Проектирование участка по производству и механообработке дисков роторно-лопастной группы
Введение
Машиностроение - наиболее крупная комплексная
отрасль, определяющая уровень научно-технического прогресса во всем народном
хозяйстве, поскольку обеспечивает все отрасли машинами, оборудованием,
приборами, а население - предметами потребления. Включает также
металлообработку, ремонт машин и оборудования. Для нее особенно характерно
углубление специализации производства и расширение ее масштабов.
Одной из актуальных научных проблем является
разработка и развитие двигателя внутреннего сгорания (ДВС). Развитие и область
применения ДВС приобрели в настоящее время всеобъемлющий характер.
Многочисленные научные исследования и разработки превратили ДВС в сложнейшую и
в то же время надежную универсальную систему. В то же время опыт длительной
эксплуатации в составе транспортных средств выявили недостатки, которые
практически невозможно исключить путем модернизации конструкции двигателя не
затронув базовых принципов его организации.
В данном дипломном проекте разрабатывается
производство детали диск малый и диск большой роторно-лопастного двигателя с внешним
подводом теплоты (РЛДВПТ) мощностью 5-10 кВт.
В процессе выполнения работы в дипломе проводится
исследование и выбор материала, на
основе которых выбирается сталь 38Х2МЮА ГОСТ 4543-71.
Подбирается самый экономичный и наиболее
приближенный к форме детали вариант изготовления заготовки, рассчитываются припуски
и допуски.
Выбирается оборудование для быстрой и точной
обработки детали с наименьшим числом переустановов.
Подбирается инструмент для обработки детали,
разрабатывается маршрут обработки, на основе которого выполняется техпроцесс.
Проводиться расчет времени на обработку и подбираются режимы резания.
Планируется участок механообработки.
Рассчитывается высота и ширина участка механообработки. Количество станков
потребное для изготовления партии деталей. Потребное цеховое оборудование, транспорт для
перевозки деталей, тара.
Проводится расчет капитальных вложений и затрат
на производство дисков. Рассматривается техника безопасности и безопасность
изготовления детали.
Общая часть
деталь обработка резание припуск
Характеристика детали
Назначение и конструкция
детали
Диски в роторно-лопастной группе выполняют две
функции: передают крутящий момент от поршней к роторам, а также служат для
неподвижного крепления поршней.
Конструктивно диски представляют собой фланцы с
двумя отогнутыми кронштейнами (рис.1). Это сделано для того, чтобы центры поршней, насаженных на
разные диски, находились в одной плоскости. Угол наклона кронштейнов
определяется конструктивно, в зависимости от толщины дисков и размеров поршней. Поверхность
прилегания поршней к диску
выполняется тороидальной с целью совпадения с внутренней поверхностью рабочей
камеры.
Передача крутящего момента от диска к роторам
может осуществляться либо с помощью шлицевого, либо с помощью болтового
соединений. Выбор типа передачи крутящего момента определяется габаритными
размерами роторов и дисков.
Торовые поверхности дисков в процессе своей
работы
постоянно находятся под
воздействием высокой температуры (до 300°С) и изменяющегося давления в рабочей камере в
пределах от 2,5 атм. до 11 атм. Кроме того, кронштейны дисков находятся под воздействием сил
инерции от поршней. Это нужно учитывать при выборе материала и расчете
конструктивных элементов дисков.
Конструкторские расчеты
детали
Прежде чем разрабатывать технологический процесс
изготовления детали «диск» нужно рассчитать некоторые конструктивные элементы
данной детали, исходя из ее назначения, а именно:
ü выбрать нужный
материал дисков, исходя из условия их работы.
Выбор материала детали
Так как деталь работает при повышенной температуре (до 300° С), испытывает давление со стороны
рабочего тела (
, а также вращается с частотой до 
, необходим материал, который имеет достаточную твердость, пределы
прочности и текучести при данной температуре.
В качестве потенциального материала детали я предлагаю выбрать одну из
следующих сталей: 40ХНМ2А, 50ХФА, 60C2A.
Заготовка детали будет вырезаться из листа, значит те стали, которые не
имеют в своей поставке листового проката отсеем сразу. Все стали имеют в
поставке нужный прокат.
1. Рассмотрим рекомендации, какие изделия изготавливают из
данных сталей:
ü Сталь 40ХН2МА: Коленчатые валы, клапаны, шатуны, крышки шатунов, ответственные болты,
шестерни, кулачковые муфты, диски и другие тяжелонагруженные детали. Валки для
холодной прокатки металлов.
ü Сталь 50ХФА: тяжелонагруженные ответственные
детали, к которым предъявляются требования высокой усталостной прочности,
пружины, работающие при температуре до 300°С и другие детали.
ü Сталь 60С2А: тяжелонагруженные пружины, торсионные валы, пружинные кольца, цанги,
фрикционные диски, шайбы Гровера и др.
2. Деталь будет работать при повышенной температуре (300°С). Сделаем сводную таблицу механических свойств, при данной температуре:
Материал
|
σ0,2, МПа
|
σ B, МПа
|
σ 5,%
|
ш,%
|
KCU, Дж/м2
|
Сталь 40ХН2МА (Закалка 850 °С, масло.)
|
1470
|
1600
|
10
|
50
|
49
|
Сталь 50ХФА (Закалка 860 °С, масло. Отпуск 480
°С. При 20 °С HRCэ 42-44)
|
1180
|
1370
|
13
|
40
|
-
|
Сталь 60С2А (Закалка 860 °С, масло. Отпуск 425
°С)
|
1270
|
1570
|
20
|
58
|
43
|
Из данных таблицы и нижеизложенных исследований можно сделать вывод, что в
качестве материала детали наиболее подходит сталь марки
Сталь 60С2А.
Сталь 60С2А Общие сведения Заменитель стали: 60С2Н2А, 60С2Г, 50ХФА. Вид поставки Сортовой прокат, в том
числе фасонный: ГОСТ 14959-79, ГОСТ 2590-71, ГОСТ 2591-71, ГОСТ 2879-69, ГОСТ
7419.0-78 - ГОСТ 7419.8-78. Калиброванный пруток ГОСТ 7417-75, ГОСТ 8559-75,
ГОСТ 8560-78, ГОСТ 1051-73. Шлифованный пруток и серебрянка ГОСТ 14955-77,
ГОСТ 7419.0-78 - ГОСТ 7419.8-78. Лента ГОСТ 2283-79, ГСТ 21997-76. Полоса
ГОСТ 103-76, ГОСТ 4405-75. Проволока ГОСТ 14963-78. Поковки и кованые
зготовки ГОСТ 1133-71, ГОСТ 14595-79. Назначение тыжелонагруженные пружины, торсионные валы, пружинные
кольца, цанги, фрикционные дики, шайбы Гровера и др. Химический состав Химический элемент % Кремний (Si) 1.6-2.0 Медь (Cu), не более 0.20 Марганец (Mn) 0.60-0.90 Никель (Ni), не более 0.25 Фосфор (P), не более 0.025 Хром (Cr), не более 0.30 Сера (S), не более 0.025 Механические свойства
Механические свойства Термообработка, состояние поставки Сечене, мм σ0,2, МПа σB, МПа d5, % ψ, % KCU, Дж/м2
HB HRCэ Сталь категорий:
3,3А,3Б,3В,3Г,4,4А,4Б. Закалка 870 °С, масло, отпуск 420 °С. 135 1570 6
20 Изотермическая закалка 860-880 °С,
расплавленнаясоль 310-330 °С. Отпуск 310-330 °С, воздух. 10 1570 1770 12
50 62 47-50 Пружины. Навивка 850-950
°С. Закалка 850 -870 °С, масло. Отпуск 430-460 °С, воздух.
388477 Рессопы. Закалка 850-870 °С, масло.
Отпуск 400-450 °С, воздух. 387-418 Механические
свойства при повышенных температурах t испытания, °C 0,2, МПа B,
МПа 5, % , % KCU, Дж/м2 Пруток диаметром 17 мм. Закалка 860 °С, масло. Отпуск 550
°С, 3 ч. НВ 340-364 [179] 20 1090 1270 11-13 3
24 300 930 1220 15 44 43 400 820 950 19 7 44 500 510 590 23 87 43 Закалка 860 °С, масло.
Отпуск 425 °С [126] 20 1570 1710 10 46 32
200 1370 1670 13 40 34 300 1270 1570 20 58 400 1080 1220 22 71 Механические свойства в зависимости
от температуры отпуска t отпуска, °С 0,2, МПа B, МПа 5,
% , % KCU, Дж/м2 HB Закалка
850 °С, масло. Отпуск 300 1960 2160 2 36 10
462 400 1470 1670 7 9 18 425 500 1080 1290 10 42 29 340 600 73 1030 17 48 24 298 Технологические свойства
Температураковки Начала 1200, конца 800. Охлаждение
заготовок сечением до 250 мм на воздухе, 251-300 мм - в яме. Свариваемость не применяется для сварных
констркций. Обрабатываемость резанием В горячекатаном состоянии при НВ 270-320, B
= 1080 МПа K тв.спл. = 0,70, K б.ст. =
0,27. Склонность к отпускной способности не склонна Флокеночувствительность не чувствительна Ударная вязкость Ударная
вязкость, KCU, Дж/см2 Состояние поставки, термообработка +2 -70 Закалка 850 С, масло. Отпуск 460 С, 1 ч, воздух. 39 34 Предел выносливости -1, МПа n B,
МПа 0,2, МПа Термообработка, состояние стали 686 1Е+6 1680 Изотермическая закалка, выдержка при 330
С, 1 ч. Отпуск 30 С, 1 ч. 637 1Е+6 110 Закала.
Отпуск 420 С. 500 1900 1760 Закалка,
масло. Отпск 400 С. 421 1570 1370 Прокаливаемость Закалка 850 °С. Расстояние от торца, мм /
HRC э 1.5 3 4.5 6 9 12 15
18 7 39 60-67 59-67 57-66 54-65
44,5-63 38,5-60 35,5-5 34-52,5 30-43,5 27-39,5 Кол-во мартенсита, % Крит.диам. в воде, мм Крит.диам. в масле, мм Крит.
твердость, HRCэ 50 47-82 24-53 51-53 90 60 36 58-60 Физические свойства
Температура ипытания, °С 20 100 200 300 400 500 600 00 800 900 Модуль нормальной упругости, Е, ГПа 212 206 198 192
181 178 158 144 134 Модуль упругости при сдвиге
кручением G, ГПа 82 80 77 74 69 68 60 54 50 Плотность, pn, кг/см3 7680 7660 7630 7590 7570 7520 Коэффициент теплопровдности Вт/(м ·°С) 28 29 29 30 30
30 29 29 28 Температура испытания, °С
20- 100 20- 200 20- 300 20- 400 20- 500 20- 600 20- 700 20- 800 20-
900 20- 1000 Коэффициент линейного
рсширения (a, 10-6 1/°С) 11.8 12.7 13.3 13.7 4.1 14.5 14.4 12.2 Удельная теплоемкость (С, Дж/(кг · °С)) 510 510 520 535
565 585 620 700
|
Обоснование выбора материала
Одним из основных и главных моментов является
выбор материала. Неверный выбор материала может привести к преждевременному
изнашиванию или же к разрушению.
Для проверки материалов проводились исследования в программе SolidWorks 2009, где была создана модель детали
с приложением сил и закреплением.
Рис. 2 Схема приложения сил
Рис. 3 Эпюра напряжений.
Для изготовления детали «Диск» используется сталь 60С2А. Предел
текучести стали 60С2А у=1570 МПа, с учетом испытаний при температурах до 300°С, после
проведения анализа, выяснилось, что под действием нагрузок, максимальная
текучесть равна 557 МПа. Запас текучести более 500.
Рис. 4 Эпюра деформаций
Анализ напряжений показал, что эпюра выдерживает
приложенные нагрузки.
Рис. 5 Эпюра запаса прочности
Проведенные расчеты показывают, что минимальный
запас прочности равен 1,3.
Рис. 6 Эпюра перемещений
Перемещение диска под действием приложенных нагрузок, не выходит
за пределы допустимого.
Проведенный анализ позволил выявить годность
выбранного материла.
Недостатки данного материала:
´ Данному материалу необходима
термообработка
´ Необходимо шлифование внутренней
поверхности шлицев
Вследствие этого был найдено два варианта материала, годных к
использованию в данной детали:
ü Сталь 30ХЗМФ
ü Сталь 38Х2МЮА
Сталь 38Х2МЮА
Общие сведения
Заменитель
|
сталь 38Х2ЮА, 38ХВФЮ, 20Х3МВФ, 38Х2Ю.
|
Вид поставки
|
Сотовой прокат, в том числе фасонный: ГОСТ 4543-71,
ГОСТ 2590-71, ГОСТ 2591-71, ГОСТ 2879-69. Калиброванный пруток ГОСТ 7417-75,
ГОСТ 8559-75, ГОСТ 8560-78, ГОСТ 1051-73. Шлифованный пруток и серебрянка
ГОСТ 14955-77. Полоса ГОСТ 103-76. Поковки и кованые заготовки ГОСТ 1133-71.
|
Назначение
|
Штоки клапанов паровых турбин, работющие при
температуре до 450 °С, гильзы цилиндров двигателей внутреннего сгорания, иглы
форсунок, тарелки букс, распылители, пальцы, плунжеры, распределительные
валики, шестерни, валы, втулки и другие детали.
|
Химический состав
Химический элемент
|
%
|
Кремний (Si)
|
0.20-0.45
|
Медь (Cu), не более
|
0.30
|
Молибден (Mo)
|
0.15-0.25
|
Марганец (Mn)
|
0.30-0.60
|
Никель (Ni), не более
|
0.30
|
Фосфор (P), не более
|
0.025
|
Хром (Cr)
|
1.35-1.65
|
Аллюминий (Al)
|
0.70-1.10
|
Сера (S), не более
|
0.025
|
Механические свойства
Сечение, мм
|
0,2, МПа
|
B, МПа
|
5, %
|
, %
|
KCU, Дж/м2
|
HB
|
|
Пруток. Закалка 940 °С, вода или масло. Отпуск 640
°С, вода или масло.
|
30
|
835
|
980
|
14
|
50
|
88
|
|
|
|
|
|
|
|
|
|
Поковки. Закалка. Отпуск.
|
100-300
|
590
|
735
|
13
|
40
|
49
|
235-277
|
|
|
|
|
|
|
|
|
Закалка 930-950 °С, масло или вода. Отпуск 640-680
°С, воздух.
|
60
|
880
|
1030
|
18
|
52
|
|
250-300
|
|
|
|
|
|
|
|
|
100
|
730
|
880
|
10
|
45
|
59
|
|
|
|
|
|
|
|
|
|
200
|
590
|
780
|
10
|
45
|
59
|
|
|
|
|
|
|
|
|
|
Закалка 950 °С, масло. Отпуск 550 °С, масло.
|
120
|
780-880
|
930-1030
|
12-15
|
35-45
|
69-98
|
285-302
|
|
|
|
|
|
|
|
|
Механические свойства при повышенных температурах
t испытания, °C
|
0,2, МПа
|
B, МПа
|
5, %
|
, %
|
KCU, Дж/м2
|
|
Пруток. Закалка 930-940 °С,масло. Отпуск 660 °С, 5
часов отпуска. НВ>=255 [77]
|
20
|
650
|
800
|
17
|
64
|
157
|
|
|
|
|
|
|
|
|
|
200
|
580
|
780
|
17
|
56
|
152
|
|
|
|
|
|
|
|
|
|
300
|
570
|
810
|
18
|
58
|
127
|
|
|
|
|
|
|
|
|
|
400
|
550
|
720
|
20
|
63
|
127
|
|
|
|
|
|
|
|
|
|
500
|
420
|
470
|
25
|
81
|
98
|
|
|
|
|
|
|
|
|
|
600
|
270
|
300
|
26
|
89
|
98
|
|
|
|
|
|
|
|
|
|
Образец диаметром 10 мм, длиной 50 мм, прокатанный и
отожженный. Скорость деформирования 20 мм/мин. Скорость деформации 0,007 1/с.
|
800
|
98
|
110
|
66
|
95
|
|
|
|
|
|
|
|
|
|
|
900
|
66
|
84
|
57
|
97
|
|
|
|
|
|
|
|
|
|
|
1000
|
39
|
49
|
66
|
98
|
|
|
|
|
|
|
|
|
|
|
1100
|
22
|
32
|
77
|
100
|
|
|
|
|
|
|
|
|
|
|
1200
|
15
|
22
|
77
|
100
|
|
|
|
|
|
|
|
|
|
|
Механические свойства в зависимости от температуры отпуска
t отпуска, °С
|
0,2, МПа
|
B, МПа
|
5, %
|
, %
|
KCU, Дж/м2
|
HB
|
|
Закалка 900 °С, масло.
|
300
|
1660
|
1810
|
8
|
43
|
39
|
550
|
|
|
|
|
|
|
|
|
400
|
1520
|
1670
|
10
|
39
|
10
|
500
|
|
|
|
|
|
|
|
|
500
|
1270
|
1420
|
10
|
44
|
29
|
450
|
|
|
|
|
|
|
|
|
600
|
1080
|
1180
|
12
|
60
|
78
|
370
|
|
|
|
|
|
|
|
|
Механические свойства в зависимости от сечения
Термообработка, состояние поставки
|
Сечение, мм
|
0,2, МПа
|
B, МПа
|
5, %
|
, %
|
KCU, Дж/м2
|
HB
|
|
Закалка 930-950 °С, масло или вода. Отпуск 640-680
°С, воздух. [81]
|
|
60
|
880
|
1030
|
18
|
52
|
|
250-300
|
|
|
|
|
|
|
|
|
100
|
730
|
880
|
10
|
45
|
59
|
|
|
|
|
|
|
|
|
|
200
|
590
|
780
|
10
|
45
|
59
|
|
|
|
|
|
|
|
|
Закалка 940 °С, масло. Отпуск 600 °С. [130]
|
Место вырезки образца - центр
|
30
|
780
|
910
|
17
|
52
|
115
|
|
|
|
|
|
|
|
|
Закалка 940 °С, через воду в масло. Отпуск 600 °С.
[130]
|
Место вырезки образца - центр
|
50
|
830
|
950
|
16
|
50
|
102
|
|
|
|
|
|
|
|
|
Место вырезки образца - центр
|
80
|
830
|
940
|
15
|
50
|
48
|
|
|
|
|
|
|
|
|
Место вырезки образца - центр
|
140
|
780
|
920
|
15
|
48
|
41
|
|
|
|
|
|
|
|
|
Место вырезки образца - центр
|
180
|
710
|
860
|
15
|
47
|
36
|
|
|
|
|
|
|
|
|
Место вырезки образца - край
|
180
|
930
|
14
|
48
|
39
|
|
|
|
|
|
|
|
|
Место вырезки образца - центр
|
220
|
730
|
880
|
15
|
43
|
35
|
|
|
|
|
|
|
|
|
Место вырезки образца - край
|
220
|
800
|
930
|
16
|
43
|
34
|
|
|
|
|
|
|
|
|
Механические свойства при 20 С
Термообработка, состояние поставки
|
0,2, МПа
|
B, МПа
|
5, %
|
, %
|
KCU, Дж/м2
|
|
Закалка 930-940 °С, масло. Отпуск 660 °С.
|
Тепловая выдержка 500 °С 5000 ч.
|
640
|
800
|
20
|
60
|
152
|
|
|
|
|
|
|
|
|
|
Тепловая выдержка 550 °С 5000 ч.
|
550
|
710
|
23
|
63
|
171
|
|
|
|
|
|
|
|
|
|
Технологические свойства
Температура ковки
|
Начала 1240, конца 800. Сечения до 50 мм охлаждаются
в штабелях на воздухе, 51-100 мм - в ящиках.
|
Свариваемость
|
не применяется для сварных конструкций.
|
Обрабатываемость резанием
|
В закаленном и отпущенном состоянии при НВ 240-277 B = 780 МПа K тв.спл. = 0.75, K б.ст. = 0.55.
|
Склонность к отпускной способности
|
не склонна [82]
|
Флокеночувствительность
|
чувствительна
|
Температура критических точек
Критическая точка
|
°С
|
Ac1
|
800
|
Ac3
|
865
|
Ar3
|
740
|
Ar1
|
665
|
Mn
|
330
|
Твердость
Состояние поставки, режим термообработки
|
НВ
|
HV
|
Закалка 930-950 С, масло или вода. Отпуск 640-680 С,
воздух. Азотирование 520-540 С с печью до 100 С.
|
269-300
|
850-1050
|
Предел выносливости
-1, МПа
|
n
|
B, МПа
|
0,2, МПа
|
Термообработка, состояние стали
|
392-480
|
1Е+7
|
810
|
650
|
Закалка 940 С, масло. Отпуск 660 С, 5 ч, воздух. НВ
255
|
608-617
|
|
|
|
Закалка 940 С, масло. Азотирование 500 С, 48 ч [81]
|
Прокаливаемость
Закалка 870 °С.
Расстояние от торца, мм / HRC э
|
1.3
|
3
|
6
|
9
|
12
|
18
|
24
|
30
|
36
|
42
|
|
|
52.0
|
52.0
|
51.5
|
49.5
|
48.5
|
45.5
|
44.0
|
43.5
|
43.5
|
42.5
|
|
|
Крит.диам. в воде, мм
|
Крит.диам. в масле, мм
|
70
|
45
|
Физические свойства
Температура испытания, °С
|
20
|
100
|
200
|
300
|
400
|
500
|
600
|
700
|
800
|
900
|
Модуль нормальной упругости, Е, ГПа
|
209
|
202
|
194
|
190
|
181
|
174
|
162
|
147
|
137
|
|
Модуль упругости при сдвиге кручением G, ГПа
|
82
|
79
|
76
|
75
|
71
|
67
|
62
|
57
|
53
|
|
Коэффициент теплопроводности Вт/(м ·°С)
|
33
|
33
|
32
|
31
|
20
|
20
|
28
|
27
|
27
|
|
Температура испытания, °С
|
20- 100
|
20- 200
|
20- 300
|
20- 400
|
20- 500
|
20- 600
|
20- 700
|
20- 800
|
20- 900
|
20- 1000
|
Коэффициент линейного расширения (a, 10-6 1/°С)
|
11.5
|
11.8
|
12.7
|
13.4
|
13.9
|
14.7
|
14.9
|
12.3
|
|
|
Удельная теплоемкость (С, Дж/(кг · °С))
|
496
|
517
|
533
|
546
|
575
|
609
|
638
|
676
|
|
|
Для данных сталей необходима специальная термообработка -
низкотемпературное азотирование при 500°C.
Исследования детали с нагрузками при данных сталях выявлены в
следующих эпюрах:
Cталь 38Х2МЮА
Рис. 7 Эпюра напряжений.
Предел текучести стали 38Х2МЮА у=665 МПа, с учетом испытаний при
температурах до 300°С, после проведения анализа, выяснилось, что под действием
нагрузок, максимальная текучесть равна 532 МПа. Запас текучести более 100.
Рис. 8 Эпюра деформаций
Анализ напряжений показал, что эпюра выдерживает
приложенные нагрузки.
Рис. 9 Эпюра запаса прочности
Проведенные расчеты показывают, что минимальный
запас прочности равен 1,1.
Рис. 10 Эпюра перемещений
Перемещение диска под действием приложенных нагрузок, не выходит
за пределы допустимого.
Проведенный анализ позволил выявить годность
выбранного материла.
Анализ точности изготовления детали и обоснование
технического требования
Так как шероховатость всех неуказанных поверхностей 
, то все поверхности у заготовки обрабатываются.
Торовая поверхность диска имеет шероховатость Ra = 0,63, ее можно получить с помощью
специального фасонного инструмента, путем тонкого фрезерования, что увеличивает
стоимость механической обработки.
В двух дисках имеются разные шлицевые отверстия, значит
требуются и разные протяжки. Это также ведет к удорожанию изготовления детали.
Поверхность кронштейнов, к которой крепятся поршни имеет шероховатость 
. Эти поверхности можно получить тонким фрезерованием.
Жесткие допуски на размеры требуют точно настроенного
оборудования и точной технологической оснастки - толщина диска 
мм.
Большое количество обрабатываемых поверхностей приводит к
большому количеству операций.
Так как данная деталь является ответственной, на неё
задаются допуски по форме и расположению поверхностей: допуск
перпендикулярности плоскостей диска относительно центральной оси - 0,01 мм;
допуск плоскостности поверхностей диска - 0,01 мм на всей длине; допуск
перпендикулярности поверхностей крепления поршней
относительно центральной оси - 0,01 мм; допуск перпендикулярности оси отверстий
для крепления поршней, относительно соответствующих
поверхностей кронштейнов - 0,01 мм.
Данная деталь имеет термическую
обработку, это не позволяет увеличить количество выпускаемых деталей за
плановый период.
Для снижения стоимости изготовления деталей введем понятие
«селективная сборка»
Селективная сборка - метод сборки машин и механизмов, при котором осуществляют
соответствующий подбор попарно работающих деталей. Поступающие на сборку детали
сортируют по размерным группам, внутри которыхрых сопрягаемые детали (охватываемая и
охватывающая) имеют наиболее благоприятные для соединения фактич. размеры (с
наиболее близкими полями допусков). Селективная сборка позволяет снизить стоимость изготовления деталей
благодаря расширению пределов допуска размера партии сопрягаемых деталей.
Соответственно увеличим общий допуск до 0,1мм и разобьем его
на 6 групп.
Внутри каждой группы детали будут иметь наиболее близкие поля
допусков размеров, что означает благоприятные для соединения размеры.
В каждой группе будем контролировать точность изготовления 2
параметров:
· Точность изготовления торовой поверхности обоих дисков, для
совпадения с поверхностью поршней 
(рис. 11)
· Точность изготовления отверстий для закрепления поршней 
(рис. 12)
Рис. 11 Точность изготовления торовой поверхности

Рис. 12 Точность изготовления отверстий для закрепления
поршней
Анализ технологичности
конструкции детали
В комплексе требований,
предъявляемых к технико-экономическим показателям изделий, важное место
занимают вопросы технологичности конструкций. Обеспечение технологичности
конструкций изделий является одной из задач технологической подготовки
производства.
Технологичность
конструкции изделия определена по ГОСТ 14.205-83 как совокупность свойств конструкции
изделия, определяющих ее приспособленность к достижению оптимальных затрат на
производстве, эксплуатации и ремонте для заданных показателей качеста, объема
выпуска и условий вполнения работ.
Рассмотрим
технологичность детали «диск»:
° Форма детали представляет
собой диск с тороидальной торцовой поверхностью, выступающими двумя
кронштейнами затрудняющими обработку торца диска в местах их соединения.
° Кронштейны имеют
поверхности под разными углами, не образующие единую плоскость.
° В центре диска расположено
шлицевое отверстие, но так как в каждом модуле двигателя имеется два диска,
шлицевые отверстия у них разные.
° Наличие резьбовых
отверстий для крепления лопаток находятся на одной линии с торцом диска.
° Толщина диска невелика,
вследствие чего при обработке могут возникать вибрации.
° При обработке кронштейнов
они могут отгибаться и возникать вибрации нужно предупредить это явление.
Исходя из этих данных, делаем вывод, о том что,
деталь «диск» является нетехнологичной. Вследствие того, что деталь конструктивно
изменять нельзя, мы снизим стоимость изготовления, применяя метод селективной
сборки.
Определение типа
производства
Масса детали, кг.
|
Тип производства
|
|
Единичное
|
Мелкосерийное
|
Среднесерийное
|
Крупносерийное
|
Массовое
|
До 1.0
|
До 10
|
10-2000
|
1500-100000
|
75000-200000
|
>200000
|
1.0-2.5
|
До 10
|
10-1000
|
1000-50000
|
50000-100000
|
>100000
|
2.5-5.0
|
До 10
|
10-500
|
500-35000
|
35000-75000
|
>75000
|
5.0-10
|
До 10
|
10-300
|
300-25000
|
25000-50000
|
>50000
|
Свыше 10
|
До 10
|
10-200
|
200-10000
|
10000-25000
|
>25000
|
На данном этапе проектирования тип производства
определяется приблизительно по годовой программе выпуска и массе.
Годовая программа выпуска двигателей 10000 шт. Так как в одном модуле двигателя 2 диска, а
двигатель двухмодульный, то суммарная годовая программа, составляет 
Масса одного диска составляет ≈1 кг. Из
этих данных определяем, что тип производства - среднесерийное. [3]
Расчет размера партии и
такта выпуска
Количество деталей в партии определяется по
формуле:

,
где 
- объем выпуска деталей в год,

- периодичность запуска
в днях,

-
Число рабочих дней в году.
Отсюда находим:
Тогда примем объем партии равным: 
деталей.
Такт выпуска определяется по формуле:

,
где F - фонд времени в планируемый
период в часах,
N - объем выпуска деталей в год.
Расчет количества станков производиться по
формуле:

,
где Тшт - штучное время
tв - такт выпуска
Технологическая часть
проектирование
исходной заготовки
Выбор метода получения заготовки
Заготовку для данной детали можно получить из
листового проката либо штамповать на КГШП, либо получить заготовку литьем. Выберем получение из
проката. Выбор способа можно объяснить следующими факторами:
´ Выбранный материал не относится к литейным
сталям
´ Штамповкой
получить заготовку возможно, но ввиду тонкого сечения диска - 10 мм заготовку
будет коробить и останутся большие внутренние напряжения.
´ Прокат может
применяться в качестве заготовки для непосредственного изготовления деталей
либо в качестве исходной заготовки при пластическом деформировании.
´ Прокат
применяется в условиях массового или крупносерийного производства, что в
значительной степени снижает припуски и объем механической обработки.
Заготовку можно получить вырезкой гидроабразивным
методом, а затем согнуть на прессе, чтобы получить заготовку максимально
приближенную по форме к готовой детали.
Из-за появлений напряжений после операции сгибания необходима
нормализация.
Таким же способом можно вырезать заготовку при
помощи плазменной резки, но, в этом случае нужен больший припуск на
механическую обработку для удаления оплавленного металла после резки, что
приводит к увеличению времени обработки резанием.
Кроме того гидроабразивная вырезка позволяет
получить достаточно чистые поверхности у заготовки без заусенцев с
минимальными припусками.
Поэтому, делаем вывод, что наиболее благоприятный
вариант получения заготовки будет гидроабразивная вырезка из листового
проката толщиной 25 мм по ГОСТ 19903 - 74.
Экономическую целесообразность выбора рассмотрим
в следующем разделе.
Расчет себестоимости
изготовления заготовки
Расчет себестоимости будем производить по 2 вариантам:
) При вырезке с помощью гидроабразивной установки из
листового проката толщиной 25 мм по ГОСТ 19903 - 74. [4]
где: 
- стоимость материала

- стоимость операций правки и разрезки

где: 
- масса
заготовки (
)

- цена
одного килограмма материала заготовки (Сталь 38Х2МЮА - 56,9 руб.) [5]

- масса готовой детали (
)

- стоимость
отходов (6500 руб./т) [6]
где: 
приведённые затраты на рабочем месте,

- штучное или штучно-калькуляционное время выполнения
заготовительной операции.

коэффициент
выполнения норм
где: 
- нормативный коэффициент экономической эффективности капитальных
вложений;

- основная и дополнительная зарплата
с начислениями,
где:
коэффициент, учитывающий дополнительную зарплату, начисления на
социальное страхование и приработок к основной зарплате в результате
перевыполнения норм (
);

- часовая тарифная ставка
станочника-сдельщика соответствующего разряда, руб./час;

,
где 
средняя заработная плата станочника-сдельщика, (40000руб.);

кол-во часов работы в месяц, (176 ч.);

,

- коэффициент, учитывающий зарплату
наладчика;
- коэффициент, учитывающий оплату
рабочего при многостаночном обслуживании

где: 
коэффициент, показывающий, во сколько раз затраты, связанные с
работой данного станка, больше, чем у аналогичные расходы у базового станка (1,3) [ссылка] ; 
практические часовые затраты на базовом рабочем месте;

удельные часовые капитальные вложения в станок, руб./час;

,
где: 
балансовая стоимость станка (16 000 000 руб.);

годовой фонд времени работы станка (
;

коэффициент загрузки станка (при серийном производстве - 0,8) [ссылка]

;

удельные часовые капитальные вложения в здание, руб./час.

,
где: 
производственная площадь, занимаемая станком с учетом проходов,

,

площадь станка в плане (
);

коэффициент, учитывающий дополнительную производственную площадь
проездов, проходов и др. (в зависимости от площади станка - 2);

годовой фонд времени работы станка (
; 
коэффициент загрузки станка (при серийном производстве - 0,8) [ссылка]

;

- штучно-калькуляционное время (мин)
где 
- подача
при обработке, в мм/мин. (85
мм/мин)
Рис. 13 Длина обрабатываемого контура

- длина вырезаемого контура (1160мм.);
Таким образом, стоимость заготовки будет равна:
Технологическая себестоимость получения одной
заготовки при гидрообразивной резке с учетом затрат на сопла:
Время работы сопла - 240 часов; стоимость
одного сопла - 1000 € = 40000 руб.
Расчитаем стоимость работы сопла при вырезе одной детали:240 час. - 40000 руб.
0,23 час. 
руб.
1) Число заготовок, получаемых с учетом полного износа сопла:
2) Количество сопел, нужное для получения 20000 шт.
В итоге необходимо
20 сопел.
Общая технологическая себестоимость получения одной
заготовки из листового проката при гидрообразивной резке:
Вывод: Общая
стоимость изготовления заготовки из листового проката при гидроабразивной резке
- 568,67 руб. с учетом затрат на сопла
Разработка схем
базирования и закрепления заготовки по операциям
Исходя из анализа
точности и технологичности разделов 1.1.5-1.1.6 предлагаются следующие схемы
базирования по операциям.
Операция 015 1 установ.
Базирование осуществляется в трехкулачковом
самоцентрирующемся патроне, с дополнительными опорами, что позволяет обработать торец и расточить центральное отверстие. Трехкулачковый
самоцентрирующийся патрон обеспечивает достаточную точность для перечисленных
выше обработок.
Рис. 14 Базирование на 1 установе
При такой схеме базирования получаемые поверхности для
базирования во втором установе не имеют радиальных и торцевых биений друг
относительно друга.
Операция 015, 2 установ.
Базирование осуществляется по уже обработанной
поверхности
на первом установе. Обрабатываемый торец диска будет параллелен базовому.
Погрешность базирования на выдерживаемый размер при этом способе зависит от оснастки
станка.
Необходимо учесть, что понадобятся кулачки меньшего размера,
для обработки фаски центрального отверстия.
Рис.15 Базирование на 2 установе
Данная схема базирования позволяет согласно требованиям
чертежа добиться требований по взаимному расположению поверхностей:
ª допуск
перпендикулярности плоскостей диска относительно центральной оси - 0,01 мм;
ª допуск
плоскостности поверхностей диска - 0,01 мм на всей длине;
ª допуск
перпендикулярности поверхностей крепления поршней относительно центральной оси - 0,01 мм;
ª допуск
перпендикулярности оси отверстий для крепления поршней, относительно
соответствующих поверхностей кронштейнов - 0,01 мм.
Операция 020
Вертикальное протягивание исключает погрешность
обработки отклонением протяжки от оси отверстия под действием силы тяжести. Ось
отверстия совмещается с осью протяжки заходным конусом.
В данном установе важна ориентация детали, поэтому добавим
дополнительную ориентацию к базированию:
Рис. 16 Базирование на протягивании
Так как для изготовления детали диск используется
многооперационный станок, позволяющий проводить фрезерные операции не снимая деталь,
использование фрезерного станка не целесообразно и вносит лишние затраты на
оборудование. Так же т.к. данный станок высокоточный и позволяет обработать отверстия с
требуемой точностью, можно обойтись без использования сверлильного станка.
Оборудование [5]
Токарные и фрезерные обработки - выбираем центр обрабатывающий
токарно-фрезерный GMX 200 S Linear. [20]
Многооперационные токарные станки позволяют:
снизить количество операций;
сократить время обработки за счет быстрой смены
инструмента;
повысить точность обработки поверхностей;
увеличить производительность труда;
увеличение срока службы;
повышение эффективности за счет исключения
человека из производственного процесса;
улучшение условий труда, освобождение человека от
тяжелых условий труда;
обеспечение ритма работы.
Рис.17 Центр обрабатывающий токарно-фрезерный GMX 200 S
linear
200 S linear располагает всеми основными
моментами, присущими токарно-фрезерным центрам. Неоспоримым преимуществом здесь
служит впервые проведенная адаптация новой системы управления Siemens
SolutionLine-Steuerung с встроенной системой программирования ShopTurn-Programmiersystem.
GMX 200 S linear открывает область подготовки управляющих программ у
действующего оборудования с графической поддержкой для токарно-фрезерных
центров. Чтобы программировать также просто и надежно на универсальном станке,
как и на токарно-фрезерном центре, имеется упрощенный выбор требуемых циклов,
включая 3-D симуляцию заготовки всех токарно-фрезерных операций вплоть до
В-осевого контура. Т.о. оператору легче и быстрее получить готовую деталь. Не
последнюю роль в новом GMX 200 S linear играет ShopTurn feature, делая его
высокопроизводительным в среднесерийном производстве, а также гибким и
универсальным центром от мелкосерийного до единичного производства, где
комплектность заготовок неограниченна.
Оснащение новым дисковым магазином на 36 инструментов
и эргономичной фронтальной загрузкой инструментов, а также защищённой сменой
инструментов.
Будь то токарная обработка, сверление или
фрезерование деталей типа втулок, прутка и валов с новым GMX 200 linear серия
GMX linear уже хорошо оснащена для больших заданий по обработке. Линейный
привод, крестовидные салазки с осями Y и B и высокодинамичный токарный и
фрезерный шпиндель с 100 Нм и макс. 12.000 об/мин комбинируют характеристики
Highend-токарного станка с силой высокотехнологичного обрабатывающего центра.
Число оборотов и синхронная по углам передача инструмента, а также
интегрированные шпиндельные моторы гарантируют как при версии с контршпинделем
так и с задней бабкой кратчайшие процессы.
Благодаря большому запасу инструментов и
возможности наладки параллельно основному времени, возможно, экономичное
производство малых партий. Новый станок GMX 200 linear расширяет серию
токарно-фрезерных центров GILDEMEISTER в зоне с диаметром до 560 мм и
превращает эту серию в обширнейшую программу 6-сторонней полной обработки с
линейной технологией.
Использование обрабатывающих центров GMX 200 S Linear позволяет
снизить количество используемых станков, сократить время обработки, а так же
добиваться высокой точности обработки.
Гидроабразивная установка - Системы водоструйной резки фирмы
"Water Jet Sweden AB"
Под гидроабразивной резкой
<#"519967.files/image102.gif">
Рис.19 Скорость резания некоторых материалов.
Производство станков находится в новых фабричных
помещениях в Роннеби, Швеция, где выполняется окончательная сборка и
тестирование оборудования перед поставкой, а также проводится обучение
персонала заказчика. Установка оборудования на заводе клиента и продолжение
обучения специалистов клиента осуществляются высококвалифицированным
персоналом.
Официальным представителем фирмы Water Jet
Sweden в России является компания Росмарк-Сталь, осуществляющая весь
комплекс сервисного обслуживания, поставку запасных частей и расходных
материалов непосредственно со склада в Санкт-Петербурге.
Для протягивания шлицев - Полуавтомат протяжной вертикальный для внутреннего
протягивания 7Б64
Для обработки протягиванием сквозных отверстий различной
конфигурации: круглых, шлицевых, прямоугольных со шпоночными пазами.
Параметры
|
7Б64
|
Номинальная тяговая сила, кН
|
50
|
стола
|
320
|
салазок
|
-
|
Расстояние от салазок до оси отверстия в столе
|
150
|
Расстояние от поверхности салазок до торца стола
|
-
|
Наибольшая длина хода салазок
|
1000
|
Скорость рабочего хода протяжки, м/мин
|
1,5-11,5
|
Рекомендуемая скорость обратного хода протяжки, м/мин
|
20
|
Мощность электродвигателя привода главного движения, кВт
|
11
|
длина
|
2875
|
ширина
|
1350
|
высота
|
3640
|
Масса, кг
|
5050
|
Для низкотемпературного азотирования - Шахтная печь для каталитического газового
азотирования
Конструкция шахтной печи: Процесс азотирования в
электропечи осуществляется в сварной жаропрочной герметичной реторте,
подвешенной внутри печи. Футеровка печи выполнена из волокнистой
теплоизоляции фирмы Unifrax. Сверху реторта закрывается с помощью
гидропривода футерованной крышкой. Герметичность перекрытия реторты крышкой
обеспечивается двумя уплотнительными шнурами. В крышке предусмотрены:
Патрубки для выхода газа в свечу и для подачи технологических газов
Кислородный датчик Каталитический элемент «Oxycan-α».
На крышке
установлен вентилятор, обеспечивающий перемешивание атмосферы внутри реторты.
Нагревательные элементы зигзагообразного типа из проволоки «Kanthal».
Механизм подъема крышки гидравлический. Комплект поставки включает: 1. Печь азотирования шахтного
или камерного типа 2. Шкаф управления 3. Система охлаждения садки. 4.
Система нейтрализации отработавших газов 5. Система подачи технологических
газов 6. Отладка технологии азотирования деталей заказчика на поставляемом
оборудовании в соответствии с согласованным техническим заданием.
|
Наименование
|
Размеры рабочей камеры (диаметр и высота) мм, не
менее
|
Внешние размеры, мм, длина-ширина- высота, не более
|
Предел рабочей температуры
|
Количество зон нагрева
|
Установленная мощность, кВт, (не более)
|
США 10.15/7
<#"519967.files/image103.gif"> Сверло CoroDrill CoroDrill® Delta-C 2 − 3 x Dc
Концевая
фреза CoroMill Plura
Сверло CoroDrill Delta-C R841-0675-30-A1A 1220
2. Для чистовой обработки:
Резец
токарный проходной CoroTurn RC SNMG 12 04 08-PR
Концевая фреза CoroMill Plura
Концевая
фреза CoroMill Plura
Резьбофреза CoroMill
Plura
Разработка
технологического процесса изготовления детали
Назначение маршрута
обработки отдельных поверхностей
Для того чтобы назначить маршрут обработки
отдельной поверхности воспользуемся таблицами средне-экономической точности
обработки. Одна и та же поверхность может иметь несколько вариантов обработки.
Средне-экономическая точность это точность, обеспечивающая на станке нормальной точности рабочим средней
квалификации на средних режимах.
Рис.22 Обрабатываемые
поверхности детали
По требованиям точности для поверхностей
назначаем маршруты обработки и заносим все данные в таблицу 1.
Таблица 1. Назначение маршрута обработки
отдельных поверхностей детали
Поверхность
|
квалитет
|
Ra
|
Маршрут обработки
|
|
-
|
0,32
|
Двукратное точение + однократное шлифование
|
|
-
|
0,63
|
Двукратное фрезерование
|
|
Н14
|
6,3
|
Однократное фрезерование
|
|
hl4
|
6,3
|
Однократное фрезерование
|
|
IT 14/2
|
6,3
|
Однократное растачивание
|
|
-
|
6,3
|
Однократное фрезерование
|
|
Н12
|
6,3
|
Центровочное сверление + однократное сверление
|
|
Н10
|
6,3
|
Гидроабразивная резка + однократное растачивание
|
Маршрут обработки
№
|
Оборудование
|
Базирование
|
005
|
Системы водоструйной резки фирмы "Water Jet Sweden
AB" NC 2560 S
|
По плоскости стола
|
010
|
Пресс
|
По плоскости стола
|
015
|
Печь
|
|
020
|
Центр обрабатывающий токарно-фрезерный GMX 200 S Linear
|
В 3-х кулачковом самоцентрирующемся патроне
сдополнительными опорами
|
025
|
Полуавтомат протяжной вертикальный для внутреннего
протягивания 7Б64
|
По оси отверстия и упором в кронштейн
|
030
|
Шахтная печь для каталитического газового азотирования США
10.15/7
|
Приспособление при оборудовании
|
035
|
Моечная
|
Приспособление при оборудовании
|
040
|
Контрольная
|
|
Технологический процесс
Так как данная деталь имеет высокие требования по точности
и допускам расположения форм: допуск плоскостности - 0,01 мм, допуск
цилиндричности внутреннего отверстия шлицев - 0,01мм, допуск радиального биения
внутреннего отверстия шлицев - 0,025 мм, толщина диска -  мм, кроме
того фасонную торовую
поверхность -  мм, что обуславливает использование оборудования с ЧПУ.
Исходя из этого, составляем для данной детали
технологический процесс с использованием оборудования, оснащенного ЧПУ.
005 Заготовительная
Вырезать заготовку из листа согласно чертежу
010 Штамповочная
Гнуть заготовку из листа согласно чертежу
015 Термическая
Нормализовать заготовку, для снятия внутренних напряжений
020 Токарная многооперационная
Установ А
1) Точить торец Ø169,92, выдержав размер 17,5 мм
Точить поверхность Ø112
Точить фаску 1×45˚/ Ø112
2) Фрезеровать начисто боковую поверхность  справа
Фрезеровать начисто боковую поверхность кронштейнов, выдерживая
угол  , справа
Фрезеровать начисто поверхость 40, справа
Фрезеровать начисто поверхость  слева
Фрезеровать начисто боковую поверхность кронштейнов, выдерживая
угол  , слева
Фрезеровать начисто поверхость 40, слева
) Фрезеровать начисто поверхость кронштейнов, выдерживая
угол  и скругление R8,32 справа
Фрезеровать начисто поверхость кронштейнов, выдерживая угол  и скругление R8,32 слева
Установ Б
1) Точить торец Ø172,84, выдержав размер
10 мм
Точить фаску 1×45˚/ Ø112
2) Фрезеровать начисто поверхость кронштейнов, выдерживая
угол  и скругление R8,32 справа
Фрезеровать начисто поверхость кронштейнов, выдерживая угол  и скругление R8,32 слева
) Фрезеровать торовую поверхность  начерно
Фрезеровать торовую поверхность  начисто
4) Центровать отверстие Ø5 , выдержав угол  справа
Центровать отверстие Ø5 , выдержав угол  слева
) Центровать отверстие Ø5 , выдержав угол  справа
Центровать отверстие Ø5 , выдержав угол  слева
6) Сверлить отверстие Ø6,7 , выдержав глубину 12 мм справа
Сверлить отверстие Ø6,7, выдержав глубину 12 мм слева
7) Сверлить отверстие Ø6,7 , выдержав глубину 12 мм справа
Сверлить отверстие Ø6,7, выдержав глубину 12 мм слева
) Нарезать резьбу М8-7Н, выдержав глубину 10мм справа
Нарезать резьбу М8-7Н, выдержав глубину 10мм слева
) Нарезать резьбу М8-7Н, выдержав глубину 10мм справа
Нарезать резьбу М8-7Н, выдержав глубину 10мм слева
025 Протяжная
Протянуть внутренние шлицы согласно чертежу
030 Термическая
Азотировать всю деталь в течение 40 часов
035 Моечная
Промывка деталей на моечной машине
040 Контрольная
Контроль заданных размеров и отклонений формы поверхностей и
их взаимного расположения
Технологические расчеты
Расчет припусков на механическую обработку
Аналитический расчёт
припусков на диаметральный размер
Рассчитываем припуск на обработку и промежуточные
предельные размеры на поверхность ∅112Н10. Технологический маршрут
обработки поверхности ∅112Н10 состоит из
гидроабразивной вырезки и однократного растачивания.
Технологический маршрут записывается в таблицу 2,
также в таблицу заносятся соответствующие заготовке и каждому технологическому
переходу значения элементов припуска.
Переходы обработки поверхности ∅112Н10
|
Элементы припуска, мкм
|
Расчетный припуск 2z min, мкм
|
Расчетный min размер d, мм
|
Допуск на изготов-ление Td, мкм
|
Принятые (округл.) размеры по переходам, мм
|
Полученные предельные припуски, мкм
|
|
Rz
|
h
|
Δ
|
ε
|
|
|
|
dmin
|
dmax
|
2z min
|
2z max
|
Гидроабразивная вырезка
|
80
|
80
|
200
|
-
|
-
|
|
Н12 350
|
|
|
-
|
-
|
Однократное растачивание
|
40
|
50
|
32,5
|
71
|
431
|
112,14
|
Н10 140
|
112
|
112,14
|
|
|
Суммарное пространственное отклонение Δ в данном случае будет равно: погрешности позиционирования режущей
головки гидроабразивной установки ±0,1 мм на 1000 мм длины, т.е. 0,2 мм или 200
мкм и погрешности растачивания.
Находим остаточную величину пространственного
отклонения после растачивания:
 при закрепление в патроне
∆см = 0 мкм
 - величина коробления обрабатываемой поверхности,
Таким образом, получим:
 мкм. при закрепление в патроне
Погрешность установки:
 мкм.
где εб=10 мкм. погрешность базирования;
εз=70 мкм.
погрешность закрепления.
Остаточная погрешность установки:
 ,
Рассчитанные величины занесем в таблицу.
Величина расчетного припуска:
 - при закрепление в патроне
Рассчитанные величины занесем в таблицу.
Таким образом, минимальный припуск под
растачивание:
Зная расчетный размер после растачивания, находим
размер для гидроабразивной вырезки:
Зная допуски на получаемые размеры, находим
предельные значения размеров:
для гидроабразивной вырезки:
для растачивания:
Определим максимальное и минимальное значения
припуска под растачивание:
Общий припуск на обработку равен:
Общий номинальный припуск с учетом
несимметричного расположения поля допуска:
Находим номинальный размер заготовки:
Производим проверку правильности выполнения
расчетов по формуле:
На основании данных
расчета строим схему графического расположения припусков и допусков при
обработке поверхности ∅112Н10.
Рис.23 Схема графического расположения припусков и допусков при обработке
поверхности ∅112Н10
Аналитический расчёт припусков на линейный размер
Рассчитываем припуск на обработку и промежуточные
предельные размеры на поверхность  . Технологический
маршрут обработки поверхности  состоит из чернового, п/чистового,чистового
и тонкого точений за 2 установа. В качестве заготовки используется лист толщиной 25 мм по ГОСТ 7350- 77. Допуск и отклонения разделим на две
стороны заготовки поровну.
Технологический маршрут записывается в таблицу 3,
также в таблицу заносятся соответствующие заготовке и каждому технологическому
переходу значения элементов припуска.
Переходы обработки поверхности
|
Элементы припуска, мкм
|
Расчетный припуск z min, мкм
|
Расчетный min размер L, мм
|
Допуск на изготов-ление TlL мкм
|
Предельный размер, мм
|
Предельный припуск, мм
|
|
Rz
|
h
|
Δ
|
ε
|
|
|
|
Lmin
|
Lmax
|
z min
|
z max
|
Заготовка
|
125
|
360
|
-
|
-
|
12.51
|
500
|
12.51
|
|
-
|
-
|
Черновое точение
|
50
|
50
|
22
|
50
|
685
|
11.825
|
h 12 150
|
11.825
|
11.975
|
685
|
1035
|
Получистовое точение
|
32
|
30
|
18
|
5
|
127
|
11.698
|
h9 36
|
11.698
|
11.734
|
127
|
241
|
Чистовое точение
|
5
|
6
|
14
|
2
|
82
|
11.616
|
10
|
11.616
|
11.626
|
82
|
108
|
Тонкое точение
|
2,5
|
3
|
7,2
|
1
|
26
|
|
10
|
|
|
26
|
26
|
Итого
|
920
|
1410
|
Суммарное пространственное отклонение Δ в данном случае будет равно кривизне проката на длине
заготовки.
Находим остаточную величину пространственного
отклонения:
- после черного точения
- после п/чистового точения
- после шлифования
При закреплении по необработанной поверхности
погрешность закрепления равна
При закреплении по обработанной начисто
поверхности погрешность закрепления равна
Далее эта величина будет определять погрешностью
станка при перемещении инструмента (ε = 5 мкм) при точении и не плоскостностью
магнитной плиты шлифовального станка.
Переходы обработки поверхности
|
Элементы припуска, мкм
|
Расчетный припуск z min, мкм
|
Расчетный min размер L, мм
|
Допуск на изготов-ление TlL мкм
|
Предельный размер, мм
|
Предельный припуск, мкм
|
|
Rz
|
h
|
Δ
|
ε
|
|
|
|
Lmin
|
Lmax
|
z min
|
z max
|
Заготовка
|
125
|
150
|
360
|
-
|
-
|
|
500
|
|
|
-
|
-
|
Черновое точение
|
50
|
50
|
22
|
50
|
685
|
|
hl2 150
|
|
|
685
|
1035
|
Получистовое точение
|
32
|
30
|
18
|
5
|
127
|
|
h9 36
|
|
|
812
|
926
|
Чистовое точение
|
5
|
6
|
14
|
2
|
82
|
10,011
|
10
|
10,011
|
|
81
|
107
|
Тонкое точение
|
2,5
|
3
|
7,2
|
1
|
26
|
9,985
|
10
|
9,985
|
9,995
|
26
|
26
|
Итого
|
1604
|
2094
|
Расчет минимального значения припуска производим,
пользуясь формулой:

Таким образом, минимальный припуск под черновое точение на
первом установе:
Минимальный припуск под получистовое точение на первом
установе:
Минимальный припуск под чистовое точение на первом
установе:
Минимальный припуск под тонкое точение на первом установе:
Рассчитанные величины занесем в таблицу.
Общий припуск zomin и zomax определяем,
суммируя промежуточные припуски:
Проверка правильности выполненных расчетов:
 

 

На основании данных расчета строим схемы графического
расположения припусков и допусков при обработке поверхности  мм.
На первом установе:
Рис.24 Схема графического расположения припусков и
допусков при обработке поверхности  на
первом установе
На втором установе:
Рис.25 Схема графического расположения припусков и
допусков при обработке поверхности  на
втором установе
Выбор и назначение
режимов резания
Расчет режимов резания [8]
Операция 015, токарная универсальная ЧПУ.
· Черновое точения торца ∅169,92
. Подача
Выбор подачи осуществляется по каталогу Sandvik Coromant
в зависимости от инструмента. Принимаем  .
2. Скорость резания
Скорость резания считаем по приведенным формулам для данного
вида обработки




 
 ; 
 ;
 ;  ;
 ;
3. Частота вращения шпинделя

4. Сила резания
 ;    
 ;
 ;  ;  ;  ;
 ;
  ;
 ;
. Мощность резания
 , кВт.

· Фрезерование однократное поверхности 
1. Подача
Выбор подачи осуществляется по каталогу Sandvik Coromant
в зависимости от инструмента. Принимаем 
2. Скорость резания
Скорость резания считаем по приведенным формулам для данного
вида обработки




 
 ; 
 ;
 ;  ;
 ;
. Частота вращения шпинделя

4. Сила резания
 ;
 ;
  ;
5. Мощность резания
 , кВт.

Приведенный расчет режимов резания носит справочный характер,
действительные параметры резания выбираем в следующем разделе.
Выбор режимов резания
Т.к. весь режущий инструмент выбирается из
каталога Sandvik Coromant, режимы резания принимаются в соответствии с
данными каталога.
Резец токарный проходной CoroTurn RC SNMG 12 04 08-PR (правый)
Режимы резания:
Глубина резания: 
Подача: 
Скорость резания: 
Обрабатываемые поверхности:
· Точить торец Ø169,92, выдержав размер 17,5 мм
· Точить торец Ø172,84, выдержав размер 10 мм
2 Сверло CoroDrill CoroDrill®
Delta-C 2 − 3 x Dc
Режимы резания:
Глубина резания
Подача: 
Скорость резания: 
Обрабатываемые поверхности:
· Центровать отверстие Ø5 справа
· Центровать отверстие Ø5 слева
· Центровать отверстие Ø5 справа
· Центровать отверстие Ø5 слева
3 Резец токарный проходной CoroTurn HP TNMG 16 04 04-PF (правый)
Режимы резания:
Глубина резания: 
Подача
Скорость резания: 
Обрабатываемые поверхности:
· Точить поверхность Ø112
· Точить фаску 1×45˚/ Ø112
· Точить фаску 1×45˚/ Ø112
Концевая фреза CoroMill Plura
Режимы резания:
Глубина резания: 
Подача: 
Скорость резания: 
Обрабатываемые поверхности:
· Фрезеровать начисто боковую поверхность кронштейнов, выдерживая угол
 , справа
· Фрезеровать начисто боковую поверхность кронштейнов, выдерживая
угол  , слева
· Фрезеровать начисто поверхость кронштейнов, выдерживая угол  и скругление R8,32 справа
· Фрезеровать начисто поверхость кронштейнов, выдерживая угол  и скругление R8,32 слева
· Фрезеровать начисто поверхость кронштейнов, выдерживая угол  и скругление R8,32 справа
· Фрезеровать начисто поверхость кронштейнов, выдерживая угол  и скругление R8,32 слева
5 Концевая фреза CoroMill Plura
Режимы резания:
Глубина резания: 
Подача: 
Скорость резания: 
Обрабатываемые поверхности:
· Фрезеровать начисто боковую поверхность  справа
· Фрезеровать начисто боковую поверхость 40, справа
· Фрезеровать начисто боковую поверхость  слева
· Фрезеровать начисто боковую поверхость 40, слева
· Фрезеровать начисто боковую поверхость ∅172,84, справа
· Фрезеровать начисто боковую поверхость ∅172,84, слева
6 Концевая фреза CoroMill Plura
Режимы резания:
Глубина резания: 
Подача: 
Скорость резания: 
Обрабатываемые поверхности:
· Фрезеровать торовую поверхность  трижды
7 Сверло CoroDrill Delta-C
R841-0675-30-A1A 1220
Режимы резания:
Глубина резания: 
Подача: 
Скорость резания: 
Обрабатываемые поверхности:
· Сверлить отверстие Ø6,7 c фаской, выдержав глубину 12 мм справа
· Сверлить отверстие Ø6,7 c фаской, выдержав глубину 12 мм слева
· Сверлить отверстие Ø6,7 c фаской, выдержав глубину 12 мм справа
· Сверлить отверстие Ø6,7 c фаской, выдержав глубину 12 мм слева
8 Резьбофреза CoroMill Plura
Режимы резания:
Глубина резания: 
Подача: 
Скорость резания: 
Обрабатываемые поверхности:
· Нарезать резьбу М8-7Н, выдержав глубину 10 мм справа
· Нарезать резьбу М8-7Н, выдержав глубину 10 мм слева
· Нарезать резьбу М8-7Н, выдержав глубину 10 мм справа
· Нарезать резьбу М8-7Н, выдержав глубину 10 мм слева
Расчет норм времени
Рассчитаем нормы времени на операцию 015 по
обработке диска.
Токарная многооперационная.
Расчет всех составляющих норм времени
Время, затрачиваемое на технологическую операцию
изготовления единицы продукции, в общем случае складывается из двух частей:
 ,
где Тш.к. - штучно-калькуляционное время;
Тшт. - штучное время изготовления единицы
продукции;
Тп.з. - подготовительно-заключительное время;
n - количество деталей в настроечной партии.
 ,
где То - основное время; [10]
Тв - вспомогательное время; [11]
Тоб - время на обслуживание рабочего места;
Тот - время перерыва на отходы и личные
надобности.
 - оперативное время.
 ,
где Ту.с. - время на установку и снятие детали;
Тз.о. - время на закрепление и открепление
детали;
 - для токарных работ;
 - для сверлильных и расточных работ;
 - для фрезерных работ;
где L -
расчетная длина перемещения инструмента или стола;
so - подача на оборот шпинделя;
i - число проходов инструмента;
 ;
 ;
 .
Расчет времени протягивания:
Основное технологическое время протягивания определяется по формуле:
 ,
где  - длина рабочего хода протяжки, мм;
 - коэффициент, учитывающий обратный
ход (К=1,4-1,50).
 скорость резания
 ,
где - чертёжная длина протягиваемой поверхности, мм;
 - длина режущей части протяжки,
мм;
 - длина калибрующей части протяжки, мм;
 - длина перебега протяжки
(10-20 мм).
 ,
где - припуск на обработку, мм;
 - шаг режущих зубьев протяжки, мм.

 ,
 - число калибрующих зубьев протяжки (Zk=4-8);
 - шаг калибрующих зубьев протяжки,
мм.


Данные, посчитанные по вышеприведенным формулам, занесем в
следующую таблицу
№ операции
|
№ перехода
|
Размер обработки D или B, мм
|
Длина обработки, мм
|
Составляющие обработки, мм
|
i
|
Составляющие времени
|
|
|
|
|
|
|
ТО
|
ТВ
|
Топер
|
Тобсл
|
Тотд
|
Тшт
|
Тпз
|
Тшт.к
|
|
|
|
|
lобр
|
lвр
|
lпер
|
|
|
|
|
тех
|
орг
|
|
|
|
|
15
|
1
|
Ø169,92
|
88,5
|
84,5
|
2
|
2
|
1
|
0,49
|
0,08
|
0,63
|
0,02
|
0,01
|
0,03
|
2,62
|
0,06
|
2,68
|
|
|
1×45˚/Ø112
|
1
|
1
|
-
|
-
|
1
|
0,00
|
|
|
|
|
|
|
|
|
|
|
Ø112
|
14
|
10
|
2
|
2
|
1
|
0,06
|
|
|
|
|
|
|
|
|
|
ƩТо
|
0,55
|
|
|
|
|
|
|
|
|
|
2
|
40
|
48
|
48
|
-
|
-
|
1
|
0,14
|
0,08
|
1,07
|
0,01
|
0,01
|
0,04
|
1,13
|
0,11
|
1,24
|
|
|
20
|
50
|
50
|
-
|
-
|
1
|
0,14
|
|
|
|
|
|
|
|
|
|
|
бок.пов
|
103
|
103
|
-
|
-
|
1
|
0,30
|
|
|
|
|
|
|
|
|
|
|
40
|
48
|
48
|
-
|
-
|
1
|
0,14
|
|
|
|
|
|
|
|
|
|
|
20
|
50
|
50
|
-
|
-
|
1
|
0,14
|
|
|
|
|
|
|
|
|
|
|
бок.пов
|
103
|
103
|
-
|
-
|
1
|
0,30
|
|
|
|
|
|
|
|
|
|
ƩТо
|
0,99
|
|
|
|
|
|
|
|
|
|
3
|
бок2.пов
|
509
|
509
|
|
-
|
1
|
1,47
|
0,08
|
1,02
|
0,01
|
0,01
|
0,04
|
1,08
|
0,10
|
1,18
|
|
|
бок2.пов
|
509
|
509
|
|
-
|
1
|
1,47
|
|
|
|
|
|
|
|
|
|
ƩТо
|
0,94
|
|
|
|
|
|
|
|
|
|
4
|
Ø172,84
|
90,4
|
86,4
|
2
|
2
|
1
|
0,51
|
0,07
|
0,58
|
0,01
|
0,01
|
0,02
|
0,62
|
0,06
|
0,68
|
|
|
1×45˚/Ø112
|
1
|
1
|
-
|
-
|
1
|
0,00
|
|
|
|
|
|
|
|
|
|
ƩТо
|
0,51
|
|
|
|
|
|
|
|
|
|
5
|
бок3.пов
|
530
|
530
|
|
-
|
1
|
1,53
|
0,08
|
1,06
|
0,01
|
0,01
|
0,04
|
1,12
|
0,11
|
1,23
|
|
|
бок3.пов
|
530
|
530
|
|
-
|
1
|
1,53
|
|
|
|
|
|
|
|
|
|
ƩТо
|
0,98
|
|
|
|
|
|
|
|
|
|
6
|
торовая
|
246
|
246
|
|
|
1
|
0,71
|
0,08
|
1,59
|
0,02
|
0,02
|
0,06
|
1,68
|
0,16
|
1,84
|
|
|
торовая
|
246
|
246
|
|
-
|
1
|
0,71
|
|
|
|
|
|
|
|
|
|
ƩТо
|
1,51
|
|
|
|
|
|
|
|
|
|
7
|
Ø5
|
5
|
3
|
2
|
|
1
|
0,01
|
0,08
|
0,11
|
0,00
|
0,00
|
0,00
|
0,11
|
0,01
|
0,12
|
|
|
Ø5
|
5
|
3
|
2
|
-
|
1
|
0,01
|
|
|
|
|
|
|
|
|
|
8
|
Ø5
|
5
|
3
|
2
|
-
|
1
|
0,01
|
|
|
|
|
|
|
|
|
|
|
Ø5
|
5
|
3
|
2
|
-
|
1
|
0,01
|
|
|
|
|
|
|
|
|
|
ƩТо
|
0,03
|
|
|
|
|
|
|
|
|
|
9
|
Ø6,7
|
14
|
12
|
2
|
|
1
|
0,05
|
0,08
|
0,28
|
0,00
|
0,00
|
0,01
|
0,30
|
0,03
|
0,32
|
|
|
Ø6,7
|
14
|
12
|
2
|
-
|
1
|
0,05
|
|
|
|
|
|
|
|
|
|
10
|
Ø6,7
|
14
|
12
|
2
|
-
|
1
|
0,05
|
|
|
|
|
|
|
|
|
|
|
Ø6,7
|
14
|
12
|
2
|
-
|
1
|
0,05
|
|
|
|
|
|
|
|
|
|
ƩТо
|
0,20
|
|
|
|
|
|
|
|
|
|
11,12
|
M8-7H
|
11
|
9
|
2
|
|
4
|
6,00
|
0,08
|
6,08
|
0,06
|
0,06
|
0,24
|
6,44
|
0,61
|
7,05
|
|
ƩТо
|
6,00
|
|
|
|
|
|
|
|
|
|
|
|
|
|
|
|
|
|
|
|
|
|
|
|
|
Ʃ
|
20
|
1
|
шлицы
|
10
|
10
|
2
|
2
|
1
|
0,33
|
3,2
|
3,53
|
0,00
|
0,04
|
3,71
|
0,35
|
4,06
|
|
|
|
|
|
|
|
|
|
|
|
|
|
|
|
|
|
Проектирование участка механической обработки
Предварительный расчёт годовой программы выпуска
и такта
Таблица 6
№ п./п.
|
№ опер
|
Наименование операции
|
Модель станка
|
Нормы времени
|
|
|
|
|
Тшт
|
1
|
015
|
Токарная многооперационная
|
GMX 200 linear
|
16,36
|
2
|
020
|
Протяжная
|
7Б64
|
4,06
|
Расчёт уточнённой программы выпуска и такта

где:  - эффективный годовой фонд времени в одну смену
 - количество смен (2)
 - такт выпуска
 - программа выпуска деталей за год
Принимаем
программу выпуска 40000 штук в год.
Тогда такт выпуска будет равен:
Расчёт потребного количества оборудования
Исходя из полученного такта выпуска, определяем
количество станков на каждой операции:


Принятое количество станков на линии равно 3 штук.
Расчёт загрузки оборудования
Рассчитываем коэффициент загрузки станков на
каждой операции:


Средний процент загрузки всех станков определяется:

проверяем условие: 
расчётный коэффициент загрузки станков не удовлетворяет
условию

Выбор типа здания [13]
Для расположения проектируемого участка выбираем
одноэтажное многопролётное здание с железобетонными перекрытиями,
поддерживаемыми системой колон.
Ширину пролёта выбираем из унифицированного ряда
и принимаем равной - 18 метрам.
Шаг колон принимаем равной 6 метрам для
обеспечения надёжной опоры мостовому крану.
Для определения высоты цеха до нижнего пояса
фермы необходимо определить высоту до головки кранового рельса.
Вычисляем высоту до головки кранового рельса по
размерам выбранного мостового электрического крана.
 - наибольшая высота у станков (3640мм.
- 7Б64);
 - безопасное расстояние;
 - высота
перемещаемого груза
( мм) - для
станка GMX200 S linear;
( мм) - для
станка 7Б64;
Принимаем высоту перемещаемого груза равной 3844 мм.
 - размер
от подъёмного крюка до головки подкранового рельса (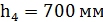 );

Принимаем 
Принимаем по ГОСТу высоту цеха до нижнего пояса фермы Н=9600 мм при ширине пролета 18000 м.
Расчёт потребных производственных площадей
В состав участка, планируемого в данной работе,
входит 2 станков, а именно:
· 2 центра обрабатывающих токарно-фрезерных модели GMX 200 S linear с массой 14000
кг.
· Полуавтомат протяжной вертикальный
для внутреннего протягивания модели 7Б64 с массой 5050 кг.
Таблица 7
№
|
Станок
|
Модель
|
Длина
|
Ширина
|
Высота
|
Мощность
|
Масса
|
1
|
Центр обрабатывающий токарно-фрезерный
|
GMX 200 S linear
|
6500
|
4100
|
3040
|
22
|
14000
|
2
|
Полуавтомат протяжной вертикальный для внутреннего
протягивания
|
7Б64
|
2875
|
1350
|
3640
|
11
|
5050
|
Длина участка L - составляет 24 м., ширина B - 18 м., таким образом,
потребная производственная площадь будет рассчитываться по формуле:
 мм
Разработка планировки участка механообработки
[14]
Межцеховой транспорт
Межцеховой транспорт служит для перевозки грузов
между цехами и складами (промежуточный и центральный). Поскольку заготовки
деталей, обрабатываемые на участке, имеют массу ≈ 2 кг, для перевозки партии
таких заготовок и готовых деталей со склада в цех и наоборот будем использовать
электрокары грузоподъемностью 1 т (см. рис.1).
Рис.26 Электрокар
Поскольку в качестве межцехового транспорта мы
используем электрокары, то при планировке участка предусматриваем магистральный
проезд шириной 5 метра в соответствии со строительными нормами и правилами.
Грузоподъёмные средства[15]
В качестве верхнего цехового транспорта и
грузоподъёмного средства используем кран мостовой двухбалочный общего
назначения КМ16/5-25,5-12,5-2K, который позволяет производить погрузку и
разгрузку электрокаров, а также в случае перестановки или ремонта, перемещать
металлорежущие станки либо другое технологическое оборудование. Основные
параметры приведены в таблице:
Таблица 8
Грузоподъемность
|
Пролет Крана
|
Высота подъема
|
Скорость подъема
|
Масса крана
|
Главного крюка
|
Вспомогательного крюка
|
|
Главного крюка
|
Вспомогательного Крюка
|
Главного крюка
|
Вспомогательного крюка
|
|
Т
|
М
|
м
|
м/мин
|
Т
|
16
|
5
|
25,5
|
12,5
|
0,055
|
0,16
|
33
|
|
|
|
|
|
|
|
|
Вид и размер тары для заготовок [16]
В качестве тары для заготовок используются
стандартные прямоугольные паллеты. Параметры выберем в соответствии с
габаритными размерами и массой заготовки. Максимальный размер заготовки 272 мм и масса 1,16 кг. Паллета имеет длину 1200 мм и
ширину 800мм, в которую помещаются 8 заготовок.
Система уборки стружки
На станках предусмотрена стружкоуборочная
система. Два стружкоуборочных конвейера располагаются за станками. Они имеют
стружкоуборочный транспортёр (ширина 400мм) и люки для ссыпания стружки. Данный
конвейер транспортирует стружку за пределы цеха (к специальным местам её
переработки).
Ширина проездов и проходов
Для перемещения электрокаров на территории цеха
предусматривается магистральный проезд шириной 5 метра. Расстояние между
станками в соответствии с нормами назначаем 1070 мм. Также на территории цеха
предусмотрены 3 прохода для рабочих шириной 1400
мм.
Фактическая площадь участка механообработки
Фактическая площадь участка механообработки определяется
непосредственно с выполненной планировки: измеряя длину  и ширину  участка на чертеже, получаем фактическую площадь:
 м2
Экономическая часть
Анализ технико-экономических показателей
существующего технологического процесса [17]
Сумма капитальных вложений в оборудование
Капитальные вложения рассчитываются по формуле:
 , руб.
где  - капитальные вложения в единицу оборудования, занятого
выполнением i-ой операции, руб.;
 - количество технологического оборудования;
 - коэффициент занятости оборудования выполнением i-ой операции.
 (руб.)
где ЦO.ti
- оптовая цена оборудования, (руб./ед.);
αТ - коэффициент, учитывающий
транспортно-заготовительные расходы;
αМ - коэффициент,
учитывающий стоимость строительно-монтажных работ
( от оптовой цены оборудования)
 , т.к. используемые
станки относятся к тяжелому оборудованию;
 ;
 руб.
 руб.
 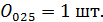
 
Рассчитаем капитальные вложения:
 руб.
Сумма капиталовложений в здание и
производственные площади
 (руб.)
где SOi - потребная площадь на i-ой
операции изготовления продукции, м2;
μSt - коэффициент занятости площади при
выполнении i-ой
операции изготовлении продукции, м.;
h - высота помещения цеха, в котором выполняется операция,
м.;
ЦЗД - стоимость 1 м2
производственного здания, руб.
SO 020 = 120,4 м2; SO 025 = 27,50м2;
μSt = 0,71;= 9,6 м.;
ЦЗД = 90 руб/м2.
 руб.
Сумма капитальных вложений в оснастку и
инструмент
 (руб.),
где КОСН.D - стоимость одного экземпляра оснастки D-го типоразмера, руб.;
ПD
- количество экземпляров оснастки D-го
типоразмера, необходимое для бесперебойного выполнения операции;
μОСН.D - коэффициент занятости технологической
оснастки D-го типоразмера при выполнении
операции;
 ;  45 000 руб.;
П015=2; П020=1;
μОСН.015=0,67; μОСН.020=0,35
 руб.
Затраты на оплату труда рабочих
 (руб.)
где tшт.
- штучно
калькуляционное время выполнения операции (мин.);
α - число операций;
в - часовая тарифная ставка рабочего (руб.);
% -
страховой налог:
 - дополнительная заработная плата рабочих (%);
tшт. 015 = 0,28 час.
tшт. 020 = 0,07 час.
α = 2;
в
= 240 руб.
 руб.
Сумма капитальных вложений в инвентарь
Сумма капитальных вложений в инвентарь составляет
1,5÷5% от стоимости основного
оборудования.
После проведенных расчетов целесообразно
составить сводную таблицу капитальных вложений технологического процесса:
Таблица 9
Капитальные вложения
|
Проектируемый вариант
|
Кап. вложения в оборудование
|
|
Кап. вложения в здание
|

|
Кап. вложения в оснастку
|
|
Кап. вложения в инвентарь
|
593 659,65
|
Итого
|
82 155 390,25
|
Расчет затрат на производство детали

где CMi - затраты на основные и вспомогательные материалы;
СЗi -
заработная плата рабочих, приходящаяся на изделия по i-ой оснастки
COi - затраты на эксплуатацию оборудования;
СKi -
затраты по использованию производственного здания, приходящееся на изделие при
выполнение i-ой операции;
СЦ - цеховые затраты;
 .
Затраты на материалы
Затраты на материал расчитывались в разделе 1.1.4
Затраты на заработную плату в расчете на единицу
изделия
 (руб./шт.)
где СЗОi - заработная плата основных рабочих по
операциям (руб./шт.);
Сзисi - средняя часть заработная плата основных
рабочих по тарифу;
αi, КqЗi, Ксi - коэффициенты, учитывающие приработок,
дополнительную заработную плату и ЕСН;
ti - норма времени i-ю операцию изготовления изделия (час/шт. - опер.);
βoi - коэффициент, учитывающий число единиц
оборудования, обслуживаемого одним рабочим;
Сзисi=240
руб./шт.
αi=1,10
КqЗi=1,15
Ксi=1,34;
tшт. 015 = 0,27 час.
tшт. 020 = 0,07 час.
βoi=1
 руб/шт.
 руб./шт.
 руб./шт.
Затраты на эксплуатацию оборудования
 (руб./шт.)
где Сai
- затраты на амортизацию оборудования;
Сpi
- затраты на ремонт оборудования;
СЭi -
затраты на электроэнергию, приходящиеся на изделие;
Сai =  руб./шт
Сpi =  руб./шт
СЭi =  руб./шт
 262,66 руб./шт.
Затраты на амортизацию оборудования
 (руб./ед.)
где КOTi
- балансовая стоимость единицы оборудования (руб./ед.)
Oi - количество технического оборудования
выполнения i-ой операции изготовления данных
изделий;
μoi - коэффициент занятости оборудования
выполнения i-ой операции изготовления данных
изделий;
a - норма амортизационных отчислений на замену оборудования
в год;
QГ.З. - годовой выпуск изделий;
 руб.
 руб.
a=11,6;
QГ.З=20000
шт./год.
 руб./ед.
Затраты на ремонт оборудования

где R -
группа ремонтной сложности основной части оборудования;
W - затраты на все виды
планово-предупредительного ремонта и межремонтного обслуживания за ремонтный
цикл, приходящийся на единицу ремонтной сложности оборудования, руб. за
цикл/ед. ремонт, сложности.
КЭ - коэффициент, учитывающий затраты на ремонт
энергетической части оборудования;
ТРЦ - длительность ремонтного цикла, год/цикл;
β1 - коэффициент, учитывающий влияние типа производства
и т.п.;
QГ.З. - годовой выпуск изделий (шт./год);
R=30
W=169 000
КЭ=1,3;
ТРЦ=7 лет
β1=1,4
Г.З=20000
шт./год.
 руб.
Затраты на электроэнергию, приходящиеся на
изделие
 (руб./шт.)
где ЭСi - годовой расход электроэнергии, кВт
час/год;
ЦЭ - стоимость 1 кВт/час электроэнергии,
руб./кВт-час
QГ.З. - годовой выпуск изделий, шт./год;
ЭСi=7,9 кВт час/год
ЦЭ=3,8 руб/кВт
QГ.З.=20000
шт./год

где Ny - суммарная установочная мощность электродвигателей оборудования;
Кврi - коэффициент загрузки по времени
электродвигателей;
KNi - коэффициент загрузки по мощности;
Кodi
- коэффициент одновременной работы двигателей;
KW - коэффициент, учитывающий потери
электроэнергии в сети завода;
ti - нормы времени на i-ю операцию изготовления изделия;
ηМ - средний КПД электродвигателей;
КВi - коэффициент выполнения норм на i-ой операции;
QГ.З. - годовая программа выпуска;
Ny 1=22; Ny 2=11
Кврi=0,6
KNi=0,7
Кodi=1;
KW=1,05;
tшт. 020 = 0,28 час.
tшт. 025 = 0,07 час.
ηМ=0,7
КВi=1,1;
QГ.З=20000
шт./год.
 кВт
час/год
Таблица 10
Модель оборудования
|
Мощность электродвигателя, кВт
|
Кврi
|
КNi
|
ηM
|
GMX 200 S Linear
|
22
|
0,6
|
0,7
|
0,7
|
7Б64
|
11
|
0,6
|
0,7
|
0,7
|
Затраты на содержания помещения
 (руб./шт.-опер.)
где SOi - площадь, для выполнения i-ой операции, м2;
μзi - коэффициент занятости площади;
СК.Г. - годовые расходы на содержание помещения,
приходящиеся на 1 м2 площади цеха
SO 015 = 120,4 м2; SO 020 = 27,50м2;
μзi=0,71
СК.Г.=3300 руб./год
 руб./шт.
Цеховые затраты

где СЗО - заработная плата основных рабочих;
КЦ - коэффициент, учитывающий цеховые расходы:
СЗО=240
руб./шт.
КЦ=0,5.
 руб.
Таблица 11
Наименование затрат
|
Затраты, руб./шт.
|
|
Проектируемый вариант
|
Затраты на материал
|
|
Заработная плата
|
|
Затраты на эксплуатацию оборудования, в то числе
Амортизация оборудования Затраты на ремонт оборудования Затраты на
электроэнергию
|
|
Затраты на содержание помещений
|
17,32
|
Цеховые затраты
|
120
|
Итого
|
|
 (руб./год)
где Зизд - затраты на изготовление единицы изделия, руб.;
Зизд = 731,81
руб.
QГ.З.= 20000 шт./год.
 руб.
Экономический
расчет проведен для изготовления 1 диска.
Полные
затраты на изготовление 2 дисков - 
Охрана труда, ИЗОС и действия в ЧС
Мероприятия по охране труда, технике безопасности и
противопожарной защите, производственной эстетике на участке [14]
Охрана труда - система законодательных актов и соответствующих им
социально-экономических, технических, санитарно-гигиенических и организационных
мероприятий, обеспечивающих безопасность, сохранность здоровья и
работоспособность человека в процессе труда.
Улучшение условий труда, повышение его безопасности и безвредности имеет
большое значение. Оно влияет на экономические результаты производства -
производительность труда, качество и себестоимость выпускаемой продукции.
Производительность труда повышается благодаря сохранению здоровья и
работоспособности человека, экономии живого труда, путём повышения уровня
использования производственных фондов, уменьшения числа аварий и т.п.
Обеспечение здоровых и безопасных условий труда возлагается на
администрацию предприятий, учреждений, организаций. Администрация обязана
внедрять современные средства техники безопасности, предупреждающие травматизм,
и обеспечивать санитарно-гигиенические условия, предотвращающие возникновение
профессиональных заболеваний.
Производственные здания, сооружения, оборудование, технологические
процессы должны отвечать требованиям, обеспечивающим здоровье и безопасные
условия труда. Эти требования включают рациональное использование оборудования,
территорий и производственных помещений, правильную эксплуатацию оборудования и
организацию технологических процессов, защиту рабочих от воздействия вредных
факторов, содержание производственных помещений и рабочих мест в соответствии с
санитарно-гигиеническими нормами и правилами, устройство санитарно-бытовых
помещений.
Характеристика проектируемого техпроцесса
В данном дипломном проекте «Планирование производства
детали диск
роторно-лопастного двигателя с внешним подводом тепла мощностью 5-10 кВт» за
счет использования нового многооперационного оборудования с ЧПУ расширяются технологические
возможности механообработки в целом.
Проводим исследование условий труда с целью
выявления опасных и вредных факторов, которые имеются в процессе работы.
Таблица Опасные и вредные факторы в ходе
технологического процесса
№
|
Наименование операции
|
Вид оборудования
|
Вредные и опасные факторы
|
005
|
Заготовительная
|
Установка гидроабразивной резки Water Jet Sweden NC 2560 S
|
Опасность травм от движений в станках, электроопасность,
шум, вибрации.
|
010
|
Штамповочная
|
Пресс
|
Опасность травм от движений в станках, электроопасность,
шум, вибрации.
|
015
|
Токарная многооперационная
|
Центр обрабатывающий токарно-фрезерный GMX 200 S linear
|
|
020
|
Протяжная
|
Полуавтомат протяжной вертикальный для внутреннего
протягивания 7Б64
|
|
025
|
Термическая
|
Шахтная печь для каталитического газового азотирования США
10.15/7
<#"519967.files/image386.gif">
Допустимая:
верхняя граница: 
нижняя граница: 
Теплый период года:
Оптимальная температура: 
Допустимая:
верхняя граница: 
нижняя граница: 
Температура внутренних поверхностей конструкций,
ограждающих рабочую зону (стен, пола, потолка и др.), или устройств (экранов и
т.п.), а также температура наружных поверхностей технологического оборудования
или ограждающих его устройств не должны выходить более чем на  за пределы оптимальных.
Перепад температуры воздуха по высоте рабочей зоны
допускается до  .
Колебания температуры воздуха по горизонтали в рабочей
зоне, а также в течение смены допускается до 5, при этом абсолютное значения
температуры воздуха, измеренной на разной высоте и в различных участках
помещений в течение смены, не должны выходить за пределы допустимых величин.
Относительная влажность воздуха:
Холодный период года:
Относительная влажность, оптимальная: 
Допустимая: не более 
Теплый период года:
Относительная влажность, оптимальная: 
Допустимая: не более  (при  )
Допускается в теплый период года повышать относительную
влажность воздуха, но не более чем на 10% по отношению к допустимым величинам.
Скорость движения воздуха:
Холодный период года:
Оптимальная скорость: 
Допустимая: не более 
Теплый период года:
Оптимальная скорость: 
Допустимая: не более 
Интенсивность теплового излучения:
Интенсивность теплового облучения работающих от нагретых
поверхностей технологического оборудования, осветительных приборов, инсоляции
на постоянных и непостоянных рабочих местах не должна превышать:
· 35  при облучении 50% поверхности тела и более;
· 70  - при величине облучаемой поверхности от 25% до 50%;
· 100  - при облучении не более 25% поверхности тела.
Интенсивность теплового облучения работающих от открытых
источников (нагретый металл, стекло, "открытое" пламя и т.д.) не
должна превышать 140  , при этом облучению не должно подвергаться более 25% поверхности
тела и обязательным является использование средств индивидуальной защиты, в том
числе средств защиты лица и глаз.
Производственное освещение
Для освещения производственного помещения применяется совмещенное
освещение.
Характеристика зрительной работы: высокой
точности.
Наименьший размер объекта различения: 0,3-0,5 мм
(деления приборов измерения).
Разряд зрительной работы: III
Подразряд зрительной работы: Г (средний контраст
объекта с фоном, светлый фон).
Выбираем тип освещения - совмещенный.
Естественное освещение. Используется в дневное
время суток. Оно обеспечивает хорошую освещенность, равномерность, вследствие
высокой способности к рассеиванию, благоприятно действует на зрение и
экономично. Естественное освещение осуществляется через световые проемы и имеет
верхнее исполнение.
Нормируемое значение коэффициента естественной
освещенности определим по формуле:

где:  - номер группы обеспеченности естественным светом;
 - значение КЕО;
 - коэффициент светового климата;
 - коэффициент запаса.

 (световой проем в трапециевидном фонаре)
Искусственное освещение. Применяется в темное
время суток, а также при недостаточном естественном освещении.
Для общего освещения (всего участка) используются
светильники типа ЛОУ с газоразрядными лампами. Данные светильники располагаются
над оборудованием в два ряда, по пять штук в ряду.
Для местного освещения (освещения на станке)
используются лампы накаливания. Они имеют отражатель из непрозрачного материала
с защитным углом отражения α=30º.
Снизу
светильник перекрывается светорассеивающим стеклом.
Величину освещения выбирают по характеру зрительной работы по
нормам СНиП 23-05-96. «Нормы проектирования искусственного освещения и
естественного освещения».
Рабочие зоны освещения в такой мере, чтобы рабочий имел
возможность хорошо видеть процесс (обработки) работы не напрягая зрение и не
наклоняясь к предмету расположенному на расстоянии далее 0,5 м. от глаз.
Обеспечивается равномерное освещение рабочей
поверхности, без бликов и теней. Величина освящения постоянная во времени.
Направленность светового потока выбираем таким образом, чтобы в одних случаях
рассмотреть внутренние поверхности детали, а в других рельефность элементов
рабочей поверхности
Рис.26 Светильники
общего освещения.
Рис.27 Светильник
для местного освещения.
По СНиП определяем необходимый минимум
освещенности - 3500 лк.
Коэффициент неравномерности освещения при
расположении светильников по периметру прямоугольника принимаем равным 1,2.
Определим необходимое количество светильников для
искусственного освещения рабочих зон разрабатываемого механического цеха. Для
этого воспользуемся методом коэффициента использования светового потока.
Светильники общего освещения расположены рядами, их
количество можно определить по формуле:

где:  - требуемая освещенность по нормам (лк);
 - освещаемая площадь,  ;
 - коэффициент запаса (1,15 … 1,8);
 - коэффициент неравномерности;
 - световой поток одной лампы (лм);
 - коэффициент использования
светового потока (коэффициент использования светового потока лампы (%),
зависящий от типа лампы, типа светильника, коэффициента отражения потолка и
стен, высоты подвеса светильников и индекса помещения.
Характер зрительной работы при обработки
щеткодержателя относится к наивысшей точности (наименьший размер различения
объекта менее 0,15 мм
Показатель помещения.

Где:  - длина помещения (30 м),
 - ширина помещения (18 м),
 - высота подвеса светильника (4 м).
Находим коэффициент использования светового потока, η=54.
Подбираем
люминесцентную лампу дневного света
Philips TLD 58W/950 Graphica
<#"519967.files/image425.gif">
Philips TLD 58W/950 Graphica
<#"519967.files/image426.gif">
В цехе соблюдаются нормы освещённости,
ограничения слепящего действия светильников, пульсации освещённости и другие
качественные показатели осветительных установок согласно требованиям СниП
23-05-95 «Естественное и искусственное освещение.
Для обеспечения минимальной освещённости (равной
10% рабочего освещения) в производственном помещении на случай внезапного
отключения рабочего освещения, предусмотрено аварийное освещение, питающееся от
независимого источника - генератора переменного тока. При аварийном освещении
используются светильники типа ГСР-400.
Производственные вибрации и шум
При работе на металлорежущих станках имеет место
общая вибрация по ГОСТ12.1.012-90, ССБТ "Вибрационная безопасность":
Вибрация возникает при работе шпинделя,
электродвигателей, элементов приводов и вентиляторов. Допустимое значение 92 дБ
- для постоянных рабочих мест в производственных помещениях при непрерывном
воздействии в течение рабочего дня (8 ч).
Локальная вибрация возникает при контакте
станочника с органами управления станка. Нормируется предельно допустимая сила
нажима работающих на части оборудования, подверженные вибрации до 20 кг (при
оптимальной форме рукояток). Рукоятки органов управления станком изолируем
вибропоглащающими материалами.
Мероприятия по борьбе с вредным воздействием
вибрации:
· проектирование рабочих
мест с учетом максимального снижения вибрации;
· исключение контакта человека с частями
станочного оборудования путем установки автоматизированного оборудования;
· создание условий труда,
при которых вредное воздействие вибрации не усугубляется наличием других
неблагоприятных факторов;
· применение регулируемых
ударных виброгасителей возле штамповочного оборудования;
· применение СИЗ рук
оператора (рукавицы, перчатки) при контакте с вибрирующим объектом.
При нормировании шума согласно ГОСТ12.1.003-96
ССБТ "Шум. Общие требования безопасности", используем метод
нормирования уровня звука в дБ А.
По временным характеристикам шум следует
подразделять на:
· постоянный - уровень
звука, который за 8-часовой рабочий день (смену) изменяется по времени не более
чем на 5 Дб;
· непостоянный - уровень
звука, который за 8-часовой рабочий день (смену) изменяется по времени более
чем на 5 Дб;
Постоянный шум:
Допускаемый уровень звукового давления в
осктавных полосах со среднегеометрической частотой 31,5 Гц: 107 дБ
Непостоянный шум:
Характеристикой непостоянного шума на рабочих
местах является интегральный критерий - эквивалентный (по энергии) уровень
звука в дБ А.
Допустимый эквивалентный уровень звука: 80 дБ А
Средства и методы защиты от шума:
· оснащение шумных машин
средствами дистанционного управления и автоматического контроля;
· совершенствование
технологии ремонта и обслуживания машин;
· при превышении допустимых
параметров шума, применить СИЗ противошумные наушники.
Техника безопасности
Электробезопасность
В проектируемом технологическом процессе используется оборудование со
следующими характеристиками:
Таблица
Станок
|
Мощность кВт
|
Напряжение (В)
|
Частота (Гц)
|
Система водоструйной резки фирмы "Water Jet
Sweden AB"
|
12
|
380
|
50
|
Центр обрабатывающий токарно-фрезерный
|
22
|
380
|
50
|
Полуавтомат протяжной вертикальный для внутреннего
протягивания
|
11
|
380
|
50
|
Шахтная печь для каталитического газового
азотирования
|
84
|
380
|
50
|
Данное электрооборудование требует заземления нетоковедущих
элементов, согласно правилам устройства электроустановок:
Рис.28 Схема
защитного заземления изолированной нейтралью до 1000В и выше.
- заземленное оборудование; 2 - проводник заземления; i3 - ток заземления; Ф1,Ф2,Ф3 - фазы; Z1,Z2,Z3 - предохранители.
Технические способы обеспечения электробезопасности:
заземление нетоковедущих частей (корпуса электрических машин;
корпуса трансформаторов, аппаратов, светильников; привода электрических
аппаратов, вторичные обмотки измерительных трансформаторов; каркасы
распределительных щитов, щитов управления, щитков и шкафов; металлоконструкции;
подвижные части (металлорукава и т.д.) заземлены оголенным
медным проводом;
отключение станков и другого электрооборудования при коротком
замыкании, осуществляется за счет автоматов и предохранителей, находящихся в
доступном месте;
недоступность токоведущих частей обеспечивается путем
расположения двигателей, релейной аппаратуры, трансформаторов и т.д., в
станинах станков в закрытых шкафах.
Питание к станкам подходит через шиносборку, расположенную на
высоте 2 м. От шины до станков, кабеля изолируют двойной изоляцией (трубы,
бронешланги)
Пульт управления оператора, управляющая и регулирующая
аппаратура, имеют питание переменным током малого напряжения-42 В., что
исключает опасность поражения электротоком.
Производственное помещение с установленным оборудованием относится к I-ому классу (помещения без повышенной опасности). Механический участок,
на котором происходит технологический процесс изготовления вала, размещен, в
отапливаемом помещении с температурой воздуха: зимой - 18-20 , летом - 21-23 ,
т.к. этого требуют инструкции по эксплуатации станков с ЧПУ. Влажность в
помещении должна быть в пределах 40-60%. Участок располагается в закрытом
помещении. Поэтому выделения химически активной и органической пыли,
разрушающее действующей на изоляцию, выделяемые на других участках предприятия,
не проникают на данный участок. Полы в помещении изготовлены из
токонепроводящих материалов.
От коротких замыканий и больших перегрузок используются электрозащитные
средства:
предохранители, рассчитанные на токи до 2,5;4,5;10;60А;
тепловые реле, встраиваемые в пускатели и защищающие электродвигатель
от перегрузок;
автоматы, рассчитанные на токи до 5;10;100А.
Лица, обслуживающие электроустановки, должны быть обучены и аттестованы
на знание ПУЭ, ПТЭЭП (правил техники безопасности при эксплуатации
электроустановок потребителей) с присвоением квалификационной группы (II-V). Переаттестация производится не реже 1 раза
в год.
Рабочее место станочника обеспечивается защитными средствами:
изолирующими подставками и настилами.
Требования безопасности при выполнении
техпроцесса
В соответствии с ГОСТ 12.3.025-96 ССБТ "Обработка
металлов резанием. Требования безопасности" правила техники безопасности
включают в себя требования к оборудованию, инструменту, общие правила:
рукоятки и кнопки управления станком должны передвигаться в
направлении движения исполнительных органов;
не допускается производить замер детали во время вращения
шпинделя;
для ускорения останова вращения, станок должен быть снабжен
тормозным устройством;
перед началом работ, должна быть проверена надежность
закрепления детали;
необходимо устранить возможность снятия детали во время
вращения шпинделя;
станочник допускается к работам после прохождения инструктажа
по технике безопасности;
инструмент, получаемый заводом, должен быть тщательно
проверен;
инструмент должен храниться в кладовых на стеллажах, полках.
Требования безопасности к производственному оборудованию
В соответствии с ГОСТ 12.2.009-96 ССБТ "Станки
металлообрабатывающие. Общие требования безопасности" требования
заключаются в следующем:
оборудование устанавливается на прочном фундаменте;
´ запрещается работа на неисправном
оборудовании;
´ отдельные механизмы должны снабжаться
прочным ограждением;
´ уборку стружки и пыли должен
производить регулярно работающий на данном станке станочник;
´ систематически должна производиться
смазка всех частей оборудования;
´ запрещается смазка привода во время
работы;
´ состав и применение СОЖ
согласовывается с санитарным надзором;
´ щитки и рубильники должны
устанавливаться в глухих металлических кожухах, запирающихся на замок с
надписями о применяемом напряжении;
´ ремонт электрооборудования
производится только специальным электромонтером.
Безопасность труда при работе с видеотерминалами
Опасные факторы при работе:
Каждому, кому приходится работать за компьютером,
хорошо знаком с чувством усталости. Компьютерная усталость специалиста, внешне
напоминает алкогольное опьянение: пошатывающаяся походка, невнятная речь.
Человек почти не замечает ее в ходе работы и может, увлекшись, просидеть за
компьютером не один час. При этом оператор длительное время находится в
неизменном положении, приводящем к мышечно-скелетному разрушению. Кроме того,
постоянное напряжение глаз вызывает утомление, резь и мельтешение в глазах,
головную боль.
Третьим фактором, влияющим на нарушение здоровья
оператора, является воздействие электромагнитных излучений видимого спектра,
крайне низких, сверхнизких и высоких частот. Эти излучения действуют на нервную
систему, минуя органы чувств.
Категория труда:
Работы на ВДТ (видеодисплейный терминал) по
тяжести и энергозатратам относятся к категории легких физических работ (Iб).
К категории Iб относятся работы, производимые сидя, стоя
или связанные с ходьбой и сопровождающиеся некоторым физическим напряжением,
при которых расход энергии составляет от 120 до 150 ккал/ч. При выполнении
таких работ температура воздуха должна составлять в холодный период года -  , в теплый -  .
Относительная влажность на рабочих местах должна быть 40 -
60%, а скорость движения - не более 0,1 - 0,2 м/с. Для повышения влажности воздуха
в помещениях с ВДТ и следует применять увлажнители воздуха, заправляемые
ежедневно дистиллированной или прокипяченной питьевой водой.
Освещение:
Естественное освещение должно осуществляться через
светопроемы, ориентированные преимущественно на север и северо-восток и
обеспечивать коэффициент естественной освещенности (КЕО) не ниже 1, 2% в зонах
с устойчивым снежным покровом и не ниже 15% на остальной территории.
Искусственное освещение в помещениях эксплуатации ВДТ и
ПЭВМ должно осуществляться системой общего равномерного освещения.
Освещенность на поверхности стола в зоне размещения
рабочего документа должна быть 300 - 500 лк.
Пожаровзрывобезопасность
Проблема обеспечения пожаровзрывобезопасности производства
представляет собой одну из важнейших задач, т.к. интенсификация техпроцессов,
концентрация производств и широкое применение легковоспламеняющихся материалов,
сопровождается повышением уровня опасности. Создающиеся факторы взрыва приводят
к травмам, отравлению и гибели людей, а также к значительному материальному
ущербу.
Пожаровзрывобезопасность объектов машиностроительного
производства обеспечивается решением большого числа мероприятий инженерного и
организационного характера.
Причиной возникновения пожара на участке могут стать:
- нарушения технологического режима (неправильное хранение,
температурный режим сушки и т.д.);
неисправность электрооборудования (короткое замыкание,
токовые перегрузки, большие переходные сопротивления), источником возгорания в
электрооборудовании могут являться: проводники, корпус электромашины;
оборудование и процесс резания без системы охлаждения;
самовозгорание применяемой ветоши и других материалов.
На механическом участке предусматриваются и выполняются
следующие организационно-технические мероприятия по предотвращения пожаров:
использование пожарной сигнализации;
организация пожарной охраны на предприятии;
использование на рабочем месте первичных средств
пожаротушения (наличие противопожарного шкафа с огнетушителями типа ОУ-8 или
ОВП-10, пожарным рукавом, ящиком с песком, лопатой, багром и т.д.);
наличие в помещении аэрационных фонарей (для возможности
удаления газов и дыма);
пожарная профилактика электроприводов;
защита электрооборудования от перегрузки по току и
сопротивлению.
На случай пожара на участке предусмотрен запасной выход для
безопасной эвакуации людей в случае пожара (необходимо обеспечить свободный
доступ).
Для предупреждения пожаров каждый работник на участке должен
строго выполнять следующие правила:
курить в строго-отведенном месте и не зажигать спички на
рабочем месте;
не загромождать сырьем, полуфабрикатами или готовой
продукцией подступы к станкам и рабочему месту;
не оставлять на рабочем месте и в карманах промасленную
ветошь;
- не хранить легковоспламеняющиеся жидкости в
открытых емкостях, в стеклянной посуде и не проливать их на пол.
Организация рабочего места
Согласно ГОСТ 12.2.033-96 ССБТ "Рабочее место при
выполнении работ стоя. Общие эргономические требования":
органы управления станком должны находиться в пределах
досягаемости рук человека;
должен быть обеспечен, возможно, близкий подход к станку;
необходимо обеспечить максимальный обзор зоны наблюдения;
необходимо оборудовать рабочее место стеллажами для хранения
приспособлений, инструмента и т.д.;
общая организация рабочего места должна быть оформлена с
учетом производственной эстетики, включающей рациональное цветовое оформление
производственного интерьера. При этом цвет используется как композиционное
средство, обеспечивающее гармоничное единство производственного помещения и
технологического оборудования (окраска станков в светло-зеленый тон создает
хорошую контрастность с обрабатываемым изделием, что снижает зрительное
утомление).
Список литературы
1. С.И. Дмитриев, Е.А. Евгеньева «Технология машиностроения»
расчет припусков на обработку.
. «Курсовое проектирование по технологии машиностроения»
под ред. А.Ф. Горбацевича.
. В.В.Шевельков Проектирование и производство литых
заготовок
Псков ППИ СПбГТУ 2000г.
4. Е.А.
Евгеньева, С.И. Дмитриев «Технология машиностроения».
5. <http://www.gkstal.ru>
6. <http://www.merametall.ru>
7. <http://www.sandvik.coromant.com/sandvik/3030/Coromant/Internet/S006826.nsf>
8. «Справочник
технолога-машиностроителя» под ред. Косиловой, Мещерякова в 2-х томах.
9. <http://www.s-metal.com.ua>
. Курсовое
проектирование по технологии машиностроения» под ред. А.Ф. Горбацевича.
11. Общемашиностроительные
нормативы режимов резания для технического нормирования работ на металлорежущих
станках. Часть 2-я. М. «Машиностроение», 1972 г
.
«Общие машиностроительные нормативы времени и режимов резания» в 2-х томах.
. М.Е.
Егоров «Основы проектирования
машиностроительных заводов» М.
высшая школа 1969г
. А.Г.
Схиртладзе «Проектирование
механосборочных цехов и участков» Дрофа М. 2006г
15. <http://www.promspravka.com/catalog/D/K/29/2/22/1/14/210/3/kran_1433.html>
16. <http://palletmarket.ru/1.html>
. И.А. Дагаева
«Методические указания по разработке экономической части выпускной
квалификационно работы по специальности 151001 «Технология машиностроения»»
18. В.В.
Шкуркин «Безопасность жизнедеятельности» Псков 2005 г.
. <http://www.lighting.philips.ru/>
20. <http://www.gerpher.co.uk>
Похожие работы на - Проектирование участка по производству и механообработке дисков роторно-лопастной группы
| |