно требованиям выбираем
предохранитель ПР-2 220В 15-60А, с номинальным током срабатывания 60A.
Так как применяется частотный
преобразователь, проводку необходимо осуществлять экранированным кабелем марки
ПВВГЭ, проложенным в трубах и каналах пола.
Определим рабочий ток нагрузки:
(2.90)
Выбираем по каталогу ближайшие
сечение кабеля по длительно-допустимому току АПВВГЭ - 4х10.
.4.4 Структурная и функциональная
схема управлением электроприводом
Общая структура электропривода
представляется в виде схемы (рисунок 2.15).
Рисунок 2.15. Общая структура
электропривода
В общей структурной схеме
раскрываются входные и выходные переменные каждого звена системы
электропривода.
Частотный преобразователь можно
разделить на три основные части: неуправляемый выпрямитель, инвертор и систему
управления выпрямителем и инвертором.
Функциональная схема системы
автоматического управления электродвигателем АИР160S6 с частотным
преобразователем, приведена на рисунке 2.16.
В соответствии с функциональной
схемой в состав электропривода входят:
исполнительный двигатель (М) -
АИР160S6
статический преобразователь частоты
(СПЧ), состоящий из силовой части и системы управления статическим
преобразователем частоты (СУ СПЧ);
система управления электроприводом
(СУ ЭП).
В качестве исполнительного двигателя
в электроприводе используется асинхронный двигатель с короткозамкнутым ротором.
Силовая часть СПЧ включает в себя неуправляемый выпрямитель (НВ), автономный
инвертор напряжения с широтно-импульсной модуляцией (АИН ШИМ) и конденсатор в
звене постоянного тока С. Система управления статическим преобразователем
состоит из трех блоков:
блок БУ1, формирующий импульсы
управления полупроводниковыми ключами VS1-VS6, которые обеспечивают
синусоидальную широтно-импульсную модуляцию трехфазного выходного напряжения
статического преобразователя частоты при работе электропривода в двигательном
режиме;
блок БУ2, формирующий импульсы
управления полупроводниковыми ключами VS2, VS3, которые обеспечивают
широтно-импульсную модуляцию постоянного напряжения, прикладываемого к двум
последовательно соединенным фазам обмотки статора при возможной работе
электропривода в режиме динамического торможения;
коммутатор прохождения импульсов
управления K.
Система управления электроприводом
включает в себя следующие элементы и блоки:
Пульт управления (ПУ);
датчик скорости ДС;
пропорционально-интегральный
регулятор (ПИ);
два сумматора С1 и С2;
функциональный преобразователь (ФП);
задатчик интенсивности торможения
(ЗИТ);
блок вычисления синхронной частоты
вращения (БВ ω0).
Рисунок 2.16. Функциональная схема
частотно-регулируемого электропривода
При работе в двигательном режиме
электропривод представляет собой замкнутую систему автоматического
регулирования с обратной связью по частоте вращения. Требуемое значение частоты
вращения двигателя и пуск двигателя при частотном регулировании устанавливается
с помощью ПУ, сигнал с выхода которого поступает на положительный вход
сумматора С1. На отрицательный вход сумматора С1 поступает сигнал,
пропорциональный фактической частоте вращения двигателя. Разность сигналов,
снимаемая с выхода сумматора С1 поступает на вход пропорционально-интегрального
регулятора, который задает необходимую зависимость изменения частоты напряжения
и величины напряжения на выходе статического преобразователя частоты.
Функциональный преобразователь ФП выполняет необходимую связь между частотой
напряжения и действующим значением напряжения на выходе СПЧ. Эта связь
определяется законом скалярного управления Костенко, который для
электроприводов со статической нагрузкой имеет следующий вид
(2.91)
где U1 - величина действующего
значения фазного напряжения обмотки статора, f1 - частота тока статорной
обмотки.
.5 Индивидуальное задание. Закон
М.П. Костенко
Основной задачей частотного
управления является исследование работы АД при различных связях между каналами
управления напряжением и частотой питания статора, называемых законами
управления, а также определение законов, обеспечивающих оптимальные условия
работы двигателя в статических и переходных режимах.
В 1925 академик Костенко М.П.
сформулировал общий закон обеспечивающий оптимальные условия работы двигателя:
чтобы обеспечить оптимальный режим работы АД при всех значениях частоты и
нагрузки, необходимо относительное напряжение двигателя изменять
пропорционально произведению относительной частоты на корень квадратный из
относительного момента:
(2.92)
где
- относительный электромагнитный
момент. Если магнитная цепь машины слабо насыщена и активным сопротивлением
статора можно пренебречь, то АД в этом случае будет работать при практически
постоянном коэффициенте мощности, запасе статической устойчивости и абсолютном
скольжении.
Закон Костенко можно получить из
следующих элементарных соображений. Если предположить, что коэффициент
перегрузочной способности <#"554221.files/image234.gif"> (2.93)
Но если пренебречь активным
сопротивлением статора, то напряжение статора будет уравновешиваться ЭДС
основного магнитного потока и будет линейно связано с частотой и величиной
магнитного потока, а отношение напряжений равно
(2.94)
Подставляя (2) в (3), получим закон
Костенко
⟺
(2.95)
Для некоторых простейших случаев из
закона Костенко можно исключить относительный момент. Полагая с точностью до
скольжения ω1≈ω, представим
уравнение механической характеристики нагрузки степенной функцией M=Cωk или, в
относительный единицах, как µ=αk. Тогда выражение (2.92) примет вид γ=α1+k/2
Отсюда для типичных видов нагрузки
получим законы управления (таблица 2.9). Механические характеристики привода
ПЧ-АД при разных законах регулирования представлены на рисунке 2.17.
Таблица 2.9
Законы управления
|
Вид
нагрузки
|
|
Статическая
k=0 М=const;
|
Вентиляторная
M=Cω2,
k=2
|
Постоянная
мощность Mω=const; k=-1
|
Закон
управления
|
γ=α
|
γ=α2
|
γ=
|
Эти законы управления являются фактическим
стандартом, заложенным во все современные преобразователи частоты широкого
применения.
Закон Костенко можно рассматривать применительно
к разомкнутым и к замкнутым системам управления. Сущностью его является
управление напряжением (магнитным потоком) машины в функции нагрузки на валу
без непосредственного ее измерения. Если нагрузка уменьшается, то магнитный
поток можно также уменьшить, уменьшив напряжение, но сохранив при этом запас
статической устойчивости.
Выше было отмечено, что общее выражение закона
Костенко получено при условии r1≈0, что соответствует внутреннему
относительному напряжению
. Можно показать,
что такое управление, т.е. оптимальное управление с учетом активного
сопротивления статора реализуется при поддержании на постоянном близком к
номинальному скольжению уровне абсолютного скольжения βo≈sном=const.
Такое регулирование можно выполнить с помощью
обратной связи по скорости в соответствии с выражением ω=ω1ном(α-
βo).
а) при постоянном моменте; б) при постоянной
мощности; в) при вентиляторной нагрузке.
Рисунок 2.17. Механические характеристики
привода ПЧ-АД
Таким образом, для того, чтобы реализовать
принцип частотного управления асинхронным двигателем, необходимо в соответствии
с выражением (2.93) и с учетом вида нагрузки управлять напряжением, подводимым
к статору двигателя, взаимосвязано с изменением частоты питания.
Функцию преобразования параметров электрической
энергии питающей сети к таким значениям, которые необходимы для нормальной
работы приводного двигателя, а также функцию дозирования величины электрической
энергии, подводимой к двигателю для регулирования его скорости и выполняет преобразовательное
устройство.
В системах регулируемого электропривода находят
применение все основные типы преобразовательных устройств: выпрямители,
преобразующие переменное напряжение в постоянное; инверторы, осуществляющие
обратное выпрямителям преобразование энергии; непосредственные преобразователи
частоты; регуляторы переменного и постоянного напряжения, обеспечивающие
преобразование уровня напряжения без изменения его частоты.
3 Охрана труда и безопасность жизнедеятельности
.1 Безопасность жизнедеятельности
В настоящее время огромное значение имеет
проблема обеспечения здоровых и безопасных условий труда, этими и многими
другими вопросами занимаются специалисты по охране труда на производстве.
Охрана труда выявляет и изучает возможные причины производственных несчастных
случаев, профессиональных заболеваний, аварий, взрывов, пожаров и разрабатывает
систему мероприятий с целью устранения этих причин и создание безопасных и
благоприятных для человека условий труда.
Охрана труда - это система законодательных,
социально-экономических, организационных, технических, гигиенических и
лечебно-профилактических мероприятий и средств, обеспечивающих безопасность,
сохранение здоровья и работоспособности человека в процессе труда [28].
В нашей стране принимаются различные меры по
обеспечению безопасности человека в процессе производства. Основополагающими
документами в области охраны труда в нашей стране являются Конституция
Республики Казахстан, Закон «Об охране труда в Республике Казахстан», который
был принят 1 января 2000 года. Для усовершенствования законодательства был
введен в действие с 12 марта 2004 да Закон Республики Казахстан «О безопасности
и охране труда».
В области правового урегулирования охраны труда
наметились определенные и улучшения, связанные с наиболее четкой регламентацией
обязанностей работодателей по обеспечению здоровых и безопасных условий труда;
гарантиями прав работников на труд в условиях соответствующих требованиям
охраны труда; созданием системы органов государственного контроля и надзора за
соблюдением, трудового законодательства и иных нормативных правовых актов,
содержащих нормы трудового права; расширением прав профессиональных союзов в
указанной области.
.2 Производственная санитария и гигиена труда
В дипломной работе на тему «Разработка
электропривода сушильной установки растительного сырья АО «Шымкентмай»»
рассматривается производственная санитария и гигиена труда. Следует обратить
внимание на безопасность и экологичность технологического оборудования и
факторы, воздействующие на организм человека, возникшие в процессе эксплуатации
технологического оборудования, находящегося в рабочем помещении.
Общие санитарно-технические требования к
производственным помещениям, рабочим местам и зонам, а так же к микроклимату
изложены в санитарных нормах и правилах санитарных нормах проектирования
предприятия [29-31].
Важное значение для охраны труда работников
предприятий имеет правильная планировка и устройство выходов, проходов, лестниц
и площадок. Они должны отвечать строительным, эксплуатационным,
санитарно-техническим и противопожарным требованиям. Размеры площадки
определяются в соответствии со строительно-санитарными нормами с учетом
возможного расширения предприятия на перспективу. Площадка должна быть на
сухом, незатопленном месте с прямым солнечным освещением, естественным
проветриванием, иметь относительно ровную поверхность, располагаться вблизи
водоисточника с отводом сточных вод. Должны быть обеспеченны удобства подхода,
подъезда транспортных средств, соблюдены условия охраны труда и техники
безопасности, а также противопожарной защиты.
Шум, создаваемый технологическим оборудованием,
а также установками вентиляции или воздушного отопления принимаются по
допустимым уровням шума на рабочих местах.
Помещения с тепловыделениями (более 20
ккал/м3с), а также производства с большим выделением вредных газов, паров и
пыли следует располагать у наружных стен зданий. А в многоэтажных зданиях
размешать в верхних этажах и обеспечивать приточно-вытяжной вентилятор.
Отделка стен должна быть прочной, гигиеничной,
экономичной в эксплуатации и отвечать эстетическим требованиям.
Полы в производственных помещениях, следует
делать из материалов, обеспечивающих удобную очистку их и отвечающих
эксплуатационным требованиям данного производства.
Рациональное размещение технологического
оборудования внутри помещений имеет существенное значение как для организации
технологических процессов, повышения производительности труда, так и для его
охраны.